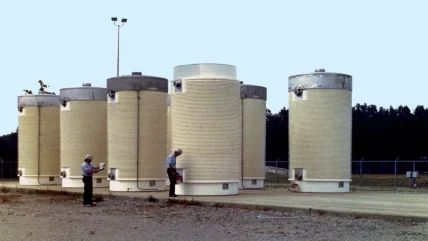
The need to find a safe way to store spent nuclear fuel is a major concern all over the world. As a temporary solution, most countries are turning to dry cask storage until more permanent solutions are developed.
Steven K Waisanen, vice president and head of global nuclear business at Konecranes explains the overall process of nuclear power generation for spent fuel storage.
“At the start of the fuel cycle, nuclear fuel assemblies are loaded into the reactor core with the fuel handling equipment,” Waisanen says. “Once the nuclear fuel is spent—no longer efficient in producing heat to turn water into steam—the fuel is off-loaded from the core and transferred to the spent fuel pool with the fuel handling equipment. The fuel will sit in the spent fuel pool until either the pool is full or a minimum of five years.”
As mandated by the individual laws of each country, if the spent fuel can’t be reprocessed for reuse in a new fuel assembly then the power plant has only two alternatives—wet storage or dry storage. This means that the spent fuel assemblies are packaged into canisters and either loaded into transportation casks and taken to the country’s centralised spent fuel pool storage facility, or the spent fuel is dry-stored in a storage cask at the plant on the regulatory-qualified and licensed spent fuel storage pad.
“This is where a Vertical Cask Transporter (VCT) comes into use,” Waisanen says. “The VCT is a specific design of material handling equipment that transports the nuclear spent fuel casks from the plant’s spent fuel storage building to the onsite dry cask storage pad.”
Chris Perkins, engineering manager for Lift Systems, explains that the casks are steel-lined concrete containers which can vary in weight from 60t to 300t depending on what size and style is employed in the storage plan at a given nuclear site.
“These containers, once loaded, must be transported to a storage pad where they are constantly monitored for temperature and radiation,” says Perkins. Lift Systems supplies handling equipment for several stages of the loading and transportation process.
Prakash Narayanan, deputy director and design engineering at TN Americas, the nuclear division of Areva, says that the inventory of spent fuel assemblies is continuously increasing. This is due to the regular replacement of approximately one-third to a half of the total number of fuel assemblies in a reactor core, which are discharged permanently every 18–24 months. “The discharged fuel assemblies are stored in the spent fuel pool—wet storage— initially and when there is no longer sufficient space in these pools, they are stored in licensed dry storage systems in an independent spent fuel storage installation,” says Narayanan. “When fuel storage is not considered, there will be no room for discharged fuel assemblies and subsequently, it will not be possible to perform reactor power operations. Without adequate consideration for storage, nuclear power generation is not possible.
Roger L Johnston, who founded company J&R in 1978 to primarily serve the crane manufacturing business, says: “As professional engineering consulting firm, we developed the first ever cask transporters in 1994. It was a crawler, to work better in confined spaces such as between the cask and the doorway. J&R was awarded the Wisconsin Governor’s Award in recognition of this product’s design.”
Travel Restrictions Apply
Regulations and codes covering transportation of spent fuel casks differ from country to country. The storage of spent fuel involves handling the fuel, loading the fuel in the storage systems, on-site transfer or transport, and storage. Narayanan explains how to understand any issue related to spent fuel, by considering two aspects: storage and transportation.
“The applicable regulations governing storage are per 10CFR Part 72 and the Standard Review Plan related to review of Applications are provided in NUREG-1536 and NUREG-1567,” says Narayanan. “Transportation of spent fuel involves handling of the fuel, loading, and offsite transportation or retrieval from a Storage System for off-site transportation.
The applicable regulations governing transportation are per 10CFR Part 71 and the Standard Review Plan related to review of Applications is provided in NUREG-1617.”
Spent fuel casks have to be designed to withstand impact without sustaining any critical damage that could result in radiation exposure above regulated limits, says Waisanen.
“If material handling equipment is required to lift a cask higher than the distance the cask is qualified to, or lift a transfer cask higher than a distance that would preclude rolling if dropped—typically 6”—then the US standards such as KTA 3902 & 3 or NUREG 0554, NUREG 0612 and ASME NOG-1 would be required for single failure proof lifting equipment necessary to pick the cask,” Waisanen says.
“If the cask is designed for the lift height, then less stringent codes and standards are required to be met. In these cases, specialised equipment with some redundant features in compliance with standards such as EN, CMAA and ANSI N14.6 could be used for the design of the lifting equipment or in some cases, standard equipment with increased safety margins are used. In all cases, adherence to the applicable safety analysis for the power plant is required.”
Perkins adds that the transport of casks on the nuclear plant site is regulated and approved in the US by the Nuclear Regulatory Commission (NRC). The site typically has to submit a dry storage plan for approval to the NRC. Through dry run tests the procedures, all storage plans and procedures are vetted and refined to meet NRC requirements.
David Weber, director of Whiting Nuclear Services says: “Individual generators frequently employ the expertise of companies such as Whiting to optimize their compliance processes for specialist cranes of types vital to all 61 Commercial Operating nuclear power plants that produce 19.6% of electricity generated in the US.”
Designing Fuel Casks
The spent fuel casks are designed and licensed in the US according to the criteria specified in the regulations and the NRC guidance documents including the Standard Review Plan. “They are usually designed to promote ease of use and operations within a nuclear power plant,” says Narayanan at TN Americas. “Some of the characteristics include the external dimensions of the cask, with a diameter of roughly 2.4m and length of 5.5m, and weight of the cask on the crane hook of 110t–125t.
“Our company designs and licenses two types of storage systems: canisterbased Horizontal Systems (NUHOMS), and metal cask vertical systems. An advantage of our patented NUHOMS used nuclear fuel transport and storage system is its horizontal orientation, which significantly reduces canister lift and suspension risks.”
Areva TN designed metal cask systems that can be also handled using commercially-available cask transporters, because there are no operations that involve stack-up or handling of canisters.
According to Waisanen, some dry storage cask manufactures have a cask designed to handle fewer fuel bundles in the canister and have an overall weight of 40t, while designs that include a higher number of fuel bundles have an overall weight of 186t. The cask can be metal or concrete and the height, based on the height of the fuel assembly, is roughly 3m.
“Konecranes entered into the VCT market because we saw the need for a rubber-tired machine, which could benefit customers because it does not damage the ground surface like a tracked vehicle does,” Waisanen says.
Konecranes VCTs also include advanced positioning features that provide the ability to travel in a vector in any direction, as well as ‘free steer’ like a car or rotate in a complete circle about its centre. “The VCT is a natural addition to our product portfolio to allow us to cover the fuel cycle from new fuel to spent fuel, and allows us to provide pool-to-pad material handling equipment and services. We also designed the VCT to be compactly packaged and easily reassembled for shipping anywhere in the world,” Waisanen says.
Perkins explains how Lift Systems got involved about 20 years ago. “Our then chief operating officer Ray Shuman, who previously worked for a defence contractor, heard about a nuclear facility’s need to move spent fuel to a storage pad,” Perkins says.
“He was involved in building a similar towable transporter at his previous employer, which led to Lift Systems being chosen to design, build and supply their first transporter. To date, Lift Systems has delivered over 30 custom and standard solutions to nuclear waste handling challenges.”
Latest VCTS
“The most recent VCT was a towable design as specified by our client,” Perkins says. “The VCT was required to have wheels, low ground-bearing pressure, to operate on asphalt travel paths, and the ability to lift and rotate 90° a cask with redundant drop prevention safety systems. Additionally, Lift Systems provided a modified 110t-capacity TriLifter and an electrically-powered, radiation-resistant rail cart for the same programme.”
To meet such requirements, Perkins explains, large-diameter hard-rubber wheels were designed for the low ground-loading requirement. The main lift beam is equipped with a spreader beam that can rotate 360°. The patented hydraulic wedge lock system was employed for the redundant drop prevention.
The latest Konecranes VCT is single failure proof and is designed per ASME NOG-1 Type 1 to not only move the casks, but to transfer spent fuel canisters into the dry storage casks, Waisanen says. The canister is not designed to be dropped, so it has to meet signal failure proof requirements as outlined in NOG-1. This means that no single failure in the load path of the material handling equipment will cause the load to drop or move in an uncontrolled manner.
“This machine was delivered to a nuclear power plant in 2015 and has completed two spent fuel campaigns to date,” Waisanen says. “The machine has multiple innovations that are currently patent pending in Europe and the United States.”
The design of VCT to NOG-1 Type 1 requirements include an integrated redundant reeving with a load block as well as totally redundant hoist machinery and brakes. Waisanen explains that they utilise a closed kinematic loop hoist design to achieve the redundancy needed to meet the requirements. This kind of design can minimise any uncontrolled motion in the case of a single mechanical component failure.
The aim of the Areva TN’s Transfer Trailer (TT) is to ensure that the transfer cask is aligned to the storage module and that the canister can be inserted for storage. Thus, the TT will also house additional components that support this primary function.
“The Horizontal Systems do not require a VCT and can employ a simple ‘commercial’ trailer or transporter for this purpose,” Narayanan says. “Thus, the main requirements of the TT are related to the commercial availability and ease of operation. Key features include the ability to be manoeuvred within the Independent Spent Fuel Storage Installation (ISFSI), a short turning radius, housing of the transfer skid, self-propelling with independent suspension and precise positioning.”
Over the last seven years J&R developed a dozen cask transporters from 80t up to 275t. This is a niche market because there are only a few hundred nuclear plant across the world, explains company founder Johnston.
“When we have to lift higher and we have to load the cask, there is the risk of a potential drop if something goes wrong,” Johnston says. “Thanks to our pretty unique dual load-paths, which means holding up the casks, this drop risk can be avoided. If they fall like a cylinder we have a backup automatic system and a Lift-NLock cam-locking system, which don’t let them fall down.”
Other features of J&R’s VCTs include the main frame with an open ‘C’ section to allow a fully entry of a storage cask.
The engine, fuel tank, hydraulic tank and operator station with controls are all mounted on the frame rear centre section.
The propel system comprises of two independent closed circuit hydrostatic systems that each drive a 248:1 planetary to drive the chain sprockets. Each system has fully variable piston pumps and motors. The pumps are infinitely variable from zero to full speed.
Johnston adds that a top lifter crawler transporter is the most desirable machine rather than the bottom lifter, which has been used for just one project. “One of the recent applications was in England in a nuclear plant,” Johnston says. “We got involved and supplied a rubber-tired, 275t capacity machine.”
Enerpac has been approached by Holtec International to develop and commission a 170tm vertical cask transporter. The transporter combines the lifting capability of a hydraulic gantry with the flexibility of a self-propelled modular transporter (SPMT) to provide safe handling of the casks.
“Holtec had experience of using Enerpac SPMTs for transporting casks out of the spent fuel building to an outdoor location, where it was then transferred to a VCT for final placement at the outdoor storage facility,” says Pete Crisci, Enerpac global business development leader for integrated solutions. “Their positive experience with Enerpac provided us an opportunity to expand our offering to include the VCT.
From an industry perspective, the VCT demonstrates the flexibility of Enerpac lifting systems and the ability to combine them. In this case, the VCT combines both gantry and SPMT technologies in which Enerpac has many years’ experience.
“The main VCT design characteristics meet these requirements, using a single vehicle for both the lifting/lowering and transportation of the casks simplifies the handling requirements; and avoids the need for an additional crane.”
The Enerpac VCT is under development and its features includes key functional and safety features including normal steer, 90° turn, crab and auto-rotation turn and drive capability, and an innovative cab design allowing the VCT operator to face the direction of travel. Safe handling of the casks can be assured by the VCT’s drop prevention system and integrated cask restraint, a hydraulically operated clamp that secures the cask for transport. The cask handling system also has low ground bearing pressure.
Applications
One ongoing project in West Valley is being carried out with a Lift Systems VCT to decommission a shut-down nuclear reprocessing facility. “The casks were loaded with a vitrified radioactive material,” Perkins says. “The cask is first moved into position; the VCT connects to the cask and then is towed to a storage pad.”
Konecranes too has also recently found new roles for its VCTs. “During a recent dry cask storage campaign at a nuclear generating power plant, our Konecranes VCT was called on to transfer the spent fuel canisters to dry storage casks and then transport the casks to the facilities storage pad,” Waisanen says. “Our technology, with advanced steering and integrated single failure proof load block, not only safely handled the canister and cask, but it nearly reduced the cycle time in half which resulted in a 50% reduction in worker radiation exposure as compared to the industry average.
“The end user is realising overall cost savings while also achieving health and safety goals by minimising risks to their employees with equipment that has integrated features designed to the highest standards.”
Describing a recent job, Narayanan says: “Once the used nuclear fuel is transferred from the reactor’s used fuel pool into the submerged NUHOMS canister, the canister is lifted from the pool, all interior moisture is removed, and the canister’s double lids are welded shut. The canister is then lifted again and laid onto the transporter’s trailer for travel to the onsite dry storage site.”
Nicolas, part of the TII-Group, recently delivered a self-propelled cask transporter for the transportation of spent nuclear fuel casks in the vertical position to an industry in the north of Russia. Designed to operate in extreme climate conditions, the vehicle supports concentrated loads, moves them safely in vertical position and keeps the mechanical stress on the transported casks extremely low.
The Nicolas cask transporter offers a capacity of 50t and has been designed to operate at temperatures down to minus 45°C by incorporating specialised wheels, steel grades, sensors and reinforced heating systems for cabin, engines and electrical installations. Equipped with four axles, it relies on the established technology behind the Nicolas MHD-G2 modular vehicles, and its frame has been particularly designed to support concentrated loads in two different standard sizes. During operation, the cask transporter reaches a maximum speed of 5km per hour, travels across slopes and narrow turns and connects several storage facilities.
“One of the main challenges was keeping the load vertically without deformation of the cask, despite vibrations and unavoidable minimal bending of the supporting frames,” explains Alexis-Pierre Durand, engineer in charge of the project.
“Classic fastening methods lock the load with tensioning systems; the Nicolas cask transporter relies on a pressure system, allowing a precise dosage of the applied forces. Also, we can guarantee that corrosion, cold and additional stress due to decontamination processes won’t harm the cask transporter.”
During the loading process, the vertical stroke of the vehicle allows lowering the loading frame directly to the ground. An upper platform also permits the operator to access the load for fixing and unfixing.
The vehicle is hydrostatically driven by a diesel engine. The Power Pack, a redundant electric engine allows downgraded emergency transportation modes in case of engine failure in the main unit, assuring a safe emergency procedure under any circumstances. The Nicolas cask transporter and all its components, such as heaters and engines, are protected by a remote-controlled fire extinguishing system. Strong work lights for all distance ranges and a back-view camera further increase the safety of load and driver.
If idle, the cask transporter can be connected to a power line, supplying an independent vehicle heater to guarantee an easy starting procedure and a comfortable working environment for the driver. An electronic logic controller of the vehicle can guide the operators while manoeuvring the vehicle, minimising the possibility of human errors.
Cask Handling Cranes
Advanced single failure proof cranes used to safely move spent nuclear fuel to dry cask storage are engineered to ensure that even if anything fails mechanically, the load will not drop.
The Whiting name has been associated with overhead cranes for nuclear applications since the Manhattan project in the 1940s, says Weber: “Whiting had the first patent on single failure proof cranes decades ago, and the current design takes the very good aspects of that original patent employed on 18 such cranes currently in service and builds on this proven success with new features including low weight, high strength and enhanced seismic performance.
“We produce and service cask handling cranes, turbine cranes and polar cranes, which are so-called because they operate on a circular runway located near the spring line of the containment/reactor building and are primarily used in the removal and replacement of the reactor head, as well as during the refuelling process.”
The company is constantly improving its designs with lighter, stronger materials and service innovations, adds Weber.
“For example, we were able to install and commission a 250t turbine bridge crane while adjacent turbine generators ran at full power with no down time, saving millions of dollars in maintenance outage costs.”
The Whiting team also constructed an entire hydraulic heavy lifting and rotation test structure off-site in preparation for the actual installation at a nuclear generating station in Michigan, which produces enough power for a city of 1.25m people.
“The savings achieved in time and money are applicable to other turbine, generator and heavy lift applications across a wide range of industries seeking to enhance safety and avoid downtime,” Weber says.
The main requirements of cask handling cranes include a lightweight, simple design with the fewest possible components to maintain.
“By taking our original designs and using what worked well but modernised with lightweight components, as well as using other new lightweight components, we achieved those goals,” Weber explains.
“We dramatically reduced the weight and the weight is very important, because of seismic performance. If we can remove the existing trolley and put up a new, more sophisticated and stronger trolley that weighs the same or less, then all the seismic design that was originally done for the crane is still valid.
“There is also a lot of machinery associated with a single failure proof, another reason why we were very conscious of weight. We used high strength material and high strength wire rope.”
Two recent applications installed in Texas contained not only the design innovations of Whiting Corporation, but also the complementary installation and service skills of Whiting Nuclear Services.
The plant has an existing 15t single failure proof crane above the 150t crane. “We devised a plan to take the existing trolley down in pieces, while the new trolley was designed to be installed in pieces, with all the pieces being less than 15t,” says Weber. “We were able to use the trolley and crane right above it to do all the installation work, which was essentially the safest way you can do it. We didn’t have to use mobile cranes or jacking towers or other devices that that have the potential to fail.
“Another aspect of this particular cask handling project was that we used our services technicians to actually build the trolley in the shop, because those were the same guys that were going to essentially build it again in the field. The trolleys were assembled and tested prior to tear down and shipment to plant where the same technicians assembled it in the field.
“It is a rule of thumb that it is five times harder and five times more expensive to do something when you are over 30m in the air—probably ten times worse in a nuclear plant where you’re dealing with the essential safety regulation.”
An example is provided by two 150t crane upgrades completed last year that cost-efficiently brought this vital equipment up to single failure proof standards so the generator involved could safely move fuel with it.
“The redesign to the higher standard ensured there are redundancies in all the mechanical devices,” Weber says. For example, if one wire rope fails, the other wire rope is a backup. On the structural side of the crane, it is seismically designed so that if there is an earthquake, it will not fail. Electrically it is designed to failsafe standards and put it in a safe state if stopped, because what we are picking up, spent nuclear fuel, cannot be mishandled.”
Konecranes entered into the spent fuel cask crane market in the early 1970s. “The Boiled Water Reactor plant design has the reactor in the same building as the spent fuel pool and the decontamination pit,” Waisanen explains. “The reactor crane also doubles and the spent fuel cask crane. The regulatory then required increased safety requirements for this type of crane. The first standard published to which Konecranes built these types of cranes was called Reg Guide. Konecranes developed several patents for the design of the hoist systems on these cranes.”
The company has been manufacturing spent fuel cranes for over 40 years and have built, or upgraded to single failure proof for cask handling, more than 50 cranes.
The latest model of spent fuel cask crane from Konecranes is fully compliant with KTA 3902 &3, NUREG 0554 and REG612 and NOG-1 Type requirements. The company’s specific design of single failure proof is trademarked ‘Super Safe’.
“We have multiple patents with the new design which we have been putting out into the market over the last 15 years,” Waisanen says. “We have also delivered the largest single fail proof cask crane in the world to Ginna Nuclear Power Plant. It is designed to telescope into the building to deposit empty casks into the spent fuel pool and then remove the filled spent fuel cask to an auxiliary building where the cask is prepared for long term storage.”
“Konecranes Nuclear and Equipment Service (KNES) designed a spent fuel cask crane according to NOG-1 Type 1 and KTA 3902 & 3 requirements which includes several features like completely integrated redundant reeving with a load block as well as totally redundant hoist machinery and brakes. We utilise a closed kinematic loop hoist design to achieve the redundancy needed to meet the requirements. This type of design minimises any uncontrolled motion in the case of a single mechanical component failure.”
Waisanen explains that KNES completed the upgrade of two existing spent fuel cranes at a customer’s site in Europe early in 2016. The upgrade involved the replacement of the trolley/hoist and the controls on each crane with a Konecranes patented designs to meet all the current codes and standards required on the project.