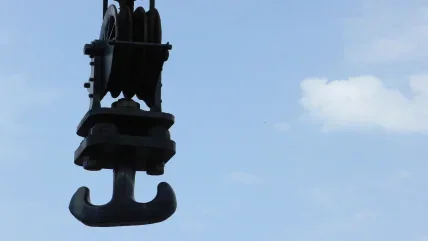
United States Steel Corporation’s Midwest Division plant is a 1960’s Sheet and Tin Finishing Facility, located on the southern shore of Lake Michigan, 40 miles from Chicago. There are 47 total EOT cranes in the Division. The majority were built to Association of Iron and Steel Engineers, AISE, Technical Report No. 6, “Specification for Electrical Overhead Cranes for Steel Mill Service”. The crane builders were Morgan, Reading, Alliance, Northern, P&H, and Zenar. The crane capacities range from 10 US ton (9t) to 75 US ton (68t). The majority of the cranes are double hoist of 50/15-ton (45t/13.6t) capacities. The cranes’ bridges are usually eight-wheeled cranes, nearly evenly split between either double A-5 drives or double A-4 drives. The majority of the bridge wheels are double-flanged, flat-treaded and usually 24 in (610mm) or 27 in (686mm) diameters. The crane wheel surface hardness is 57 – 63 Rc. All wheel assemblies have spherical roller bearings. Bridge speeds are in the 400-450 ft/m (122-137m/m) range. DC motors with 250 V input power the vast majority of the bridges; however, there are a few 440 VAC applications.
The runway bridge rail system is predominately a floating rail expansion bay system held by standard type H1 single welded clips and holders on a steel underlayment base. The bridge rails are #175 crane rail in 39 ft (11.9m) lengths with bolted splice bar joints. The majority of the rail spans are 120 ft (36.6m) or 130 ft (39.6m); however, there is a runway of 1,745 feet (532m) in length that facilitates the use of synthetic rubber nosed rail clips mounted on a synthetic rubber pad with flash-butt welded rail connections. This particular report will refer specifically to the A-5 drive with the 230 VDC series motor on the runways with the flash butt as well as the splice bar rail applications.
Every steel plant maintenance group has from time to time a specific event, or series of events, that gets a critical investigation and review that puts the affected group on a new course. Often these events are undesirable situations; but, looking back can be acknowledged as beneficial in the end because they initiated a new practice, procedure or methodology that resulted in an improvement to the operation that came because of it. At Midwest in December 2003, such an event occurred when thin and broken off crane wheel flanges caused an Electrical Overhead Traveling (EOT) crane derailment and an unscheduled crane repair outage for wheel assembly replacements. It was the second occurrence of this nature within a two-month period on separate EOT cranes. The crane’s unavailability initiated a maintenance review that led to improved maintenance practices, extended service life of the crane components, and reduced costs in maintaining the EOT cranes.
About 80 percent of the wheel assemblies replaced at the plant have been replaced because they wore thin or had broken flanges. Efforts to eliminate these problems have been pursued in the past several ways. Thick-flanged wheels and harder wheels of 57-63 Rc have been tried, but they wore thin and required replacement.
Use of two different lubricant types at the interface between the rail and the wheel flange has been utilized. The oil-type application was tried but not found to be as successful as required. It involved dispensing minute amounts of oil using a rotating felt wheel in contact with the wheel flange. The design was complex, composed of a lot of moving and wearing parts requiring regular repair or replacement. The inherent headaches associated with trying to keep the numerous applicators functioning, and the overall cost of replacement parts, which were expensive made this particular application undesirable. Another hydrocarbon product was applied to the side of the railhead with a brush. This product has been found to work for a period of time, but it is difficult to install, takes excessive amounts of valuable maintenance time, is messy and its effectiveness short lived. It also required a great deal of care in the application. During application the lubricant could contact the railhead area and be transferred to the crane wheel tread area-causing difficulties controlling the bridge activities of the crane. Crane outage maintenance time is always at a premium, and the frequent reapplication schedule was hard to maintain with the higher priority of other work always occurring.
Articles have been written on this subject before. The latest related paper was “Not accepting crane wheel flange failures,” (Steel Technology September 2000, p.56-9). The author, J. J. Davis, listed a choice of six different lubrication systems for crane wheel flanges and rails. The author says that the most commonly utilized on cranes in the US is the patented dry lubricant system by Trans-Lube, Inc. He says that the system consists of a spring-loaded holder assembly with bayonet cap and a small clip to attach the holder to a bracket. The patented graphite-based stick measures1x1x6in (25mm x 25mm x 152mm). He adds: “The typical mounting arrangement of the lubricant system is a lubricant holder on each flange, two per wheel.”
The plan
It was decided that the five cranes using the most wheels should be identified and that flange thickness measurements would be taken to evaluate how well the lubrication system worked on these cranes. An additional consideration in selection of the cranes was to test the graphite stick lubrication method on the splice bar rail connection rail as well as a flash butt-welded rail application. This trial, if successful, would reduce the major problem of wheel replacement.
The cranes were identified by their plant designation number as 6, 11, 17, 18, and 19. Crane six services the tin free steel (chrome) line and the electrolytic tin line (ETL). Crane 11 supports the continuous anneal (CA) and cleaning line. Crane 17 services the cleaning line. Cranes 18 and 19 support the pickle line.
Then technicians inspected each of the cranes’ wheels and record the current thickness and finish of the flange. This would provide a firm benchmark for start of the test.
The next step was for technicians to fabricate the brackets to mount the lubricant holders and purchase the lubricant system. Once this was accomplished the units were installed on the designated applications. After installation of the lubricant system on each crane, periodic inspections were performed during the monthly preventative maintenance inspection to again document the wheel flange conditions and make corrective adjustments in the aim of the holders to the wheel flange and keep them refilled as needed.
A model of the lube system arrangement was built in order to show the lubricant arrangement to the crane crew. The model facilitated being able to inform and demonstrate what the test involved and also to be able to better explain how the holders should be aimed for effectiveness.
The test was planned to operate for several months to see how changing weather, from summer through autumn to winter, would affect rail alignment and gauge changes.
The lubricant brackets also included a rail sweep function so the end corners of the crane included this feature. Two different brackets were required, one for 24” diameter wheels and one for 27” diameter wheels.
In May 2004, the five identified cranes, each having 8 bridge crane wheels had their wheel flanges inspected and some brackets for the lubricant fabricated and installed. In June the first crane, #11 had all its brackets installed and the lubricators aimed and filled. By the middle of July two more cranes, #6 and #18 were completed. By the middle of August, the last two cranes #17 and #19 were completed. Flange condition thickness measurements and finish conditions were recorded.
The Results
After proper implementation of the new dry lubricant system, the finish on the flange becomes very polished. There is a noticeable change easily visible with the inspector’s eye. The change is discernible after a short period of time on these high-duty cycle cranes (less than two weeks). Amazingly, the flange gets a smooth and shinny appearance changing from its gray, galled and gouged finish and quickly becomes as bright as the chrome finish on automobile bumpers. It is very smooth to touch.
The measured rate of wear of the flange seems to come to a halt. This smoother and repaired mirror-like finish on the flange aids in maintaining a strong flange thickness. The flanges are not getting noticeably thinner. The matching side of the railhead is also being polished.
When crane wheel flanges and the rail were wearing, a high-pitched sound was generated. This is during abrasive and adhesive contact between the wheels and the rails as the crane bridges down the runway. This sound is often an intense screeching that is penetrating and distracting The presence, and at other times absence, of some of the sounds make it apparent that there is some direct relationship of noise with outside climatic temperatures. The lubrication has significantly lessened the noise.
Crane crew craft personnel are convinced that lubrication of the wheel flanges greatly reduces the wear and will make the wheels last longer. No one on the crane crew likes changing wheel assemblies, especially when the temperature is 140ºF (60ºC) up on the runway. Members of the crane crew, on their own initiative, started making more of the brackets needed to mount and install lubricators on additional cranes in order to prevent their wheel flanges from wearing out.
Since the wheel flange lubricators were installed, there has not been a wheel change on any crane with the lubricators.
Some findings
The plan was to have lubricants examined during the monthly preventive maintenance inspection. The inspection and correction of the aim and refilling the lube sticks was immediately incorporated into the normal routine. This action made a smooth transition that evolved into a considerable decrease in the need for supervisory interaction in monitoring the lubricators and having them refilled.
There is a need to closely examine the alignment or aim of the lube stick in the very beginning to insure it is correctly meets the wheel flange at its outer diameter tip on the rail contact side and is not aiming down or centered at the radius of the tread with the flange. This was communicated to with the craft persons making the second round of inspections and adjustments. If the lubricant is in contact with the wheel flange tip, the lubricant wipes down the surface of the flange toward the tread radius as the wheel rotates.
The working end of the lube stick holder needs to be positioned as close to the wheel flange as possible without touching the rotating wheel flange. A 1/8-inch (3mm) gap is ideal. The crane wheel naturally regularly reverses and having a large gap will cause the lube stick to rotate back and forth inside the holder. The farther it is away, the more it rotates back and forth in the holder tube, wearing the sides of the lubricant stick. Also, short pieces of the lube stick will fall out of the end of the holder the farther away the end of the tube is positioned from the wheel flange. Ideally, if a close position is maintained, and a lube stick is worn out against the wheel flange, very little of the lubricant is wasted.
To speed up the corrective action in the lubrication of the entire flange it is advisable during initial installation to chip off the contact edge of the lube stick to mate it as near the shape of the flange as possible. This is about a 45º angle in most cases. This then allows the lube stick to accelerate its wear in to the exact contact profile faster and provide total flange area lubrication. Not beveling the lube stick wearing end but leaving the square edge on the corner of the lube stick, will result in just a small contact zone on the wheel flange until the lube stick wears-in to the exact profile. This could take some time and during wear-in it is not helping to polish the untouched surfaces of the flange.
It is advisable to keep as much tension on the lube stick as possible. This then means adding a half-lube stick, if it can be added, to keep the tension at a maximum. The goal is to get the flange to as polished a condition as quickly as possible to provide the lubricant protection. A polished flange is not wearing the rail or itself out.
Another observation in these tests was that all five cranes, all double A-5 drive arrangements, appeared to favor one side of the runway. This condition was theorized as a consequence of correctly adhering to keeping driver wheel diameters matched within the specified 0.010-inch (0.25mm) tolerance. The double A-4 drives are commonly seen with this characteristic as a normal condition of operation.
To conclude, the dry lubricant system is not free. But the cost of purchasing and installing the system on the five initial cranes was less than the cost of rebuilding one wheel assembly. The payback makes this a very good investment.