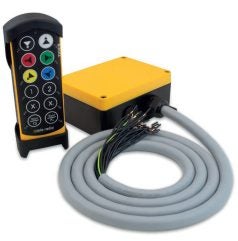
It is a year since I last wrote about control systems in this magazine, and in a year a lot can happen, especially in the world of digital technology.
And a lot has happened. Specifically, AI Sure, Artificial Intelligence existed a year ago, and I wrote about it; but it was something exotic, specialised, seemingly out of the far sci-fi future, and for the esoteric and tech-obsessed end of the market only. Since then, it has descended onto the non-specialist world, and with a vengeance. We can all download Chat GPT on our smartphones, and for free; AI voices on robo-calls can help us or scam us, depending on the entity behind them; articles like this can be written by AI – though I promise that I am actually a real person, though I do not know of a way to prove it: (I do tick the ‘I am not a robot’ box on those verification web-pages, but surely a robot could be taught to do that also). And AI can control hoists and cranes.
But ‘can’ and ‘does’ are two different things. Academic papers have been written, and are being written, explaining exactly how overhead cranes can be controlled by AI. An example, is a paper by SCISPACE entitled ‘Bridge Crane Monitoring using a 3D LiDAR and Deep Learning’. But despite the rapid penetration of AI in other areas, it has yet to penetrate the lifting world in any real, market-place, sense. Sophisticated software is used in warehousing, to select items for lifting, packing and handling; software is also in use to work out economic stacking and handling procedures for steel coils and the like and to automatically control the overhead hoists that do so; but the difference between software that runs automation – where humans tell it what to do, and it works out the best way of doing it – and AI that delivers true autonomous crane operation, without benefit of any human input is huge. It is the difference between self-driving cars, long promised as just around the corner but never actually arriving, and almost-self-driving cars, which can do 99.99% of the job but still need a driver to sit there getting bored but alert enough to slam on the brakes now and then. That last little fraction is the hard bit.
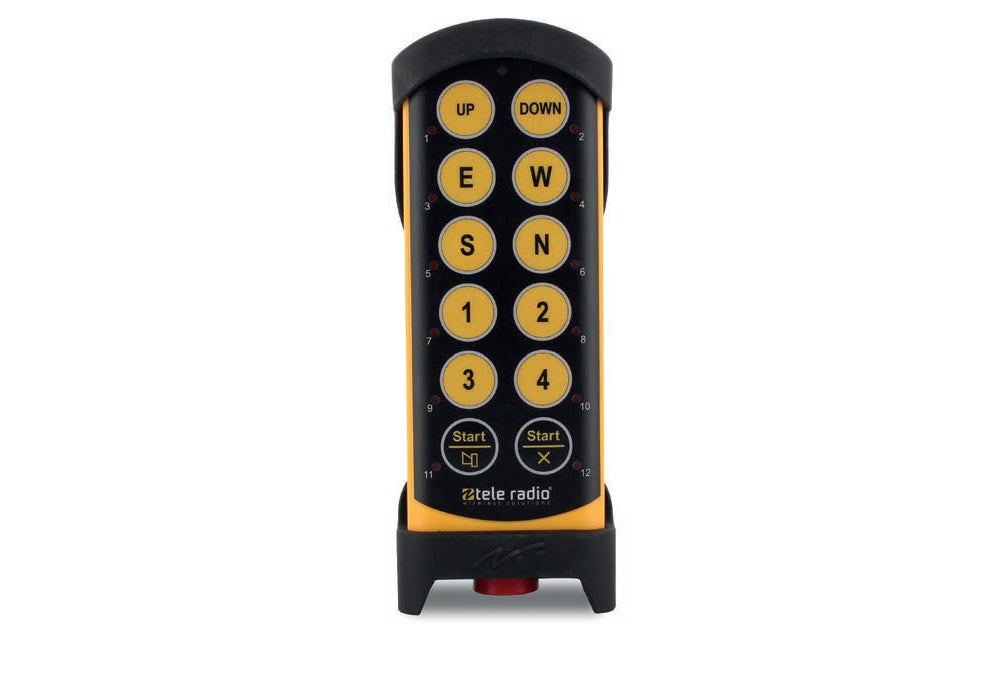
So, crane and hoist control systems are currently not done by AI. If I write another control article a year from now that may have changed; but for this one, control systems are running on what we shall soon have to call good old-fashioned hightech digital technology. But what good old-fashioned high-tech digital technology can achieve would have seemed quite extraordinary even a couple of years ago. In this world, the future is coming very fast indeed.
So for now, lets look at what is currently out there.
Street Crane has its Street Sabre wireless controller. Street Sabre uses 2.4GHz frequency, which is the global standard and allows the same system to be uses worldwide. It also allows group standardisation for operator familiarity and spare parts commonality. It has automatic frequency hopping technology, which gives extremely secure signalling and eliminates interference between multiple remote control stations and allows up to 50 controllers to operate simultaneously within a single factory as well as adding an additional level of security and safety to the system. There is optional command monitoring for protection against unintended operation.
A feature claimed as unique is the shape and layout of the handset: it is designed for one-handed operation – the operator can grasp the handle in the palm of the hand and press the buttons with fingers or thumb. Unlike conventional push button systems, says Street, this design allows the operator to naturally select the correct command for the required crane operation without taking their eyes off the load.
This significantly increases safety. The push button pressures are designed to help reduce operator fatigue in cases of continuous and repetitive use.
It comes in three versions. Sabre 1 has 8 buttons and 12 output relays; Sabre 2 has 18 outputs and 18 digital inputs; and Sabre 3 has 12 buttons (6 auxiliary) and 18 output relays and 18 digital inputs.
Charging time is only 15 minutes for a full charge; five minutes of charging time is sufficient for four hours of continuous operation. This highly efficient system, says Street, negates the need for any back up. The average estimated life expectancy of a Street Sabre battery is about five years, which they say is at least twice that of a traditional battery.
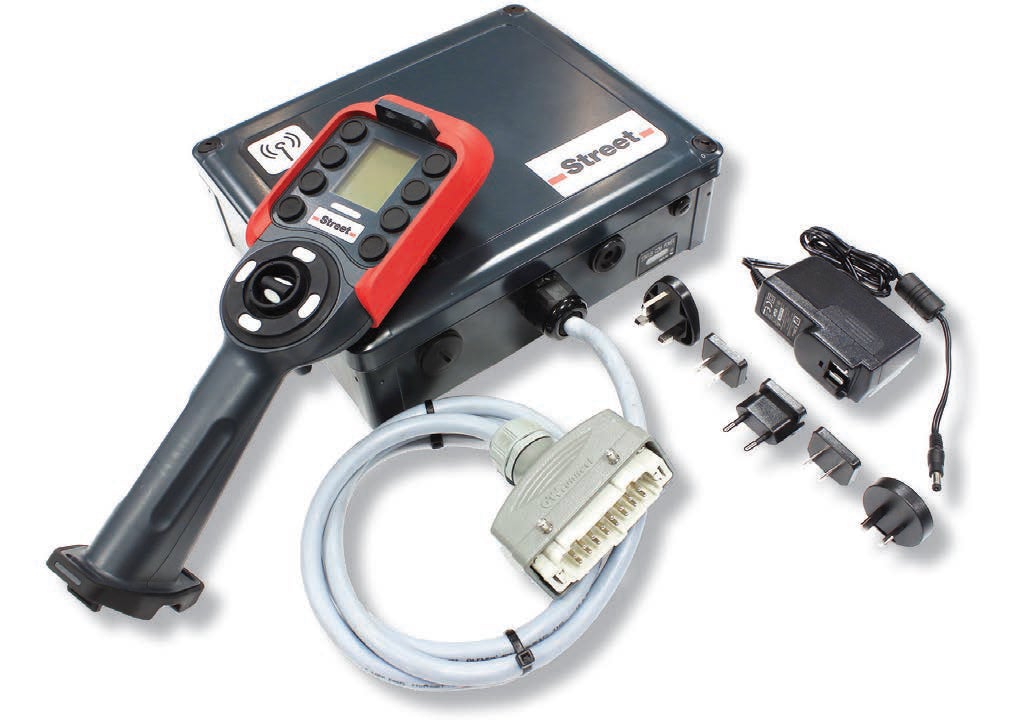
Installation is by simple plug-in; it can be installed on new cranes or as an upgrade on existing ones.
There are up to 6 configurable alarms, and optional alarm warnings with notifications through handset vibration.
Who among us has not bought a state-of- the-art all-singing all-dancing digital gizmo – something as simple as a doorbell camera even – then struggled to get it to connect, via Bluetooth, WiFi or indeed any means at all, to whatever device it is meant to be talking to and controlling?
The problem is clearly not confined to domestic applications – and if you are seeking to control your hoists and lifting devices that way, the last thing you want is a day or a week’s delay while the IT experts debug, reload, suck their teeth and tell you they think they have discovered where the problem lies, that it’s a software incompatibility issue, that sensor A is operating on a different system to receiver B and that a factory re-boot will probably with luck sort it out.
It is presumably for reasons like that, that Tele Radio has brought out a radio control system which makes a point of quick and easy installation. It is specifically designed for lifting and hoisting applications.
The set includes its Panther T29-12 remote control and R23 receiver, both of which come pre-wired from the factory for what Tele Radio describe as ‘easy plug & play installation.’ To which they add that the feature ‘greatly reduces installation time, providing valuable efficiency.’
The transmitter and receiver are both well-established products within the Tele Radio range. They have a proven track record in high-risk work environments, which makes them highly suitable for operations involving hoists and winches, overhead cranes, gantry cranes, and similar equipment. The set has a certified stop function to prioritize safety. It adheres to the EN 13849-1:2015 PLd/Cat3 standard and has received external certification from a recognized independent testing institute (Notified Body (NoBo)) in accordance with EU guidelines.
The Panther remote control transmitter is an upgraded successor to Tele Radio’s T19-2. It holds a PLd/Cat3 certification and operates on the globally compatible 2.4 GHz frequency, has 12 push buttons— four more than its predecessor—allowing control of up to 24 different functions. The transmitter is powered by a rechargeable Li-ion battery that gives over 150 consecutive hours of use and a range of up to 700 meters. It can be customized to meet specific user requirements, has an IP65 degree of protection and a robust housing against drops and impacts. The foil with symbols can be tailored to match the user’s branding.
The R23 receiver comes from the factory with wiring already in place for many standard applications, which as we have said streamlines the installation process. It comes standard with 15 relays. For installations requiring additional functionality, the non-pre-wired version of the R23 receiver is a modular unit that can be easily expanded without compromising safety-related features such as the stop function. Possible expansions include extra relays, support for various fieldbus protocols, additional inputs, analog outputs, and the option of an external antenna. The R23 receiver is seamlessly interchangeable with all Panther transmitters meaning that work can continue uninterrupted in the event of an unexpected incident. The combination of the R23 receiver with the Panther T29-12 saves time and money, says Tele Radio, without compromising on quality and safety.
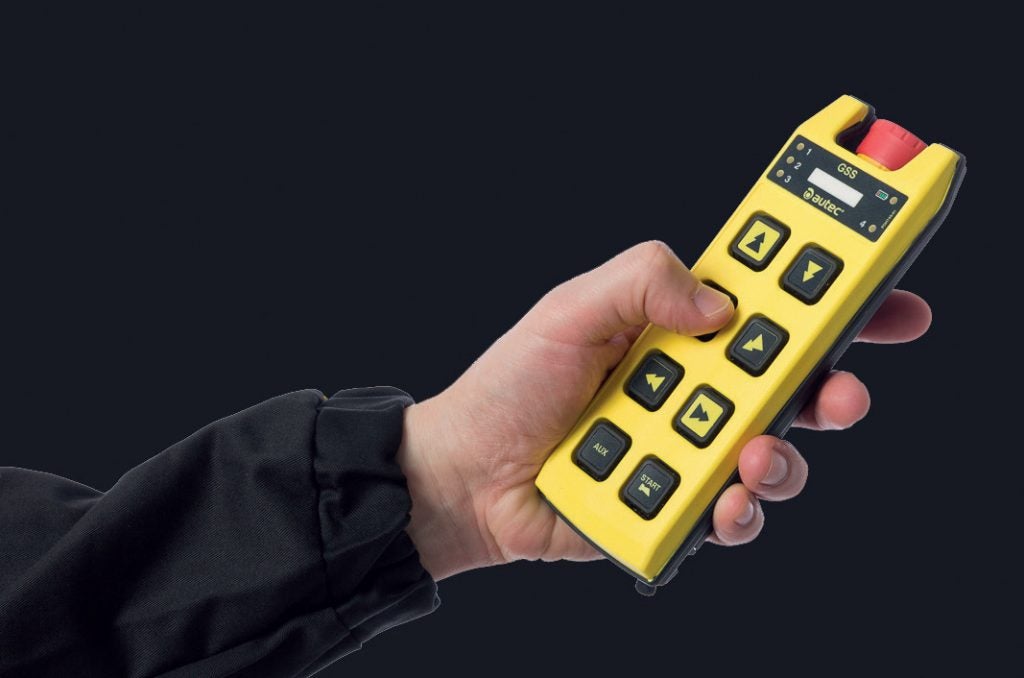
Autec are also stressing simplicity. Its LIFT pushbutton portable control station can be considered a fully-fledged and reliable cableless control system for hoists, gantries or even mobile vehicles if that is your requirement; it combines simplicity, they say, with innovation.
The connection between the pushbutton station and the machine occurs is 2.4 GHz Bluetooth in FHSS mode. This standard and worldwide communication mode gives reliable use of several device in the same area.
The system uses ‘My Lift Autec’, which is a free App that allows the most diverse configurations. Once you have downloaded it on your mobile device and have registered, the app can be used quickly and easily for different actions.
Among them are these: Should there be a malfunction, so-called “pairing” between the base station in use and a new pushbutton station can avoid machine downtime or the ned to ship the system to a service centre;
An automatic switch-off time can be set to preserve the battery lifetime when the station is not being used; the working range of the unit can be modified to prevent possible improper use by operators; and a PIN code can be set to control accesses to the station.
HBC Radiomatic has a compact, tailor-made hand-held radio control for industrial cranes in the form of its FST 314 micron M. It has three drives and trolley/ hoist preselection. Safety features include the ‘radiomatic zero-g and ‘switch, which can trigger predefined safety functions on the machine in emergency situations; should the activated transmitter be dropped by the operator, for example, the zero-g switch, comes into play and prevents potentially dangerous unintended movement of the hoist.
The system has the Merlin TUC (Transmitter User Card). This lets you easily and securely organize access rights to your cranes, protecting against unauthorized use. There is also the Merlin RMC or Receiver Master Card.
The radio systems come without pairing, but the RMC, says the company, lets you easily pair the transmitter and receiver yourself. You can use it to freely combine all merlin radio systems, and therefore reduce your variety of inventory. Similarly, if the radio transmitter is damaged, you can activate a spare transmitter straight away, even without the original transmitter.
The HBC proven catch-release feature is included at no extra charge. Also included is high-performing automatic frequency management Adaptive Frequency Hopping.
The HBC RadioMatic system, like those above, also has plug and play. ‘The radio system can be installed and commissioned in just a few simple steps and without complex wiring’ they say. The FSE 314 radio receiver is certified to UL/CSA 61010-1 and UL/CSA 61010-2-201, making it optimal for the North American market.
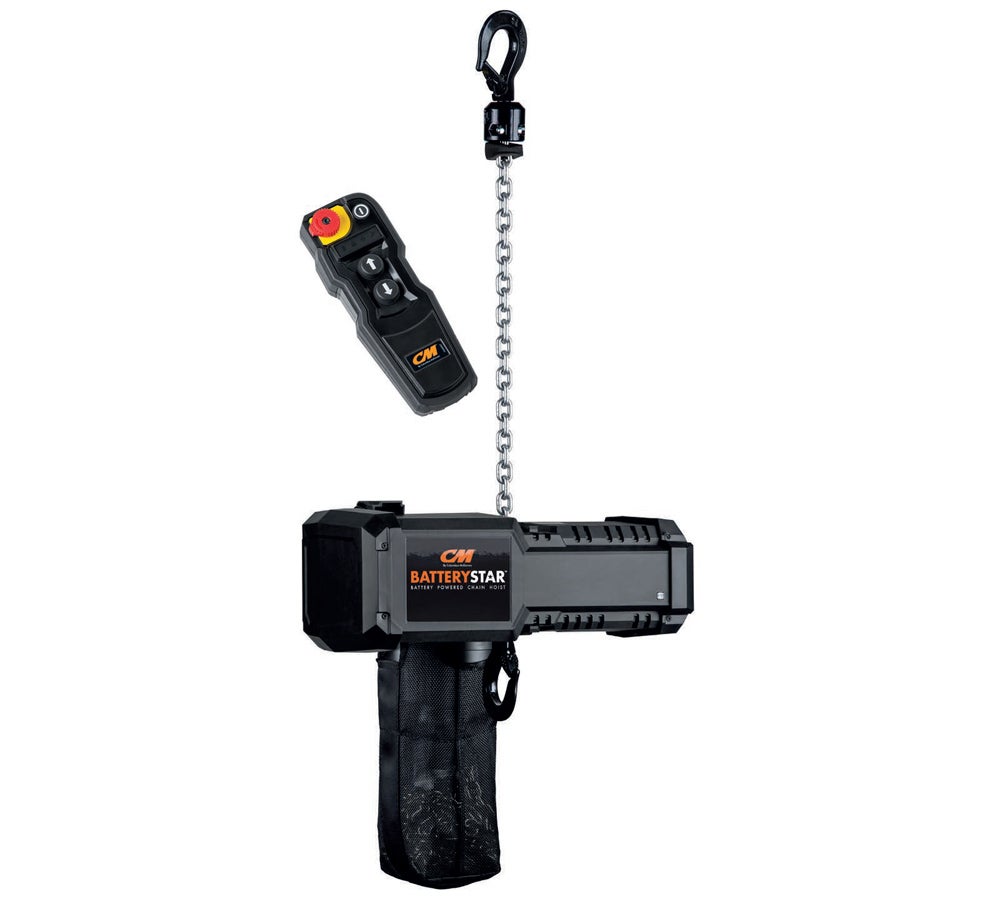
Battery lifting is up
It is seldom that a completely new concept arrives in the world of lifting; it is very seldom that it arrives in the apparently mature and simple world of the portable chain hoist. The chain hoist is a fairly basic machine that has been around since Roman times and has seen no fundamental change since then. It is susceptible to gradual and marginal improvements, certainly, as technology progresses; but what radically could be done to it while still keeping it a chain hoist?
Columbus McKinnon has come up with an answer. It has made it batterypowered. It is an obvious idea in retrospect; but then in retrospect all the best ideas seem obvious.
CM, experts in hoists, have combined with Milwaukee Tools, experts in lithium-ion and brushless motor technology, to produce this first of a kind. The BatteryStar hoist provides the lifting strength and speed of an electric chain hoist and the portability of a manual hoist without the need for time- (and effort-) consuming manual operation or access to a power source.
“The BatteryStar creates a new category of lifting technology,” said Mario Ramos, Sr. Vice President, product development and marketing, Columbus McKinnon. “One of the most exciting features of the BatteryStar is the portability it provides.
“With the standard 20 feet of chain it weighs in at only 46 lbs [YYY kilos], so this hoist can be transported and installed anywhere it is needed. It can be used in an inverted orientation, which eliminates the need to carry the weight of the hoist up to the anchor point; that improves ergonomics and reduces operator effort.”
The BatteryStar is powered by Milwaukee Tool’s industry leading M18 Redlithium battery, which customers are already using on job sites around the world.
The hoist reduces operator effort and fatigue with the elimination of manual effort. It also keeps the operator out of the load path, and therefore safer: this is because it has a wireless remote that can control the hoist from up to 60 feet away. The remote also has built-in intelligence that alerts the operator when the hoist is over capacity or if the battery has less than 25% of charge, so the battery can be replaced proactively.
The BatteryStar allows an operator to replace the battery quickly and easily for minimal downtime and interruption. Other features include a patentpending mechanical brake for added safety as well as true variable speed for precise lifting and improved efficiency.
The BatteryStar hoist has a 1-metricton lifting capacity with 20 feet of lift as standard and lifting speeds of 8 feet per minute. The hoist will be available for sale from Columbus McKinnon beginning in the Summer of 2024. It will be sold under the CM® brand in North America and Latin America and the Yale® brand in Europe, the Middle East, Africa, and Asia Pacific.