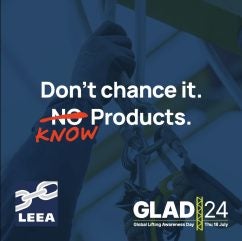
Alex Beltrao, Director of Compliance at The Lifting Equipment Engineers Association (LEEA), explains what lifting equipment related documentation needs to be provided by product manufacturers and suppliers to assure customers of legal compliance.
‘Operators across the globe place their trust in lifting equipment, so need assurance that the equipment supplied meets the standards and legislation. All lifting equipment should be of adequate strength, sound material, of good construction and suitable for the duty it must perform. It should be verified in accordance with the requirements of the standard being worked to. New equipment should comply with the essential health and safety requirements stipulated in the applicable legislation, and product standard where available, and issued with the required conformity documentation.
It is important for lifting equipment to carry unique identification for safety, maintenance, compliance with regulations as well as to help with tracking the equipment’s usage history, inspections and certifications.
Manufacturers and suppliers of lifting equipment and related inspection services are usually legally required or bound by product standards to provide the correct documentation to their customers. Yet confusion often surrounds what document should be provided in different circumstances. To provide clarity on the responsibility, let’s look at who, what, when, where, why and how for correct documentation requirements.
Who?
The documentation should make clear who the manufacturer and/or importer/distributer is, because applicable regulations may define different obligations and responsibility to these entities. In some cases, the involvement of a third party may be required to assess whether the product conforms with legislation.
What?
It should be clear in the technical documentation what the equipment type is, intended use, its material and its performance, (for example, its maximum load). To make the declaration of this information easier, most products in the market will have a standard or technical specification clearly defining these requirements. In this case, the manufacturer can simply declare compliance with the standard. This reference should be unambiguous and unconditional.
Some information can be of legal character and, in that case, it should be clear what the legal framework is. As an example, simply claiming that a product is CE marked (in Europe) is not enough. A construction product may be CE marked under the Construction Products Regulation, but machinery may be also CE marked under the Machinery Regulation.
When?
The documentation should be issued as soon as the product is placed on the market.
Where
The documentation should be in line with the legislation of the country where the product was placed on the market. However, when the product crosses the border to a different country, the documentation will then have to be in line with the legislation of that country. The European Economic Area is an exception to this as it is a single market with free movement of goods. This means that a product placed on the market and CE marked in any of these countries will be automatically accepted in any of the other countries.
Why
Documentation is important because it contains the technical information that will allow the user to safely operate the product and claim conformity with the relevant legislation, when relevant.
How
It is usually required that relevant information is in an accompanying document. However, technical information can be quite long and there is a risk that it may be lost or associated to a different product in the supply chain. To avoid this, manufacturers and legislations are increasingly adopting digital methods, such as a QR code in the product, to improve traceability to the correct information.
Look for the LEEA logo
Ignorance in relation to lifting in can result in severe consequences, so managers need to pay serious attention to their equipment and service providers. A simple step for end user operations seeking to mitigate risk when procuring lifting equipment is to look for the LEEA logo. This shows that the provider is a member of the Lifting Equipment Engineers Association. To become an Association member, the provider will have undergone a rigorous auditing process to uphold LEEA’s ‘gold standard’ that provides customers with the assurance of excellence and compliance to standards and legislation. LEEA works hard to make guidance more meaningful and effective, helping members to remain compliant, to manage risk, to maintain best practice and ultimately to enhance their know-how.’
Free guidance for best practice
LEEA strives to promote enhanced standards for lifting worldwide to make best practice become normal practice. Given that lifting is a common practice globally and that safe use of lifting equipment is vital, LEEA has made its Code of Practice for the Safe Use of Lifting Equipment (COPSULE) widely available to download free in PDF form as well as a searchable, interactive version at https://leeaint.com/copsule.
The COPSULE offers a regularly updated state of the art guide enabling lifting equipment users all over the globe and across different industries to meet legislative requirements. Covering a range of lifting machines, supporting structures and lifting accessories, it gives comprehensive guidance on safe lifting practice, authoritative information written by impartial industry experts using up to date industry practice and globally applicable guidance. Based on the highest levels of safety legislation, standards and industry practice – which collectively address all health and safety issues – the code meets the minimum safety requirements globally and is an essential source of information for everyone involved in lifting.