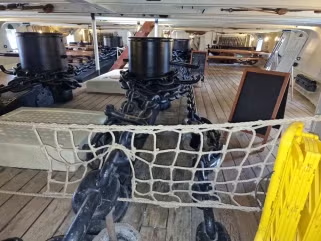
Dynamic Load Monitoring (UK) (DLM) and Lifting Gear & Safety (LGS) have combined to measure tension on mooring chains, over a three-month period, keeping HMS Warrior safely docked in Portsmouth, UK.
Southampton-based DLM is a specialist in the design, manufacture, repair, and calibration of load cells, load monitoring, and cable working equipment for the offshore, renewable energy, marine, subsea, and lifting and rigging industries. LGS, which has a facility at nearby Fareham, specialises in the hire, sale, and service of lifting, marine, and safety equipment.
LGS accepted a scope of work from a longstanding customer that handles mooring and marine construction in the Portsmouth area. Portsmouth Historic Dockyard had a requirement to measure the tension on mooring chains that keep HMS Warrior, the crown jewel of the Victorian Navy, safely docked. The iconic ship is reimagined exactly as she was in 1863 and is still afloat over 160 years later.
“We have been working with LGS for a number of years, on various projects serving a variety of important industries. This latest project is a good example of us providing distributors with technical support, while they oversee equipment supply and project management in order to provide a combined service at the point of use,” said Ryan Phillips, technical manager, DLM.
Stuart Wilson, business development manager, LGS, added that DLM has supported them as a supplier by attending the job site and complementing its skills in rigging with their technical knowledge in load monitoring.
“Without the data-logging technology and the Bluetooth connectivity to a laptop, we would have had to organise manual logging of data. DLM’s service support and products saved us and our customer time, money, and effort,” he said.
DLM provided two telemetry dongles; two 100t capacity tensile links; two laptops, complete with the TW-3.0 toolkit installed; two uninterruptible power supplies, to keep the system running even in the event of a loss of power; and two TW-3.0 handhelds, which served as a further failsafe system.
LGS provided four 120t capacity shackles and carried out installation of the load cells aboard the vessel. Lever hoists were used to create slack in the anchor chain, before high-modulus polyethylene (HMPE) grommets were used to attach the chain to the load link.
“As part of our standard product range, the selected fleet of equipment provided an ideal solution for this mooring chain application. The dongles are designed to be used alongside the TW-3.0 toolkit, and together they provided the end user with all the tools required,” added Phillips.
Tests were ongoing for three months, giving Portsmouth Historic Dockyard a large volume of data, gathered over a significant timeframe, which can be used to analyse the load being pulled on the mooring chains. DLM’s Phillips was on call for the duration and visited the ship on multiple occasions to provide in-person support.
The dockyard remained open to visitors throughout; extra precautions were taken due to the risks associated with working in a public space.