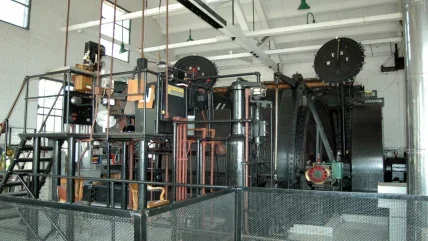
Chain hoists, manual or powered, look simple: a chain, a sprocket or two and a hook, and you are most of the way there. They may seem a mature technology: it is not as though the ever-accelerating advances in digital control of big data can do much for a hand-pulled chain that runs over a sprocket then down to a load. But even in manual chain-hoists advances and improvements are happening and new products are announced. The ones we describe here have almost all been introduced since the beginning of the year.
We can start with Oz lifting, who are Minnesota-based rather than antipodean. In February this year it launched two spark resistant products – one a chain hoist, the other a push beam trolley, which can support it. The target applications are in hazardous environments where dust particles or gas make a potentially explosive atmosphere. Typical markets include oil and gas, wastewater, paper, mining, and others.
The hoists have been launched as a complete capacity range – 0.5 ton, 1 ton, 2 ton, 3 ton, 5 ton and 10 ton – that covers most likely applications. As with other manual chain hoists in the Oz catalog, 10 ft., 15 ft., 20 ft., and 30 ft. heights of lift are offered as standard but custom lengths are available on request.
“The new hoists and the trolley go hand in hand,” says Steve Napieralski, president, Oz Lifting. “We saw a need in the market for spark resistant manual chain hoists, and if you are going to offer them, you typically will be hanging the equipment from a trolley that also needs to be spark resistant. However, the products can work independently of each other.
“You might have a situation where the manual chain hoist doesn’t need to travel down an I-beam and is fixed in one location. And the trolley can accommodate either one of our manual spark resistant hoists or one that is powered.
“The term ‘explosion proof’ usually applies to electrically-driven products; ‘spark resistant’ is for those operated mechanically” he says. Both the chain hoists and trolleys are manufactured in compliance with the EU’s explosion-proof standard ATEX94/9/ EC and Machinery Directive 2006/42/EC. They can operate at explosion levels EX II2 GD c IIICT135 C and are suitable for use in Zones 1 and 2 (gas) as well as Zones 21 and 22 (dust).
The hoists feature a unique hand wheel design; minimal load lifting effort; fully enclosed gearing; stainless steel or copper components; and totally enclosed gearing. They are suitable for pulling, as well as lifting, applications. The push beam trolleys have copper-plated trolley wheels and lifting bale; copper riveted identification tags; precision ball bearing trolley wheels; and anti-drop plates. They are compatible with most I-, S-, and W-beams. Both products come with individual test certificate and serial number.
Also in February, Kito expanded the range of its CX series of hand chain blocks. The series as a whole is designed to be extremely lightweight, with perfect handling and precise positioning of the load. The 250kg and 500kg capacity models were already available. The new addition, the CX010, extends the range to one ton.
“Launching it means we are answering a great demand,” a company spokesman said. “Almost all users wanting compact hand chain block for mobile applications choose by two criteria: the dead weight and the load capacity. It is because you need as little weight as possible and as much power as possible at the same time. That is why we designed the CX range. CX blocks are small and compact, easy to carry, easy to handle, and they fit in tight spaces. The newest one, the CX010, despite its load capacity weighs just 7.3 kg.”
Its construction, he says, is though it is small it is strong. This big brother of the range has a housing of lightweight aluminium. Inside is a two-stage precision gear; a heat-treated steel frame, serves as a stable bearing for the gearwheels, which are cold-forged for maximum and constant performance. The chain sprocket is high-quality cast and precisely matched to the gearbox so that the nickel-plated load chain is carried flawlessly.
Kito has tried to consider all possible risks that might occur during product use. An overload limiter comes as standard. As small manual chain hoists are often transported and set up in different, sometimes confined and hard-to-access, places, the new ‘Twist Checker’ is also part of the standard equipment. It is a small tool to determine quickly and easily if the load chain is twisted or if the hoist can be used immediately. It would seem a genuine improvement for the daily work routine.
Kito has brought interesting changes to the manufacturing process. Instead of a complex manufacturing line, each unit is put together by a single expert who is digitally guided step by step. Cameras scan every movement during the construction and detect if a component is assembled incorrectly. The result is quality that combines the best of hand-made and automated production.
Italian company Misia has been selling its small and powerful MH chain hoist series since 2013. It is currently selling more than 400 units annually. Durable, safe, and easy to use, the company claims a high quality to price ratio as one rationale of its success. Its range covers capacities from 125kg to 2t, in four configurations for supporting the hoist: by eye-hook, open hook, manual trolley or electric trolley. Standard lift is 3m, but customisation is available. An end travel limit switch is always included and motors conform to IP55 as standard.
Moving on to powered chain hoists, here the new ubiquity of digital control and data-monitoring is beginning to be felt. Columbus McKinnon has just announced, in March this year, the first electric chain hoist on the market to have remote monitoring and wireless connection. It may prove to be a game-changer. And just before that, in yet another February launch, Demag announced it is expanding its DCBS chain hoist series with a balancer function that it introduced last year. The balance function means loads can be lifted or lowered intuitively, – that is, the operator can use the control handle on the hoist, or can push down on, or pull up on, the load directly with their hands. The load will then move as desired: it feels just like lifting the load by hand – except of course that the load seems much lighter.
Until now, the DCBS has enabled users to handle loads weighing up to 160 kg easily and safely. The range is now being expanded to a load capacity of 250 kg, resulting in a wider range of applications.
Earlier this year, Tiger Lifting introduced its twin hook air hoist, which has two chain falls with hooks for alternate working.
Its TAH-M series of air hoists were originally designed for mining applications and are suitable for both pulling and lifting operations. They are now deployed globally in various marine and industrial applications.
Tiger point out some of the advantages of pneumatic, compressed-air, power for hoists. They are ideal, it says, for tasks that need rapid lifting speeds and constant use. A key benefit is they have a 100% duty cycle – which is significantly higher than most electric hoists. A typical electric chain hoist might have a 25% duty cycle, meaning it can be operated continuously for only 15 minutes in a one-hour period. Hoists that are powered by compressed air do not have this limitation; they can remain in constant use until the job is done.
Tiger’s twin hook models are available in various configurations. The TAH21M has each 2t hook in single fall; the TA33M comes in a 3t/3t configuration, with two three-ton hooks, again each on a single fall, and a 3t/6t version; in this, one of the hooks is of 6t capacity and on a double fall. An integral differential-pressure load limiting valve automatically prevents the operator lifting a load of more than 125% of the working load limit, and non-asbestos self-adjusting disc brakes apply automatically when the air supply to the hoist is shut off. Hooks can be standard, closed-eye, grab or self-locking.
“The twin hook air hoists have extensively been used in the mining industry, particularly for hauling applications. Customer enquiries from shipyards indicated a need for twin hook air hoists to also be introduced in other industries,” said David Inglis, managing director, Tiger Lifting. “Feedback has been really positive across the whole air hoist range. Operators love the precise control that the range offers. The ability of the hoists to be used for fleeting, cross hauling and oblique pulling has received great praise along with the safety aspect of the load limiter. And our maintenance partners are finding the hoists exceptionally easy to maintain.”
The humble chain hoist, it would seem, is going up in the world.