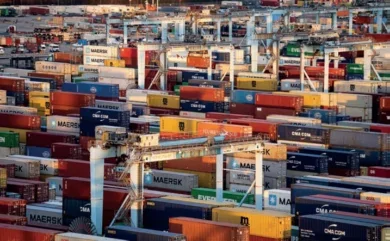
Automation is transforming machines from all corners of the manufacturing world — and cranes and hoists are no exception. Remote operation, advanced safety features and integration with Industrial Internet of Things (IIoT) technologies are just some of the benefits you can expect when you integrate these traditionally manual machines with new, cutting-edge automated systems. Keep in mind, however, that the addition of sensors, controllers and communication networks increases the already lengthy list of demands placed on crane cable management systems. Not only must these devices be able to efficiently organize a wider variety of cable components, but they must also prioritize safe and reliable operation despite the harsh operating conditions associated with crane and hoist applications.
Let’s explore how modular cable carriers made from highly engineered plastics can successfully support automation while addressing the typical challenges associated with crane operation — specifically, indoor and electric overhead traveling (EOT) cranes in production plants. We’ll also discuss the ways these technologies offer a compelling alternative to festoon cable systems, overhead crane busbar systems and cable reels.
THE DRAWBACKS OF TRADITIONAL FESTOON AND BUSBAR SYSTEMS
Although they have their place, festoon and busbar systems have limitations when it comes to efficient, reliable cable management in many crane applications.
In traditional festoon systems, cables and hoses hang unprotected on the crane. Able to swing freely, they’re prone to tangling or getting caught on the structure, leading to downtime and costly repairs. In outdoor facilities, cables also face wind, weather, varying temperatures, sand, salt and other adverse conditions. In addition, festoon systems require regular maintenance to lubricate the cable trolleys and ensure the motors, shock cords, tow ropes and other parts are operating wear-free. Because the cables are clamped in bunches at each trolley, adding or replacing cables is also a time-consuming hassle.
In addition to their high maintenance requirements, festoon systems consume a lot of space on the crane rail, requiring roughly 115 percent of the travel length in cable and limiting the amount of crane travel.
Electrical busbar systems, which supply power to the crane via metal conductor bars, are even more labor-intensive than festoon systems, requiring regular inspection and maintenance.
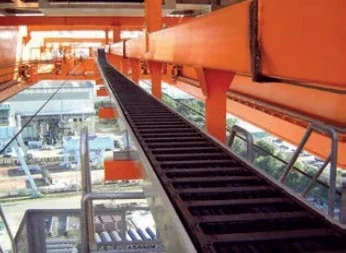
For example, personnel must regularly inspect and replace the collector shoes installed on the collector arms once they wear out, requiring the entire system to be powered down.
Despite their complexity, busbar systems are also limited in their functionality. Each conductor requires its own conductor bar and collector, meaning it’s usually not feasible to install more than eight conductor bars on a single system. For this reason, busbar systems are limited to power and control cables only, with additional cables and hoses requiring guidance by a separate system.
MODULAR, COMPACT AND INNOVATIVE CABLE CARRIERS
Modular cable carriers, or energy chains, made from highly engineered plastics overcome the various challenges faced by traditional festoon and busbar systems in indoor and EOT crane applications. An example is the igus e-chain system, in which the cables are fed into the e-chain in the middle of travel. The e-chain is then pushed or pulled halfway.
These modular systems can accommodate energy, data, air and liquids all in the same energy chain, enabling them to accommodate Ethernet, sensors, camera systems and other IIoT technologies and supporting plant owners in their automation efforts.
Here’s a rundown of some of the additional benefits of e-chain cable management systems:
- Space savings. Modular cable carriers require roughly 50% less cable and 10% less structural steel than festoon systems. They also need about 800 millimeters (mm) of system height compared to the 5,000 mm required by festoon systems in a 100-meter application. Thanks to their efficient, compact design, e-chain systems can operate in confined installations.
- Dynamic. Cable festoon systems tend to reach their limits at speeds of 240 meters per minute (m/min) and accelerations exceeding 0.8 meters per second squared (m/sec2). On the other hand, modular e-chain systems can be operated at speeds over 600 m/min and with an acceleration over 2 m/sec2.
- Ease of installation and maintenance. Unlike labor-intensive and downtimeprone festoon and busbar systems, e-chain systems are virtually maintenance-free and can run for years without an issue. Due to their modular nature, they also make it easy to replace or add cables without having to overhaul the entire cable management system. In addition, e-chain systems offer easy side-mounting capabilities for girder cranes and indoor hoists via the Guidefast steel trough system, saving up to 80% installation time.
- Safe, secure cable guidance. In e-chain systems, cables are safely guided in the energy chain and can’t get caught on the crane structure unlike the cables in festoon systems. And, whereas busbars expose bare-loaded conductors to potentially hazardous plant conditions, e-chain systems incorporate standard electrical cables that are insulated from the surrounding environment. For particularly hazardous locations, e-chain cables are even available in a special electrostatic discharge (ESD) material, further increasing operational safety.
- Flexible and easy to customize. Modular cable carriers are easy to customize according to their application. For example, they offer many mounting options — on the side or top of the crane, for example — while their Extension Link feature enables operators to add an additional link, which is connected to the two outer bands via crossbars. This Extension Link increases the possible load capacity of an E4 e-chain series.
The e-chain systems also come in many versions depending on the crane application, including small and lighterweight energy chains, long-travel and heavy-duty energy chains and closed versions to protect cables from debris, and “smart” energy chains with self-monitoring and breakage-detection capabilities.
ENERGY CHAINS IN ACTION: RETROFITTING THE PORT OF VIRGINIA
Energy chains provide an efficient, hassle-free cable management system for transferring power, control and fiber optic cables from a fixed point to a moving point. In ship to shore (STS) cranes, they transfer cables from the crane structure to the moving trolley itself. These applications have their own set of demands, requiring reliable cable management systems that eliminate unnecessary maintenance and downtime in modern container ports.
When it comes to traditional festoon systems, a damaged trolley wheel or other component will cause the entire system to fail, having ripping effects throughout the port. Technicians will need to stop unloading the ship, fix the broken festoon system and then get the crane up and running again so that the ship can travel to its next port of call once it’s fully unloaded.
In addition, the vessel windows at container ports are tighter than ever. Vessel lines need to get in and out of the berth and unload the containers as quickly as possible. At the same time, the terminal operators need to keep the berth full at all times; as soon as one ship has finished, it’s time for another ship to take its place. Any delay will therefore cost a significant amount of money for the ships — not to mention all the logistical headache.
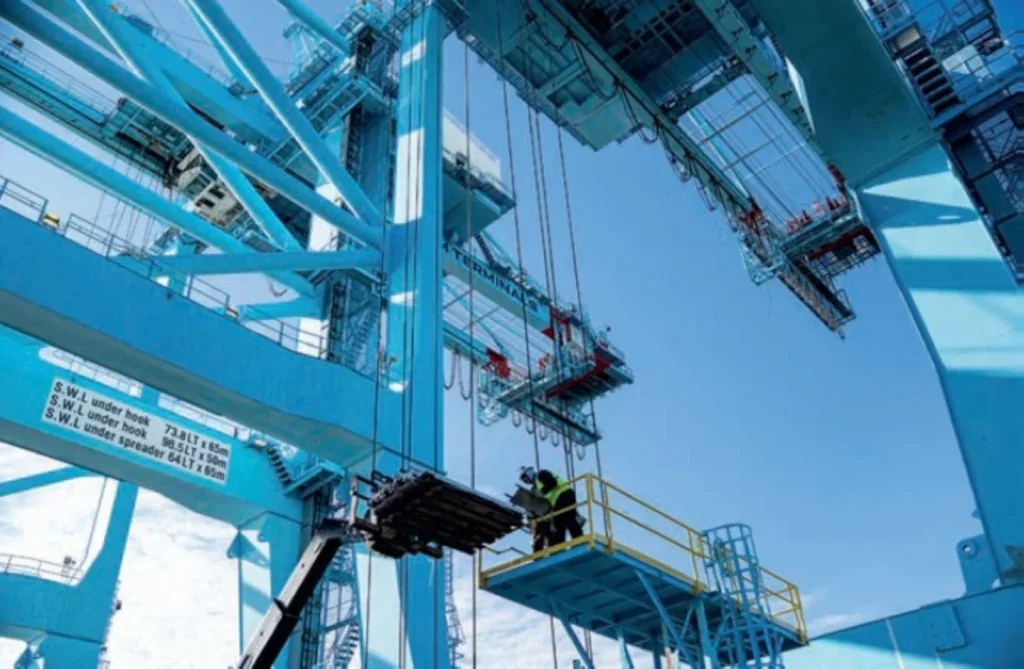
For these reasons, energy chain systems have emerged as a reliable alternative to many festoon systems in container ports. In fact, the first e-chain installed on a North American STS crane was at the Port of Virginia. Prior to implementing the e-chain system, the port’s festoon cables constantly swung into and tugged on each other, placing tension on the cables that eroded the cables’ health. Repairing the large, dangling cables 200 feet into the air also put personnel in a precarious situation.
Overcoming these challenges, igus retrofitted the festoon system with an e-chain system. This process involved fabricating steel brackets and beams that would be installed onto the girder, as well as platforms that would enable technicians to access the energy chain once it was installed. The technicians also set up the trough on the brackets and installed the chain. With assistance from a crane company, the technicians brought the chain up and pulled it through the trough. From there, they anchored down the fixed-end and installed the moving end to the tow arm. Igus also performed full test runs to ensure the system ran smoothly.
Since this successful application at the Port of Virginia, many STS crane companies have since seen the value of the energy chain system as a reliable, maintenance-free cable management system that can keep up with the demands of modern ports.
POSITION YOURSELF FOR THE FUTURE — TODAY
Cable reels, festoon systems, busbar systems and other traditional crane cable solutions make it difficult to add or reconfigure components, keeping them a step behind ever-advancing IIoT and automation technologies. The right cable management system, however, is adaptable and can provide you with the flexibility you need to take advantage of new technologies while maintaining a competitive edge.’