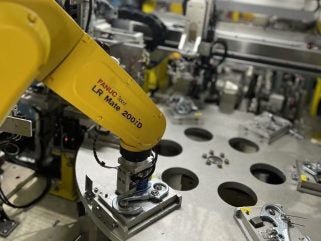
As YOKE Industrial Corp. continues to expand its fleet of robots and recruit new talent, it remains at the forefront of a manufacturing revolution that blends robotics, digitalization, and human ingenuity to create a more efficient and sustainable future. The company’s 56m² factory in Taiwan is one example of how technology can work hand-in-hand with a skilled workforce to produce industrial lifting equipment with quality and efficiency.
In addition to embracing new technologies, YOKE’s commitment to continuous improvement is reflected in its employee-driven suggestion program, which was introduced in 2021. Every month, staff members are encouraged to submit ideas that could help reduce production costs, improve quality, enhance efficiency, or drive innovation. The top proposals are rewarded and highlighted across the company, ensuring every employee has a voice in shaping the future of the business. This initiative underscores YOKE’s belief that technology and human creativity can work together to push the company—and the manufacturing industry—forward.
Since adopting robotics in 2011, YOKE has heavily invested in automation, currently operating 71 automation systems and 108 robotic arms, including those made by global leader Fanuc. The company’s US$30 million investment has paid off, proven by its production of 20 million units per year, with robots logging more than 5,000 hours of operation in October 2024 alone. While the factory has become a symbol of technological advancement, YOKE has never viewed automation as a substitute for human labor; instead, automation is seen as a tool to enhance the workforce’s capabilities and improve overall operational performance.
Steven Hong, the president of YOKE, explains that the company’s commitment to automation is rooted in a vision that combines technological progress with the human element. “We are integrating both robotics and digitalization to create a competitive edge in manufacturing,” Hong says. “The goal is to improve efficiency and product quality, while also providing our employees with the opportunity to work with the latest technology, which in turn helps us stay competitive in the future.”
The company’s smart factory is an evolving testament to this philosophy. What began with simple robotic arms stacking finished products onto pallets has expanded into an interconnected system of Automated Guided Vehicles (AGVs), optical inspection systems, and digital platforms that provide real-time production data. The factory is constantly undergoing updates, with a dedicated team continuously evaluating new automation possibilities and working to optimize production processes through data-driven insights. “The pace of automation will never stop,” Hong says underscoring that YOKE’s journey of innovation is ongoing.
But while the company’s robots and automation systems drive its production, YOKE has also prioritized the development of its human workforce. The integration of robotics has not led to job reductions; instead, it has shifted the roles of workers toward more complex, technology-driven tasks. Employees are now responsible for overseeing automated systems, managing production lines, and designing the fixtures and molds used in manufacturing. These changes have allowed employees to transition from repetitive, manual tasks to higher-value roles that require problem-solving and technical expertise.
This shift is one of the key reasons YOKE continues to attract new talent, especially younger generations who are eager to work in environments that foster innovation and skill development. “The younger generation is more inclined to engage with new technologies,” Hong notes. “A smart factory environment gives them the chance to challenge themselves, learn new skills, and contribute to a more dynamic, fast-paced work culture.”
For YOKE, automation and digitalization are not just about improving productivity—they are integral parts of a larger strategy to create a sustainable, future-proof business model. Hong stresses that the integration of smart sensors, cloud-based platforms, and data analytics are critical to this vision. “By combining automation with digitalization, we are not only optimizing production but also improving our ability to make data-driven decisions,” he explains. “This allows us to remain competitive in a rapidly changing industry and ensure that we are always on the cutting edge of manufacturing technology.”
YOKE’s partnership with Fanuc has been instrumental in realizing this vision. As one of the world’s largest industrial robot manufacturers, Fanuc has provided YOKE with the tools necessary to automate everything from stacking to precision inspections, enabling the company to maintain high standards of quality and stay ahead of competitors. Hong believes that strong partnerships are key to unlocking the full potential of automation. “We trust that Fanuc can provide the right solutions for each of our manufacturing processes,” he says. “Together, we are working to drive the next generation of industrial manufacturing.”
As YOKE continues to expand its use of automation and recruit the next generation of skilled workers, it remains a shining example of how robotics, digitalization, and human ingenuity can come together to create a more efficient and sustainable future for manufacturing. By fostering a work environment where technology and people grow together, YOKE is not only redefining how lifting equipment is made, but also how a modern factory can operate in the digital age.