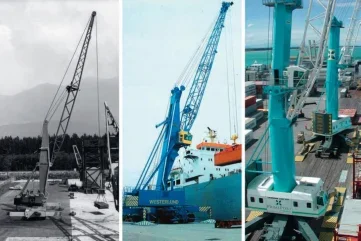
Liebherr has developed its flagship mobile harbour crane over five decades of changing industry demands, standards, and trends. Upgrades over the years have served to accommodate larger and heavier cargoes, while maintaining high standards in performance and reliability.
In recent years, all-electric cranes optimised for energy efficiency and sustainability have come to the forefront. And the newest LHM series focuses on advanced electronics and sensor technology for future automation.
The legacy and evolution of the Liebherr mobile harbour crane couldn’t be more illustrative than with the LGM 1130 introduced in 1974. Mobile harbour cranes in those times were often used as backup for STS container cranes, positioned under the container crane itself. This was made possible through a folding-tower design that allowed the LGM to fold its boom, drive underneath the container crane, and erect itself again to support the STS. The LGM was introduced when containerisation was becoming increasingly dominant, and global trade routes were expanding.
Mobile harbour cranes are renowned for their flexibility and versatility, and this trait was reinforced over time. Capable of handling various applications such as bulk handling, container handling, and heavy goods transport, these cranes needed to offer more efficiency compared to other port equipment.
The rubber-tired undercarriage provides excellent load distribution, eliminating the need for extensive quay preparation and easy transition to new projects or ports.
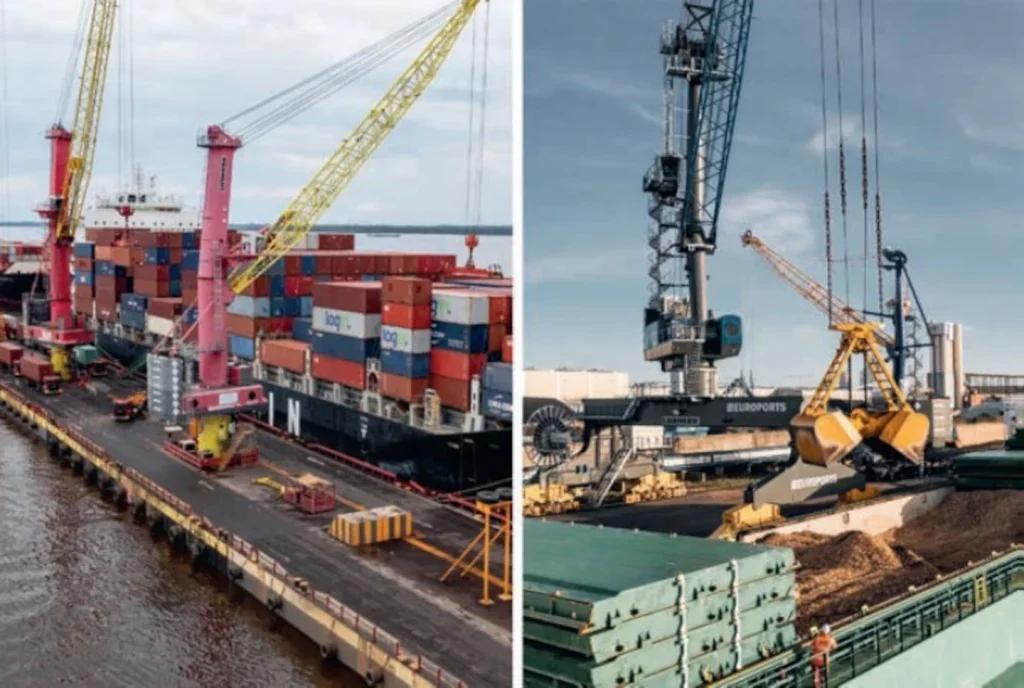
With the introduction of the LHM 250 in 1996, new benchmarks for efficiency and innovation were set. This crane featured an X-shaped undercarriage and individually steerable wheelsets, allowing for improved manoeuvrability in increasingly narrow port environments. The LHM 250 was also the first Liebherr mobile harbour crane to incorporate telemetry, enabling remote monitoring and data transmission. This innovation was crucial as the industry demanded greater efficiency and larger cranes to handle the growing size and capacity of container ships.
“Over the years, Liebherr has continuously adapted to market demands, introducing groundbreaking models that have had an impact on port operations,” said Sebastian Simon, product manager, Liebherr Rostock. “Our commitment to innovation and quality has made us a trusted partner in the maritime industry.”
The LHM 500, launched in 2002, continued this legacy with its robust design and increased focus on environmental sustainability. The crane’s tubular tower and 4-chord boom were designed to enhance steelwork reliability, extending the crane’s lifecycle and reducing its environmental impact. In 2010, innovation saw a shift towards the integration of digital technologies and automation in port operations, with the LHM 550 incorporating advanced telemetry and other features.
Enhancing technical capabilities is just one aspect of improving logistical operations. Maximising limited space is another, and portal crane solutions excel in this area. Liebherr’s LPS cranes have been pivotal in port operations for decades. Their rail-mounted configurations and spacesaving portal undercarriage, combined with versatile mobile harbour crane technology, ensure efficient cargo handling in tight locations. The LPS series, including models like the LPS 420 E, epitomises innovation and practicality, handling containers, bulk goods, and heavy lifts up to 308 tons with the LPS 800.
The assistance systems that launched soon after the LHM 550 helped to evolve the logistical capabilities of mobile harbour cranes. SmartGrip, launched in 2014, is an intelligent system that optimises grab filling rates through self-learning. It offers higher performance and nearly eliminates overloads. Analyses showed only 70% of the grab’s capacity was typically used due to factors like suboptimal angles and varying material densities.
SmartGrip adjusts automatically, recognising bulk density, compression, granularity, and conditions like depth of impression and grab type. It optimises filling to maximum capacity within seven cycles, ensuring the rate exceeds 70% from the second cycle.
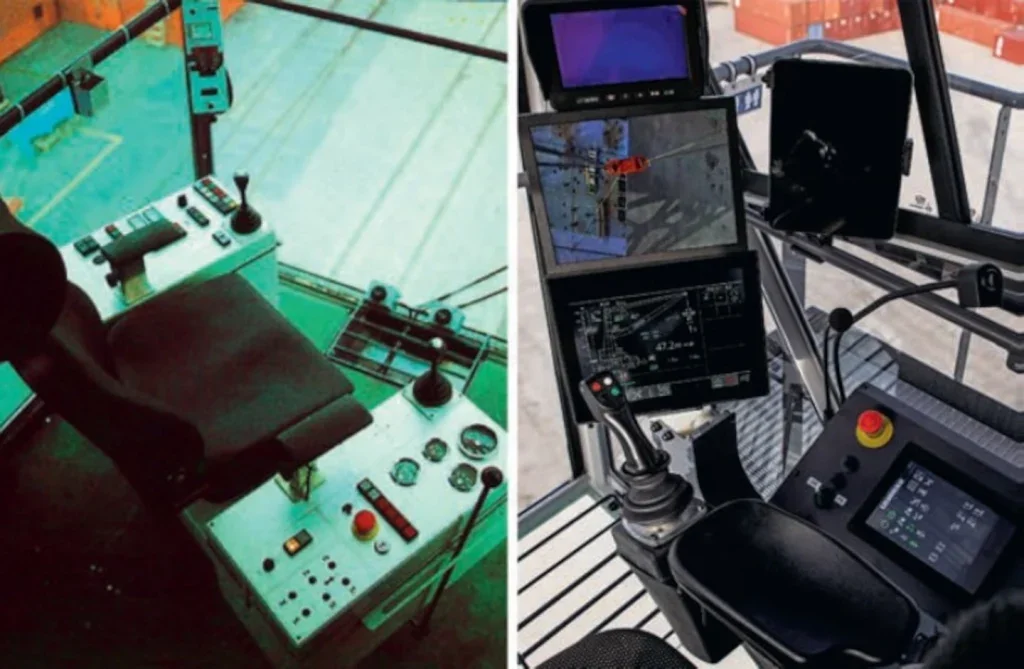
The need to handle larger and heavier cargo led to a modification in mobile harbour crane performance. To accommodate heavy-lift project cargo, particularly from the wind industry, two LHMs must work together. Sycratronic was developed and released in 2004 to maximise performance and turnover by improving the safety and efficiency of tandem operations. It connects two cranes via a Controller Area Network (CAN bus), allowing their Programmable Logic Controller to communicate and synchronise movements. This enables the leading crane to provide input on slewing angle, hoisting height, and load weight to the following crane, which then adjusts automatically. Hybrid technology is playing a crucial role in modernising port logistics by making operations more efficient and environmentally friendly.
One of the standout developments in port logistics over the past decade is the increasing demand for a more sustainable infrastructure. In 2019, the LPS 420 E marked a significant milestone as Liebherr’s first all-electric portal crane. All crane movements – like luffing, hoisting, slewing, and travelling – were done by electric motors, no hydraulics required. The LPS 420 E was designed for high-efficiency bulk and container operations, reflecting the industry’s increasing focus on reducing CO2 footprint – goals for the next half-century.