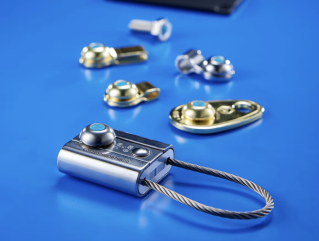
The shift away from traditional hard stamping methods in the rigging and safety equipment industry is set to bring far-reaching benefits, according to Andy Charlesworth and Richard Oldknow of YOKE Industrial Corp. While hard stamping—a technique that leaves an indentation on products for identification—has been a long-standing practice, it remains an outdated method in an industry that is increasingly embracing advanced technologies such as the Internet of Things (IoT), Artificial Intelligence (AI), and Blockchain. Despite the industry’s technological advancements, hard stamping remains widespread, with workers still using it to mark batches of shackles and prepare individual certifications.
The drawbacks of hard stamping are significant. Not only is the process time-consuming and accompanied by extensive paperwork, but it can also damage products. Without clear guidance on where to stamp or the proper tools to use, the stamping process can introduce stress raisers, making products more prone to premature failure. Additionally, hard stamps often result in markings that are difficult to read, with inconsistent font sizes and sharp-edged impressions. The practice also extends to color-coded tie-wraps, commonly used to mark equipment for inspection periods. However, these markers do not ensure the equipment has undergone the necessary pre-use checks.
In response to these challenges, YOKE Industrial Corp. has championed the move toward Radio Frequency Identification (RFID) and Software as a Service (SaaS) technologies. According to Charlesworth and Oldknow, the company made a pivotal decision several years ago to fully digitalize its product range, where feasible, rather than test a limited selection of RFID-enabled items. This commitment to digitalization aligns with YOKE’s broader mission to provide high-quality rigging and safety equipment that enhances safety and streamlines inspection processes, while also preparing for the upcoming EU Machinery Regulation.
The Machinery Regulation, which comes into effect in January 2027, will supersede the EU Machinery Directive 2006/42/EC, unifying the requirements across all EU member states. One of the key changes under the new regulation is the requirement for original product certifications and manuals to be provided digitally, signaling a move toward a more environmentally friendly and paperless future. YOKE’s approach to digitalizing its product range is designed to remove the need for paper records, with the product itself carrying a digital history from its initial supply through to its end of life.
RFID technology, long used in industries like agriculture for livestock identification, has posed challenges for adoption in the rigging sector due to manufacturing complexities. However, YOKE has overcome these hurdles with innovations in Near Field Communication (NFC) technology. By incorporating NFC-enabled RFID chips, YOKE ensures that its products, from shackles to snatch blocks, are equipped with durable tags capable of withstanding extreme conditions. These tags, known as BlueSupra, feature the SupraNano RFID chip, which can be pressure-fitted directly into steel or applied to products via retrofit methods. The chips are rigorously tested for impact, temperature resilience (ranging from -30°C to +125°C), and water ingress, making them reliable in harsh environments.
The RFID technology, in combination with SaaS from providers like RiConnect, allows users to access detailed information about the equipment simply by scanning the tag with a smartphone. This information includes the product’s unique identification number, brand name, registration date, and documentation, ensuring that all essential data is readily available for safety and regulatory compliance. YOKE even provides these RFID chips to competitors, helping to standardize the industry and overcome barriers to adoption.
The benefits of RFID technology extend beyond product identification. It also addresses critical challenges related to inspection and reporting. While legislation requires manufacturers to mark lifting equipment with unique identification numbers if specified, user legislation mandates that duty holders conduct thorough inspections and provide reports that clearly identify the equipment. Using RFID, each item can be easily traced, ensuring that inspections are accurately documented and defects can be addressed efficiently.
As industry practices continue to evolve, the adoption of RFID and SaaS solutions offers a more efficient, cost-effective, and environmentally friendly alternative to hard stamping and color-coded tie-wraps. These digital technologies eliminate the risks associated with hard stamping, such as damage, readability issues, and logistical challenges during inspections. Furthermore, as inspection companies move away from traditional pen-and-paper methods and equip their staff with mobile devices, RFID provides an invaluable tool for inspectors, reducing the time spent deciphering hard stamps and increasing the accuracy and speed of inspections.
In the near future, as the Machinery Regulation comes into force, companies like YOKE Industrial Corp. are poised to lead the industry toward a more advanced, safer, and digitally integrated approach to equipment safety and regulation compliance.