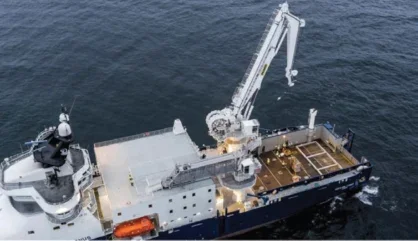
Offshore lifting is very different from onshore lifting. For one thing, the lift height is different. The continental shelf is generally 100-200m deep. Onshore, such heights are the province of tower cranes, and even they can only lift to 70-80m unless they are tied in along the way to the building they are constructing. And subsea lifting is by no means confined to continental shelves. Shell’s Perdito Spar platform, in the Gulf of Mexico, operates at a water depth of 2,450m. It is fed by a network of pipes 44km long on the ocean bed. Those pipes had to be put into position somehow.
So lifting (and lowering) heights can be very great indeed. That means that lift ropes must be very long, and so will need very large-diameter drums to hold them. They will also be very heavy: 100m of six-strand 100mm wire rope weighs around 4.4t; 1,000m of it weighs therefore around 40t.
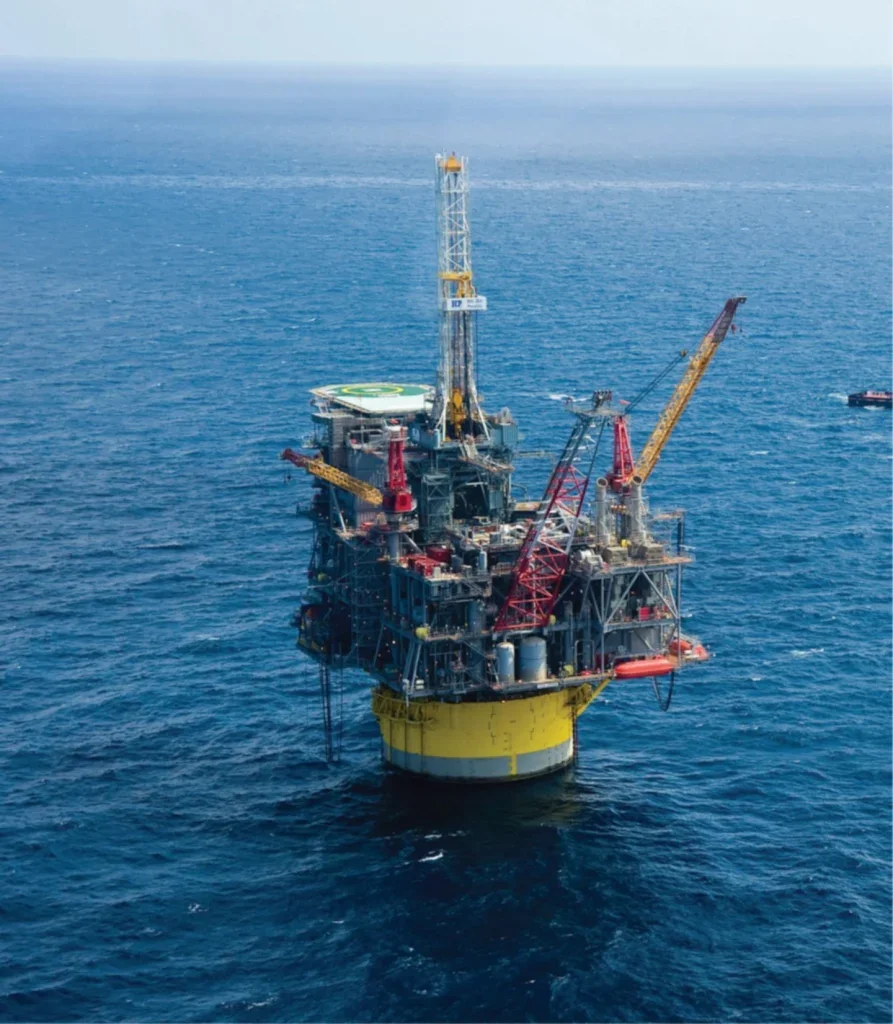
That is the weight of the rope in air. It is, though, a load that, at full extension, is not actually borne entirely by the offshore hoist or crane. In water, it weighs rather less, owing, of course, to the upthrust. Synthetic ropes are lighter than steel ones; indeed, many synthetic ropes actually float. For offshore use they can be engineered to have neutral buoyancy, inclined neither to float nor to sink, which makes for one calculation the less during lift planning.
Buoyancy affects not only the rope; it affects the load as well, and generally rather more greatly. When a submerged load is being lifted from the water it ceases to experience upthrust, so its weight suddenly increases, possibly several-fold, as it emerges. Its effective centre of gravity may also change position, which has to be taken into consideration in the rigging arrangements. Onshore operators do not generally have to cope with loads whose weight, and the geometry of whose weight, changes radically over the last few metres of the lift.
There is another factor in offshore lifting that onshore operators lose no sleep over. Offshore lifting is generally performed from a ship or floating platform. Ships and floating platforms get lifted up by waves. So they accelerate upwards, and the load they are lifting gets accelerated upwards as well. The force that accelerates the load comes from the rope, so the tension in the rope increases correspondingly also, and possibly quite suddenly.
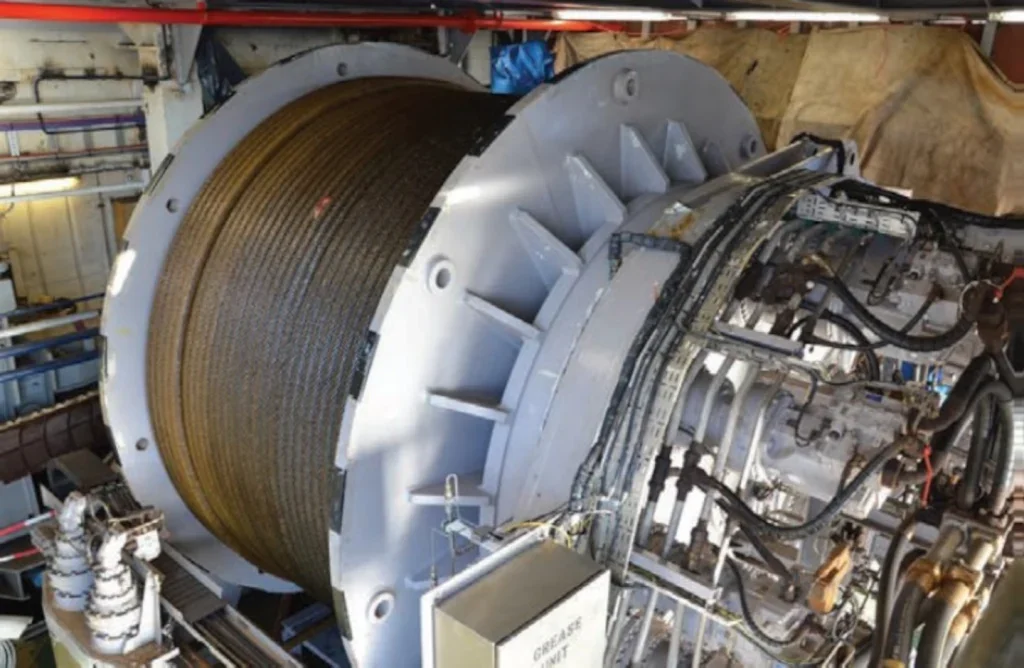
Similar considerations apply to a fixed winch – say, on a windfarm tower or nacelle, when it is just about to raise a load from a barge. The average wave height when unloading vessels in the North Sea is around 3m. The barge suddenly falling by 3m just as the load is about to be raised from its deck can cause a sudden snatch load on the rope and hoist. If the crane operator gets it wrong, and hoists the cargo as the vessel is dropping into the trough of a wave, the resulting shock load will create a dynamic effect that can increase the load on the crane by up to three times the actual weight being lifted. These dynamic amplification factors must be factored into the load plan.
Such complications are one reason why specialist companies exist to help planning offshore lifts. Thus Cranemaster, based in the Netherlands, offers full analysis of a proposed offshore lift operation, including force analysis in the winch or load during transfer lifts or through the splash zone, operational weather window calculations, and subsea landing speed analysis.
Calculations are carried out using OrcaFlex software. The company can also provide a feasibility study, and a normal level technical report.

For particularly complex operations an extensive level statistical analysis is possible, which gives a full extreme-value statistical analysis of the lifting operation and detailed weather windows with an agreed confidence level.
The added stresses of dynamic amplification are also where heave compensation comes in. It is a system that aims to reduce or remove them. Digital algorithms added to the winch controls can be made to pay out rope, or to take it in, to compensate for wave motion of the lifting vessel. Attitude and heading control (ACH) systems depend on input signals from a digital motion reference unit (MRU), which basically calculates the vertical movement of the support vessel.
Palfinger Marine’s Active Heave Compensated (AHC) system is specially designed for load handling in rough seas from a vessel or rig towards the seabed, underwater installations or other fixed targets on the seabed. The position of the load relative to a fixed object is determined by the control system using the real-time signal from the MRU. In response to this signal, the AHC system will adjust the rotation of the drum to keep the load at a constant elevation relative to the seabed.
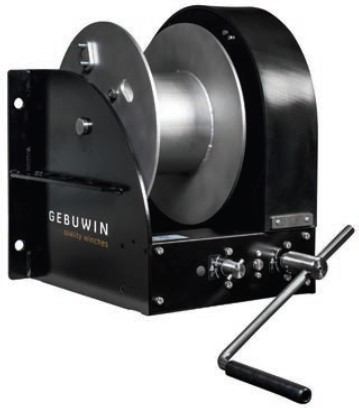
Three operational modes are available: normal (i.e. as a standard hoist); constant tension, which as the name suggests keeps the force on the wire rope constant, thus eliminating sudden stresses on it; and active heave compensation, which accords priority to keeping constant the velocity or position of the load.
Palfinger Marine supplies both electric and hydraulic AHC winches. The algorithms and hydraulic system it uses reduce load movement, it says, by 98%. It differs from most in that there is zero load drop when the brake is removed. The hook and load will never move when the brake is opened. The system will also make it possible to hold a load with the brakes off, without any slow lowering of the load due to leakage. This means that the load can be held in subsea mode with brake off and all safety systems active for several days if necessary without any movement of the load – which is a great benefit in creating subsea installations. The hydraulic AHC winches are available with SWL from 10- 400t and wire lengths up to 3,000m. The electric-powered ones are available up to 20t SWL.
Subsea technology company Seatools is another firm offering AHC. Jointly with offshore hydraulic equipment specialist Degra it has introduced a standardised range of AHC hoisting winches that are on sale but are also available through a rental pool, making heave compensation technology more accessible than ever before to the offshore market.
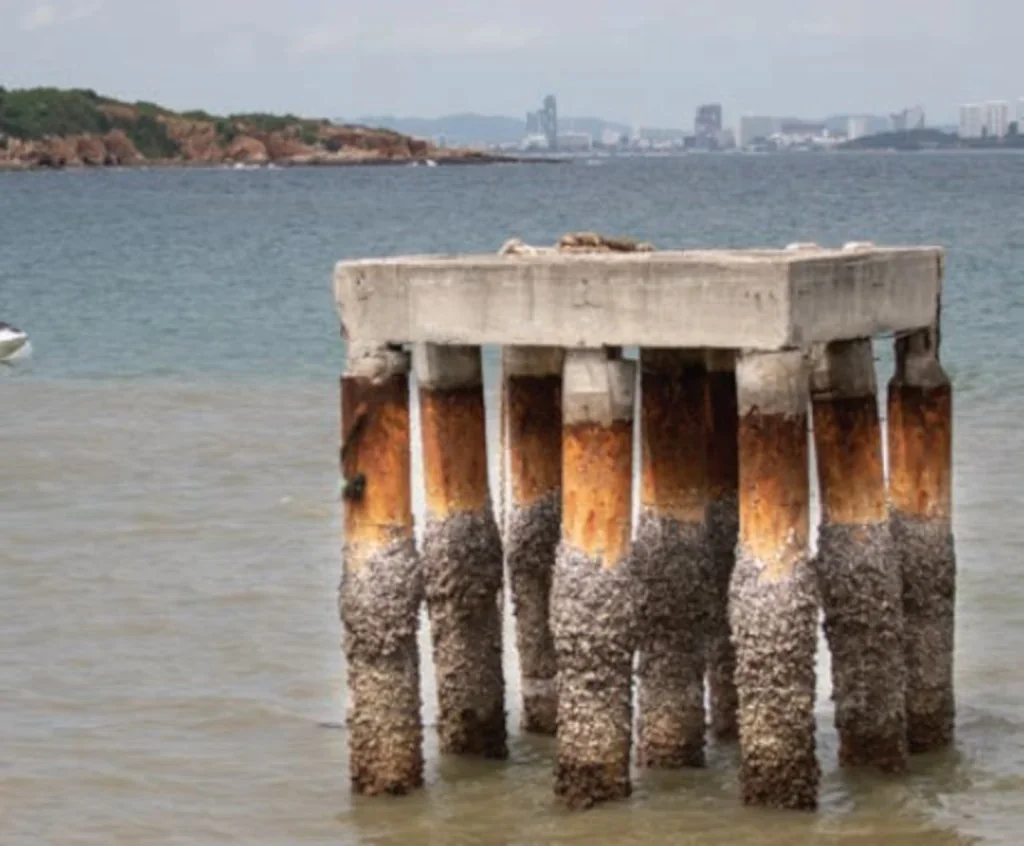
Its 15t AHC hoisting winch is a self contained plug-and-play unit that, in its basic configuration, contains the hydraulic winch and hoisting wire, electronics cabinet including its HeaveMate controller, a remote controller, and a laptop.
The intelligent control system features a self-learning algorithm, which makes on-site commissioning straightforward. The operator enters only a limited number of situational parameters – the intelligent control system will then automatically configure and optimise itself. The obvious benefit is a minimum of commissioning time. Seatools carries out thorough simulations in each case before installing, to predict the system’s performance in any situation – which again means that only fine-tuning is required on-site. Accuracies (not including MRU inaccuracies) to less than 1cm or 3%, whichever is worse, are claimed.
The design stage includes simulations of component failures, such as failure of the MRU. Consequences of such failures are analysed, and in this way a system is developed that features fault tolerance.
At each AHC winch delivery Seatools and Degra provide an operator training programme to familiarise and train clients’ operators with the system. Optionally, Degra/Seatools operators can be provided to operate the winch throughout the client’s entire offshore operation.
Huisman have been designing and building heave compensation systems since 1985. It uses three different systems for active heave compensation: secondary controlled hydraulic winches, frequency controlled electric winches, or hydraulic cylinders.
The main advantages of its systems, it says, are increased weather windows through high compensation speed combined with high payload, low power demand through clever energy management, and redundancy to increase safety.
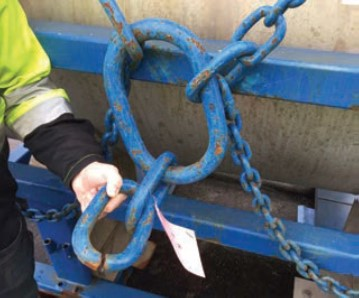
Passing the splash zone is perhaps the most hazardous part of an offshore hoisting operation. This is where loads can suddenly and unpredictably alter as waves strike and buffet the load from side to side and alternately supply and remove upthrust until the load is fully submerged. To reduce load peaks on the payload or on the equipment, particularly in this zone, Huisman has a Load Peak Shaving system. This significantly limits the impact forces while lowering payloads through the splash zone and during subsea operations without the need of additional equipment in the rigging.
CORROSION
Offshore is a harsh environment, even in calm weather. Salt water, sea air, waves and wind form an extreme environment, and normal steel, good for many years of use inland, will corrode extremely quickly in marine applications. For which reason, special coatings, special steels and protective techniques such as sacrificial anodes are de rigeur at sea.
Even simple hand hoists and winches need to be marinised. Dutch company Gebuwin are specialists in hoists and winches, for many applications, but the maritime and offshore industry is its largest market.
Gebuwin has therefore developed hand winches especially for this industry. All parts of the marine winch that are exposed to the weather are made of stainless steel 316, which is the highest corrosionresistance grade. The winch has a worm gear transmission to increase safety when hoisting, pulling or tensioning heavy loads. The transmission is enclosed with an IP54 rating against particle and water ingress. It is also possible to apply a marine coating to the winches
For example, its 3,000kg worm gear hand winch in addition to the stainless steel construction has three layers of C5M paint – C5M, whose technical classification is Very High Corrosivity, Marine is the standard for very high protection in coast and sea environments. The winch is ATEX certified and can be driven pneumatically or electrically as well as by hand, and 500kg and 1,500kg versions are also available.
Corrosion, of course, affects onshore equipment also, but steel in marine environments is subject to a type of attack and consequent failure that is much more frequent, and much more severe, offshore than on. Hydrogen embrittlement is a phenomenon that was until very recently not well understood. Ben Burgess, director at chain and hoist specialists William Hackett, produced a peer-reviewed report on the topic just a few years ago, which is still a standard reference.
For hydrogen embrittlement to take place, he says, three elements are required: first, a source of hydrogen – such as the hydrochloric acid that is a product of corrosion; second, material susceptibility – harder and lighter steels, such as increasingly used at sea, are more susceptible than low-strength ones; and, thirdly, mechanical stress.
The mechanical stress, says Burgess, typically comes not from the strains of conventional lifting but from dynamic loading, which as we have seen, is an offshore phenomenon.
Those stresses open up micro-scale gaps in the grain structure of the steel. Hydrogen migrates into those cracks. There it creates internal pressure, which tends to push the steel apart. This can lead to catastrophic failures.
Unlike weakening of machinery directly caused by macroscopic cracks, hydrogen embrittlement is near impossible to observe and to predict, says Burgess. This, of course, makes it highly dangerous.
As we have seen, harder steels are more susceptible than softer ones. This is a consequence of their tighter grain structures, which allow more scope for hydrogen to penetrate between the grains. Preventative measures recommended by the William Hackett report therefore include maximum hardness quotas on steel for chains used in the offshore industry, as well as the application of corrosion-resistant finishes to all chain types. Both these measures make it more difficult for hydrogen to enter the structures in the first place.
Another relevant factor is that Norwegian government regulations, the Norsok Standards that are a requirement for North Sea and other operations, dictate that marine lifting slings should be made from chain rather than wire. They forbid any mechanical fixings, meaning the normal method of cutting chain and using connectors is not permitted. Chain slings, therefore, stay attached semipermanently to the load and are left open to the hostile marine environment where hydrogen embrittlement can occur.
William Hackett has therefore developed its Zinc Tough Technology coating, which satisfies all Norsok requirements and all but eliminates the risk of salt water ingress and hydrogen embrittlement.
With its manufacturing partner Mckinnon Chain in South Africa, it produces fully welded chain sling assemblies from its Marine Grade 8 lifting chain. Manufactured specifically to be suitable for working in extreme environments, the chain undergoes a specific heat treatment process that controls the alloy steel to give it a maximum hardness of 38HRC. The chain is fully treated with the Zinc Tough technology, while the assemblies are DNV type approved. The company holds stocks of common sizes, but most assemblies are made to order.
The chains have a range of diameters from 7-32mm. All sizes are proof tested at manufacture to 2.5 times the given working load limit and are fully compliant to EN818 material requirements. The manufacturing process of the Marine Grade 8 chain gives improves toughness and ductility in extreme conditions with increased resistance to hydrogen embrittlement and stress induced corrosion cracking.
It is possible that in all the above we may have given the impression that offshore lifting is an order of magnitude more difficult than standard onshore operations, with hazards and factors all of its own. If we have, we may not be that far wrong.
MODULIFT RAISES OFFSHORE TUNNELLING MACHINE
Modulift’s customer, a specialist in tunnelling and microtunnelling, had excavated an undersea tunnel and now needed to recover its micro-tunnelling machine from the seabed.
The beam had to be designed for use above and below the water. This required consideration of factors such as the differences in the centre of gravity location in the water and out of it, and the increased weight of the micro-tunnelling machine once above the surface due to the removal of its buoyancy force. Nevertheless, Modulift’s in-house team was able to achieve the correct tilt and balance to ensure a safe and effective lift. The bespoke solution was required to meet the stringent DNV industry standards (for marine operations), and to have a dynamic amplification factor of 2.0.
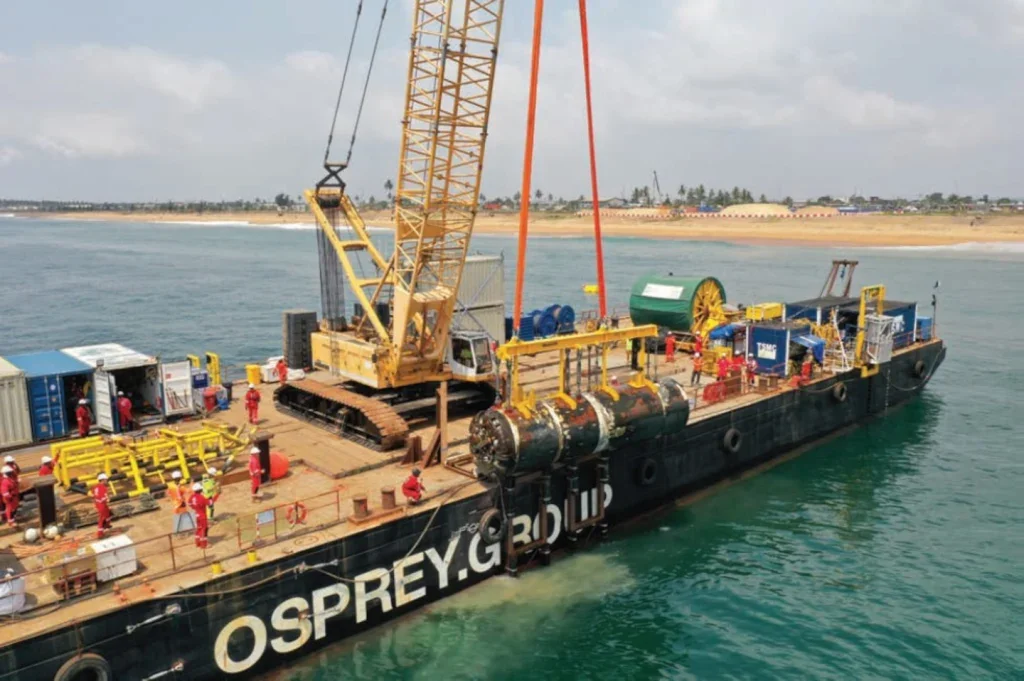
Modulift’s engineering team designed the 6.7m-long lifting beam with eight lifting points. Turnbuckles connected the lifting beam to the tunnelling machine. The beam featured two top lugs and four bottom lugs, and tugger points were installed for manoeuvring the beam into the right orientation before lifting.
The team used 3D structural analysis in STAAD Pro. Finite element analysis was conducted on the lifting lugs and welds using ANSYS software. At the customer’s request Modulift engaged DNV to perform a third-party design review and certify the beam in compliance with DNV-ST-N001. The design was successfully approved in the first round of reviews, allowing Modulift to complete the project within eight weeks and this from design and drawings, to fabrication, painting and procurement of rigging.