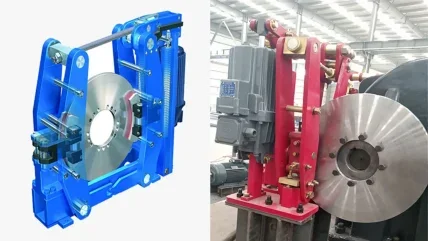
Without brakes no hoist system could operate successfully. Not only must loads be lifted and then moved in some way on rails, trolleys, gantries to be placed elsewhere, they must also be stopped from moving when they arrive at the right place, and before that if they threatening to collide with other activities. The provision of brakes has been vital for both proper load management and safety.
These little remarked components have their own development path and three main trends at least are apparent in their technology and use; the advent of the disc brake over the drum brake, the increasing emphasis on safety in modern factories, mines and in other uses, the theatre notably, and the rise in use of electronically-controlled inverter type motors, whose "infinite speeds" change the function of the brake. Since the motor slows the load down, the brake is often now for holding and securing the load at rest rather than slowing its motion.
Historical developments
Perhaps the most obvious of these developments is the advent of the disc and calliper type of brake. Vice-president of sales for US maker and distributor, the Hilliard Corporation. Juan Parra describes the development: "In the post-war period the drum brake was most often used, an external shoe type rather than the internal drum brakes you find on a car."
But as the technology developed for disc brakes in cars it also started to be used for industrial applications, he says, with one of the first calliper disc types being offered by the British company Twiflex, now part of the Altra Industrial Motion Group. These did not use a drum but a disc attached to a spinning power transmission shaft with clamping callipers applying brake pads.
"There are significant advantages to the disc type" says Parra. The most important is the way the brake can disperse the considerable heat build up that braking friction always produces. "Most drum brakes have one side more accessible than the other and heat passes out on one side unevenly.
Another type of brake, the plate brake, has even bigger problems he says. Plate brakes have a sandwich of several friction plates and braking surfaces which provides a lot of braking surface in a compact space, which is sometimes useful, but "there is no easy way to dissipate the heat".
If the brake is used only occasionally, as on aircraft landing gear for example, where there is time to cool again, that can be overcome. "But not for frequent use."
New materials
The problem with hear loss through one surface is that a hear gradient is created with causes expansion and other effects on materials he says which in turn can lead to cracking or other problems. New materials are being developed which can help this, but the symmetrical structure of disc brakes allows more even dissipation and greater material stability he says.
Another advantage of disc brakes is that they can cope with greater torque. This has allowed the location of the brake to move over the years from the motor drive shaft to the gearbox output shaft, which turns faster but with higher torque. Disc brakes can also be built to greater sizes he says whereas drums are limited to less than 30" (750mm).
"Another development is to put the brake even further along on the cable drum itself," he says. That requires the drum to have one flange enlarged to act on the outside as the brake disc.
The advantage is that the braking action is further along the connection which offers greater safety if the transmission should break; stopping the motor output is no use if the geartrain has broken.
"Mostly the drums are not being made that way but you can retrofit with welded or bolted extensions" he says.
Drum braking
An extension of the drum braking is the addition of various safety brake systems particularly in elevators and some theatrical stage equipment he says, with brakes fitted on cab roofs and running over a vertical rail, activated by sudden acceleration to clamp on and stop.
Systems like that are used too in mines for the explosives wagons running to the face.
Hilliard makes some of its own brakes and particularly in very large sizes, says Perra; one of the biggest is for a moving stage setup at one of the large theatrical stagings in Los Vegas.
These are hydraulically activated rather then using the electro-mechanical methods which open the callipers on most disc brakes. The hydraulic method has greater pressure for pushing open the springs on the very large brakes. Like all these braking systems the callipers have to be opened actively during operations, creating a "fail-safe" condition where they close if the power fails.
"But we also buy a lot of our brakes from Twiflex and are the North American dealership for their products" says Perra. The range of industries covered is large from paper mills to mining and steel mills to shipyards, and other marine applications. Theatre and sport is also a used from scenery hoists in opera to scoreboards in stadiums.
Broad range
Twiflex in the UK also offers its products directly of course serving a wide range of industries. A major application has been in a customised mine hoist system supplied by a leading manufacturer.
The supplier specified Twiflex VMS3/SPS brakes for use at the new $1.4bn Goldcorp Eleonore gold mine in northern Canada, which will be processing a 7000t/day ore throughput. It should produce 600,000 ounces/year of gold for the next 15 years making it one of the largest underground mines in Canada. Production begins late next year.
The order was for callipers to be installed for a huge 20 foot (6.1m) diameter double-drum, single-clutch mine hoist. The hoist has two brake discs, one on the fixed drum and one on the clutched drum.
Each brake produces 240kN braking force at a 2.5 mm air gap with greater than 2 million cycles fatigue life available at this rating. The company also supplied VMS-DP brake callipers with pedestals plus a hydraulic power pack for each of the two primary mills.
Twiflex says the VMS3/SPS is a robust design which features a strengthened housing holding additional springs for improved braking force. It is totally sealed for corrosion and dust protection.
"The brake design offers set-up and maintenance advantages including tamper-proof pad/air-gap adjustment, external pad retraction, on-site torque adjustment and a ‘Park-Off’ feature which allows for fast seal changes without special tools" says the company. Seals can be changed from the rear without having to remove the brake from its mounting.
Braking force
The design uses small size pistons for quicker reaction times, coupled with an improved drainage system and a reduced retraction pressure of 137 bar at this rating. Braking force can be simply changed up to 275 kN at 3mm air gap by adding or removing shims located behind the rear cover. The brakes can be supplied with sensors to signal brake on/off and pad wear.
Europe is also the location for a number of other major supplies, particularly in Germany. One of the best known is Mayr which supplies many major hoists manufacturers including Kone Cranes in Finland.
"For hoists we would usually use disc brake types" says Petri Partanen a product support manger at the hoist and cranes maker. "They are sued to stop the load." Brakes are also needed for travelling bridges or trolleys he says. "On top of that there are emergency brakes quite often drum brakes which hold the load in the event of failures."
For hoist mechanisms electromagnetically operated spring loaded disc brakes are the norm he says. "We also sometimes use compact brake motors where the starting of the motor releases the brake by the axial movement of the shaft."
But for high risk operations like hot metal manufacture or mining, it is important to keep the brake independent of the motor, he adds. "In these situations there is an additional brake mechanically actuated if there is a sudden load increase."
Safety first
At Mayr, marketing manager Helmut Kleinheinz says that safety is an increasingly important consideration for braking systems, particularly as the inverter-controlled motor becomes more commonplace. Use of fine control speeds on motors means that the load is usually slowed by the motor itself rather than the brake and that means that the brake is used more to hold the load when it is static.
But although this reduces demands on the brake, and particularly changes the wear that brakes experience it is still vital to calculate the needed capacity of brakes in terms of falling loads. The worst case scenario, when perhaps something has gone wrong must be the basis.
Mayr provides a wide range of brakes for different industries. One with particular safety demands is the theatrical hoist used in opera and theatres to lift heavy scenery and where the dangers are obvious of a hoist failure. A particular example of Mayr’s brakes being sued was at the international Eurovision song contest held two years ago in the Düsseldorf Arena, which became the largest television studio in the world for the event.
For the complex changes of scenery, stage elements weighing tonnes had to be moved over the heads of the 35,000 strong audience and artistes alike. Power transmission stage brakes were integrated into the chain hoists for safety.
To convert the football pitch, more than 40 large trucks were required for the stage alone. Around 120 trucks of the same size were needed to transport the hall lighting, the LED technology, mounts for 2200 light units and sound equipment. To suspend lighting and decoration on steel cables and chains, maximum safety requirements were needed. Chain hoists with power transmission safety brakes were used for much of the moving of stage elements during the show.
Important standards
Mayr makes theatre hoists to different standards required by German law. All electric chain hoists for stage technology must fulfil the BGV standards but the basic standard only allows movements without people below only and loads may only be moved for setting up when people are not around.
For live movements over people there is a more severe standard says Mayr and hoists must have two independent DC voltage brakes. These would be of the type ROBA-stop -silenzio or ROBA – secustop series which Mayr especially developed to suit this purpose.
A compact and enclosed design ensures simple handling and installation it says with a working air gap is pre-set without any need for re-adjustment. Malfunctions due to operating and adjustment errors are excluded.
"The unit has an integrated damping system to reduce noise and for maximum operating safety and reliability, every single brake in the plant is subjected to a 100%check in completed state prior to delivery" says Mayr.
The stage brake is mainly maintenance-free. Maintenance is limited to inspection of the long-life friction linings, which are highly wear resistant. Mayr can offer hoists to the highest standard approved for moving scenery usage during performances and events over people.
Extremely quiet stage brakes by power transmission make a star appearance daily at numerous events all around the world says the company. Another significant hoist brake maker in German is Intorq, once part of the Lenze group and now an independent subsidiary though still a major supplier to Lenze. Its units are found in many significant hoist brands – in the UK Street Crane` uses them and they also supply Konecranes.
They make brakes for a wide range of purpose and are not concentrating simply on the hoist market at present says Geoff Spear UK marketing manager for Lenze. But within the range a number of models are used for the hoist market including the Intorq BFK468 spring-operated brake for high-performance applications where drives are generating ever higher motor speeds and drive torques.
"Although performance requirements are increasing, less and less space is available for the brake" says Lenze. For this innovative multipole technology allows it to be released through a large air gap, even when forces are high. The large working air gap means long maintenance intervals
The units have fixed or adjustable braking torque and can ‘cold brake’ by holding current derating.
More directly for hoists there is the BFK468 multipole brake which have high braking torques, short response times and low-noise operation. They can also be adapted to the contour of the motor.
The spring-operated brake uses a calliper and is for multiple and redundant arrangements. It releases without residual torque and quiet operation, can "cold brake" and can have air gap or wear monitoring using a micro switch.
Growing trend
One growing trend is the use of compact design brake motors and the Italian company Coel Motori specialises in these with four different series of brakes motors.
First are the F type, which are closed and externally ventilated. The brake groups and all the motor parts are designed and made by Coel. The brake group is supplied on series with AC 3phase electromagnet but a DC version is also available.
The FK motors are DC with rectifier and like the F-type can be driven by inverter though that means a separate power supply for the brake and the motor. These have die pressed aluminium cases and braking surfaces in cast iron.
A final series the SW is made for situations where the motor faces frequent water contact. The brake motors are not ventilated and are totally enclosed.
Coel sells substantially to the oil and gas industry and particularly for environments where explosion proofing is needed there is the new modular explosion proof brake the VIS. It has a patented design for hazardous location areas says Coel marketing manager Alessandro Tonon.
"The unit is designed for multiple application fields such as hoisting and travelling applications, winches, capstans, wire rope hoists and chain hoists," he concludes.