<p>Before going into the details, I must start with the terminology as the terms ‘lifting beam’ and ‘spreader’ are often used interchangeably. Also the term ‘lifting beam’ is sometimes used for a beam which is part of the structural support for a lifting machine, such as a runway beam. That is not what I am referring to here. In this context they are both below hook lifting accessories. They are both a means of providing two or more lifting points from the hook of the lifting machine spaced so as to match the position of the lifting points on the load. The difference lies in the way the forces are transmitted.</p><p>A lifting beam is loaded in bending. Typically a simple lifting beam will have a single lifting eye above the beam which engages with the lifting machine hook and lower lifting eyes at points on the underside of the beam to connect to the load.</p><p>A spreader, often called a spreader beam, is actually a strut loaded in compression. Typically a simple spreader will have a suspension sling which connects the lifting machine hook to the ends of the spreader which are then connected to the load. In fact some of the earliest spreaders were simply a rod with a fork at each end which was used to spread the legs of a two leg chain sling. The forked ends engaged with the chain links to prevent slippage. This arrangement enabled the sling to lift, for example, a cable reel from its axle whilst preventing the chain legs damaging the drum flanges.</p><p>The design of modern spreaders is usually much more sophisticated but the principle is the same. In practice a combination of beam and spreader is often used for reasons which I will explain later. It might explain the confusion of the terms. I hope it is clear that, whilst the terms are often used interchangeably, the equipment itself is not interchangeable. It must be loaded in the manner for which it was designed.</p><p>Although not covered by this article, a variation of the lifting beam is one designed to connect two overhead travelling cranes and provide one or more lifting points. This facilitates tandem lifting. The total lifting capacity can be that of the two cranes less the self weight of the beam and any allowance for uncertainty in the sharing of the load.</p><p>Most lifting beams and spreaders will be designed for specific applications. For example a lifting beam for use with vacuum pads or lifting magnets to lift long flexible loads which needs support at regular intervals to prevent sagging. A spreader might be designed to lift a load such as a vehicle or boat, lifting it from the base but keeping the slings clear of easily damaged areas.</p><p>Lifting beams and spreaders are often used when there is limited headroom. Ideally it is best if the attachment points on the load are above its centre of gravity as that will ensure that the load will always hang in a stable position. However if the lifting beam or spreader is connected to the load by slings which attach to the load below its centre of gravity, care is needed to ensure that the load will be stable when lifted. </p><p>A typical application of this kind might be a generator set mounted on a skid. The lifting beam is connected to the skid by four vertical single leg slings. When viewed from the side, the lifting beam, skid and slings form the four sides of a rectangle. Without triangulation the four sides form a mechanism which can deform into the shape of a parallelogram. That is what happens if the load is unstable and starts to topple. Looked at from the side, the figure below illustrates the situation. </p><p><br /><div class="inlinepic a"><img alt="Lifting beam triangles" src="/uploads/Pictures/web/a/g/n/liftingBeamTriangles_1_.jpg" imagecode="73533" /><br /><div class="storypicscaption"><div class="photocredit"></div></div></div></p><p><br />The forces which prevent or cause toppling come from the vertical distance from the seat of the lifting machine hook to the sling attachment points on the lifting beam (A) and the distance of the centre of gravity above the attachment points on the skid (B). The centre of gravity will always try to be as far from the hook as possible. If A is greater than B the arrangement will be stable. The larger the difference, the more stable the arrangement will be. However if B is greater than A, the arrangement will be unstable and will topple. The relationship between dimensions C and D also affect stability. If C is greater than D the arrangement will be less stable. </p><p>The issue of stability should be considered at the lift planning stage and not left to checking at the time of rigging. The static friction at the pivot points can be sufficient to allow a well balanced load to be lifted vertically. However when a travel motion is started this can be sufficient to break the frictional grip and, once the load starts to topple, there is no going back. It will continue.</p></p><div class="advert"><MIDDLEOFSTORY/></div><p>The example described is a four point lifting arrangement but the same problem can occur with other arrangements. For example a load held by two slings in basket hitch, one at either end connected to a straight lifting beam. Viewed end on, the load is held securely with triangulation provided by the basket hitch. However, viewed from the side, there is the rectangular mechanism supporting the load from below the centre of gravity with only the friction between the slings and the load to stabilise it. </p><p>Lifting beams often have a profiled plate eye to engage with the lifting machine hook. This keeps dimension A to a minimum but can cause stability problems for these types of applications. The obvious way to ensure stability is for dimension A to be significantly greater than B and this is where a spreader, suspended by a sling, often has the advantage over a lifting beam. Alternatively the combination design I referred to earlier can be used. In this the beam is suspended from a sling connected part way along the beam rather than at the ends. It increases the A dimension and the forces in the beam are a combination of bending and compression.</p><p>Lifting beams and spreaders can also be designed for multipurpose applications. There are two basic approaches to this. Lifting beams can have adjustable lifting points which can be moved along the beam to suit the particular load. Spreaders can be made in modules which are assembled into the configuration required. Lifting beams and spreaders of these types are often available from hire outlets making them cost effective for one off or limited applications.</p><p>Lifting beams can also be designed for applications where the load is to be intentionally tilted or where the position of the top suspension eye needs to be adjusted to match the centre of gravity of the load. Designs which incorporate adjustable lifting points or tilting facilities should take account of the possible operator errors in not adjusting or tilting accurately.</p><p>There is a harmonised European Standard, EN 13155, which specifies the requirements for lifting beams and spreaders. It deals with all these variations as well as specifying the fundamental requirements. Buyers are advised to specify this standard.</p><p>Finally, a few last matters to consider when purchasing or hiring lifting beams or spreaders. The self weight of the item is usually a significant part of the total weight on the lifting machine so should always be included in the calculation. It is normal practice to mark the lifting beam or spreader with its self weight. In the case of permanent assemblies such as a lifting beam with magnets, that will be the weight of the complete assembly. However in the case of those designed for multipurpose applications, caution is required to check whether the marked weight includes the variable accessories or whether they must be accounted for separately.</p><p>When not in use, the lifting beam or spreader is usually set down and detached from the lifting machine. If the ancillary items such as slings, shackles and turnbuckles are trapped under the beam, they can be damaged. If detached beforehand, they may need separate storage to prevent loss. The beam may not be stable unless supported or laid flat. Therefore consider whether it can be designed to be set down or whether a separate stand is required.</p><p>The beam or spreader should have its own unique identification marks. Most lifting beams and spreaders have ancillary items such as slings and shackles which are detachable although normally kept as an assembly. In such cases it is normal practice to mark each item with an ID mark linked to that of the assembly. The certification for the lifting beam or spreader should cover the complete assembly, listing the main ID and those linked to it.</p><p>Multipurpose items may utilise general purpose lifting accessories selected by the rigger for the particular application. In that case each accessory should have its own unique ID and certification.</p><p>If the lifting beam or spreader is for use with a double girder crane, remember that the upper limit switch is usually set so that the bottom block will rise up between the girders. This will allow the beam to foul the girders before the limit switch operates. Adjustment of the limit switch or a secondary operational limit is necessary. Relying on the operator is not good practice. </p><p>As with most equipment, lifting beams and spreaders have some limitations. Nevertheless they have many advantages and provide a method of handling loads which cannot easily be handled by other means.</p>
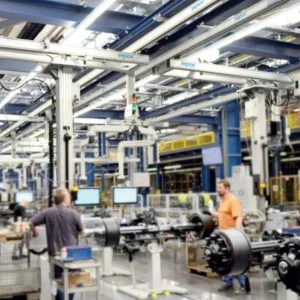