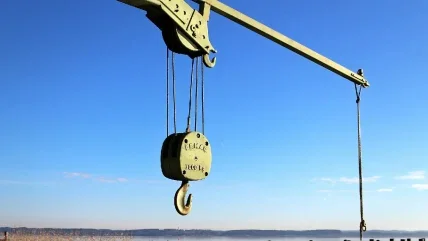
Sporting success
Yaplex has provided handling systems for a UK sports car manufacturer.
Yaplex, UK designers and manufactures of bespoke dedicated handling systems and standard lifting solutions, has provided expert advice on a range of handling requirements for a British sports car manufacturer’s new range of vehicles.
Having experienced extremely long lead times and a lack of technical/service back-up from an Italian supplier, Lotus Cars was keen to use a UK manufacturer for its handling equipment and Yaplex ‘fitted the bill’ by providing design and manufacturing from its UK headquarters and manufacturing facility in Chesterfield, Derbyshire.
Yaplex was tasked with providing handling solutions for the lifting and manipulation of chassis frames, sub-assembly frames, fuel tanks, batteries, instrument panels, cable harness and fusebox assemblies, seat frames, seats, wheels, tailgates, and doors with weights ranging from 15kg up to 600kg.
The company designed a range of innovative solutions to meet the customer’s needs. These included pneumatic balance arm handling, which the company says “proved to be an ideal solution for the required reach-in requirements”, where ‘reach in’ means that the load being lifted needs to reach inside the vehicle – for example, fitting a car seat into a vehicle; electronic balancer handling “for precise and quick movements thanks to the touch-sensitive controls and automatic balancing of the load”; and electronic linear handling, enabling balanced linear movement of the load.
Additional column-mounted swing jibs, electric chain hoists, conveyors, fixtures, and lightweight X-Y travel gantry cranes were supplied to complete the project.
“We were proud to receive positive feedback on us meeting the tight deadlines imposed, and the quality of the equipment installed, which has resulted in additional enquires and orders. We continue working closely with Lotus as they continue to expand and introduce new models,” says Yaplex.
A monorail solution
CraneWerks has installed an outdoor, manual freestanding monorail and a hoist for a US national commercial truck dealer.
A national commercial truck dealer within the transportation industry sought CraneWerks’ expertise to design, build, and install an outdoor manual freestanding monorail complete with a hoist with an 8.0-ton capacity, shelter for the hoist, and epoxy paint that could stand up to Detroit, Michigan winters.
The permanently mounted monorail crane system with 15ft of width clearance and 14ft in height clearance was intended to facilitate the undecking of tractors from semi-trucks.
The company had been renting mobile rotator tow trucks each time they needed to undeck the trucks. With CraneWerks’ monorail solution, the dealer eliminated this need. This has resulted in cost savings and saves time.
The truck dealer had previously engaged with CraneWerks on another project at its Texas location, and CraneWerks took this experience and tailored it to the requirements of the Detroit facility.
Part of the process
Bang Kransysteme has supplied a second process crane to car manufactuer’s Volkwagen’s newest workshop addition in Bratislava, Slovakia. The cranes now feed the plant’s production and maintenance lines.
The parts project
An automotive recycler says it’s ‘very satisifed’ with a Met-Track crane system solution
Based in North Carolina, US, Atlantic Hoist & Crane has been selling and servicing hoist and crane equipment for its customers since 2006.
It was given the task of providing a Met-Track crane system to Cunningham Brothers Auto Parts, an automotive recycler that sells parts to automotive OEMs and their dealers, commercial and municipal fleets, and extended warranty coverage and insurance companies.
Met-Track’s portfolio includes bridge cranes, jib cranes, portable gantries and monorails.
The crane system had to aid the breaking down of vehicles that Cunningham Brothers acquires from accidents.
Cunningham’s initial idea was to purchase a ceiling-mounted top-running 5.0-ton bridge crane, but upon inspection by Atlantic Hoist & Crane it appeared that the building, which at the time was newly constructed, would require extra steelwork to support the weight created by the crane and load it would carry. Unfortunately, the building would have to have been redesigned and rebuilt, which was not an option due to the expense and loss of production time.
A solution involving individual cranes was chosen, and due to the application being complex and standard cranes not being suitable, Met-Track worked with Atlantic Hoist & Crane to create a bespoke design.
The unique Met-Track workstation bridge crane system consists of several side-by-side systems, one end being floor-supported using hangman columns, with intermediate supports ceiling-mounted on additional steelwork designed to support adjacent cranes from a single beam above.
Each crane system provides a lifting capacity of 1.0 ton to each of the five areas requiring handling/lifting assistance, and being majority ceiling-mounted this meant the floor space could remain unrestricted.
Cunningham’s was supplied within six weeks of ordering and was very satisfied with the overall outcome, which has resulted in a more efficient production facility.