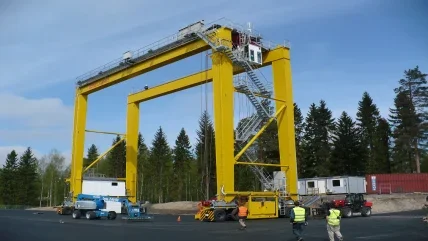
People who need light objects lifted can use chain hoists, wire rope hoists and, now, even webbing hoists. The hoists can be manual or electric hoists, mounted statically or on monorails, which in turn can be of steel or of aluminium. Or users can turn to vacuum lifters and manipulators, or to air balancers, davit cranes or jib cranes – and even then the list is not exhausted. The options for light lifting are many and varied.
We shall in this article call ‘light lifting’ anything up to around 5.0t, although that is fairly arbitrary, and we have some exceptions. It is certainly a load that requires lifting apparatus: in the UK, the Health and Safety Executive (HSE) says that a man should not lift anything heavier than 25kg, while the safe lifting weight for a woman is no heavier than 16kg. In the US, the National Institute for Occupational Safety and Health (Niosh) has developed a mathematical model that helps predict the risk of injury based not only on the weight being lifted but also on criteria such as how high it is being lifted, at what distance from the body, how often such lifts are performed, and whether the lifter is having to rotate or twist their back. The maximum load under these guidelines is 51lbs (23kg), which is reduced as the different factors come into play.
PLENTY OF OPTIONS
Konecranes covers a fair number of light lifting options. Its KL manual leverpull chain hoist has a capacity of up to 3,000kg, while the KM2 hand chain block and manual trolley can manage up to 20,000kg. Both have dual-pawl Westonstyle brakes with two friction discs. They come hook suspended, or with an I-beam trolley, which is propelled by manual push (up to 10 tons) or hand-geared chain (up to 20 tons).
Turning to electric power, the company’s model C-series electric chain hoists can lift up to 5.0t. They have inverters, and selfadjusting brakes, and a redesigned chain and sprocket interaction that Konecranes describe as “flawless” and that prolongs the chain life.
Any of these hoists – or Konecranes’ pneumatic lifters – can be mounted on trolleys on overhead rails; for example on the company’s steel workstation cranes, or its aluminium versions. The advantage of aluminium is, of course, its weight, or rather its lack of weight. Aluminium also gives less rolling resistance, so trolleys can be pushed by hand with minimal effort. (Of course, motorised trolleys can also be fitted – generally, any load over 1,000kg or a girder length over 6m needs a travel drive, says Konecranes.)
These are modular systems. Track sections bolt together, with no welding, so changing and adding sections is easy. Workstation cranes can have many different configurations – as monorails, single- or double-girder bridge cranes and so on – and steel and aluminium systems can be combined. You could, for example, have steel profile overhead track for long, unsupported runs, giving way to aluminium nearer the site of operations. The aluminium system is also available in versions for hazardous environments.
As we have said, a huge variety of different lifting systems can be mounted on these tracks. As well as its C-series Konecranes particularly suggest its CLX and SLX electric chain hoists as particularly compatible. The SLX has a capacity of up to 2,500kg with a stepless inverter; the CLX can double that load, raising up to 5,000kg with twospeed controls.
Konecranes also has its XM light crane system, which can lift up to 2.0t. It handles loads of up to 2.0t. The overhead rail has a dip galvanised hollow profile to protect components from dust and dirt. The modular design bolts together without welding, so can be expanded easily. The rails are of steel, which allows long spans between supports, so reducing costs and optimising the working area below the crane. The rails can be configured as monorails or as single- or double-girder cranes
PROFILES
Erikkila, part of the Kito Crosby Group, have its Kito Erikkila light cranes, with track profiles available in steel or aluminium as hoist tracks or in single or double girder cranes. The maximum rated capacity of its single girder steel crane is 1,500kg, and of aluminium it is 1,000kg. In double girder form, the figures are 2,000kg for steel and 1,000 kg for aluminium. The two can be combined to cater to individual needs. Double girder construction increases the lift height and the crane’s rated capacity.
All of the standard light cranes can be manually operated or equipped with electrical movements for the trolley and bridge. The aluminium profiles 4/180 ICR and 5/220 ICR and steel profiles S200 ICR and S260 ICR are equipped with an internal conductor rail to maximise the crane’s coverage.
The trolleys for the steel profiles are designed to minimise rolling resistance and have a maximum load of 800kg for one trolley, with a steel body and integrated buffers. Trolleys for aluminium profiles carry a maximum load of 600 kg.
In use, the trolleys centralise the load automatically to the correct lifting position, which minimises the swing of the load. Switches and turntables are available for hoist tracks – they can be mounted on free-standing pillars if ceiling support is impossible.
Jib cranes are another option for light lifting. The jib cranes come in wall-mounted, column-mounted and low-headroom versions. Wall-mounted versions tend to be cost-effective since they need no support other than the wall of the building. They are also economical regarding space, so they are typically used when floor area is at a premium. Erikkila’s wall cranes have a load capacity of 1,500kg.
Slewing is up to 180º?, capacities, jib lengths and hoist types come in various options to suit different material handling needs. Erikkila’s jib cranes can lift 500kg at 8m jib arm length or 1,500kg at 5m jib. The same crane in a column-mounted version has up to 270º? of slew, with slew limiters when needed to confine lifting to a secure working area.
And finally, Kito Erikkila has portal cranes, also called gantry cranes. Steel legs mounted on swivel castors support an aluminium beam, and the whole is designed to be moved from place to place (though not with a suspended load). In the desired position, the castors are locked and lifting can begin. It comes in four lifting capacities (125kg/250kg/500kg/1,000kg) and two standard power supply options, flat cable, and internal conductor rail, and is available in single or double girder formats. So, once again, there is a plethora of choices available.
TIGER TRACK
Harrington Hoists – another member of the Kito Group – in March this year introduced its Tiger Track freestanding workstation cranes.
These are lightweight but powerful modular units that make operation, they say, even easier than using traditional bridge cranes. The track design is an enclosed one, maximising smooth movement and minimising the accumulation of dirt and dust in the track. This means operating the system takes very little effort from the user. Four or more freestanding legs either side of the work area support crossbeams, from which the two profiled running tracks hang; the bridge is suspended between them.
Tiger Track workstation cranes are fully customisable to fit material handling and production needs and can be easily modified by adding components as production or facility requirements change. The cranes come in single- and doublegirder configurations in all-steel or allaluminium, or as an aluminium bridge with steel runway. They are available in standard headroom or low-headroom styles with raised bridges in capacities of 0.125t through 2.0-ton capacities.
VECTOR CONTROL
In June, Columbus McKinnon made its Yale YK and Shaw-Box SK electric wire rope hoists available with OLV, which stands for open loop vector control. The open loop vector control units come equipped with variable frequency drives (VFDs) from Magnetek.
Combining these VFDs with fourpole OLV motors makes the YK and SK electric wire rope hoists more flexible and allow more precise lifting than models with two-speed control. They also come in at a cheaper price point than the alternative closed loop vector (CLV) control systems. The drives and hoists are specially designed to work together for optimal performance and provide infinite speed control or programmed, stepped speed control.
The OLV hoists are equipped as standard with paddle limit switches, sixposition electronic operation limits, and an overspeed/direction sensor to ensure the load is always under control.
The advantages of OLV, say Columbus McKinnon, are many. Compared to singlespeed or two-speed OLV hoists provides not only variable speed, but more precise load control and increased duty cycles. This latter is partly because although there is a mechanical brake, it is not used for slowing the load. Slowing down is performed by the VFD; heat dissipation is through an external brake resistor. This reduces heat generation in high dutycycle applications. The ramp-down-tostop feature decreases load bounce and increases brake life, since the brake is only a holding device, not a decelerator.
There is a longer life for the gearbox and other mechanical features because of the smooth start/stop, and the VFDs give built-in thermal overload and overcurrent protection from the hoist motor.
As well as that, Columbus McKinnon’s Intelli-Connect Mobile Wireless Drive Monitoring, Analytics, and Configuration option can be integrated so that operational data, fault codes, speed adjustments, and more are accessible directly from the plant floor. There is no need for an operator to go up to the hoist to find this data, which eliminates costly and potentially dangerous conditions.
Load control is more precise with OLV, and load bounce is decreased. Gearboxmounted speed sensors protects against overspeed and speed deviation, and a Quick Stop feature allows the hoist to stop within 3.0in (8cm) at high speeds. Other features enable operation above base speed with an empty hook (<50% load) for increased productivity. There is also torque proving, which confirms the motor is providing enough torque to safely lift a load prior to releasing the brake.
Chain hoists we know about. Wire rope hoists tend to be for greater loads and are also familiar. There is a third type, less well known than the others, that uses neither chain nor wire – nor for that matter rope. The belt hoist does what it says on the can: it lifts with a polyester belt that is resistant to acids, bases, mineral salts, solvents and oil. It also needs no lubricants, all of which means that there is nothing to contaminate foodstuffs, pharmaceuticals, or other products where high purity or hygiene is required.
Konecranes makes them, in capacities up to 2,000kg. The belt runs on highstrength polyamide pulleys, the casing provides IP55 water and dust shielding, there is motor overheating protection, and the whole can be suspended from an electrically isolated steel or stainless steel hook block installed on jib cranes, monorails or in stationary applications. It has electromagnetic, self-adjusting brake requires very little service.
Dutch makers Gebuwin also make winches suitable for use with webbing rather than rope. In this case, the winches are hand-driven, with worm gearing, and come in four capacities from 250kg to 1,500kg. They are suitable for vertical or horizontal mounting – an application they show for the product is lifting components into a 3D printing machine.
If you want a conclusion for all of the above, it is that the world of light lifting can be your oyster. We are spoiled for choice, in the technology and in the manufacturer. Happy lifting!