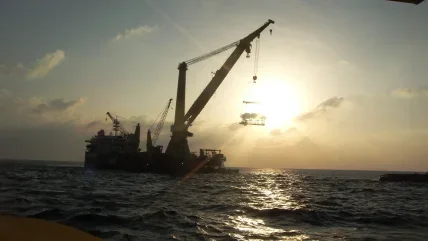
A report from market intelligence and consulting services provider Contrive Datum Insights (CDI) projects that the global offshore crane market will be worth $35.17bn by 2030, registering a CAGR of 9.68% during the period 2022-2030.
The report says that growth in the exploration and production of oil and gas in offshore areas – including deepwater and ultra-deepwater locations – as well the increasing popularity of renewable energy, such as offshore wind, is driving demand for offshore cranes. The development of new and advanced technologies, such as remote operation, automation and safety features, plus government initiatives to encourage offshore exploration and production, are also factors. Emerging markets, too – the offshore crane market has a lot of room to grow in places such as Asia-Pacific and Latin America, the report says – is predicted to also drive growth, while both the North American and European markets are expected to expand at “significant” rates.
Market restraints, meanwhile, include a lack of skilled cranes operators. Other restraints cited in the report were those that are constant features of the offshore crane market, namely the initial high costs of offshore cranes, the cyclical nature of the oil and gas industry, which can affect the demand for offshore cranes, and strict safety regulations.
CDI describes its offshore crane report as offering “an analysis of various business aspects such as global market trends, recent technological advancements, market size, shares, and new innovations”.
One of the key players profiled in the study is Cargotec. Its subsidiary, the cargo and load handling solutions and services provider MacGregor, has received an order worth more than €25m to supply general cargo cranes for ten 84,500dwt multipurpose vessels built in Asia.
The order was booked into Cargotec’s 2023 third quarter orders received. The cranes are scheduled to be delivered between the fourth quarter of 2024 and the first quarter of 2026.
A total of 40 cranes, each with a lifting capacity of 75 tons, are to be supplied. All cranes are connected to the latest worldwide service support and equipped with an active safety system.
MacGregor says it was selected as the supplier of these general cargo cranes due to its well-known design capabilities and long-term good cooperation with the unnamed customer.
“I’m very proud of the confidence that the shipyard has shown in choosing us to supply cranes for this important project. We look forward to providing our customer with our high-class equipment and services,” says Magnus Sjöberg, senior vice president, merchant solutions, MacGregor.
Elsewhere in Asia, in a first for the business in Asia, Enermech has been awarded a five-year contract to provide its specialist offshore crane operation and maintenance services in Malaysia.
Enermech’s global team of crane operators, mechanics, inspectors and technicians are being deployed to the region to provide crane operations and maintenance services across several offshore assets. They will transfer and competency train a number of qualified local personnel from the incumbent’s workforce into its employment to provide consistent project support for the client.
The specialist technical solutions firm is also looking to hire new talent within the region to supplement the delivery of the contract.
Christian Brown, chief executive officer at Enermech, says: “As we continue with our strategic growth plans around the world, securing this long-term contract in Asia with a client we support in other areas plays a key part in our progression.
It underlines how our integrated technical solutions, complemented by our collaborative approach with clients, are being recognised and more sought after than our competitors.”
Garry Ford, Enermech’s regional director for Asia-Pacific, adds: “Our strong track record and understanding of this client’s operations combined with our global crane experience ensures we are ideally positioned to provide an optimised technical solution to support each campaign across all assets covered in this new contract.
“Bringing Enermech’s safety culture is core to each campaign. As we transition many of the existing Malaysian team into our own work pool and look to add further new recruits from the local community, we will be providing incentives to retain employees as well as competency training. We are fully committed to developing talent on our doorstep and offering sustainable career opportunities in country.”
SCANDINAVIA
Earlier in the year, Deme Offshore, an offshore energy contractor, and Liftra announced that they will join forces to develop a novel offshore installation methodology for the next generation of offshore wind turbine generators.
The Liftra crane technology will be fully integrated on board Deme’s vessels on an exclusive basis.
Denmark-based Liftra is providing the design and engineering, based on its patented LT1500 Turbine Installation Crane technology, and this is combined with Deme Offshore’s engineering, operations and installation technology.
Deme says the Offshore Turbine Installation Crane offers the possibility of erecting higher and heavier turbines using existing vessels at a lower cost, while at the same time reducing the environmental footprint, and is suitable for both bottom fixed and floating turbines.
Bart de Poorter, general manager, Deme Offshore Renewables, says: “Deme Offshore is excited to again bring a game changing installation concept to the industry. Our exclusive partnership with Liftra combines the best of both worlds: Deme Offshore’s expertise and our long track record of successful wind turbine installation with Liftra’s crane technology.
There are many advantages of this new joint technology, the major one being the ability to install fixed or floating turbines from a floating vessel, which naturally means there are no limitations regarding water depth. As well as this, there are no longer any lifting height issues, and relative motions at high heights can be controlled. This new method also reduces the environmental footprint on the seabed at the wind farm’s location and in port.”
Per Fenger, CEO of Liftra, adds: “This offshore partnership with Deme Offshore underlines that Liftra’s lifting and transport technology is state of the art, also in the offshore wind sector. Liftra is proud to contribute with our innovative LT1500 installation crane technology, which is based on ten years of self-hoisting crane product experience, and the special configuration with two cranes working in parallel, is also proven and goes back many years.
“Liftra very much looks forward to collaborating with Deme on this new offshore turbine installation methodology. Liftra cranes always incorporate an extremely compact design and are well-known for their efficiency and sustainable set-up. Liftra is thrilled to team up with Deme, given its entrepreneurial drive and proactivity to bring state-of-the-art offshore solutions to the wind turbine industry.”
Deme says that due to its flexibility, the system can be exclusively integrated for use on board its floating offshore heavylift vessels such as Orion or Green Jade, as well as its existing jack-up vessels.
The partners will develop and integrate the technology in stages and following a testing programme the new system is expected to be operational in 2027. Staying in Scandinavia, we turn from Denmark’s Listra to the Norwegian offshore crane supplier Red Rock. At the start of autumn the Red Rock service team was busy with commissioning three cranes for a vessel belonging to service vessel operator North Star that will see service at Equinor’s Dogger Bank wind farm project off the north-east coast of England.
The three cranes are a 2.0t 3d Motion Compensated Crane, a 2.0t Boat Landing Offshore Crane, and a 1.0t service crane. Meanwhile, Huisman, which manufactures and services heavy construction equipment, has been awarded a contract from Norwegian vessel operator Havfram Wind, an installation contractor for offshore wind turbines, for the delivery of two packages of auxiliary cranes for both of the company’s NG-20000X-HF Wind Turbine Installation Vessels currently under construction at CIMC Raffles Shipyard in China.
The auxiliary crane packages include a 40mt full electric Huisman Pedestal Mounted Offshore Crane to be installed on the port side. This offshore crane is “designed according to the latest energy efficient technology on variable frequency drives for crane applications”. With this type of crane, Havfram Wind can perform operations on the vessel itself, as well as offboard operations, such as lifts to the turbine foundations, to supply vessels, or to the quayside when in port.
Havfram Wind has ordered the auxiliary cranes packages in addition to the 3,000- plus mt main leg encircling crane orders that the company recently awarded to Huisman. With these packages, Huisman has six cranes on order to be delivered for Havfram Wind vessels. The cranes will be produced at Huisman’s production facility in Zhangzhou, China.
Cees van Veluw, product director cranes, Huisman, says: “We are highly appreciative of the trust that CIMC Raffles and Havfram Wind have put in Huisman for selecting us as the manufacturer of the auxiliary cranes for their innovative newbuild jack-up vessels.
With these auxiliary cranes included in the package, we can further integrate our lifetime service offering to these vessels, thus improving their efficiency and effectiveness.”
REPLACE AND MANAGE
Sparrows Group, the engineering and maintenance services specialist for the global energy and industrial sectors recently rebranded as Altrad Sparrows after a 2022 takeover, has been awarded a major crane replacement contract for a client in the Middle East. The project, which is worth $13m, is expected to last 18 months.
The scope of work will see Sparrows complete all aspects of the engineering required to replace four BOS (board offshore) Liebherr cranes of four offshore platforms, which are beyond their expected operational life.
Sparrows will handle all crane interfaces, installation, commissioning and testing, as well as engineered lift plans for the removal and installation of the cranes using a lift barge, which is to be supplied by the main contractor, along with the new cranes. The project will be carried out in two phases, with phase one taking place onshore from the company’s Abu Dhabi facility and workshop and phase two offshore.
Charlie Topp, regional director – Middle East, India, Caspian and Asia-Pacific at Sparrows, says: “This is a significant contract win for us. We’ve got an extensive track record in the Middle East, and this contract reflects the confidence of operators and contractors in the region to utilise our expertise as part of safetycritical work. As cranes age, it’s vital that maintenance is done to prolong their life, but in instances like this, where ongoing and frequent maintenance is impacting operations, it’s crucial that new infrastructure is deployed.”
While Sparrows will undertake the majority of the scope of work, it has employed a trusted and local partner to undertake structural fabrication, electrical work, public address and general alarm systems, fire and gas systems and telecoms, as part of the full scope of work.
The company has also secured a contract worth approximately £50m with a major UK Continental Shelf operator to provide crane management services across its operating assets in the North Sea.
The five-year agreement, which also has two, two-year extension options, will see Sparrows deliver crane operations and maintenance services across ten of the operator’s assets in the region.
Sparrows has held the contract since 2018 and will continue with the provision of operation, maintenance, and engineering services to ensure the safety and reliability of 38 cranes. The scope includes development and implementation of planned maintenance routines, as well as undertaking planning and risk assessment for all lifting operations.
All onshore support will be carried out from Sparrows’ Aberdeen, Scotland, headquarters, including technical and safety audits, and repair and refurbishment work as required.
Stewart Mitchell, chief executive officer at Sparrows, commented: “This new fiveyear contract is in addition to the inspection services work, which we were awarded by the operator two years’ ago, demonstrating the high-quality service we have delivered to ensure safe and efficient operations.
“Although we have been diversifying into the renewables and onshore industrial markets in recent years the North Sea remains a core area in the business, so we’re pleased to continue working with the operator across these assets. With more than 45 years’ experience in the region, we have an unrivalled knowledge of the market and demands of the challenging environment on safety-critical lifting equipment in the field.”
Staying in Scotland, KenzFigee, the Dutch supplier and service provider of offshore and marine cranes, announced in September the relocation of its branch office KenzFigee (UK) to Altens, near Aberdeen’s South Harbour.
The company says the move from the Blackburn Industrial Estate outside of the city “marks a significant milestone in our company’s journey and sets the stage for future growth and success. The decision to relocate was made after careful consideration and extensive planning to ensure that our new facility aligns with our strategic goals and provides us with the resources and infrastructure needed to better serve our clients in the UK.”
The new location offers a modern workspace and significant workshop facilities designed to enhance collaboration and productivity.
“We believe that this new location will foster an even stronger sense of teamwork and customer-centric focus, enabling us to continue delivering exceptional solutions to our valued customers in the wind and oil and gas market. Being in the heart of the action will enable us to respond quickly to market demands, build stronger relationships, and capture new opportunities,” the company says. Garry Stuart, UK service manager, says: “KenzFigee has been a long-time service provider to the UK and we believe that our physical presence here, more so at our new location in the heart of Aberdeen, will further support the growth and development of the business. This strategic positioning will allow us to be within reach of key industry players, clients and suppliers. Altens’ accessibility provides better connectivity to key industry hubs, making it easier to serve our clients’ needs and collaborate with industry partners.
“The close proximity to Aberdeen’s South Harbour played a crucial role in our decision. With the move, we will benefit from improved logistics and streamlined operations for offshore projects. Easy access to the harbour will enable us to optimise our supply chain, expedite project execution, and provide prompt and reliable services to our clients.”
Modulift case study
UK below-the-hook lifting equipment manufacturer Modulift and its in-house engineering team designed and manufactured a bespoke lifting beam that was capable of recovering a micro tunnelling machine from the depths of the sea earlier in the year.
The 50t custom beam had to be designed for use above and below the water, taking into account the differences in the centre of gravity location and weight of the micro tunnelling machine due to the buoyancy force. Modulift’s in-house team achieved the correct tilt and balance to ensure a safe and effective lift.
At the request of the customer, a specialist in tunnelling and micro-tunnelling, Modulift engaged DNV to perform a third-party design review and certify the beam in compliance with DNV-ST-N001. The design was successfully approved in the first round of reviews, enabling Modulift to complete the project within eight weeks, from design and drawings, to fabrication, painting, and procurement of rigging.
The company engineered the lifting beam with eight lifting points, together with turnbuckles to connect the lifting beam to the tunnelling machine. The 6.7m-long beam featured two top lugs and four bottom lugs, and tugger points were installed for manoeuvring the beam into the right orientation before lifting. 3D structural analysis was carried out using Staad Pro. Finite Element Analysis was conducted on the lifting lugs and welds using Ansys software.