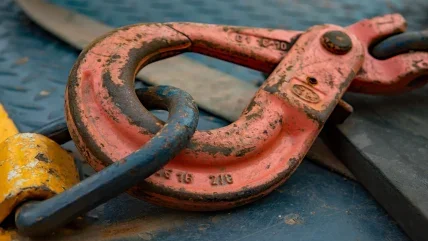
Say the phrase ‘North America’ and most listeners if they are not actually Canadian themselves will take you to mean the United States, with Canada added if you are determined to be all-inclusive. This is, of course, grossly unfair. Canada’s land area, at ten million km2, is bigger, if only by a fraction, than that its neighbour’s, which can only manage 9.8 million km2. Canada’s population on the other hand is 38 million, while that of the US is 332 million, which means that Canadians are outnumbered by Americans nine to one.
But Canada’s GDP, at $1.71trn, ranks tenth in the world, and any country with an economy that size cannot be considered a mere adjunct or afterthought – all the more so since the Canadian economy showed the greatest growth of any of the G7 countries in the first quarter of 2023, when GDP grew by 3.1%.
Such growth will provide demand in the lifting industry.
SMALLER GANTRY CRANES
Munck Cranes Inc. is a Canadianowned and operated company, and is an independent licensee of Norwegian company Munck Cranes AS. The Canadian entity has been manufacturing material handling equipment out of its base in Stoney Creek, Ontario, since 1983 and serves all of North America, as well as parts of South America, Mexico and the Middle East.
Overhead bridge cranes, gantry cranes, jib cranes, wire rope hoists, under hook attachments and transfer carts are all part of its product range. Its gantry cranes in particular range from the smallest portable ones to the very largest capacities.
Munck points to a not usually considered advantage of its smaller gantry cranes – their suitability for semi-permanent fabrication sites or for businesses that may be considering changing premises: “In recent years there has been a trend for smaller manufacturing business and fabrication shops to operate in leased properties such as industrial-style ‘mini mall’ units” it says. “These types of buildings typically do not ideally support the dynamic loads that would be forced upon the structure by an overhead bridge crane, making a gantry or semi-gantry crane solution an ideal fit for feasibility and costeffectiveness in material handling.
“Another great feature of the gantry or semi-gantry crane is portability, allowing business to relocate the entire crane with them to a new location when required. Gantry and semi-gantry crane systems remain a portable solution,” placing no constraints on the choice of an alternative location to move to when a business wishes to relocate.
That is perhaps less relevant for its larger gantries, which as well as more conventional applications find outdoor uses in construction projects, in particular recently on the repair and reconstruction of bridges. Current projects, south of the border in the US, include on the I- 140 Valley Bridge in Ohio, where deck replacements on the existing 40-year-old structures, plus the construction of a new bridge, neatly sandwiched between the westbound and eastbound piers and carriageways of the existing structure, will carry four extra lanes in each direction. Munck has supplied three 50-ton custom overhead gantry cranes, which have been used not only to erect structural steel but also to support the entire superstructure. In total, 203 girders have been placed across 15 spans on the new centre structure. The project is due to be completed in autumn this year.
The Mile Long Bridge on Central Tri-State Tollway (I-294) in Illinois, US, built in 1958, is now in need of renovation and enlarging. It is a critical piece of infrastructure as it carries eight traffic lanes over two major railways, the Des Plaines River and two canals, as well as local roads and also over a major distribution centre for UPS and Burlington Northern Santa Fe Railway.
The $500m project includes construction of two new bridge structures by Walsh Group that will increase capacity to five lanes in both directions. In addition, the inside shoulders will be built to serve as additional flex lanes that can be used for a variety of needs.
The new Mile Long Bridge will include two, side-by-side 4,800ft-long carriageway structures. Each will have 27 spans supported by 26 piers, compared to the 53 piers supporting each of the original bridge structures. The reduction in pier numbers is to reduce the environmental impact on the waterways and industrial areas below.
For the project Munck supplied three 30- ton custom-built double girder overhead gantry cranes, with load measurement systems reading out to digital displays mounted on trolleys. Laser distance detection monitors the distance between cranes when they are operated in tandem. Power is from a generator mounted on the end truck sill.
The gantries are 28ft tall and 145ft wide. They extend from the existing southbound bridge structure across to the newly constructed northbound bridge structure. They run on rails installed on both existing structures. During beam placement each gantry is controlled by a crane operator.
Gantries are positioned on each end of the beam as they are hoisted into place, and the third gantry can be used to hold the beams in position while the other two gantries move to deliver the next beam segment into place.
Using gantries instead of traditional cranes allows beams to be installed in areas that are difficult to access from below and that would otherwise require barges, large cranes, and heavy lift equipment. The gantry system also allows four lanes of traffic to remain open in both directions on the bridges as the beams are installed. Some 150,000 vehicles flow daily on either side of the gantries with no impact to traffic as well as reduced impacts to industrial ship traffic on the canal beneath. All work on the project is scheduled to be complete by the end of 2023.
NAVIGANTRY
Also heavily into gantries is Motivation Industrial Equipment of Woodstock, Ontario. It also makes pallet lifters, floor cranes, forklift crane booms, hydraulic box dumpers and wire rope hoists. But its Navigantry is a patented product of its own. It is an electrically powered fully steerable gantry crane, which the company says eliminates the need for fixed or trackmounted gantries. It runs on steel, urethane or phenolic wheels, or can be track mounted if desired. As with Munck’s product it too is designed for use in lightweight industrial buildings that lack the structural strength to support a bridge crane.
The Navigantry is constructed from cross-braced steel A-frames angle braced to a self-levelling underslung beam and can be used with almost any type of hoist required. A-frames at each end have a drive wheel, powered by an electric motor, that can be independently controlled by colourcoded forward and reverse buttons. It has a soft start and gradual torque build-up to minimise load sway.
Because the wheels of the Navigantry are fully steerable the crane has endwise travel as well as being able to move forward and backwards. It steers left to right and can even pivot on its axis – which Motivation says is a unique capability within the industry. It can traverse from bay to bay or even into and out of the workshop.
Standard models have up to 10-ton capacity and 30ft span. Motivation’s engineers will customise the machine to fit other requirements.
WF Steel and Crane is based in Alberta, Western Canada, and specialises in custom overhead crane solutions. Oil and gas, power generation, manufacturing and mining are all areas of expertise. At the end of last year it expanded its premises, adding 25% more production space to a total of 48,000ft2 for steel processing and fabrication.
A recent client was the Cascade Power Project, a 900MW combined cycle power generation facility being constructed in Yellowhead County, Alberta. WF Steel and Crane supplied two 140t cranes for the turbine rooms. Each was totally customdesigned to the client’s specification. They are top-running double girder cranes, each with a 22t auxiliary hoist as well as the 140t main hoist. Because of the capacity and high lifting height required the main hoists were of custom-order open winch style. All the motors are powered by variable frequency drives. WF also supplied around 385,700lbs of concrete test weights and a testing skid to carry out the load test. There was very limited space for load testing, but WF’s project manager presented a solution that was executable. Covid-induced supply-chain problems were overcome without affecting delivery times and the cranes were commissioned and tested in April last year.
ELECTRIC HOISTS
Vulcan Hoist, based in Montreal, claims to be the only Canadian manufacturer of electric hoists and trolleys. Established in 1947, it nevertheless has company links back to the invention of the three-motor overhead gantry crane in 1884.
The inventor of the gantry crane in its current modern form was J.H. Whiting, owner of the Whiting Foundry Equipment company of Harvey, Illinois, US. The three motors in his design powered lift and travel vertically and along both horizontal axes, giving full lift and travel over a complete rectangular area. The overhead gantry, now established in the form we know it today, was a godsend to the still young and expanding railway industry of the time, which was for the first time able easily to lift and move entire carriages and locomotives in their repair shops.
Whiting expanded into Canada in 1930, establishing a sales office in Toronto and some years later a manufacturing plant in Welland, Ontario. In the 1960s, the Vulcan Hoist Company in Montreal bought the fabrication rights for Whiting hoists and has since been improving on and modernising them, while maintaining the original Whiting quality and robustness.
Current Vulcan products include electric chain hoists of up to 15t capacity, in one- or two-speed models. The Vulcan engineering team has developed a second safety device installed in addition to the limit switch, an additional measure intended to increase protection and safety when using the hoist. Called Safety Stop, it replaces the chain guide on single- and double-fall electric hoists and is designed to prevent collisions caused by obstacles such as the hook or knots on the chain. It consists of two springs through which the chain passes, and a balance.
If an obstacle comes into contact with Safety Stop, the spring compresses to absorb the impact, causing the balance to pivot. This rotation activates a switch that immediately stops the high or low signal from the pendant or radio controller, depending on which side of the Safety Stop is activated. This series of steps ensures that no obstacles on the chain can collide with the hoist.
Once the chain is stopped, simply running it in the opposite direction will return the balance to its original position, and operations can continue.
Vulcan custom-builds products to meet clients’ specific needs. Its products comply with ANSI B30.16 or B30.21 standards and are CSA certified.
75TH ANNIVERSARY
Finally, Canada has some international names in the business. One is Timberland, a large and diverse company headquartered in Ontario. Recently, it celebrated its 75th anniversary. Hoisting, winching, pulling and tensioning systems are only part of its remit but a central part – its winches, hoists, mooring systems, capstans, sheaves, A-frames and derricks – are in service in more than 50 countries as well as offshore. It has supplied hoists for spillway and water control gates for Tennessee Valley Authority (TVA), for the Brilliant dam in British Columbia, Tionesta Creek lake in Pennsylvania, and on the upper Mississippi.