Training crane operators can improve safety in factories and reduce maintenance costs, argued speakers at Crane Safety 2004, a conference held by Hoist and sister magazine Cranes Today in June.
According to a straw poll conducted by Derek Reece, managing director of KCI Konecranes Benelux, 35% of service calls were due to misuse of the crane, and 60% of those were due to a lack of understanding of the crane operation, or inadequate training. In other words, customers could trace maintenance costs directly to operator misuse.
Reece reported that it was hard to tell whether operators misusing a crane did not know better, or simply did not care: ‘It is difficult to differentiate between lack of training and lack of due care without knowing the customer’s training history and culture.’
Reece concluded that training can foster a culture of care and attention that prolongs the in-service life of the crane, which improves safety in the working environment, and also production volumes. (See also ‘How to organise training,’ Hoist 33, p.19).
In the USA, overhead crane training remains unpopular, reported Phillip Kinser, technical coordinator for the National Committee for the Certification of Crane Operators, which runs a scheme to test mobile crane drivers. The group is developing a certification programme it plans to launch next year. ‘The whole reason for certification is because no one is getting their training,’ he says. Like the mobile crane operator training scheme, the programme will consist of a written theoretical test and also a practical examination.
The risks of overhead materials handling can scare off operator candidates, Kinser said. Operators are more likely to go into jobs without lifting, such as driving excavators. (See also ‘Operator certification scheme may require training course,’ Hoist 33, p.2).
Well-trained operators and the right equipment help prevent hoisted loads from falling, argued Rolf Lovgren, president of CranePoint International. Operators can be trained to position the crane bridge directly above the load, so that when the load goes up it does not swing. Control devices can also reduce or damp out load swing, lessening the risk of a load slipping out of its rigging and falling to the floor. Also, large loads, such as tubes, can fall if they are lifted without the correct rigging, he said.
Lovgren also argued that a planned maintenance programme can cut costs. He argued that when General Motors implemented a preventative maintenance programme on 500 cranes, ongoing maintenance costs fell by more than half, because there were far fewer emergency repairs.
At the same time, he argued that some manufacturers are over-specifying maintenance. On a good crane, the service interval should be 100 to 200 hours, he added.
His research found that items that failed most frequently on overhead cranes were wheels, mostly because they weren’t lubricated enough, wire rope, because of kinks and strand breakage, sheaves, because they weren’t lubricated enough, and control panel enclosures primarily because of failures of contact tips.
Load limiters are the first line of protection for cranes and their operators. Ivar Horst, managing director of load limiter manufacturer Piab, argued that its devices, which mount on wire rope, measure rope deflection as an indicator of load, and pull on the upper limit switch, can be retrofitted to old cranes. Because they do not affect the load-bearing mechanism of the crane, the crane does not require recertification. Horst said that Piab’s mechanical version relies on the resistance of spring washers, requires no power feed, and resists physical damage. Piab’s electronic limiter, which uses a transducer, can also function as a datalogger.
The safety of a crane depends partly on those examining it. Many standards specify that a competent person perform a periodic examination of the crane, to make sure it is safe to use. But most standards do not qualify what constitutes competence. Derrick Bailes, chief executive of the Lifting Equipment Engineers’ Association, argued that LEEA is the only UK organisation to have done that job. In particular, he said that in order to be competent, inspectors need a good theoretical knowledge base, sufficient experience to be able to have good judgement, an enquiring mind, and no pressures due to conflicts of interest. Although legislation in the UK and other countries requires a competent person, it usually does not define what characteristics are sufficient for competence. He argued that this person needs plenty of time and a degree of freedom to perform the job well.
In his presentation on an automation job at an Italian steel mill, David Stocker, systems engineer for TM GE Automation Systems, reported that maintenance costs actually fell after the cranes were automated. The system was more gentle with the cranes and steel grabs than operators had been. If the automation system reduces the amount of swinging and unpredictable movements of crane grabs, the warehouse could be safer for any riggers or slingers that happened to be on the floor. Stocker added, though, that because automated cranes have a mind of their own, and cannot always sense the presence of people, it is important to make sure the site cannot be entered. The job was previously reported in Hoist (issue 31, p. 13).
The two-day conference, held in London in June, drew an audience of 170 from a total of 17 countries. Other presentations covered topics such as lift planning, crane maintenance and maintenance planning, working at height, wire rope selection, maintenance and drum spooling, wireless rated capacity indicators, data logging, simulators and screening potential crane operators, CE marking, and more. Crane Safety 2004 was organised by Cranes Today and Hoist, and sponsored by the Certex group, Hitachi-Sumitomo, Liebherr, Manitowoc Crane Group, Sparrow Crane and Terex Cranes.
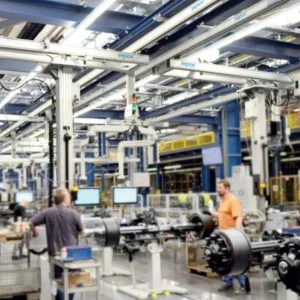