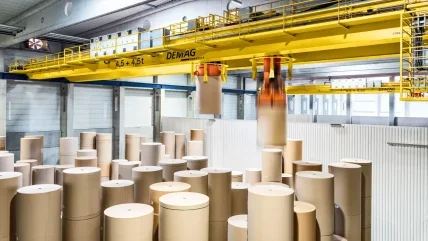
Heimann GmbH & Co. KG is a German company that manufactures steel structures for a range of applications – from special plant construction, mechanical engineering and municipal utilities to complete industrial buildings. With the addition of a new workshop, the company has expanded its central site to 18,000m2 of production space, where mainly steel sheets will be prepared – through various process steps such as cutting, grinding and straightening – for installation.
Heimann planned the flow of materials taking into account the fact that components with very different shapes, dimensions and weights would be handled there, and placed great importance on the design of the transfer points. This resulted in an integrated handling system that is flexible and meets all the requirements of the specific lifting and handling tasks.
“Heimann sometimes prepares very large and heavy steel sheets for further processing – for example, in workshop construction, with operations such as flame cutting and straightening. The environmental conditions are rather harsh and the cranes are expected to be highly reliable and available,” says Tilo Kupfer, the Demag sales engineer responsible for delivering the cranes on the Heimann project.
“It was also important for our customer that the operator feels ‘at home’ when changing workstations.” Kupfer says the company “attaches great importance to safety and ergonomics” too.
The components are transported on two levels: firstly, crane systems feed the cutting machines, and, secondly, workstation cranes support the processing steps.
Three Demag cranes on a common crane runway handle the steel sheets removed from the warehouse. Two singlegirder cranes and one double-girder V-type crane with 10t and 12.5t load capacities are used. All three are equipped with infinitely variable long and cross-travel drives, the frequency inverters of which make it easier for the crane operator to avoid load sway during long travel.
Several crane systems from the KBK modular crane system handle the blanks and components at the workstations. Two KBK monorails with a track length of 12m and 29m provide point-to-point handling. Power is supplied through a KBK II-R profile section via an integrated conductor line, eliminating the need for externally visible power supply cables and any risk of collisions.
KBK single-girder and double-girder suspension cranes serve the workstations. The KBK double-girder crane has a runway length of 20m, along which a crane bridge with a span of 4.2m travels under electric power.
“In my opinion,” Kupfer says, “the exciting thing about planning the KBK system was the directly parallel arrangement of cranes and monorails. We thus created the conditions for the operators to transfer workpieces to the work areas without the need to set them down.”
Among the hoists used are nine Demag Manulift chain hoists. Each one is operated with just one hand using the control handle, with the load controlled by thumb using rocker switches.
The Manulift hoists are used, for example, for the precise positioning of components at workstations across various production centres and as travelling hoists for the KBK single-girder cranes with different runway lengths and spans. Two particularly short crane girders with a span of 1.1m stand out – these help to load manufactured metal parts from a pallet onto the roller conveyor of a roller straightening machine and back onto a pallet after the production step is completed.
All cranes are equipped with Demag’s SafeControl system, which continuously monitors all relevant functions and movements, including overlapping movements. It can bring the system to a standstill independently if any irregularities occur, while dangerous conditions can be identified and prevented in advance.
The first meeting
Tilo Kupfer, the Demag sales engineer responsible for delivering the cranes on the Heimann project, discusses the information that needs to be collected when meeting a customer for the first time.
“First of all, the customer describes which processes they would like to carry out in the new workshop or with the new lifting equipment in the future and where the lifting operations will take place. The properties of the stored goods – in particular their dimensions and weights – play a role, as do the user’s objectives – for example in terms of flexibility and throughput.
“This results in a basic concept for the selection and number of cranes… which will be further refined over the course of the project. This includes a discussion of safety, ergonomics and operation, among other things. Are variable-speed drives required, which level of positioning accuracy is required, and which lifting and load handling devices are used? Should cranes work in tandem and, if so, where? Do loads need to be turned over? These are all questions that need to be answered before we can start working on the concept in more detail.”