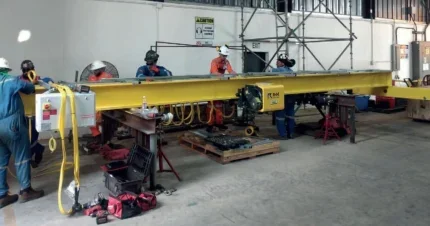
The latest research study on the global Electric Wire Rope Hoist market finds that the global Electric Wire Rope Hoist sector reached a value of USD 453.17 million in 2023 and is expected to achieve USD 665.16 million by 2030, exhibiting a CAGR of 5.64% during the forecast period, according to Kingpin Market Research (KMR).
In order to meet this demand, SWF Krantechnik has launched its wire rope hoist NOVA2 rope, continuing the success story of its NOVA wire rope hoist and at the same time introducing the next generation of electric wire rope hoists.
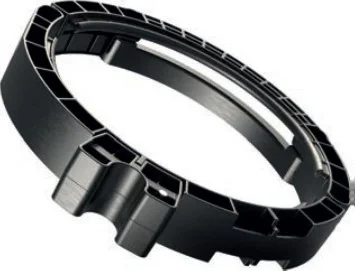
“This new series sets the course for a comprehensive redesign of the classic wire rope hoist, which is not only based on innovative materials, but also on advanced design and functionally optimized components. Other key topics that have been incorporated into product development deal with user-friendliness, sustainability, digitalization, monitoring, control, service, and maintenance,” said Karlheinz Schäfer, product manager Wire Rope Hoists, SWF Krantechnik.
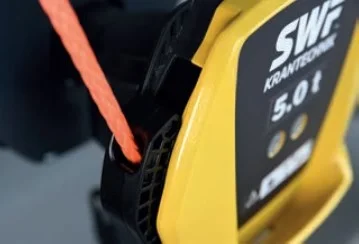
The entire structure of NOVA2 rope has been redesigned. As an alternative to conventional steel rope, it can be equipped with a high-strength synthetic rope made from a chemically produced fibre structure based on polyethylene meaning it is 90% lighter than steel rope.
“The new rope guide completely encloses the rope drum and contributes significantly to the safety, efficiency, and durability of the crane system. In addition to the perfect rope guide, in which the rope is reliably and precisely guided in the correct groove, it has a high level of strength. The rope guide is highly resilient, robust, spark-resistant, and UVprotected. Due to the design, a slack rope is prevented during operation and the wear of the entire reeving system is minimized. The user also benefits from noise minimization when lifting and lowering the load,” added Schäfer.
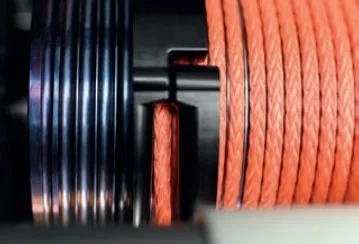
The rope drum has bearings that are maintenance-free and lubricated for life. Both the synthetic rope and the steel rope can be used on the same rope drum.
The rope drum can be converted from synthetic rope to steel rope at any time. Only the rope attachments are different for the two types of ropes. The hoisting motor with brake and the gearbox are located on the outside of the drum. This arrangement makes maintenance easier for the service technician.

The hook block is identical for the rope made of steel and synthetics. NOVA2 rope also offers an ergonomic hand pocket in bottom block, which ensures easy and reliable guidance of the hook. For user-friendly maintenance, lubricating the axial bearing of the RSN hook (DIN 15401) is effortless. SWF Krantechnik relies on two driven wheels that provide maximum traction. This ensures safe and precise movement of the load. The use of thrust rockers and/or counterweights ensures balanced driving characteristics of the hoist. The wear-reducing guide rollers also contribute to quiet and almost smooth movements.
In addition, equipped with the digitally networked hoist monitoring system OMNI control, the frequency inverter VARIO control and intelligent electronic monitoring and control features, users can get their crane solution ready for the digital future.
In addition to Crane Intelligence control and monitoring features, SWF Krantechnik is introducing three new rope angle measurement features. They are based on continuous sensory rope angle measurement. If predefined values are exceeded, the control options support the user fully automatically. With the Easy Following function, the operator “controls” the crane manually via the empty hook. Crane and trolley follow independently in the desired direction.
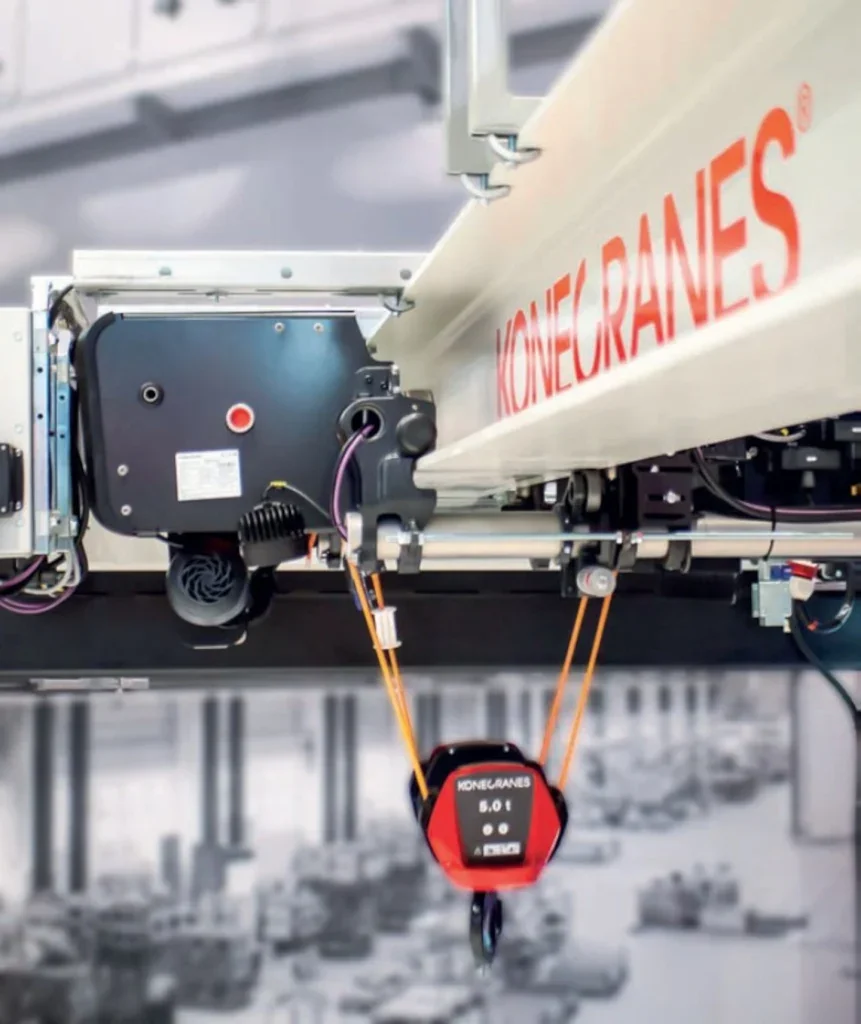
With the Easy Centering function the crane and trolley automatically centre themselves directly above the load when lifting. Side pull is thus reliably prevented. With the Easy Prevention function the crane slows down and stops on its own if a hook, sling, or load accidentally collides with or gets caught with another object. The Can-Bus technology is used to connect the different components and sensors with each other and allow them to communicate.
“With NOVA2 rope, SWF Krantechnik anticipates the changes in the market and offers solutions for the challenges of the 21st century in the hoist industry. With the new wire rope hoist, the company is also optimizing its production process. Thanks to a flexible and robust frame structure as well as the use of fewer components and modern materials, SWF Krantechnik is revolutionizing the wire rope hoist market today just as it did 20 years ago,” added Schäfer.
One of the pioneers of synthetic wire rope hoists is Konecranes. In 2019, it launched the S-series hoist and since then has introduced a low headroom version of this series with the X-series crane, claiming it is the first company to produce overhead cranes with synthetic rope as a default made with Dyneema – one of the world’s strongest fibers, which has been used for more than 30 years in demanding rigging applications such as lifting slings, mooring and towing large sea vessels.
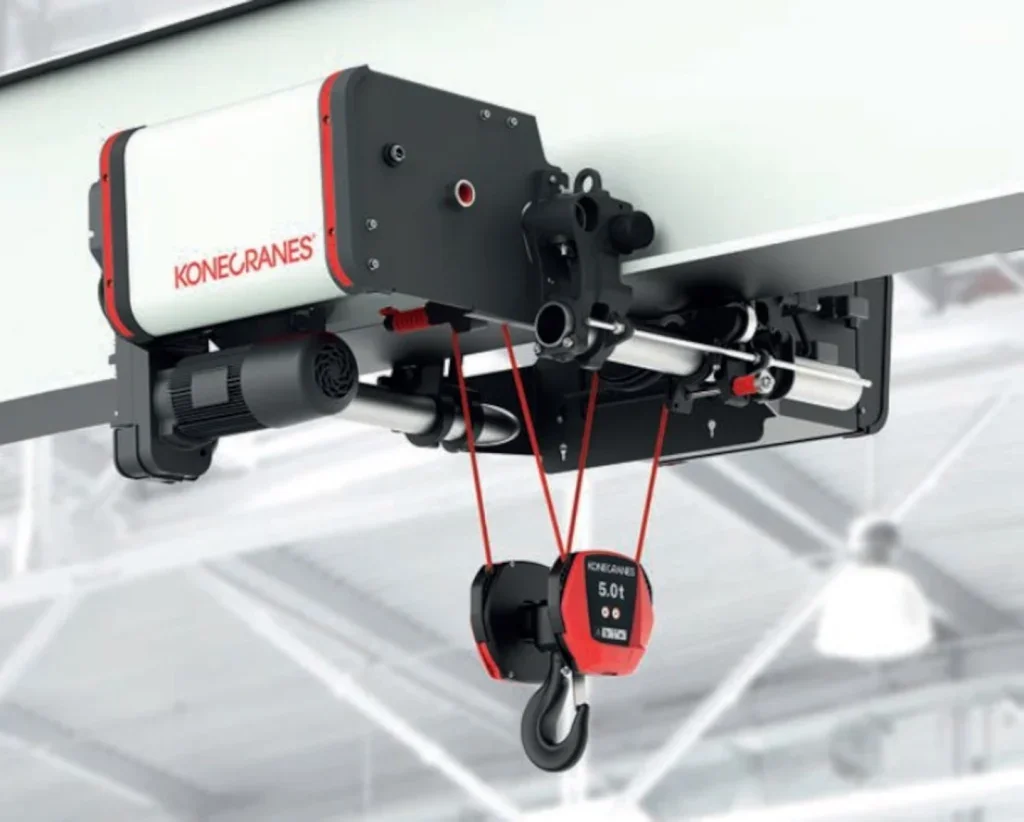
According to Jussi Luokomaa, product manager, Standard Cranes, Konecranes EMEA, the Konecranes X-series crane, is quite literally what’s new on the market with sales now in Europe, and other regions to follow.
“The X-series is the successor to our popular CXT model with a new compact design and safe, reliable technology that, thanks to its wireless upgrade capabilities, can adapt to customer needs now and in the future. We’ve already sold the very first X-series cranes in Central Europe, and initial customer feedback has been excellent. We use this feedback to further refine and develop our products and how can we improve to also meet customer requirements in the future,” he said.
“The Konecranes X-series is a safe, smart, and strong crane that boosts productivity in a safe, connected way. The wireless technology of the X-series crane creates a foundation for easy upgradeability in the future, as well as providing access to important crane data 24/7 through our customer portal, making predictive maintenance easy.
“The new crane includes innovative features and lifting capacities of up to 10 tons, and soon up to 20 tons when the double-girder version is launched in early 2025. There is also a smooth, stepless lifting motor and the CANMAN radio controller, featuring real stepless buttons that operate much like a car’s gas pedal.
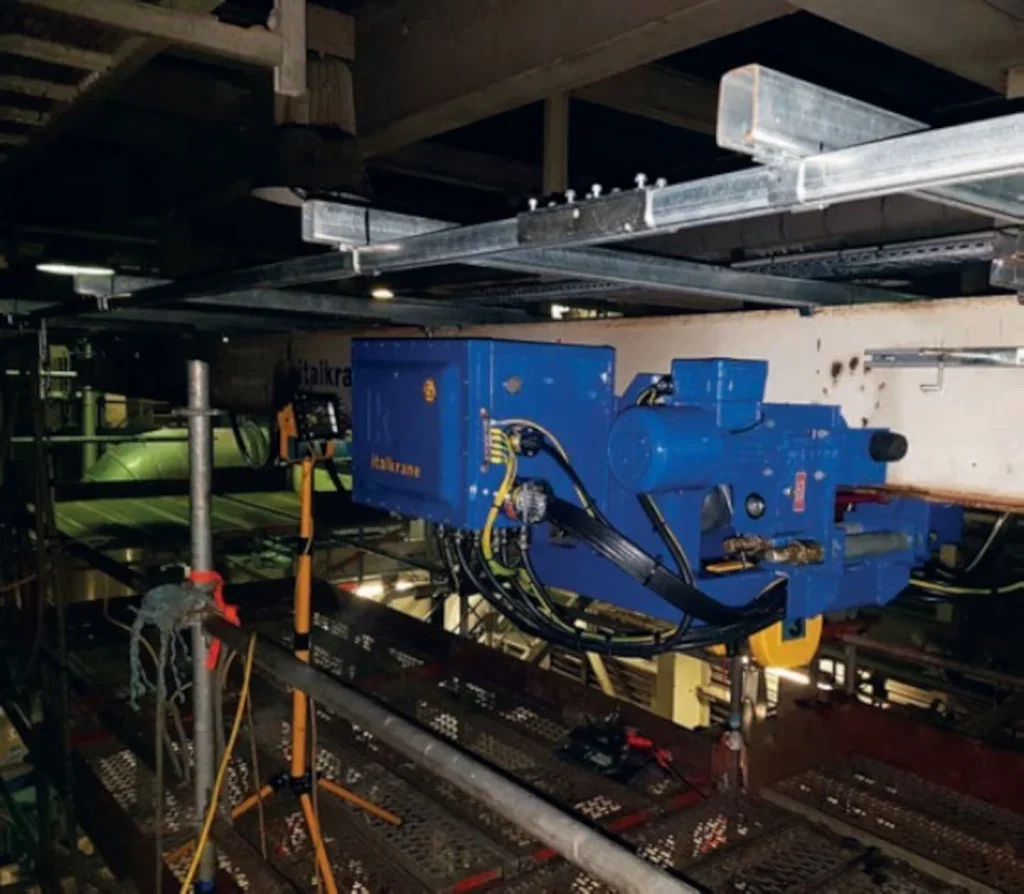
“And there’s something very important about the X-series: its incorporation of sustainable design choices, including a compact motor, synthetic rope, and optimized components that reduce environmental impact. The use of lightweight, durable synthetic rope improves safety and handling, while the optimized belt drive and inverter lifting technology minimize energy waste and extend the equipment’s lifespan.
“The CXT was launched way back in 2000, and to date has sold well over 100,000 units globally. We expect good demand in the years to come for the X-series across multiple industries. That’s because the market at the moment is putting a high premium on scalability and advanced safety features, and on cranes that can offer precise, frequencycontrolled, stepless motions.
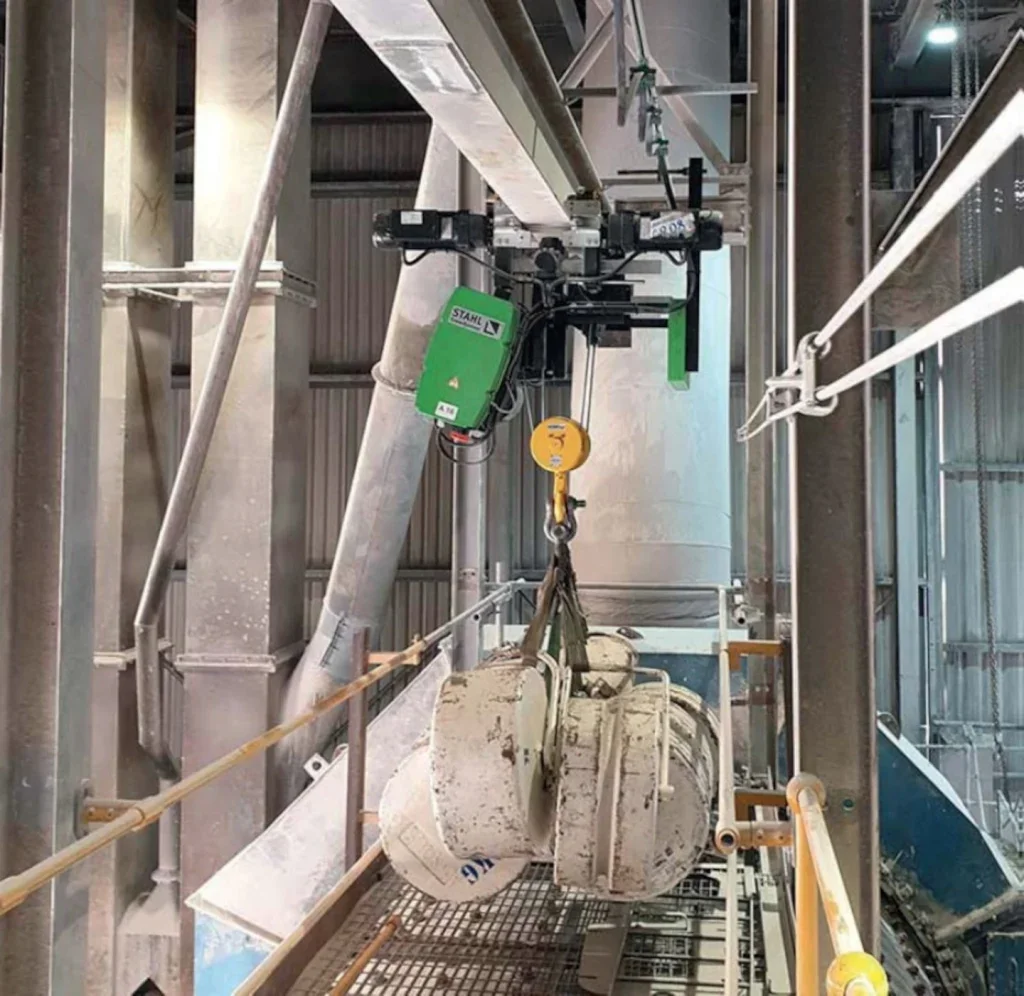
“Competition within smaller loads, under 10,000kg is picking up in Europe, and Konecranes is meeting this with its scalable products. We have a solution for every customer requirement, from standard robust cranes to more advanced smart cranes.
“Customers also seem to lean more and more towards frequency-controlled, stepless motions in lifting, and that is where Konecranes has been strong throughout the years. We are now even stronger because of the new real stepless control buttons of the CANMAN radio, which increases both safety and usability significantly in our cranes. We are absolutely able to meet that demand.”
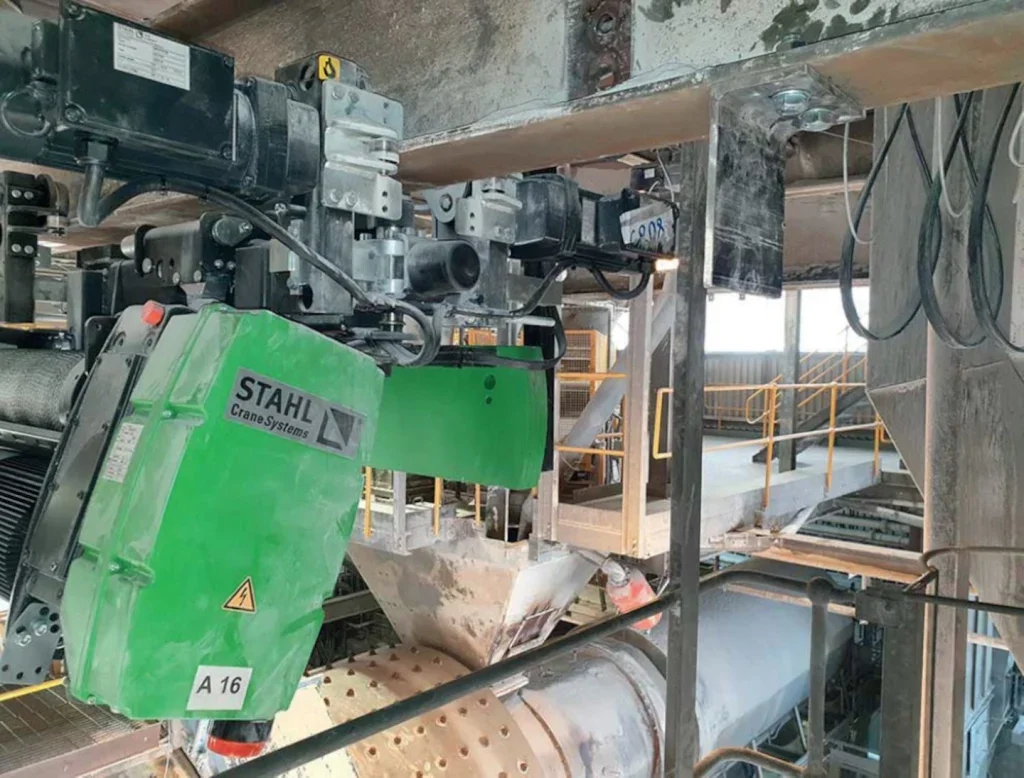
In the UK, Andy Allen, director, Hoist & Winch, based in Winchester, says the overhead crane market has always predominantly used wire rope hoists in its manufacturing, aside from when a more cost effective electric powered chain hoist is preferred for up to around 2t SWL(Safe Working Load) for low to medium duty applications.
“However, we find for more permanent installations with low to medium duty, more standard monorail beams or jib crane hoisting applications in general industry, electric powered chain hoists are more often found up to around 5t SWL when compared to wire rope hoist units as these are generally more cost effective and offer more compact overall dimensions than wire rope hoist units,” he said.
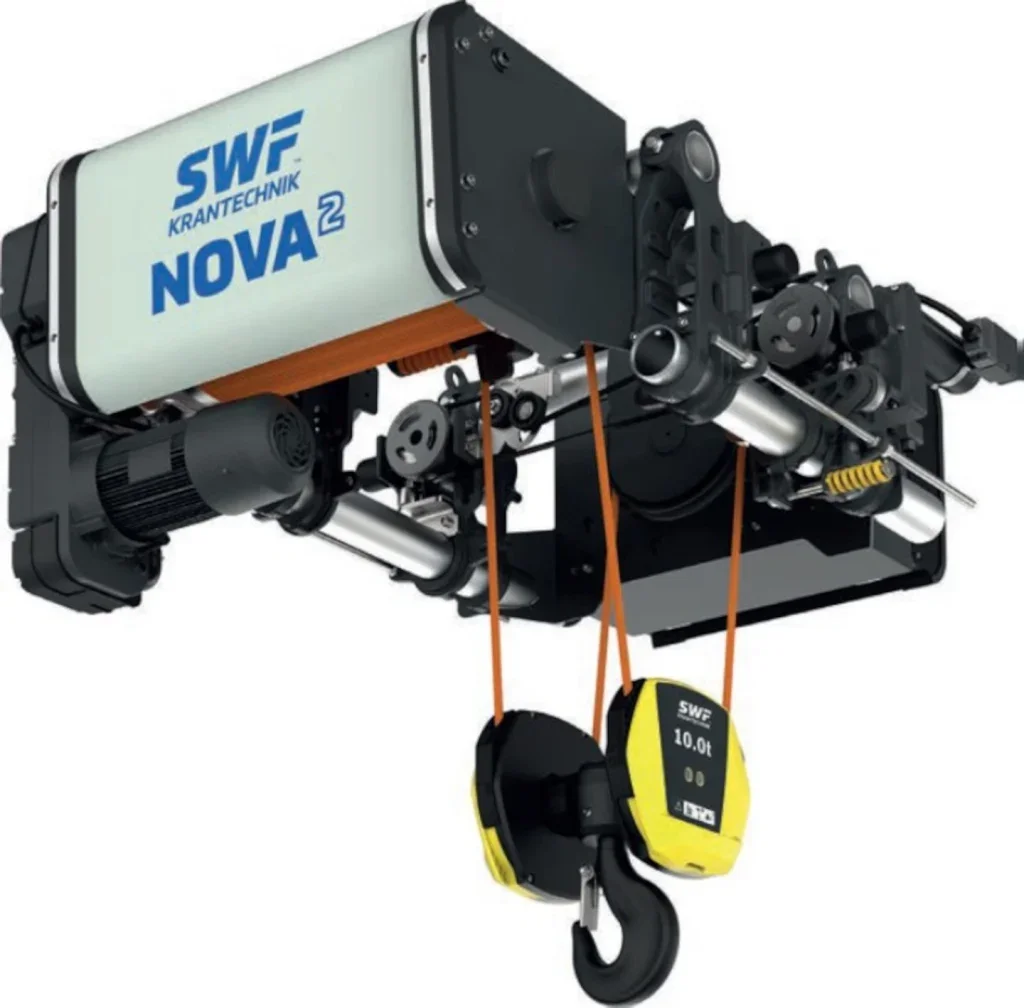
“Above 5t SWL, whilst larger capacity electric powered chain hoists are available they tend to have comparatively slow operating speeds and we find are most often are only used where there are dimensional restrictions and their use is occasional e.g. maintenance applications or their use is for temporary hire purposes during plant installation projects.
“We therefore find for monorail beam applications wire rope hoists are most often only used for larger capacity applications or where longer heights of lifts are required with faster operating speeds than chain hoists can offer, or for special applications where rack and pinion drive is maybe required e.g. marine application, where articulated hoist trollies are required for curved monorail beam applications, or for higher duty applications in heavier industries.
“Finally, in hazardous area industries where there is a risk of explosion and electric powered hoists are preferred rather than manual or air powered hoist, wire rope hoists are generally used for applications above 2t SWL as most manufacturers of ATEX rated electric powered hoists only offer a electric powered chain hoist solution up to around 2t SWL from our experience.”
Recent projects by Hoist & Winch include; handling the annual powered lifting equipment service requirements, emergency repair and new project installation work at two of the largest UK Cement Production Works as well as providing the same services on a UK wide network of smaller subsidiary Cement Industry sites.
Working in the Cement Production Industry can be very challenging due to the arduous operating conditions, 24/7 production demands and safety critical nature of the industry. For this application the customer was re-commissioning a cement mill which had been mothballed for a number of years. H&W was tasked with surveying the existing 5t SWL wire rope hoist unit operating above the mill and advising on its suitability for continued service.
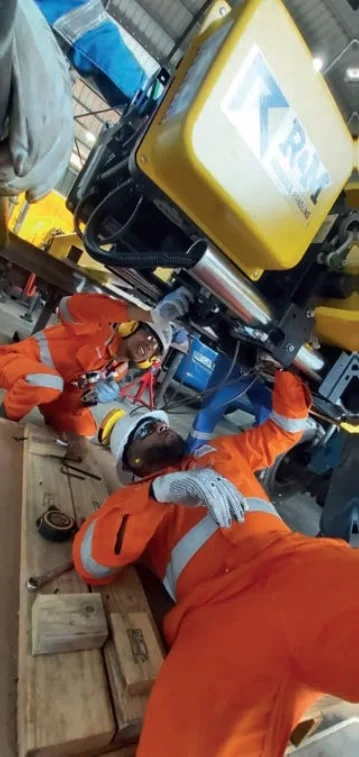
“Our examination of the existing 5t SWL wire rope hoist unit identified that this hoist unit was supplied without an overload protection device and mains contactor safety circuit as these features were not a mandatory requirement at the time the equipment was originally supplied. In addition, the electrical control equipment cabling fitted to the hoist unit was in a poor condition and required replacement/ upgrade, whilst a hard wired mobile pendant control was fitted to the existing hoist unit although the application was best suited to a remote radio control system,” said Allen.
“After reviewing the costs of refurbishment of the existing equipment compared to provision of a complete new wire rope hoist unit and preparing a detailed report for our customer it was decided that it would be more cost effective to supply and install a new 5t SWL wire rope hoist unit fitted with a remote radio control handset system.
Another project was the supply, installation and load testing of electric powered wire rope hoists for use on three off Royal Fleet Auxillary Troop Carrying Ships in dock for a re-fit program.
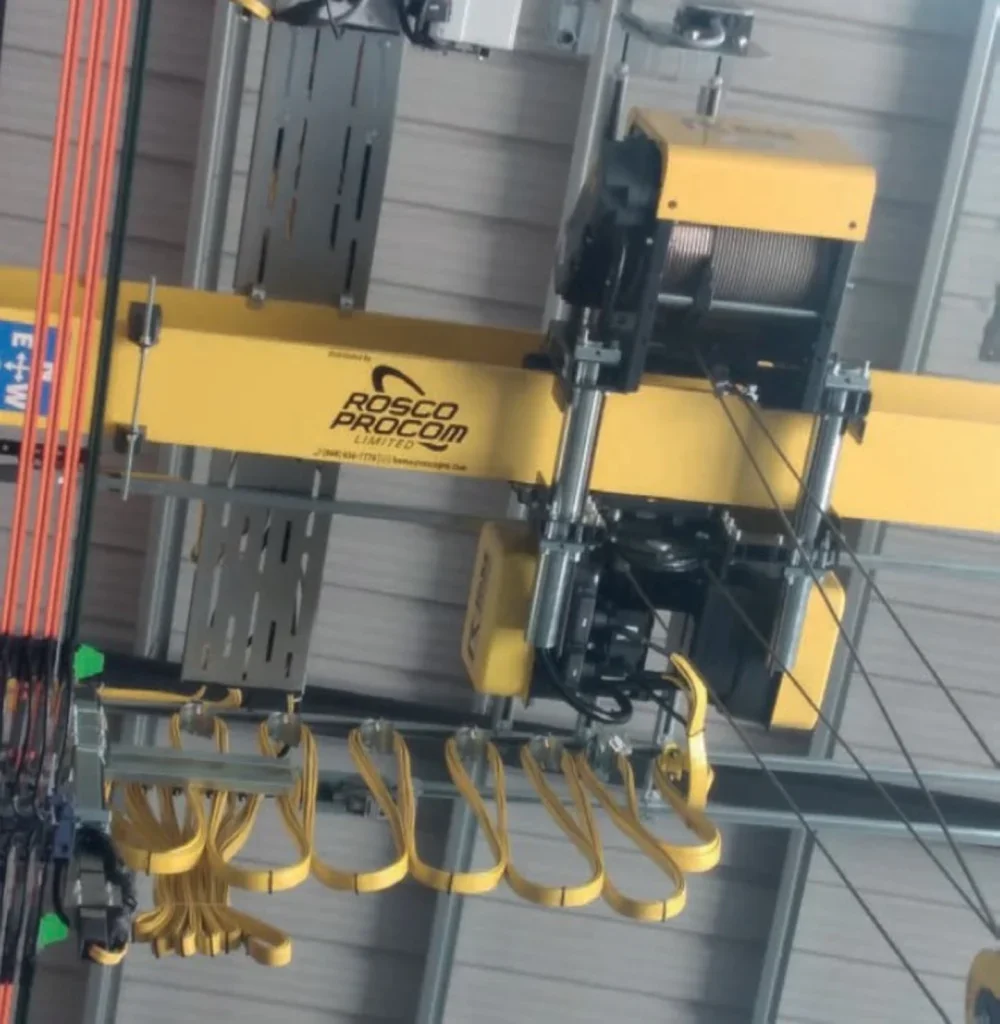
The tendering process called for Hoist & Winch to carry out a pre-tender survey on one of the three – off troop carrying ships to check overall hoist dimensional clearances within the tight confines of the ship, and to discuss and recommend hoist operating speeds. These hoist units were also required to feature a rack and pinion cross travel drive motion feature to still allow the hoist units to operate, subject to the wave motion applied to the ships during day to day service.
Following order placement, Hoist & Winch first carried out a hoist unit General Arrangement Drawing approval procedure to confirm details of the equipment to be supplied, and to verify the end client requirements before manufacture commenced. This was followed by a staged hoist installation programme over a twoyear period for the three off ships, which also included load testing of hoist runway beams installed by the dockyard.
To facilitate hoist installation, Hoist & Winch worked from a mobile scaffold tower using four – off Yale manual chain hoists and two- off “T” Bar design lifting frames clipped to the top flange of the hoist runway beam.
Handover on completion of all work included handover by the RFA Ship chief engineer, as well as the dockyard project manager.
On completion, Hoist & Winch issued a LOLER Thorough Examination Report for the completed electric wire rope hoist with rack and pinion drive and the hoist unit runway beam installation work.
All site installation work was again subject to very stringent planning requirements, which required very carefully documented Risk Assessments and Method Statements, which were reviewed/agreed by the project manager and the safety department before any work could commence.
Finally, Rosco ProCom, a distributor of R&M in Trinidad and Tobago, recently completed the installation and supply of an R&M Spacemaster SX 5 t wire rope electric hoist at Asequith Engineering and Contracting, an engineering and fabrication company in Point Lisas.
Sean Corson, director, sales, Latin America, R&M Materials Handling, said R&M electric hoists offer the lowest headroom and best wheel loads while providing near true vertical lifts with single reeved hoists.
“Asequith Engineering did the structural engineering design and fabrication inhouse and Rosco ProCom did the subsequent installation and load testing. We are now waiting for an order for another crane kit for Asequith’s location in Trinidad and possibly two to three more in 2025 for the location they broke ground on in Guyana,’ he added.