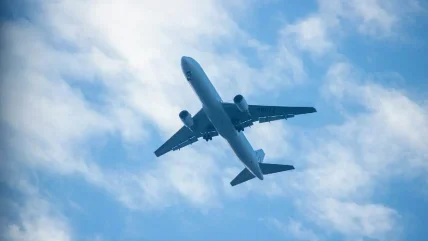
It’s been one year since Airbus Defence and Space developed and tested a loading system to lift outsized military cargo into the Airbus Beluga A300- 600ST aircraft.
The capability was successfully tested during an exercise with the German Armed Forces, the system’s first customer, by loading a CH53 military medium-lift helicopter into the Beluga.
Since then, the operation has been gathering pace – with its first two A300- 600STs now traversing the globe delivering special payloads for customers. The third aircraft will join the fleet later this year, and by the end of 2025 all five Beluga ST airframes should be in operation.
"The demand for outsized air cargo capability is on the rise. Capacity is scarce and, in light of current geopolitical developments, many customers are looking for new, fast and efficient solutions. This is exactly what we offer with our BelugaST fleet,” says Michael Schoellhorn, CEO, Airbus Defence and Space.
“Our teams have been working on a remarkable solution to facilitate a speedy, efficient and autonomous handling to load heavy military cargo onto the aircraft. Speed, agility and autonomy are crucial elements for our customers when it comes to such operations.”
The self-funded cargo loading system and jig, developed by engineers at Airbus Defence and Space, have now been unveiled to customer reps from international armed forces following the verification event in Manching, north of Munich.
The system was developed and manufactured in one and a half years – from the initial exchange of ideas with the German customer to its verification. The system enables arrangements for the loading of a CH53 in a reduced state of dismantling to be completed within less than 90 minutes while the actual loading process into the Beluga aircraft can be accomplished in about an hour.
The total lifting capacity of the system, which requires no crane for its use, reaches 35 tons and can be relocated to the aircraft’s destination.
“Together with ATI we’ve made great progress in the first year of operations: we performed six real missions with payload, which means we could really convince Airbus Helicopters and Airbus Defence and Space (ADS) about the confidence they can place in our solution to deliver their outsized cargo to their customers anywhere in the world,” says Benoit Lemonnier, MD, AIBT (Airbus Beluga Transport) part of Airbus Transport International (ATI)
The first mission – to deliver a new Airbus H225 helicopter from Marseille, France to Kobe, Japan – was followed by four more H225 deliveries to Singapore and one ACH160 to Sao Paulo in Brazil.
LIEBHERR
It’s well-known that Liebherr-Aerospace – the aerospace equipment manufacturing division of Liebherr, which also makes lifting equipment – and Rolls-Royce have a 50:50 joint venture called Aerospace Transmission Technologies (ATT) to develop manufacturing capability and capacity for the power gearbox for Rolls-Royce’s new UltraFan engine.
Rolls-Royce has started high power testing of the gearbox for its UltraFan engines, due to come onto the market in 2025. It will offer at least 25% improvement in fuel burn compared with the first generation of Rolls-Royce Trent engines.
The gearbox is a key component of the UltraFan design, which will be the UK firm’s first geared engine design. In geared engines, like the Pratt & Whitney PurePower family, a power gearbox between the fan and intermediate pressure compressor allows the fan to run at a different speed from the compressor.
Tests are taking place at Rolls-Royce Power Gearbox (PGB) facility in Dahlewitz, Germany, where the gearbox will ultimately run at up to 100,000hp.
The manufacturing of the components is initially being done in existing Liebherr facilities, in its Friedrichshafen plant, which is Liebherr-Aerospace’s centre of excellence for helicopter and aircraft gears and gearboxes, and at its plant in Biberach an der Riss (Germany), which specialises in the manufacture of planetary gears and other components. These are used in products such as Liebherr cranes, mining trucks, earth moving applications, port equipment and wind power plants. As production volumes increase, the joint venture will look at options for creating a standalone manufacturing infrastructure.
Apart from Liebherr’s know-how in the production of gears, ATT also benefits from the group’s expertise in machining centres for gears, which it has been developing and manufacturing at its plant in Kempten (Germany) for decades.
In general aerospace business news, Erickson and Helicopter Express has partnered to support and diversify S-64 Air Crane operations to meet a growing demand for the aircraft’s sustainment, modernisation, and production. Chamblee, Georgia-based Helicopter Express was the first commercial operator to acquire an Erickson S-64F (N159AC) with plans to acquire more.
“The Helicopter Express team is thrilled to own and operate additional cranes, support existing customers, and bring the crane’s unique construction and firefighting expertise to new customers in North America and abroad,” says Scott Runyan, president, Helicopter Express.
Founded in 1995, Helicopter Express operates a fleet of 24 helicopters and specialises in heavy lift, utility construction, and aerial firefighting operations. Its business model is built on the acquisition of new-production aircraft. Through the first half of 2023, Erickson owned and operated 15 Air Cranes.
“The alliance with Helicopter Express is a strategic step for us,” says Barry Kohler, chief exec, Erickson. “Erickson is channelling resources to integrate the global supply chain and improve support for all operators.”
GE AEROSPACE
Elsewhere, in North America, GE Aerospace, which provides jet engines, components and systems for commercial and military aircraft, officially debuts its public company in Evendale, Cincinnati, US, this year.
Previously based in Boston, General Electric announced plans to restructure the company in 2021, to split it into three separate business entities following spin-offs of its healthcare and energy businesses.
GE officials confirmed that “once the transformations are complete, there won’t be a separate ‘GE Corporate’ anymore”, just GE Aerospace.
“GE Aerospace continues to have a strong commitment to Cincinnati and the surrounding community, and our headquarters will remain here following our transition to a stand-alone public company in early 2024,” the company said in a statement.
Following the announcement, Larry Culp will become CEO of GE Aerospace, employing approximately 7,500 workers in Greater Cincinnati and Northern Kentucky.
Following the news, GKN Aerospace in the UK has strengthened its partnership with the company, to provide new technology, original equipment production and expanded aftermarket engagement. This will include the introduction of sustainable material solutions, and life-of-programme ]contracts for the GEnx, CF6, GE90 and GE9X fan cases.
“GE Aerospace and GKN Aerospace have had a strong relationship for more than 40 years and we are extremely proud of our partnership. Over the years we have grown our responsibility across all major GE engines and today we are in longterm partnerships with design authority for multiple programmes. This major new agreement is the next step. It ensures that we will continue to jointly develop the right technologies and solutions for worldleading engines such as the GEnx and CF6 for today and the future,” says Joakim Andersson, president, GKN Aerospace’s Engines business.
Hoist spoke to Gary Crawford, marketing manager, RHC Lifting, which also works with GKN Aerospace both in Bristol and at their Filton and Avonmouth sites.
“We service and maintain over 210 lifting equipment appliances over both sites. We are subcontracted via GKN Aerospace’s facilities management company Dalkia Facilities (formally Imtech Inviron),” he says. “We are also activity involved in designing, manufacturing, installing and testing any new lifting equipment, which often requires bespoke lifting equipment.”
The UK recently signed a trade pact with Washington state facilitating aerospace deals with the US, to bolster economic ties, in the absence of broader free-trade discussions with President Joe Biden.
The Memorandum of Understanding, the sixth such pact with a US state, is focused on forging closer ties between the two countries’ aviation sectors.
The UK has sought closer commercial ties with individual states with a broader US free-trade deal and signed agreements with Indiana, North Carolina, South Carolina, Oklahoma and Utah, and hopes to sign deals with Florida, Texas and California.
BAE systems
BAE Systems (BAES), the British multinational defence, security and aerospace company, plans to construct a pre-paint outfitting facility, called Ramsden Dock Facility (RDF), at Dova Way, Barrow-in-Furness.
The development is part of BAES’ submarine development phase, the Boat Build programme.
“The RDF building is an essential asset for our Boat Build programme, mirroring the function of the Central Yard Facility (CYF) within our main site, with the added benefit of a Goliath crane in an annexe structure,” the company said in its planning permission application.
The RDF building will rest on piled foundations, encased in a steel-framed, clad envelope, and feature a floor slab to support the structure. It will incorporate an efficient drainage system, hard standing pavement, and soft landscaping.
Infrastructure improvements may be required to accommodate the transport of heavy loads, potentially affecting the area from the roundabout at Michaelson Road and Bridge Road, south towards Ramsden Dock Road. Specific details are yet to be finalised and will be approved in a separate application.
The RDF’s layout and design are currently under development. However, the main production hall’s footprint is expected to be approximately 66m wide by 175m long, with a height of approximately 45m.
The support building, housing workshops, stores, offices, plant rooms, welfare facilities, and a canteen, will adjoin the main RDF building either on the northern or southern side. An additional annexe-type structure on the western gable end will house a 450-ton Goliath crane.
The main production hall will consist of a central aisle with eight pre-outfit bays on each side (16 in total). Operational processes will include pre-paint outfit, volume outfit installation, unit combinations, local system testing activities, and tank testing activities.
“Emissions from welding, cutting, and grinding processes will be managed by extraction systems. The RDF is designed to control noise and vibration within acceptable levels, in accordance with the planning authority’s requirements,” says a spokesman from BAES.
Upon completion, the RDF will accommodate approximately 400 workers during the day, 250 workers during the night, and 165 office workers. Construction is scheduled to start in the second quarter of 2024, with completion at the end of 2025. After handover and close-out procedures are finished in the first quarter of 2026, the RDF will be fully operational in 2027.
Condra Rescue Simulation Centre
Last year, Condra was appointed as the mechanical subcontractor to MH Automation for the University of Johannesburg’s Rescue Simulation Centre, under construction on Doornfontein Campus.
The company installed a specialised crane to replicate helicopter motion by lifting, rotating and tilting an actual fuselage. The 5.0-ton double girder electric overhead travelling crane will also position helicopter underwater escape training (HUET) simulator equipment. The centre is to train helicopter crews and emergency personnel in aviation rescue under a range of simulated weather and flying conditions
Condra worked closely alongside MH Automation, which designed and supplied the crane’s electronics and control systems for motion simulation.
A four-storey-high building with 6.0m-deep wave pool was constructed at the centre. After equipping with an AS365 Dauphin helicopter fuselage supplied by Airbus Helicopters, the crane will simulate the operational conditions of a machine hovering over either water or land by manipulating the lifting points of the suspended airframe.
UJ’s Rescue Simulation Centre would be Africa’s biggest search-and-rescue training facility, delivering a broad spectrum of staged situational environments, including rescue from a submerged vehicle and/ or airframe. MH Automation’s electronic systems and Condra’s overhead crane will be key to these simulations, complemented by replicated lightning, wind, and rain. A high-speed fan fitted above the overhead crane delivers pseudo rotor downwash to make training conditions as close to real as possible. There is a wave simulator to produce the disrupted water surfaces of flood conditions.
The AS365 Dauphin airframe and HUET simulator is to be stored in tandem on a raised platform above the pool area, the crane positioning them as required.
Condra supplied several key components to the Rescue Simulation Centre: the crane itself with hoists to simulate helicopter motion in the hover, the crane gantry, the mechanism for helicopter rotation, and fans and lighting for downdraught and different daylight conditions.
It also designed frames to fit onto the helicopters for hoisting. Crews and rescue personnel will board the helicopter, which the crane will then lift into position as required, manipulating it to simulate the motion and rotational movement of helicopter flight by means of the rotating mechanism and the hoists that will lift and lower the frame’s ends.
Control of airframe movement from the centre's floor is by radio remote joystick via IGBT (Insulated Gate Bipolar Transistor). variable-speed drive controls fitted to the hoist motors are provided by MH Automation.