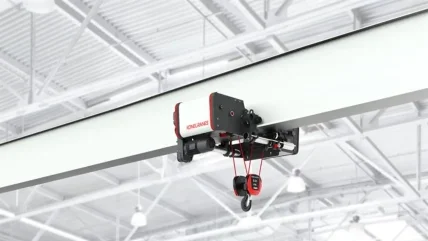
Firstly, to define portable cranes: they are carried, or sometimes pushed, and generally by hand, though sometimes a forklift or an overhead hoist can be used. When they are carried by hand it is generally by one person. A common practice is to have sockets set in various places around a factory floor, with a single crane that is moved between them as and when it is required.
This of course means they have to be lightweight. That in turn means that their structures tend to be simple: many are davit designs—a vertical mast or kingpost with an arm—with some gantries used as well. And being lightweight they are used for lighter tasks, and are generally operated by hand. There are exceptions to all the above statements, and we shall come to them, but we can start off with cranes that fit the criteria fairly exactly.
Typically, they are used in smaller workshops and factories that have an occasional need to lift something slightly too heavy or awkward for one man to lift easily. When the cranes are not needed they can be carried out of the way to a storeroom, to be brought out the next time they are required. Again, there are exceptions. “That is accurate, but it is not the whole story,” says Dusty White, technical sales manager of Idaho-based Syclone Attco, makers of the Skyhook range of portable cranes. “We are useful to those many small factories and concerns, but not only to them. We regularly supply to the semi-conductor industry, to aerospace, to automotive and to others.
“Every industry has components that it has to move around, and they are of that weight and awkwardness that makes a guy say to a colleague ‘Hey, can you give me a hand moving this?’. That is where people get injured; and reducing that is our business.”
It is, he says, even more important just now, given the crisis in public health. “Two people lifting something by hand together—that is where they get too close for social distancing recommendations.” Reducing a two-man lifting task to a one-man job can be essential to carrying out safely the job in hand, and to keeping production going.
“We have actually had a massive response from customers trying to adhere to social distancing requirements. Twoman lifts are a thing of the past now,” he says. “A portable crane gives the solution that people need for getting the job done while still staying safe. And I am proud to say that some of the jobs we are helping to get done are in the factories making the sanitisers, the ventilator machines and the protective clothing that are helping to fight the virus.”
Reid Lifting, based in Monmouthshire in Wales, make gantries and davits. The company has a T Davit and a Porta Davit range, as well as gantries, and has recently launched a dedicated US operation to expand its business. Their products use aluminium to keep weights low.
“Lightness is a key design consideration,” says MD Simon Luke, “as is ease of transporting it, but so is speed of erecting it. Five minutes assembly time is easily achievable on all but our larger gantries. All our smaller cranes, up to 2t capacity with shorter beams, can certainly be set up and moved by one person, without tools.
Because of the unique way our product is assembled, the person setting up the crane never has to bear the full weight of any of the component parts. We have online assembly videos to show how this can be done; it is true even of our ingenious Porta Gantry Rapide, which is a unique award winning patented design. It is a one-piece folding gantry, with one tonne capacity, that can be easily moved around a work site and used for many different tasks not limited to lifting goods. It can lift personnel as well and act as an anchor point for fall protection. It has a beam length of up to 4m.
“Our standard Porta Gantry is larger, a three-piece unit, with a range of height options and beam lengths and capacities of up to 5t.”
It may come as a surprise that light portable cranes can be used for personnel lifting, but in fact their capacities can be well within required safety limits. “Of course all personnel lifting operations should be carefully planned and include a risk assessment, a method statement and a rescue plan. And we would always recommend more than one person, and all involved should be trained and competent.
“Applications vary enormously, due to the great flexibility of our products,” he says. “A gantry could be used for lifting, relocating and moving a piece of machinery in a factory or on a site, or it could equally be used by a museum to lift a valuable statue. Generally speaking, gantries are able to lift much larger, heavier loads, so that could influence a customer’s decision. Davits are often specified where a piece of equipment may need to be regularly and consistently lifted or maintained from the same location, or where access is required over a leading edge or balustrade.”
An example of that is in water and sewerage plants. “The water purification industries use davits a lot,” says Alan Siertsema of Dutch manufacturer Gebuwin. “They have pumps at the bottom of water tanks, which need to be lifted out of the water from time to time for servicing. You need an arm to reach out over the water above them, and some sort of lifting device on the arm. You might have several pumps, eight or nine perhaps; so you embed a socket at the edge of the tank at each position, but you buy just one davit crane and move it from socket to socket as required. That makes it a very economical solution. We have three different socket designs, one above ground, one that is flush with the ground with a plastic cover to leave an unobstructed floorspace when the davit is not in position, and one for wall mounting.”
We have said that such davits should be lightweight. They also need to be simple and quick to erect. “Our main design target is to have a 500kg capacity crane without losing the flexibility of a lighter-capacity machine,” says Siertsema. “The total weight of our 500kg-capacity SD500 model is 25kg—and that is for the whole unit, not just the largest component. That is well within the range of normal lifting by one person. And our cranes are carried as one piece: you don’t have to go back and forth between the storeroom and the site several times to get all the parts there and then spend time assembling it, then after a five minute lift job disassemble it and make all those journeys over again to get it back to the storeroom. It is a one-piece crane: carry it to the site, set the end in the socket, flip it open, and it is ready.”
A low weight can come from light materials; or it can come from good design. “We could, for example, use aluminium for our davits,” he says, “but that costs—it is expensive. Instead, our shapes—the profiles and cross-sections of our jibs—are what give strength with light weight. We have ball bearings at the bottom of the mast to make the swivelling action frictionless. That makes it very easy to turn. Those are also expensive, but worth it: a finger can move the 500kg load.
“Gebuwin have 50kg, 125kg and 500kg models,” he says. “Each has a different arm length, because of strength considerations: the 50kg model has the longest arm length.”
An ingenious feature is that the crank handle of the hand-driven winch can pull out to change its radius: a large radius is easier to turn but is slower, since the operators hand has to travel further for each revolution; a stronger operative lifting a lifter load can set the handle to a smaller radius. Some portable davits have reaches that are adjustable under load. Most do not, and rely on swivelling the mast to move the load horizontally. “The reach is not adjustable; we are working on a new design that will have an adjustable reach with a 2m arm length—the arm length of our 125kg model is 1m,” says Siertsema. “The new design will lift 400kg, so that is a big upgrade. We are scheduling the prototype for this year, with production this year or early next.”
Boom Time
Several companies offer luffing booms as a way of moving the load horizontally. Reid’s T Davit has a horizontal boom that can slide across the top of the mast, under load, giving an infinitely-variable radius of lift. Another solution is an articulated arm. This acts as an elbow joint that can move in the horizontal plane only. Opening or closing it brings the load nearer to or further from the mast. Oz Lifting, who are based not in Australia as their name might suggest but in Minnesota, are innovative here. Their newest series, the Tele-Pro steel davit, comes in 500lb, 1,000lb and 2,500lb capacities. The unique feature is that the boom is telescopic and extendable under load. A winch handle winds it in and out, or a hand-held power drill can connect into the socket to do the job mechanically, to extend the radius from 36in to 66in with the boom horizontal. When the boom is set at 45°, the minimum lift radius comes down to 23in. The drill can also be placed in the winch winding socket, for faster winding and lowering on long lifts. More innovative still is Oz Lifting’s Compozite range, in which the booms and pillars are made of lightweight composite material.
Carbon fibre, they say, strength for strength is about 40% lighter than steel. Their 1,200lb capacity Compozite davit crane weighs only 83lb. “They are the lightest and most portable on the market,” says sales manager Richard Miller, “and they continue the legacy of one-person assembly and truly portable design without any tools needed for setting up.” The boom can be set by hand to four different lengths; a ratchet screw-jack adjusts its angle, giving the ability to luff under load. It shares with the Tele-Pro the capability of being drivable by power drill.
Their Compozite Elite davit is lighter still, at just 37lb but lacks the telescopic feature of the boom. It has a 42-inch fixedlength reach when the boom is horizontal, compared to the 66-inch infinitely-variable reach of the telescopic version. AC and DC power winches are available for their davits as options.
Portable cranes are carried by people and are typically powered by people, as we have said. “Our products are manpowered,” says White of Syclone Attco.
“Our customers enjoy that aspect of it. With electric power there is the possibility of holding your finger on the button just too long, the load travelling just that bit too far, and you can damage things. That’s not acceptable. We want you to be able to go as slowly and as precisely as you want. That makes us a precision tool. When you come down to it, the human hand and the human eye still make a very good tool when you put them together.”
Solid Foundations
A davit needs a stable mounting fixture. These, unlike the davit itself, can be permanently fixed in place. Some are sockets that are bolted to the floor or to the workbench; others are set flush into the floor, so that when the crane is not in use they do not impede the aisle or work area. Others again are wheeled. Most manufacturers offer various choices: thus Skyhook has a four-legged mount that is designed to fit around the corner of a workbench, and ‘cherry-picker’ mounts, with the wheels on a horizontal U-shaped bracket that can straddle a manhole.
Unusual is their ‘cart mounting’: a pressed steel trolley on castors that can be pushed around the factory floor, with the davit mounted at a front corner. The component it has been used to lift can be unloaded onto the cart and pushed to its destination. Any davit in their range can be fitted on any mount. “Most popular is our articulating arm on the mobile cart,” says White. “That is ideal for, say, replacing a chuck on a lathe: the articulating arm gives manoeuvrability while the trolley parks out of the way and lets the operator get close to the task.”
Thern, based in Minnesota, have Ensign, First Mate and Commander ranges of portable davits. Despite the names they are designed for land-based rather than nautical operation, though they can be mounted on boats and landing docks as well. They can also be mounted on small utility trucks. At the other end of the operating scale NASA have four of them at their test site for the rockets used in the Artemis space program which is due to send the next generation of astronauts to the moon by 2024. Thern davit cranes can be found as well on top of two massive cranes that are constructing the world’s longest suspension bridge, across the Dardanelles in Turkey. The davits are used to lift spare parts for the cranes.
All can be assembled and moved by one person. Booms extend to one of four positions, to give different reaches, and can also be luffed with a ratchet and screwjack mechanism. The davits can be fitted with manual winches, either spur-geared or worm-geared; the worm takes more turns to lift a load but each turn takes less effort. Alternatively power winches can be fitted for longer lifts or heavier loads.
Pedestal, flush or wall mounts are available, as are wheel-based mounts, in which the front wheels are on struts that project past the load, giving stability without the need of a counterweight.
“Our Ensign 500 and Ensign 1000 portable davit cranes are designed for economy, clearance, lift height and flexibility,” says marketing co-ordinator Gloria Gibson.
“The Commander series offers flexibility, with multiple boom lengths and angles to choose from. An optional base extension can give additional hook height without affecting the rating of the crane for the First Mate and Commander series.”
Most portable gantries once positioned over a load will lift it, but can then move it only along the beam; they are not designed to transport the load to another location. But Lancashire-based Granada Material Handling can specify and provide a motorised gantry crane made by French partner company, Comege. Electric motors on two of the wheels allow it to travel under load across a suitable factory floor.
The motions are controlled by a standard pendant or radio remote control and are synchronised to turn at the same speed for straight-line travel, but their relative speeds can be varied to allow the gantry to manoeuvre or to turn on its axis. Flexible proximity limits around each leg ensures the gantry stops harmlessly if it comes into contact with an obstacle.
Motors and hoist can be powered by battery or by cable. The cable reels in on an overhead system to avoid trailing across the factory floor. Alternatively, the whole system can also be battery operated to avoid the need for any wires. The system can lift and manoeuvre a load of up to 6,300Kg.
Granada also supply mobile slewing jib cranes from their partner Vetter. These are not mounted into sockets but instead are on a set of concrete rings—the number can be increased or reduced according to height and load-weight requirements— which provide stability and counterbalance.
This design in most applications also negates the need for foundation blocks or civils works. The rings themselves are mounted on a small-wheeled trolley. The whole assembly can be pushed around the factory floor by hand, towed or lifted by forklift, and also carried from place to place by overhead gantry crane. A hoist can be traversed along the jib arm, which can rotate through 270 or 360° depending on the configuration. There is also a version with an articulated jib-arm.
Portable cranes may not be the most expensive investment in industrial machinery, but the right choice will ease production and take strain off workers.
There is certainly enough choice in the marketplace for consumers to find the solution that fits them best.