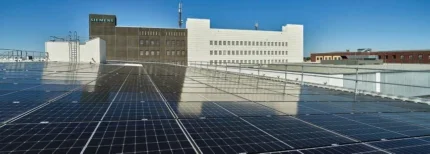
Germany’s autonomous crane market is set to experience significant growth, with a compound annual growth rate (CAGR) of 4.9% projected from 2025 to 2035, according to Future Market Insights.
By 2035, the market size is estimated to reach approximately USD 343.3 million, fuelled by the integration of advanced technologies like artificial intelligence (AI), machine learning, the Internet of Things (IoT), and 5G connectivity.
These innovations have greatly enhanced operational productivity, safety, and reliability, particularly in sectors such as construction, manufacturing, and logistics, where precision and efficiency are vital.
The demand for autonomous cranes is further driven by Germany’s ongoing investments in infrastructure, including the construction of roads, bridges, and renewable energy facilities. These projects require cranes capable of performing complex lifting tasks with high efficiency.
The German government plans to invest EUR 300 billion in infrastructure development by 2030, increasing the need for autonomous cranes. Additionally, Germany’s focus on renewable energy, including wind farms and solar parks, makes autonomous cranes indispensable for heavy lifting and the assembly of largescale structures in remote and challenging environments.
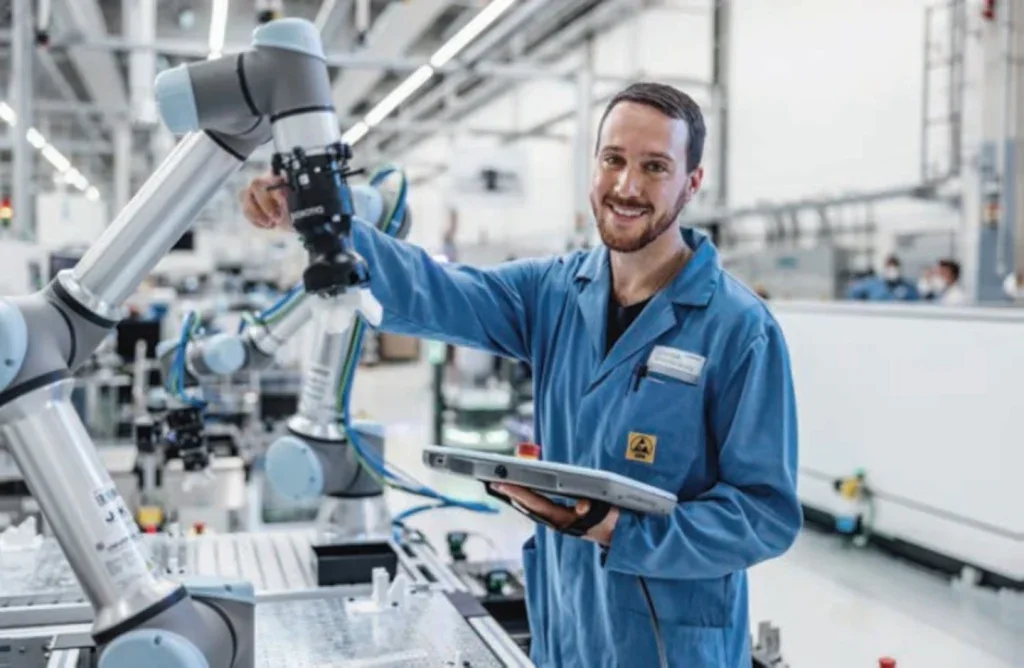
The technological advancements incorporated into autonomous cranes are reshaping safety and operational standards. AI-powered decision-making allows for real-time assessments of load stability and optimal lift paths.
IoT sensors monitor operational data, track maintenance schedules, and reduce unplanned downtime, while machine vision ensures precise material placement and obstacle detection on construction sites. Furthermore, 5G connectivity enhances the remote monitoring and operation of autonomous cranes, improving efficiency and safety.
Germany’s proactive approach to automation, supported by initiatives like Industry 4.0 and the Future Mobility Fund, has placed the country in a strong position to lead the global autonomous crane market. The nation’s strong industrial base in automotive manufacturing, aerospace, and logistics provides a solid foundation for the widespread adoption of autonomous cranes. Moreover, Germany’s commitment to renewable energy and sustainable construction practices further bolsters the market for autonomous cranes.
Autonomous cranes with a payload capacity of 50-200 tons, which hold a 45% market share, are the most common in infrastructure, logistics, and manufacturing industries. Heavy-duty cranes (over 200 tons) are essential for large-scale projects such as wind turbine installations.
As sustainability becomes a more prominent focus, Germany is seeing a rise in the use of electric and hybrid cranes, particularly in green construction projects.
Electric cranes, which produce fewer emissions and generate less noise, are ideal for urban construction, while hybrid cranes offer both fuel savings and high performance, making them suitable for a range of applications. A recent example of sustainable operations is Siemens’ manufacturing facility in Fürth, Germany, which has been honored by the World Economic Forum (WEF) as a ‘Sustainability Lighthouse’, a distinction given to 21 factories worldwide.
This recognition highlights the plant’s approach to sustainable manufacturing, combining technological innovation with significant reductions in energy use, emissions, and waste.
The WEF’s Sustainability Lighthouse network showcases organizations making major strides in energy efficiency, decarbonization, and circularity.
For Siemens, the award underscores the company’s commitment to proving that sustainability and productivity can go hand in hand. At the Fürth location, the team has achieved a 64% reduction in energy consumption per unit of output, while increasing production by 145%. Greenhouse gas emissions have also dropped by 72% per unit of output since 2019.
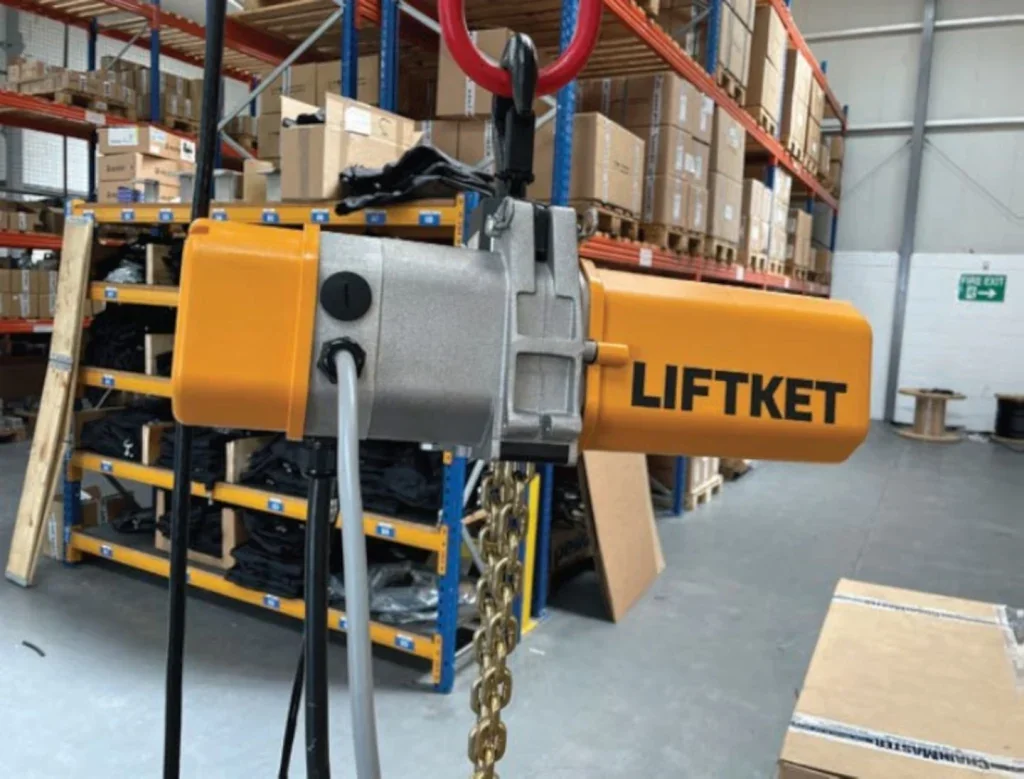
“This award recognizes the extraordinary efforts of our team in Fürth. By implementing our smart energy systems, we’ve demonstrated that you can significantly boost productivity while cutting emissions and energy use. Our work benefits not only our own operations but also offers sustainable solutions to our customers,” said Cedrik Neike, a member of Siemens’ Managing Board and CEO of Digital Industries.
The Fürth site, which has been part of Siemens since 1954, employs approximately 1,700 people and produces industrial-automation products, including Simatic HMI panels used in manufacturing plants worldwide. It is a vital part of Siemens’ strategy to lead in sustainable manufacturing. The site is aiming for netzero emissions by 2026—four years ahead of the company’s broader goal.
Key to the plant’s sustainability efforts is an energy system that integrates Siemens’ own technologies. This system, which includes tools like the Simatic Energy Manager Pro and Siemens Navigator, collects real-time energy data from over 350 power meters throughout the facility. This allows the team to identify areas for improvement, resulting in substantial energy savings. For example, the lighting system alone saves 952 megawatt-hours of energy annually—enough to power around 2,000 households.
But it’s not just about energy. Siemens has focused on reducing waste and improving the longevity of its products.
An on-site repair center helps extend the life of select products, with the goal of growing this service from 310 products today to 2,000 by 2026. These efforts help prevent emissions associated with manufacturing new products and reduce waste from product disposal.
The plant is also taking steps to become more energy independent. In late 2023, Siemens installed a large 3,300-squaremeter photovoltaic system on the roof of the parking garage, significantly boosting the facility’s solar power capacity. The site now produces its own nitrogen, used for manufacturing processes like welding, and is exploring ways to use waste heat from industrial processes to help heat the building.
Siemens’ broader sustainability initiatives are also making an impact. Since 2019, the company has reduced its overall CO2 emissions by 60% through investments in energy-efficient technologies and processes. With over 90% of Siemens’ products and services supporting customers in achieving their own sustainability goals, the company is positioned as a leader in the green transition.
For Siemens, the Fürth Sustainability Lighthouse recognition is a proud milestone—but it’s only the beginning. The company plans to continue pushing boundaries, demonstrating that sustainability and innovation can fuel each other to create a more sustainable future.
The autonomous crane market in Germany is also benefiting from strategic partnerships and technological innovation.
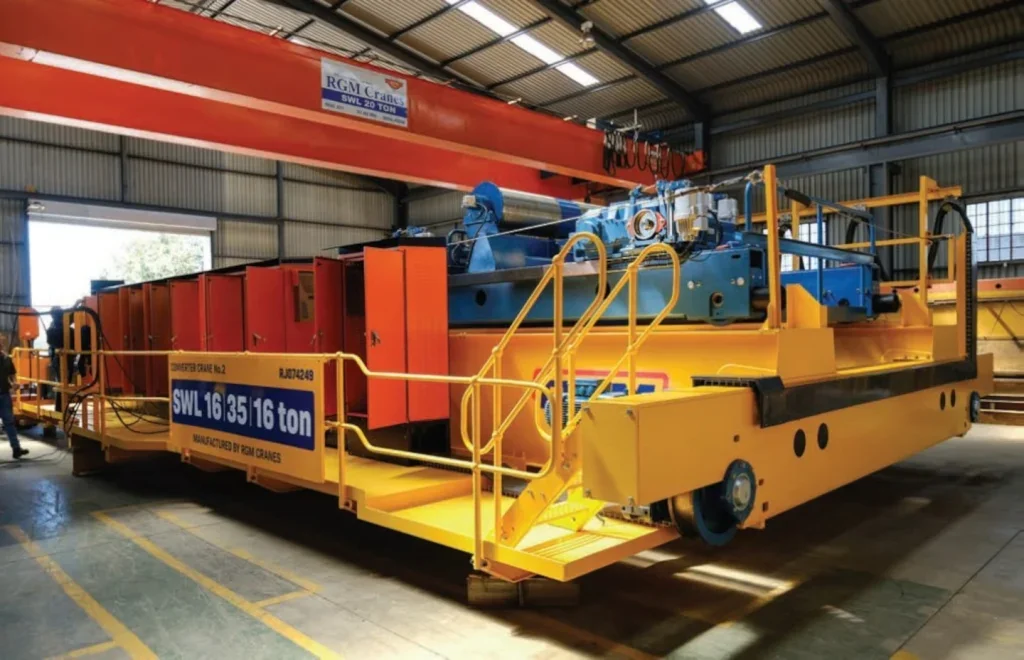
Only recently, Liftket UK announced it has partnered with MOVEKET, in Germany to expand its product portfolio in the Stage industry. The new offering complements its Chainmaster product line, allowing Liftket UK to address both key areas of the stage sector – rigging and automation – while providing tailored solutions to meet customer needs.
To support the expansion Liftket UK has welcomed Rick Williamson to the sales team, who has over 15 years of experience in electric chain hoists and automation, supporting some of the most demanding shows, festivals, and tours. He will now be responsible for managing the entire Stage portfolio in the UK.
“The addition of MOVEKET to our product range is an exciting step forward for Liftket UK. Together with Chainmaster, we are uniquely positioned to offer high-quality solutions for both rigging and automation. With Rick on board, we have the perfect combination of expertise and dedication to drive growth and deliver exceptional service to our customers,” said Barry Williams, director, Liftket UK.
Williamson added the introduction of MOVEKET alongside Chainmaster gives them a fantastic product lineup to meet the evolving needs of the Stage industry.
“I’m eager to support our customers and help push the boundaries of what’s possible in live entertainment,” he said.
Illustrating strategic partnerships – KoRo RIW, a machinery parts manufacturer in Wetter, Germany, has successfully completed an industrial crane rehabilitation project with RGM Cranes in Johannesburg, marking a significant milestone in their ongoing partnership.
The project involved a full turnkey operation, from the removal of the existing crane to the commissioning of a new, highperformance system.
The collaboration involved more than just replacing an existing crane – the goal was to integrate the latest crane technologies while enhancing the operational efficiency of the facility. Project manager Emel Fleischmann of RGM Cranes highlighted the ambitious nature of the project, noting the challenge of aligning the crane’s capabilities with the client’s detailed requirements while ensuring compatibility with existing stock components.
Rolf Gressner, MD, KoRo RIW also commented; “Achieving these goals required a seamless blend of innovation and engineering excellence. The objective was not only to meet the client’s operational needs but to push the limits of performance and safety by implementing the latest standards for high-duty cycles and advanced industrial technology.”
KoRo, founded in 1924 as Rheinische Isolierwerke (RIW), began with a focus on insulation materials before evolving into crane components by the 1930s. Known for its engineering precision and safety, KoRo pioneered the RIW Components Manual in 1984, setting industry standards. After merging with KoRo in 2012, the company expanded globally, opening new facilities and achieving technological milestones, including the design of a 600t lower block.
Elsewhere, major players like Liebherr, Konecranes, and Terex are leading the way in integrating AI and IoT systems to improve crane efficiency, while emerging startups are offering retrofit solutions which allow companies to upgrade existing cranes with autonomous technologies.