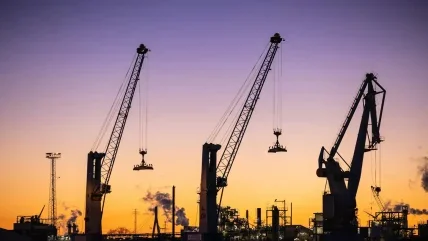
Richard Phillips is an associate mechanical engineer at Casper, Phillips & Associates (CPA). In addition to being engineering consultants who help specify crane purchases and perform design reviews to make sure the crane meets the technical requirements, the company also designs cranes themselves. The question to him was straightforward enough: what sustainability practices does your company employ?
Here’s what he said: “We have designed cranes that perform dynamic braking through a variable frequency drive with an active front end. When a hoist lowers the load the motor is actually being used as a generator and is producing electricity. An active front end sends the electricity generated during lowering into the power grid. It’s the same idea as a hybrid car, but instead of sending the generated power to a battery we send it to the electrical grid.
“Additionally, we always try to minimise the material used on the cranes.
“Many cranes send the generated electricity to a resistor bank to be dissipated as heat. In other words, the electricity generated by the hoist gets turned into heat when it passes through the resistor bank. With an active front end we are re-using this energy to power whatever is connected to the grid such as lights, cell phone chargers, or whatever is connected to an electrical outlet.”
Now while the Konecranes news is impressive in terms of the scale of its impact, isn’t it wonderful to know that the industry is working to tackle the issue of sustainability at a more micro level?