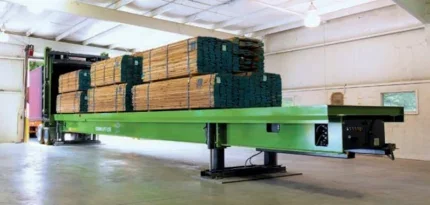
Combilift has been working with port operations and dock operations for a number of years. We have equipment assisting in the recovery of AGVs (Automated Guided Vehicles) with our Straddle Carriers (Combi-SC). We are handling containers with our straddle carriers and large offshore components for the wind turbine industry with our Mobile Gantry (Combi-MG)
We’ve been working with these industries for quite some time. On the port side with their AGVs, they have been automating and electrifying their operations for a long time and states such as California are going further into that electrification of forklifts, engine powered vehicles and Combilift has been designing in our R&D department to meet that demand.
Almost all of Combilift’s equipment is electrified up to 30,000 lbs on a forklift, 65% of our production is electric that comes out of the factory. And then we’ve got new models that we’ve developed such as the Combi-CB 155E (Counterbalance), which is a larger capacity CB, that’s multi directional, and can be used in port side operation and dockside, which has been developed only as an electric machine, launched in 2023.
California’s been driving a lot of the regulation with carbon neutral, and they’ve always had the strictest emissions and driving stricter emissions. And now they’ve moved to their electrification of over the road trucks.
There are new regulations coming in, on January 1, 2026, to more or less remove the sale of LP gas engines or large spark ignition engines. So that will push either towards diesel or electric units for those applications. So, there’s regulations to limit the older technologies and drive new technologies in California. They’re definitely at the forefront of pushing this towards electrification for sure.
Ports in the US have always been looking at this and trying to lower their emissions, and obviously they are a big contributor to local emissions because of the engines running at ports with the ships and the vessels. They also want ship to shore power to remove those engines running and electrification of cranes and everything around it. So, ports are probably second in the US after California, but California is definitely driving it across the board and other industries.
I’ve been in the industry now for about 25 years, and I’ve seen a lot of changes in terms of advancements in technology. A lot of the industries have become more sophisticated and they’re wanting to see their utilisation, they want to have their uptime, and much better reliability on their equipment and having more advanced systems on their equipment. Telematics has become a big part of the business to see the utilisation and the remote diagnostics of equipment, which has also been built onto our systems with Combi Connect, so we can track equipment with GPS. We can log in remotely, we update software, we can change settings and diagnose any fault remotely from anywhere where our equipment is connected.
This has become a big part of large fleet analysis or even large fleets that are single units in lots of locations. It’s become very useful for the customer and for the service provider to maximise lower costs in terms of service and make sure they’re getting the utilisation out of the equipment they need so that there’s not excess fleets or equipment that’s not been utilised. That’s been a big change and obviously that’s maximising their spend by adding a small cost to each piece of equipment and reducing the overall fleet, that’s been a big part of the business here.
Coming from Europe to the US, (Short moved to the US 11 years ago from Ireland) I’ve seen a lot of the European technologies moving across to the US and definitely that’s been a big advancement over the last 11 years from my time in the US.
In terms of advancements in technology there’s a lot of optimizations needed before there’s automation, but automation’s the end goal. We see a lot of customers here where optimising and standardising what they’re doing is the next big step before automation. A lot of industries are not just fully suitable for automation at this point because of the technology base isn’t there. The infrastructure in terms of technology isn’t in place in some industries, and that advancement has to come before you can fully automate, for example, a dockside lumber yard or a stevedore.
But we do see optimization as key and that’s something we offer as a service – warehouse optimizations, material flow, warehouse layouts as a free service to help customers maximise what they have at the minute, get it flowing and then from there you can take the next step and in 10- or 15-years’ time to automate it, if the loads are suitable.
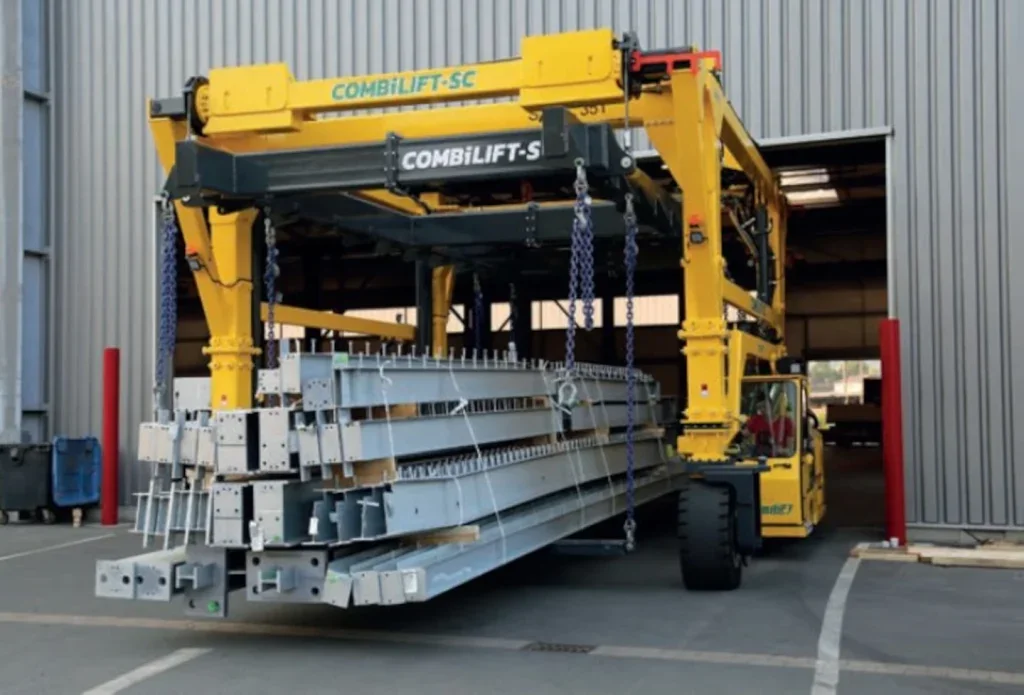
Optimization is one of the big things we’ve been doing, coming from Europe where space is at a premium and not very available, we’re very used to maximising that. To make every square inch count. In the US traditionally there’s been lots of space to use, but that’s becoming less and less as we see across cities now where warehouse space is in high demand. More and more warehouses are being constructed and being close to ports is critical, but you have to maximise that space, and you have to optimise it for the best use.
A lot of regulations are happening in California at the moment, to change a lot of the engine powered equipment to electric, but there are some Federal regulations that are overriding on the diesel side, which California it appears can’t change too much. But the diesel fleet will be the next thing.
There are obviously always improvements to be made on emissions, but the biggest one here is at the end of 2025 to 2026 to phase out operation of Large Spark-Ignited (LSI) forklifts in California, which we expect other ports will follow in time.
The big challenge in California is the availability of all the charging power, so the infrastructure to charge large fleets of vehicles that are electric, that is going to be a challenge considering in the summertime when it’s very warm we have brownouts (a drop in the magnitude of voltage in an electrical power system). There’s not a lot of excess power to do this, so the power availability is going to be a question. And I think it’s going to take some time to get all that infrastructure in place.
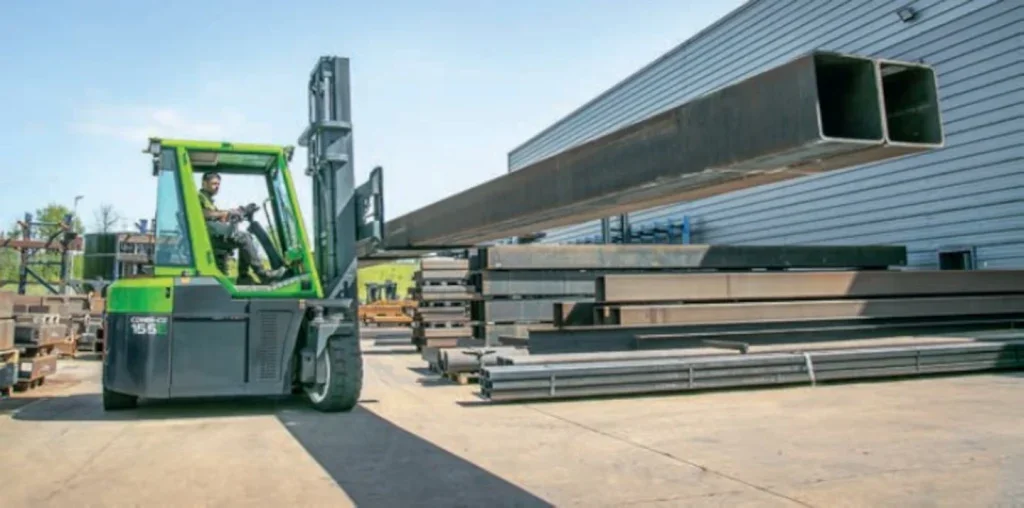
There’s a lot of battery storage systems going in to store solar power and wind and everything but where that peaks at in relation to when they want to have all their over the road trucks electric and so on, will be the key if that infrastructure is in place.
The regulation is expected to come in, in 2035, when they want to have no more sales of gas cars in California. So, the over the road trucks are happening at the minute. If you’re over a fleet of 50, or a company of over 50 people, or over $50 million dollars in revenue, you have to start to have a portion of your truck fleet as electric, so they’re phasing that in as it stands.
But we do see challenges with that where large trucks need immense power to charge five or six battery vehicles overnight. There isn’t the power availability at warehouses or charging stations to charge these large vehicles at the minute, so it’s proven a bit of a challenge, but there are incentives out there for these with the California Government, they’ve got a core programme to encourage it and they are given incentives. We would expect to follow this shortly.
The news that former President Biden was announcing a series of actions to strengthen the cybersecurity of America’s ports and to stop buying Chinese ship-toshore cranes and to start buying American ones made good headlines.
It mostly centred on the two biggest ports Los Angeles and Long Beach, which were importing everything from Asia. There was a lot of material coming from there to the US for manufacturers. I think there’s a lot of components coming from that direction. I understand it on the solar/ battery side because there wasn’t an industry in the US that produces that. Even battery manufacturing for automobiles or storage systems, was all coming from Asia.
There are virtually no solar panels made in the US. I understand trying to boost the industry here, but you can’t increase solar without getting the components and at the minute the bulk of that is manufactured outside the US. So Biden’s statement was slightly contradictory.
Combilift manufactures everything in Ireland and ships it to the US, we don’t expect that to change any time soon.
We have a lot of production capacity at the factory in Ireland and when the factory in Ireland reaches capacity, we’ll look at a second or additional production. But at the minute we’ve got no production in the US, we’ve got spare parts distribution in Greensboro, NC and we’ve got about 55 technicians here in the US, mostly based in , and a remote sales team around the US and Canada. The US is our biggest market. 30% of our machines come to the US.
Other things people are talking about at the moment is the US elections. People are waiting to see what happens. It creates anxiety in some businesses, whereas other companies just proceed with their CapEx and their spend and continue to keep investing for the future. Others take an approach of wait and see based on who gets in, after the election in November when it’ll all be over, and everyone will get back to normal.
FUTURE INVESTMENTS
Combilift invests 6-7% of its turnover in R&D, investments in new products and continues to work on autonomous products, electrifying new products. This year we launched the Combi-CLL Log Loader, and a new model of the Combi- CSS Container Slip-sheet.
The Combi-CLL is a new model of the CSS, designed specifically to load logs designed for fast loading of freight containers with a maximum capacity of 30,000 kg this year. Those are in use on the East Coast with hardwood mills.
R&D is our biggest investment, that’s what keeps our business alive, listening to customers and understanding their challenges. If they come to us with a problem, we try to find a solution and invest our time and engineering in coming up with that solution. There are always some expansions at the factory and new equipment but nothing significant to announce just yet,” said Short.

The main challenges we find are customers always want to increase their safety. They want to handle their loads in a safer way. Travelling with loads elevated is always a safety risk. So when you’re handling long awkward loads, which pass over vehicles or other products the easiest way to do it is to lift it. So, we’re always trying to find ways to handle that load as safely as possible as close to the ground with the best visibility for the operator.
Our goal is to make the environment safer for everyone else operating equipment and for low travelling. The walkie products inside manufacturing plants has increased safety a lot. So there’s no forklifts but they still have to move the products and they’re doing it with walkie or pedestrian products very safely with WRCS (Walkie Radio Communication Services) and Combi-PPT, Powered Pallet Truck for small to medium-sized warehouses and production facilities, with a lifting capacity up to 16,000kg and Combi-CS tiller arm which allows operators to operate very safely without being in a crush zone or increasing their visibility of the load when they’re travelling. Comment: All the models in the Pedestrian range are equipped with the Combilift tiller arm, so both the Combi- PPT and the Combi-CS have it.
It could be a retail operation or a manufacturing plant where they want to have less forklifts where there’s lots of pedestrians and we go in and design a product around that. It could be the Combi- CB 155E or we’ve had customers that asked for a 15,000 lbs multi directional forklift that still operates like a regular lift, but it’ll travel sidewards and handle long loads, whether it be steel, lumber, whatever it is you know a lot of them in Europe have been used on dockside and portside applications for stevedores and so on.
It gives them that extra flexibility and added safety, when on portside, rather than elevating the long load travelling between unloading the ship or the vessel to unloading trailers. So it’s usually around safety is what we’re trying to increase.
We’ll hopefully have a couple of product launches next year which we’re pretty excited about. We’re just in the final stages of testing. This year we’re really expanding our reach into certain industries. In Europe and around the world we’ve had a lot of success with the offshore wind industry, and we see that about to kick off in a real way here in the US where we’re starting to see real growth. And, based on our success in other parts of the world, that’s an industry where we feel we have a lot of good offerings with our products and existing customer base. So that’s a big area for us on the offshore wind when things get going there again.
Otherwise, we’re just growing our products, our biggest challenge is customer awareness. A lot of customers don’t know they have a problem, and they don’t know that Combilift is the solution for that problem of handling their loads. So we’re just getting out in front of customers and making sure they’re aware of what we do and what we can do for them, whether it’s optimising their warehouse or their material flow or storage yard or handling loads safer.’