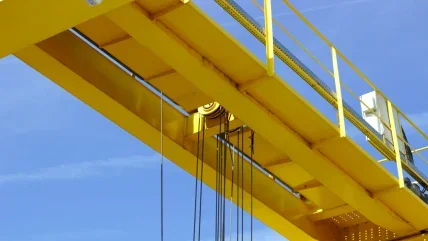
As Cargotec announces it is refocusing its strategy for higher financial performance through sustainability and its core businesses, especially in digitalisation, following news about the cancelled merger between Cargotec and Konecranes, Hoist takes a look at the latest technologies to come to the fore.
“Customers have been progressively more interested in “smart” technology that allows them to predict and prevent problems like equipment breakdowns or necessary part replacements before they occur and integrate communication technology into their systems,” says Dan Beilfuss, director of sales, Americas, CMCO.
Columbus McKinnon’s Intelli-Connect Diagnostics and Analytics provides operators with trends, alarms, and alerts to their personal electronic device to monitor the health of a crane or hoist. Using the Intelli-Connect Mobile and Mobile+ apps, users can access detailed Magnetek variable frequency drive (VFD) information right from the plant floor.
“With the advent of mobile applications in the industry, available on phones, tablets, or laptops, wireless data collection is now possible. This eliminates the need to halt equipment operation to have a technician climb up to a crane or hoist and manually connect to a drive to get system data. Information is available at their fingertips – reducing equipment downtime and potentially hazardous situations in facilities.”
Christian Heid, managing director, SWF Krantechnik, explains that the awareness of the relevance of machine data has changed in recent years and is growing continuously. But what needs to be developed further is the distinction between machine and personal-related data, so that machine-related data can be used profitably and personal data can stay safe and secure.
There is enormous potential, however, the industry still needs to take further development steps in this area.
“SWF Krantechnik is working on the gradual modernization of all of its electrical components, laying the foundation for the development towards IoT and digitalization and preparing for the new digital and interconnected working environment,” he said. “We are currently developing a scalable hardware platform for monitoring single hoists and cranes up to sophisticated installations that consist of several cranes. This platform is supplemented by further electrical components which will be launched step by step.”
SWF currently provides OMNI control, hardware for hoist monitoring and VARIO control series frequency inverters via a CANbus network. VARIO control is configured via a Bluetooth dongle connecting to a smartphone app. Going forward, the advantages of the CANbus network will make additional hardware or tools unnecessary.
“All components are based on a bus technology. This technology links the electrical components and they communicate with each other via this system. In this context OMNI control will be the heart of the digitalisation of the crane system in future. SWF is launching the entire package on the market in several consecutive steps,” said Heid.
“OMNI control and VARIO control have already been launched. The new gateway modem, the new family of radio remote controls as well as the app for programming OMNI control are currently under development and will follow next.
“In future, the equipment from SWF Krantechnik will provide an interface for the exchange of master data. In the current implementation phase pure crane data are processed. The currently available interface is a bus interface, which allows automated process cranes to be combined and controlled.
“IoT and digitalization play an increasing role in our industry. We already offer solutions called Crane Intelligence. Crane Intelligence provides optional features for smart electronic monitoring and control to make operating a crane safer and more user friendly. Maximum performance always, higher productivity and time savings gives a customer a fast return on investments. We offer multiple solutions that meet various requirements such as: Sway Control prevents loads from swinging during movement; Inching enables precise load positioning in predefined increments between 2mm and 100mm for hoist, trolley, and crane movements; Shock Load Prevention gently lifts loads at a reduced hoisting speed and Cranes in Tandem enables simultaneous long and cross travel including lifting and lowering.
“However, it is not about implementing these intelligent crane functions in a single machine. Users and partners want to enable communication among these machines and their functionalities in the future. This information, of course, will not just be available for the machine. Every user or service representative can view it – and even control it – online.”
In future, Heid says the trend must be towards raising awareness when dealing with and using data profitably. In the collection and profitable use of machine data, ‘fearlessness is required’.
“In addition to today’s data collection and usage we are also studying in direct and indirect connection on how to decrease our carbon footprint. We as a provider need to maximize the efficiency of the usage of energy, enhance our crane applications and to support with this package the same targets our partners and end-customers have,” he said.
GH Cranes has its own real-time digital plans. It started to record operational data locally in 2008, storing all data in the crane’s own dataloggers and over the last five years has progressed in the connectivity and transmission of this data automatically to the cloud, allowing the company to monitor the crane’s performance in real-time, issue automatic alarms, carry out data analysis to obtain behaviour patterns, and offer advanced digital services for crane maintenance.
“All this has been possible thanks to GH Real Time,” explains Eneko Ariznabarreta, head of R&D, GH Cranes & Components.
Customers using the technology want to know the state of the DWP (Design Working Period), the remaining lifetime of the crane and the way in which it is being consumed.
They are also interested in knowing about the live performance of the crane, obtaining failure alarms and possible problems that could arise, to improve safety, as improper use is identified, such as overloads, or excessive inching, etc.
And now, customers want to obtain productivity data on the cranes, on the plants themselves based on the operation of the cranes. All these services are offered by means of the GH Real Time digital plans.
Ariznabarreta points out that in regards to communication and integration of the cranes with other machines and operations, GH Cranes is a member of the working group defining the OPC UA communication specification for the Overhead Cranes sector. In future this will make it possible to establish standardised horizontal communication between machines.
“The most technological customers that have productivity scorecards increasingly ask us for more integration of data originating from the monitoring of cranes in their own information systems. This is a significant technological challenge, bearing in mind the requirements of each customer are specific. This technology is demanded by sectors such as steelworks, paper mills, etc. that want to know their production processes in more detail, identify waste and increase their overall efficiency,” he said.
“One of the main trends where GH is a leader, is in predictive maintenance based on the statistical analysis of operational and service data, which are obtained by means of our Corebox equipment. Beyond collecting data, what is important is their analysis and processing to generate digital services that provide added value for the customer. GH has worked intensively in this field, even with emerging Artificial Intelligence techniques, and as a result we have the GH Real Time digital maintenance plans. Our system is so versatile that it can be installed in existing cranes, both by GH and by other manufacturers, quickly offering advantages to the end customer.”
Earlier this year Tiger Lifting joined the growing network of RiConnect, uploading its product information and certification to the RiConnect platform, scanning product chips using near-field communication (NFC) technology, so that product information relating to usability and traceability of a product is readily available.
It allows users to access information using the RiConnect smart phone app and a smart phone (with NFC capability).
“At Tiger Lifting, we think that making use of digitalisation technologies like RFID/ NFC to digitalise inspection management systems and efficiently manage inventory will become essential in the future,” says Alice Inglis, UK director, Tiger Lifting.
“When RFID is incorporated with lifting products this allows access to digitised safe-use instructions, certification and pre-use checklists. Having this information available digitally significantly reduces paper waste helping companies manage their environmental impact, and it keeps essential information accessible and reduces time for equipment to be put into service enabling more efficient operations. “Tiger products are available with the highly corrosion and impact resistant Yoke RFID SupraTag. Moving forward we will see more of our products with RFID chips embedded during the manufacturing process.”
Inglis said it is also working closely with other key manufacturers and is thrilled to be able to offer Yoke digital products like chain fittings and lifting points alongside the Tiger digital range in the UK, offering an enhanced digital product offering to global rigging distributors and end users.
“It has been straightforward to upload our manufacturer information into the system and many of our lifting equipment distributor customers are welcoming the technology,” Inglis added. “We’re excited to see how the RiConnect platform develops.”
To explain more about how the technology works, Marelize du Toit, senior business development manager Europe, RiConnect, says it is a cloud-based SaaS (Software as a Service) with no download required, which specialises in asset management and Pre-use Check.
It focuses on the integration of RFID technology, cloud-based software and the use of mobile devices.
“RiConnect enables manufacturers, distributors, asset owners, field operations employees, inspection operators, and end-users to save and transfer information on one platform for the entire life cycle of manufacturing, use, maintenance and retirement of products and assets, to achieve product line digitalisation and maintain a safer working environment. We believe safety is essential and a digital platform like ours will help improve this and even change the entire industry,” she said.
“A key feature of the software is access to an equipment manufacturer’s Pre-use Check information. Lifting operations needs to be planned, supervised and carried out safely and a lifting plan should ensure that equipment remains safe for the range of lifting operations it might be used for. Users of any lifting equipment should have training and instructions so that they can ensure the lifting equipment is safe to use. Pre-use checks are essential so the operator can identify any faults or damage to equipment which may affect its safe use and helps field staff stay away from danger effectively.
“The ability to access the check list and record the results of the Pre-use Check by using the RiConnect App and scanning the RFID attached or embedded in a piece of lifting equipment helps ensure this vital check is carried out and the findings are recorded.
“The system has recently been enhanced to include an OEM (Original Equipment Manufacturer) function and a maintenance function for equipment owners to have a more complete regular maintenance system. Also, we’ll develop the inspection module in the near future,” adds du Toit.
“We have been able to showcase the platform at recent industry events where it has been positively received and we’re pleased to have welcomed more manufacturers and asset owners into the ever-growing network.”
Digitalisation can help lifting equipment inspectors and service engineers increase productivity, cut costs, and enhance compliance and with the labour market continuing to tighten, companies must do more with less when it comes to service engineers. Digitisation can be ‘a quick win’ in this regard, as going paperless is proven to boost productivity.
Digital job management platforms such as BigChange are increasingly used by companies to manage their mobile engineers’ activities and increase customer satisfaction at the same time.
BigChange brings together customer relationship management (CRM), job scheduling, live tracking, field resource management, job finance and business intelligence into one platform.
Jason Nash, head of product, BigChange said: “Today many companies are still burdened with paper or with systems such as accounts, vehicle tracking, and job booking that are completely disconnected. It’s all very inefficient and hinders any improvements in productivity and customer service. There has been a seismic shift to digital working in recent years and the pandemic has accelerated that trend. A lot of crane inspection and servicing operations have already made the first moves to be at least partially paper-free, with software for accounting as well as for compliance, job booking and scheduling – and many have installed vehicle tracking.
However, these various systems often operate separately, which increases workloads and complexity along with the challenge of dealing with multiple suppliers. Staff have to switch from one system to another and then manually enter data for customer reporting, invoicing and accounting. Job management platforms enable workers on site to use mobile devices to synchronise in real-time with the office -and managers out of the office – giving everyone 24/7 visibility of all jobs. Compliance is made easy as vehicle trackers provide live location information, which is supported by accurate, time-stamped records, all backed up with accompanying photographs from site.
The coronavirus pandemic accelerated a transition to digital platforms that was already underway, and those companies ahead of the curve are now reaping the benefits. “By eliminating paperwork all the way from booking to job completion, productivity in the office is transformed,” said Nash. “The number of staff needed to manage operations is typically halved. And in the field, better job scheduling and more dynamic resource allocation, plus full digital reporting via mobile devices, means teams can complete more jobs per day with productivity increased by 20% or 30%.
“In addition, there are big benefits to management as systems provide 24/7 visibility of everything going on. Furthermore, live ETA alerts and digital reports from site – backed by tracking data and on-site photographs – significantly boost customer service.”
Digital tools also enable companies to scale up much faster and in a more sustainable way. “Gains in productivity, management and customer service free up resources and help with business retention, allowing more work to be taken on,” said Nash. “However, there are specific characteristics that a system needs to support business expansion. Traditionally systems have been pretty inflexible – for example, creating new job cards and reports was a time-consuming and costly exercise. You need a system with unrestricted adaptability and in particular a mobile app that can be easily customised. This allows workflows, job cards and reports to be configured to meet virtually any conceivable type of job.
“Traditionally only the larger companies could afford the investment in advanced IT systems, making it difficult for smaller players to compete. Today, platforms like BigChange put all companies on a level playing field. This is particularly important when pitching for new business where clients need their suppliers to stick to stringent procedures in areas such as health and safety, quality, compliance and certification. Many of our users say the platform is vital to winning more business.”
With crane inspection, maintenance and repair work now often being done by third parties, companies also need the flexibility to add and remove contractors from job management platforms.
“We deal with quite a few businesses that have expanded from being just a local business to a being a regional or national business and they often do this by contracting,” said Nash. “Crucially, any contractor can immediately access the BigChange mobile app. It is exactly the same app connected to the same central system. This means the service is seamless; everything coming back from the field is as if it is from one of their own operatives.”