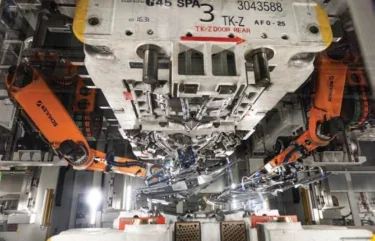
2025 marks the 56th anniversary of Sellick Equipment, a company that has grown from a small family operation to a global leader in the forklift industry. The journey began in 1969 when Walter Sellick, along with his sons Howard and David, converted a Ford 4500 industrial tractor into a 6,000-pound forklift designed for outdoor use.
This initial innovation marked the beginning of a family-run business that would evolve over the decades into Sellick Equipment Ltd., a renowned manufacturer of roughterrain and truck-mounted forklifts.
In the early 1970s, Sellick began with basic tractor conversions, but the company’s growth accelerated when they developed an integral one-piece frame for their forklifts. This design allowed the forklifts to accommodate various industrial powertrains and led to major partnerships with well-known brands like John Deere and International Harvester. The idea that started in a small workshop in Harrow, Ontario, soon grew into a company with a global footprint. Today, more than 11,000 Sellick-built forklifts are in use around the world, and the company has over 200 dealers throughout North America. Remarkably, Sellick Equipment is still a family business, with Walter’s grandson Colin Sellick leading the company.
Sellick’s forklifts come in a wide range of sizes and capacities, from 5,000 to 16,000 pounds, and are designed with features like the Sellick See-Thru mast, which provides visibility for operators at higher lift heights of up to 30 feet. Four-wheel drive is a standard feature on all models, making them perfect for rough terrain. Other standard features include operator guarding, full instrumentation, and lighting. Customers can also choose from a range of options, such as fully enclosed cabs with heating and air conditioning, hydraulic fork movement, and various fork lengths and carriage widths, allowing for customization based on specific needs.
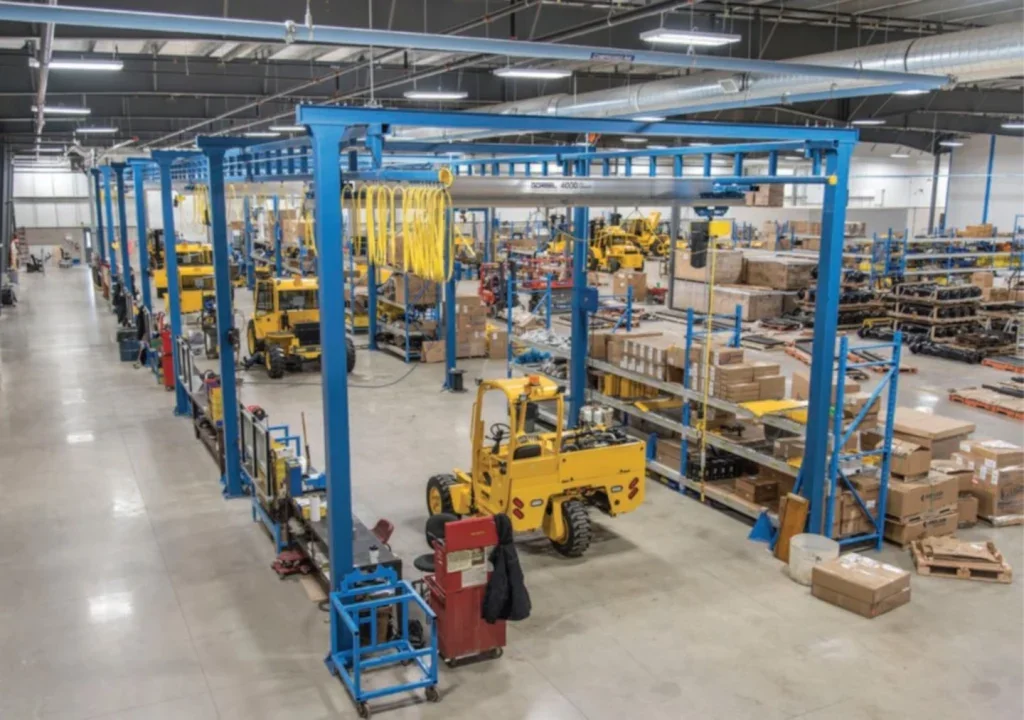
In 2018, Sellick took a significant step in expanding its manufacturing capabilities with the opening of a $21 million, 126,000-square-foot assembly plant in Harrow. This new facility was equipped with state-of-the-art machinery, including CNC laser cutting machines, automated storage and retrieval systems, and a dedicated paint line. One of the key focuses of the new factory was to improve the movement of heavy, welded subassemblies around the shop floor. To address this, Sellick engineers visited several trade shows, including the Fabtech show in the United States, where they tested various systems and ultimately decided to partner with Gorbel, a company based in Fishers, NY, known for its advanced crane solutions.
“When it came down to ease of use, it was Gorbel by far,” says Colin Sellick. “There was no one that was even close to having a system that worked as well or as easily as the Gorbel system.”
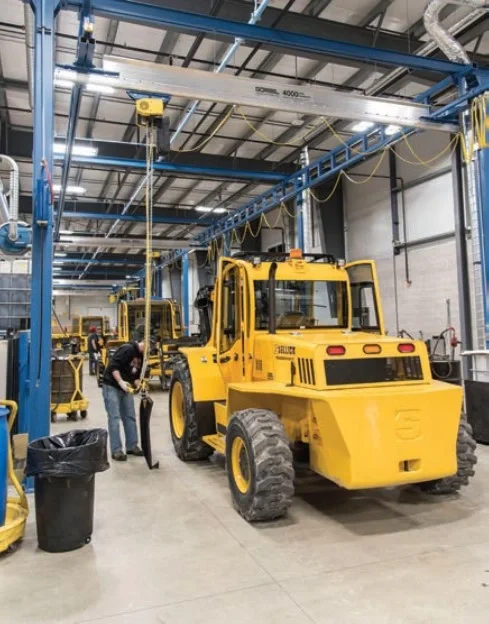
At Sellick’s old facility, engineers had to contend with a number of obstacles, including low ceilings, structural columns every 15 feet, and limited floor space. These limitations made it difficult to move materials efficiently, and in some cases, forklifts were needed to help transport items during the assembly process. But with the new facility, Sellick was able to install two free-standing Gorbel workstation cranes in the fabrication area to support their milling machines. These cranes, which feature a moving bridge that runs across parallel tracks, provide a flexible way to move heavy loads both vertically and horizontally, helping to streamline the production process.
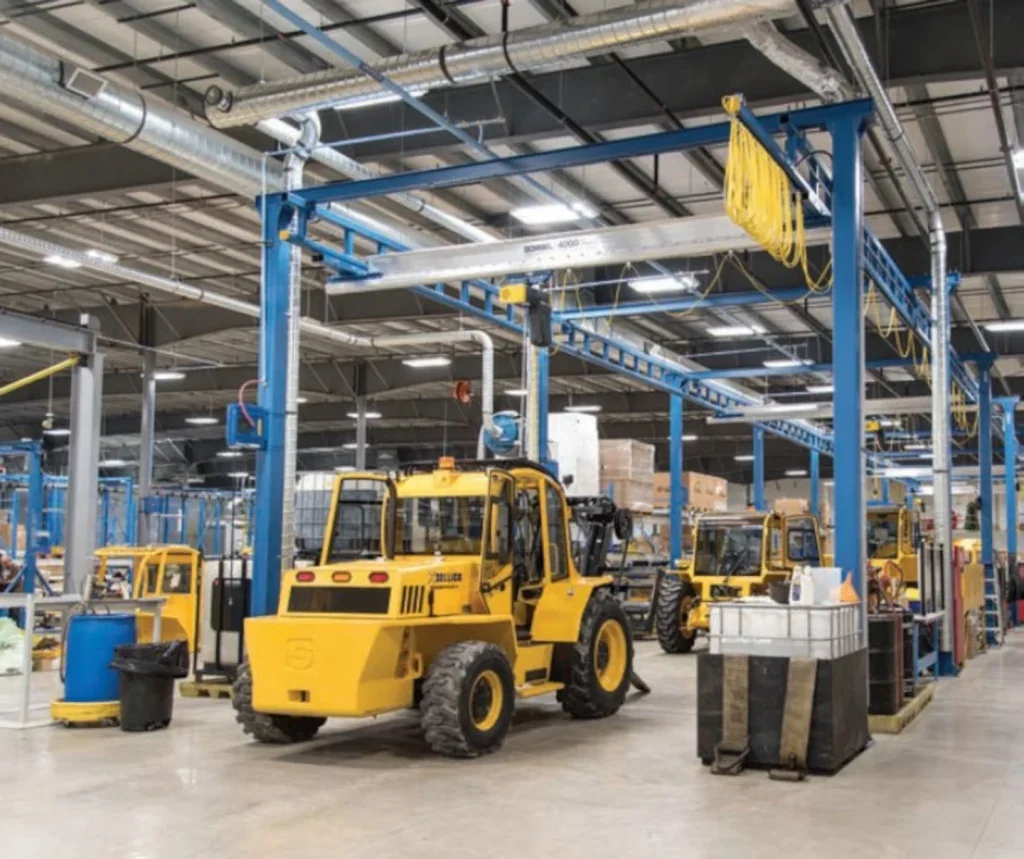
One particularly notable installation was a 140-foot long workstation crane on the assembly line, which was equipped with four aluminum bridges, including two 2-ton cranes and two 1-ton cranes. This system is capable of servicing 16 welding cells along the line, providing a smoother and more efficient workflow. Productivity has increased as a result, with workers now able to move parts freely along the assembly line without restrictions. The crane system has also created more space for part storage, further improving the flow of operations.
Assemblers at Sellick are particularly pleased with how easy the Gorbel systems are to use, especially under load. The cranes are designed to ensure that the load stays exactly where it should, without drifting or sliding along the bridge, which makes it much easier to place parts with precision.
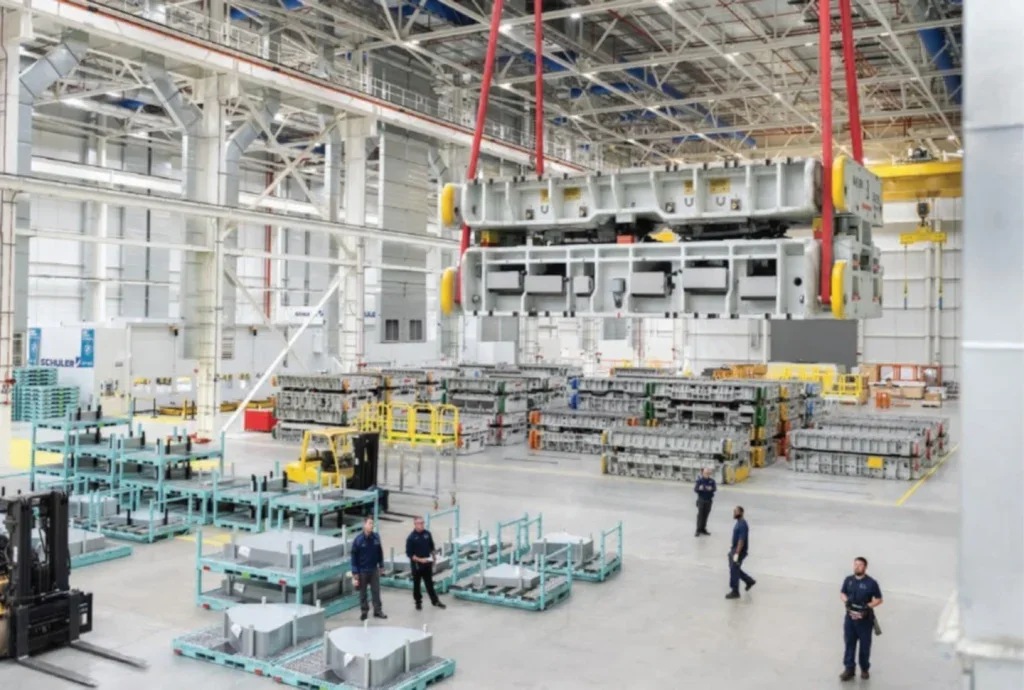
The push for automation and innovation doesn’t stop at Sellick. Companies like Konecranes have been leading the way in the use of automation and advanced material handling technology in the automotive industry. In 2000, Konecranes won one of its largest orders from General Motors for the modernization of assembly plants across the US and Canada. More recently, Konecranes has partnered with BMW to help support their new press shop in Spartanburg, South Carolina, which started operating last summer.
The press shop is crucial for the production of the BMW X3 Sports Activity Vehicle, stamping large metal parts like doors, fenders, and body sides. This facility is part of BMW’s larger strategy to transition to electric vehicle production, with plans to begin assembling fully electric models in Spartanburg by the end of 2026.
“We are further expanding our commitment,” says Milan Nedeljković, a board member at BMW. “At the end of 2026, assembly of all-electric Sports Activity Vehicles will start here in Spartanburg.”
The new press shop in Spartanburg represents a $200 million investment and will play a key role in BMW’s goal of assembling at least six fully electric models in the US by 2030. The press shop is equipped with the latest technology to improve efficiency and quality. The highspeed presses are capable of producing up to 10,000 parts per day, with a new automated system designed to move blanks from one station to the next quickly and efficiently. After the parts are stamped, they go through quality control, where they are checked under special lighting that mimics natural daylight to ensure consistency and accuracy.
BMW’s Spartanburg facility, which has been operational for 30 years, has produced more than 6.7 million vehicles and remains one of the largest automotive plants in the world. The site is highly automated, with over 2,600 robots used in various stages of production, including assembly, painting, and material handling. The plant is also committed to sustainability, generating around 20% of its own power from methane gas and using hydrogen fuel cell technology to power around 800 pieces of material handling equipment.
According to Tad Dunville, managing partner of Safe Lifting Partners, stamping cranes, like those used in BMW’s press shop, are among the largest in the automotive industry. These cranes are essential for moving heavy steel coils into the stamping area and for changing dies in the stamping machines. The dies, which can weigh up to 40 tons, are crucial for shaping car body parts like doors, hoods, and fenders.
“Stamping cranes usually have two main tasks: one, to move the steel coils off of railcars and trucks into the inventory of the stamping plant and then from inventory to the processing area where the coils are decoiled – unrolled – then blanked – cut into flat sheets of perhaps 4’ square – and then stamped into car doors, hoods, roofs, and fenders; and two; for changing the dies in the stamping machines so that the stamping machine in a particular area can change from making left doors to hoods or similar,” he said.
“As time goes on the human cost goes up, and that includes safety and injury costs. The BTH, as we call it, or Below the Hook device, has gone from a couple of chains to rigid C-hooks and/or spreader bars to motorized retracting and rotating devices. What this has enabled automakers and steel companies to do is keep hands away from the load, which has been shown by empirical evidence at companies like Nucor Steel to be leading cause and cost of injuries.
“The next generation of change is to take “smart crane” features like sway control and load monitoring and make the BTH smart with similar products. This is because it is very important to automakers to change stamping dies very fast but the dies are very expensive, very big, very heavy, and hard to see around. One stamping die is the size of a small Volkswagen and weighs over 40 tons, which is the weight of 40 Volkswagens. A stamping die is essentially two solid blocks of steel stacked together, with the mated faces in the shape of the door or hood that is desired.”
He explains; as powered BTH devices are becoming more common, companies are trying different things to make them smarter and improve productivity. “Some things have failed – for example, workers in certain Detroit factories took offense at the presence of cameras, even though they only fed to the crane operator’s control box and not to management. Other ideas have worked better, such as strain gauge sensors that detect the presence of a load and the even distribution over lifting points. You might be surprised to hear this, but many companies required a red circle light to shine under the crane. My company has an innovative light that is not only brighter for better visibility in well-lit buildings, but the pattern of light it throws is faster recognized by the human eye. This device is quickly becoming popular in environments where the company wants operators – and their hands – to stay away from the load for safety reasons.
“Another BTH innovation that myself and some other guys came up with for an automotive stamping project at a leading Japanese-American manufacturer and have used repeatedly since then is the automation-ready BTH. In the past, there were silos of buyer/contractor/ crane builder/BTH builder/automation contractor. Each had their own goals and the back-and-forth just to design and estimate the costs was costly and time-consuming. With our pre-engineered automation-ready BTH, we had most of the smart crane sensors required to perform common tasks and could quickly estimate and produce an automation-ready BTH.
“As smart cranes and smart BTH become more and more common at top tier manufacturers such as big auto and big steel, we’ll see these features start to trickle down into steel services, processing, and distribution to speed up throughput and prevent injuries.”
Meanwhile, Yuantai Crane (part of Dongqi Group) based in Zhengzhou, Henan Province, otherwise known as “the Hometown of Hoisting Machinery of China”; has also been improving material handling in the automotive industry with their KBK crane systems. These cranes, designed to handle heavy components like engine blocks weighing up to 3,300 pounds, have been successfully implemented in several assembly lines, including for a German automobile manufacturer. The cranes have helped reduce assembly times by up to 30% and have cut manual handling injuries by 40% over the course of a year.
“Efficient material handling is crucial in automotive assembly, as it directly impacts safety, productivity, and overall operational efficiency,” a spokesperson from Yuantai Crane explains. “By reducing manual lifting and optimizing the movement of heavy items, these cranes help ensure smoother workflows and reduce costly delays.”
The KBK cranes are designed with safety features like overload protection and compliance with industry standards. These systems have proven to improve quality control, reduce assembly times, and minimize the risk of injury in the workplace. In addition, they offer significant energy savings, aligning with the automotive industry’s push toward more sustainable practices.
“This implementation allowed for smoother workflows and reduced assembly times by up to 30%. Additionally, the ergonomic design of the cranes minimized manual lifting, resulting in a 40% decrease in reported manual handling injuries over a year. Another case involved a manufacturer that used KBK cranes to streamline the testing phase of engine blocks, enhancing precision in positioning and reducing the risk of damage. This resulted in a notable improvement in quality control metrics, demonstrating the cranes’ positive impact on both efficiency and safety,” the spokesman added.
“Additionally, the safety features of KBK cranes, including overload protection and compliance with industry standards, ensure that operations are conducted with the utmost safety and reliability. By investing in this advanced technology, companies can streamline operations, reduce the risk of injury, and improve overall productivity. Engaging with suppliers and experts in the field will provide insights and tailored solutions to meet specific manufacturing needs. Embrace the benefits of KBK cranes to elevate your production capabilities and foster a safer, more efficient work environment.
“The successful installations of workstation KBK cranes offer several key takeaways. First, thorough planning and assessment of the facility layout before implementation are critical to maximizing the cranes’ effectiveness and ensuring smooth integration with existing processes. Second, investing in comprehensive operator training proved vital for maximizing safety and efficiency; operators who are well-trained in the crane’s functionalities can better utilize its capabilities. Lastly, continuous monitoring and feedback mechanisms can help identify areas for improvement, enabling manufacturers to adapt their processes and enhance overall productivity. By learning from these implementations, other facilities can replicate similar success in optimizing their heavy component handling.”
While workstation KBK cranes offer numerous benefits, there are some limitations to consider. One primary concern is their load capacity; although designed to lift heavy engine blocks (up to 1,500 kg or 3,300 lbs), exceeding these limits can compromise safety and performance. Additionally, workspace constraints can impact crane installation; facilities with low ceilings or complex layouts may need customized solutions to fully utilize the crane’s capabilities. Furthermore, the flexibility of KBK systems, while advantageous, may require careful planning to avoid interference with other machinery or workflows in tight spaces.
Looking ahead, there is growing interest in the development of smarter, more automated crane systems that can adapt to changing production needs. Innovations like smart sensors, IoT connectivity, and lightweight materials are expected to further enhance the performance and efficiency of crane systems, allowing manufacturers to improve throughput and reduce the risk of injury.
“KBK cranes play a critical role in improving material handling efficiency and reducing energy consumption,” the Yuantai spokesperson says. “As sustainability becomes more important in the automotive industry, these systems will be essential in achieving greener, more efficient manufacturing processes.”
With continued investment in automation and smarter technologies, companies like Sellick Equipment, Konecranes, and Yuantai Crane are helping to shape the future of manufacturing, improving efficiency, safety, and sustainability in industries ranging from automotive to material handling.
CAR-O-LINER LAUNCHES ERGONOMIC COLLISION REPAIR TECHNOLOGY
Car-O-Liner has launched a BenchRack Versa collision repair technology.
“The Car-O-Liner BenchRack Versa revolutionizes repair with its unmatched versatility and effi ciency,” said Tim Garner, National accounts and OEM sales manager, Car-O-Liner. “Its adaptable design and high productivity make it a signifi cant breakthrough in the shop for today’s technicians. It is easy and ergonomic to use, allowing for safe and fast vehicle lifting.”
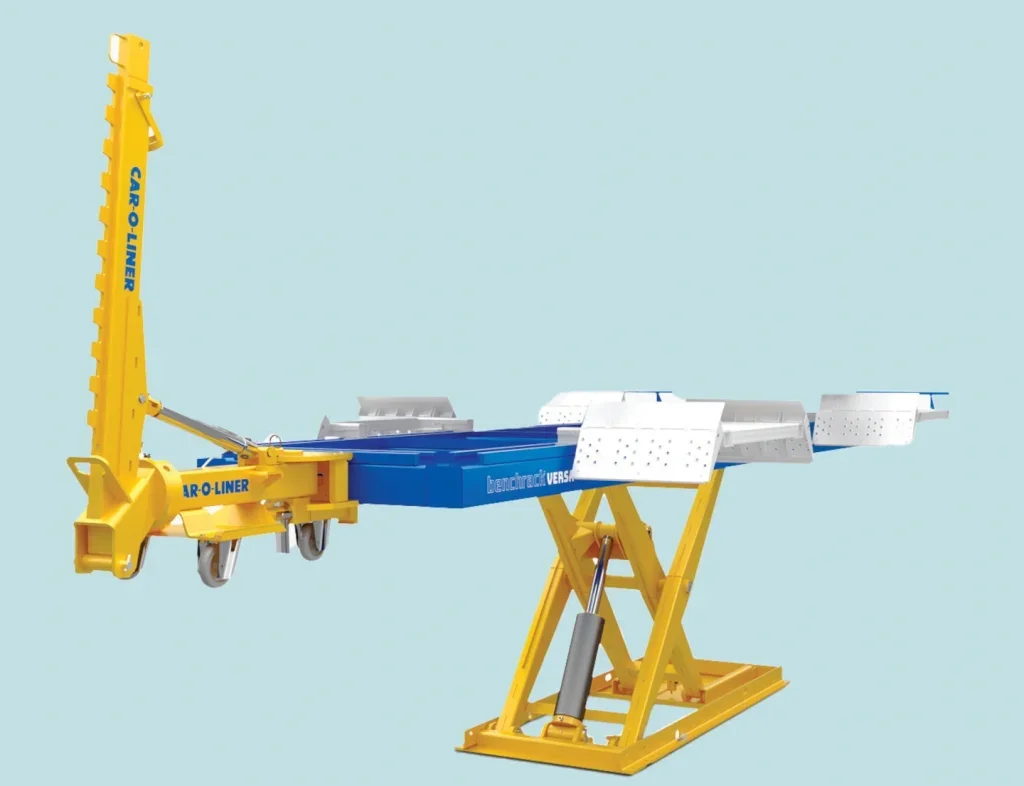
The BenchRack Versa features steel and aluminum ramps that facilitate quick and proper vehicle lifting, providing full access for immediate work. The new short ramps enable lifting by the wheels, allowing technicians to quickly and securely position vehicles at an optimal working height.
The lightweight steel and aluminum ramps are designed to reduce weight and improve ergonomics. These ramps are also positioned higher on the frame, allowing for quick diagnostic measurements while the vehicle remains lifted, enhancing both efficiency and safety.
Key features of the BenchRack Versa include an increased lifting capacity up to 10,000 lbs. and a lifting height of up to 57 inches, significantly enhancing the ergonomic working height and providing greater comfort and efficiency for technicians. Low-profile, lightweight ramps eliminate the need for rubber blocks when lifting vehicles, ensuring OEM compliance, especially for electric vehicles.
The design of the BenchRack Versa enhances shop fl ow by enabling drive-over access, allowing seamless integration into any workshop layout. This feature ensures that equipment placed behind the BenchRack Versa remains easily accessible, optimizing space and efficiency.
The Quick Clamping Q63 arms allow users to achieve faster clamping with less eff ort. This provides higher effi ciency, more vehicles processed and increased profi tability for the shop.
“BenchRack Versa significantly boosts productivity and return on investment by allowing repair work to begin immediately upon lifting,” said Garner. “With effi cient drive-on ramps and the optional Q63 arms, shops can drive over, lift and start working. This enhancement means more cars serviced, more measurements taken and ultimately, more revenue for the shop.”