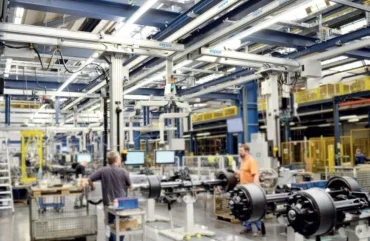
Most factories need cranes. If the factory makes only light objects, it may need only a light crane. A portable A-frame gantry crane serves many autorepair shops and the like very well, and very economically; a small wall-mounted jib crane can also suffice. But sometimes these do not offer all the functionality that is needed. The area they serve can be small; and they are not good at moving loads from A to B across the factory floor or into neighbouring sections of the plant, say from fabrication to paint-shop.
A full-blown large overhead bridge crane system can do these things – or most of them – but becomes very expensive. It may be overkill in terms of the loads to be lifted; it requires expensive installation and a building that is strong enough to take it; and once it is in place it is difficult or impossible to alter or to extend the area it can cover.
Light crane systems fall between the two extremes and can tick all the boxes. There are easy and cheap to install; they have capacities of up to around 2000kg (above that, and it is pushing the boundaries to call them ‘light cranes’). If you don’t want them or cannot have them hung from walls or ceilings they can stand on their own legs, so they can be put into any building no matter how flimsy its construction is as long as it has a floor of a couple of inches deep of concrete, which most places do; and these things are modular, which makes them far more adaptable and far more flexible than their larger brethren. For the right situation there is really nothing not to like about a light crane system.
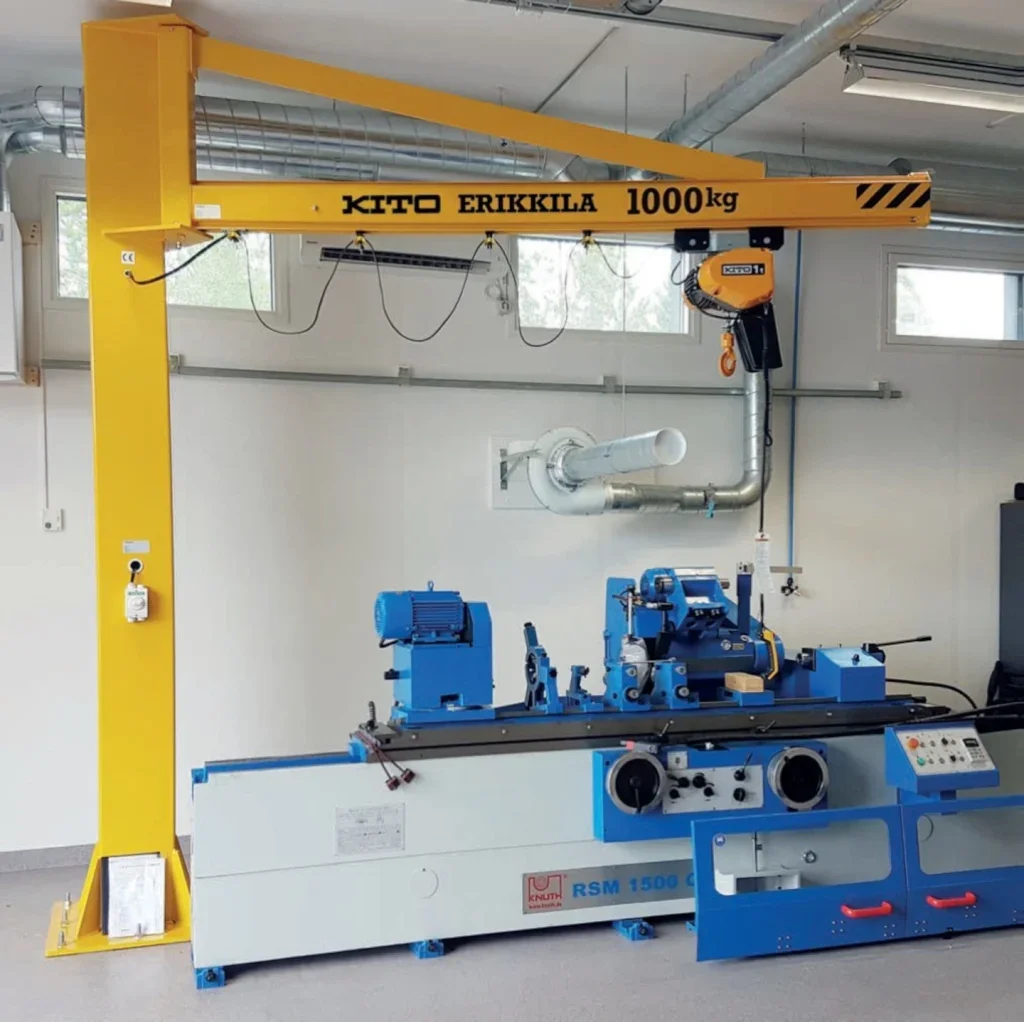
They can come in a number of designs: as mini bridge cranes, which cover a rectangular area and can move in both X and Y directions within it; or as hoists mounted on monorails, which can run all around your factory along a line only – though the line can be straight, curved or looped, and can be equipped with switches and turntables to your heart’s content to carry your load from machine to machine, or process to process; there are even profile devices that can let them go through open and closeable doors if you like, which is not something that I have seen a fixed overhead gantry crane doing very often if at all. And of course they are customisable to your own requirements; and when your requirements change, they can be added to, shifted a bit, moved, or whatever.
Monorails are, essentially, hoists that are hung from overhead tracks. Generally, rather than being simple I-beams, the tracks are special designs of enclosed profiles; different track profiles are available for different purposes. The profiles enclose the trolley wheels, to give protection against dust and contaminants and therefore longer life and smoother running. Profiles can also carry electrical contact strips for powering motorised hoists and trolleys; (the alternative of course is manually-propelled ones.)
Other advantages of profile over I-beams are that profiles, being smaller, can fit into lower headroom spaces. Their construction can give more side-to-side rigidity, which allows steadier travel of loads, more accurate load positioning, and on bridge designs reduces or eliminates crabbing on the bridge travel.
They offer very low friction, which makes it much easier to push the load on a manual system, and lighter motors and more economy on a powered one. Track profiles are lighter than I-beams and therefore impose a lower dead load on the supporting structure and are easier to handle when installing.
Profiles are widely available in steel and in aluminium. Steel track is stronger than aluminium but weighs more, meaning that a steel profile is heavier duty and can span longer distances between supports; but aluminium generally gives smother trolley movement, and does not need painting against corrosion.
The same considerations apply to bridge girder designs. Thus Erikkila offer, as well as light jib cranes, single and double girder light cranes, in steel or aluminium, that can be manually operated or equipped with electrical movements for the trolley and bridge. The maximum rated capacity of a single girder aluminium crane is 1,000 kg; the maximum rated capacity of a single girder steel crane is half as much again, at 1,500 kg. Double girder steel cranes have a rated capacity of 2,000 kg. Steel and aluminium profiles can be combined to give optimised solutions for any particular need. The hoist and trolley easily moves between the two.
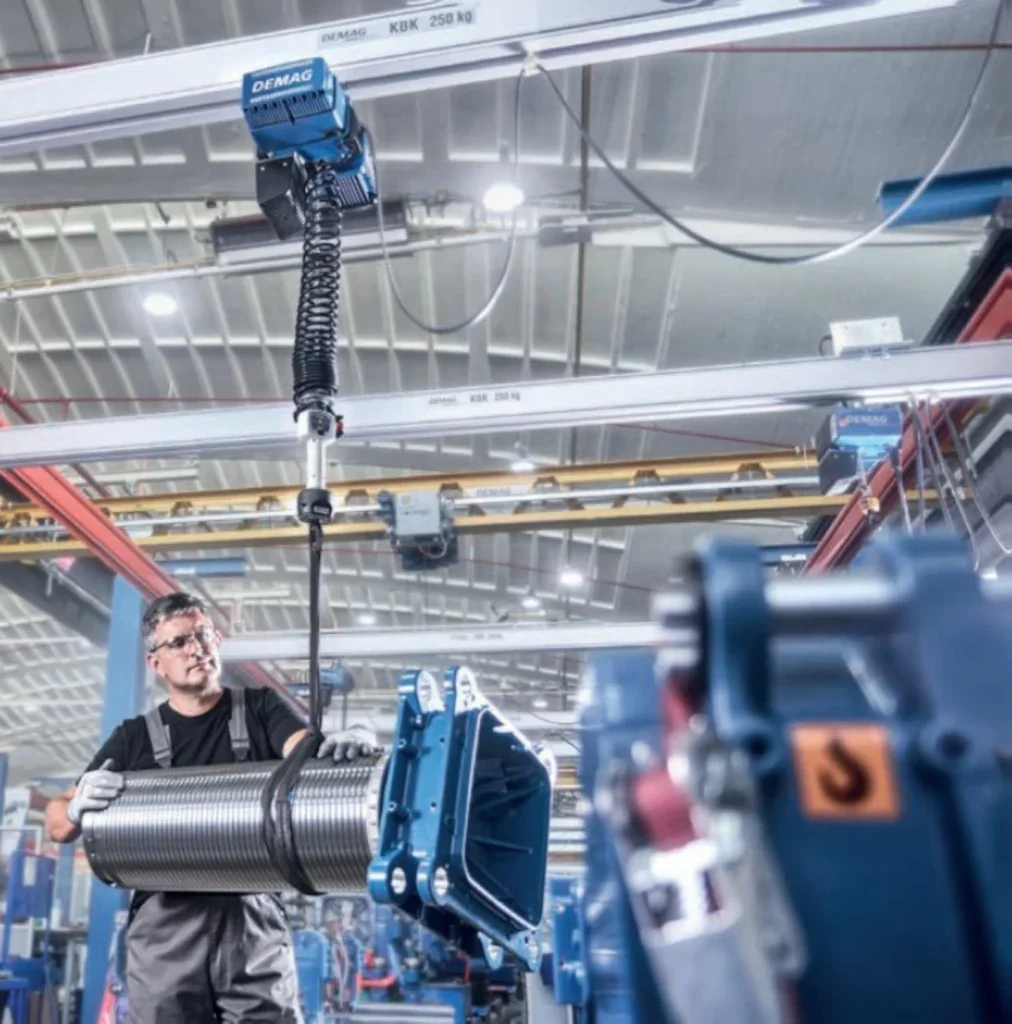
Headroom can be another consideration. Low headroom versions of their single and double girder cranes are available. In these the bridge profile is raised between the tracks to maximize the available lifting height. Erikkila’s enclosed profile track protects the trolley and internal power supply from dust and external impacts.
A smooth-running trolley centralizes the load automatically in the correct lifting position and helps minimise load sway.
The correct articulated track suspension combination for each application can be built from a wide range of standard components for different ceilings columns and profile types.
Street Crane has its Light Crane System (LCS), which is an advanced modular system which combines monorail and overhead girder elements in one.
Once again, the bridge is itself a monorail profile beam, of aluminium or of structurally-optimised folded steel inside which the motorised trolley travels. The trolley supports the lifting hoist, which is a Street LX electric chain hoist. Monorails and single beam cranes are available in capacities up to 1500kg, and double beam cranes up to 2000kg capacity
They form cost-effective and highly durable workstation cranes, custom made for each individual application and ideal when handling requirements are localised. They may be suspended from the building’s structure, or free-standing on their own columnar supports. Curved profiles, in radii down to one metre, and turntables are available to connect several systems together.
Street Crane points out that such work station cranes significantly improve productivity even if the workplace is already equipped with a main overhead crane spanning the workshop. “Efficiency is improved because individual operators in localised workstations often have the requirement to repeatedly lift lighter loads. In these cases the workers concerned spend a high proportion of their time waiting for the main overhead crane to become free, and then they spend even more time away from their workstation bringing the main crane to the lifting point.”
Other advantages are true vertical lift with no hook drift throughout the hook stroke, long-life disc brakes on the hoist, overload protection by a torque-limiting clutch in the hoist mechanism, and external removable fan-cooled motors with cooling fins on all motions of the crane.
In August this year, German light cranemakers eepos, based in North Rhine- Westphalia, became part of the Kito Crosby Group. At its foundation in 2006, the eepos business model was that of supplying the niche of smooth-running modular crane systems which for weight reasons were to be made entirely of aluminium.
They are also claimed to be completely jam-free, extremely low-maintenance and extremely durable. Carmakers Audi adopted the system early on, which helped establish the eepos one aluminum modular system as what the company says is a new quasistandard for light crane systems up to 2t.
The eepos one light crane system can be used as a surface crane system with up to 14m span and combined with crane bridges that can be moved manually, electrically or pneumatically. Slewing cranes and power supply columns can be added; all eepos products are compatible with each other.
Their aluminium profiles come in sizes from XS to XXL. The eepos trolley is an aluminium forged part with eight rollers aarranged on two levels for smooth running. They run significantly quieter than on standard aluminium systems, say eepos, who also claim that the operator need exert only one-third of the normal pulling force to move loads.
Systems can be electrically powered: the eedrive crane drive has permanentlyexcited synchronous motor and integrated servo controller with a gearless direct drive to the wheels. It can take tensile loads up to 1t and give travel speeds from one to 80 metres per minute.
Demag has its KBK light crane system. It is a modular kit – it claims the world’s largest section of system components for it – and the components can be combined to create bridge cranes, monorails, and even pillar and wall-mounted slewing jib cranes. The running rails of bridge crane assemblies do not have to be parallel, which means that non-standard shapes of buildings or production areas can be more fully catered for.
The steel version of the KBK carries up to 3,200kg – which is above our self-imposed and somewhat arbitrary 2,000kg limit that we set above. It has six sizes of profile, and nine different profiles altogether when you count the versions which carry integrated conductor lines for electric powered operations. It is compatible with, and can be combined with, their KBK Aluline system, the track of which of course is aluminium (and which does stick to the more standard 2,000kg capacity limit.) The Aluline system has five sizes of profile section, three of which have the added option of integrated conductor lines.
One advantage of combining the two systems of track is that steel sections can span longer distances between supports so cold be used for the wider gaps, with aluminium giving quieter and smoother travel elsewhere.
The trolleys have plastic wheels mounted in anti-friction bearings and lubricated for life, a design which is intended to give smooth-running performance and minimum rolling resistance over their entire service life as well as effective shock absorption.
Travel drives can be electric or pneumatic; traction, through large friction wheels, does not depend on the position or the weight of the load.
Demag stress the reduced approach dimensions, which allows installation close to walls and maximises the lifting area available in any setup; the system, they say, is virtually maintenance free.
It can be assembled as push-travel and electric systems, or with pneumatic operation, or as fully-automated installations; new components can be integrated or existing units can be easily replaced at any time.
The monorail profiles can of course be supplied with curves, but 90 degree rightangle turns can be accomplished using a manually- or electric-powered turntable.
Similarly, junction points for merging or separating tracks can also be manual or electric. Up to eight conductors can be set into the profile section, to allow multiple independently-controlled trolleys on the same track. Power can also be supplied by trailing cable.
All in all, light crane systems offer flexibility, economy, adaptability, and simplicity. They are one of those rare concepts which are absolutely fit for their purpose.
KONECRANES MAINTAIN MOTORS
The MAN Service Group is one of Europe‘s leading commercial vehicle, engine, and mechanical engineering companies. Challenge MAN Nederland Dealer is a repair shop focusing on truck and bus maintenance. Loads mostly consist of motors, gears, axles, and tires. In their old facilities, MAN had only one crane for both trucks and buses. “We noticed that this single crane was not enough, so we decided to separate these maintenance functions and invest in two cranes in our new facilities,” said Arjan Wijkamp, plant manager, MAN Nederland Dealer.
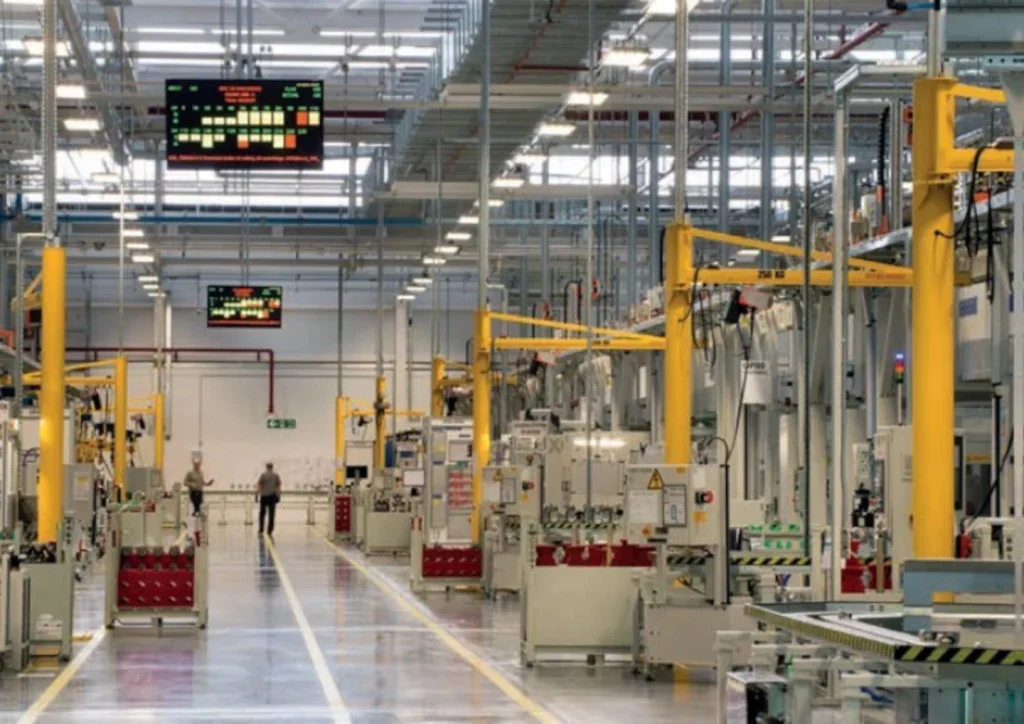
It was clear that the plant needed two basic cranes for this kind of maintenance job. The cranes are only used occasionally – sometimes they get daily use, but other times, there could be a break of up to two weeks between uses.
The customer invested in two Konecranes CLX overhead cranes to increase productivity. The CLX crane is equipped with travel inverters, which greatly improve accuracy in load positioning. This is particularly useful during precision tasks like removing and replacing engines – exactly what the customer needed.
“I thought CLX would be the answer because of its accurate low hoisting speed and its very modern outlook in this modern plant,“ said Frank Tros, specialist, Industrial Cranes & Service. Besides these two cranes, the MAN training centre in the central Netherlands has also ordered a 3.2-ton chain hoist crane. There they educate their service technicians to use their cranes. Operators who are new to the crane take some time to get familiar with the travel inverters, but they soon notice that the load moves much more smoothly.
Another Konecranes automotive application is at Jaguar land Rover’s Engine manufacturing centre in Wolverhampton, UK. There, the assembly halls are home to some 150 Konecranes hoist and crane systems. Standing as a versatile production line lifting solution are 70 free standing XMP pillar jib cranes (Illustrated) each equipped with Konecranes’ popular and versatile CLX electric chain hoist that provides a maximum lifting capacity of 250 kg.
Also on the site are some 80 workstations that centre on Konecranes’ new and modular XA lightweight aluminium crane system.
Spanning up to eight metres in length, 50 of the stations have been specified with additional CLX chain hoists, also rated to 250kg.