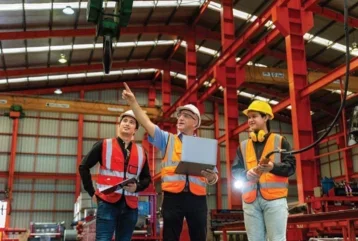
Load monitoring is of course essential. To start with the obvious: it is clearly a good idea to know what is hanging from the end of your hook or hoist. One of the more basic things to know about it is how much it weighs. Lifting machinery has safe working load limits, and to exceed them is a very bad idea indeed.
So, monitoring devices that tell you the weight of your load are a good place to start. There are very many such devices. Generally, they fit somewhere between the lifting device and the load. Different geometries are available: they can be below-the-hook, in the form of load links, or actually part of the normal lifting arrangements in the form of load pin or load shackles. Almost (but not quite – see box) without exception they all use the same technology. One or more strain gauges – delicate, thin networks of wire carrying electric current – are incorporated into them, glued on to the pin or shackle. When the support comes under load it stretches, so the strain gauge stretches with it; which changes its electrical resistance and therefore the value of the current passed through it. The change in current is amplified, measured, and sent to the readout device.
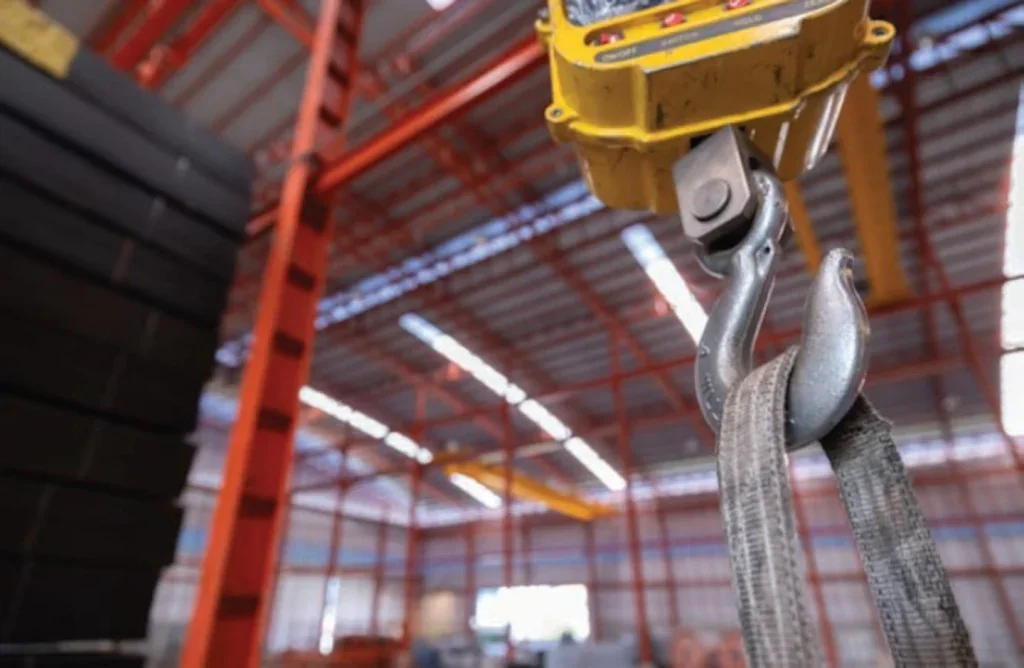
The heavier the load on a pin or shackle the greater the stretch or deformation, and the greater the change in current. Calibration of course is necessary, and devices come with appropriate certification from one of the recognised bodies.
The degree of accuracy is also an issue: especially since the obvious reason for having load measurement in the first place is to prevent overloading your crane or hoist. You want, therefore, to be very sure exactly how heavy the load you are lifting is – and if you reach or exceed that limit your load monitor can set off alarms, or can stop the lift.
Here, geometry plays a part. A lifting link hangs vertically between hook and load. The force of the load is applied straight downwards; the link just stretches, and it does so in a more or less linear way: double the load and the extension more or less doubles. The strain gauge glued to the link also simply stretches with it. Its resistance therefore changes in a relatively straightforward way (though calibration of course is required.)
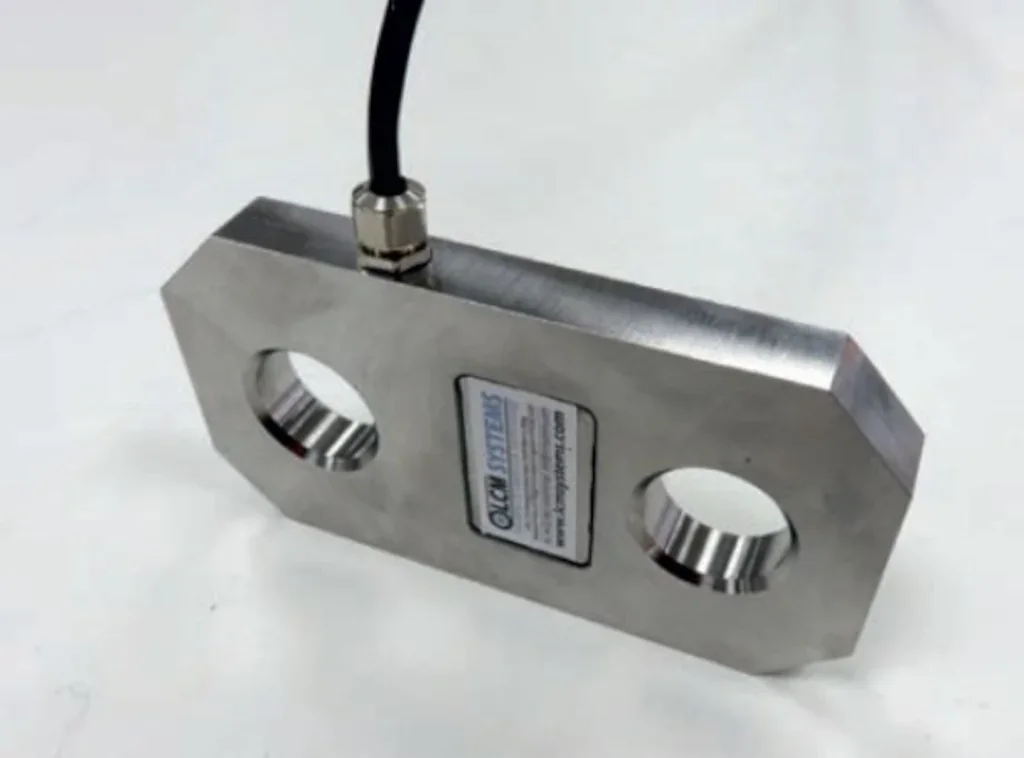
In a lifting pin, however, the situation is different. The pin lies horizontally, with a shackle supporting the ends and the load pulling down on the middle. Without further precautions the pin therefore would not simply stretch: it would bend.
The lower, outside, edge of it stretches more than the upper, inner edge. Complicated things are happening, involving bending moments, arcs of circles and possibly compression of one part of the pin while another part is in tension.
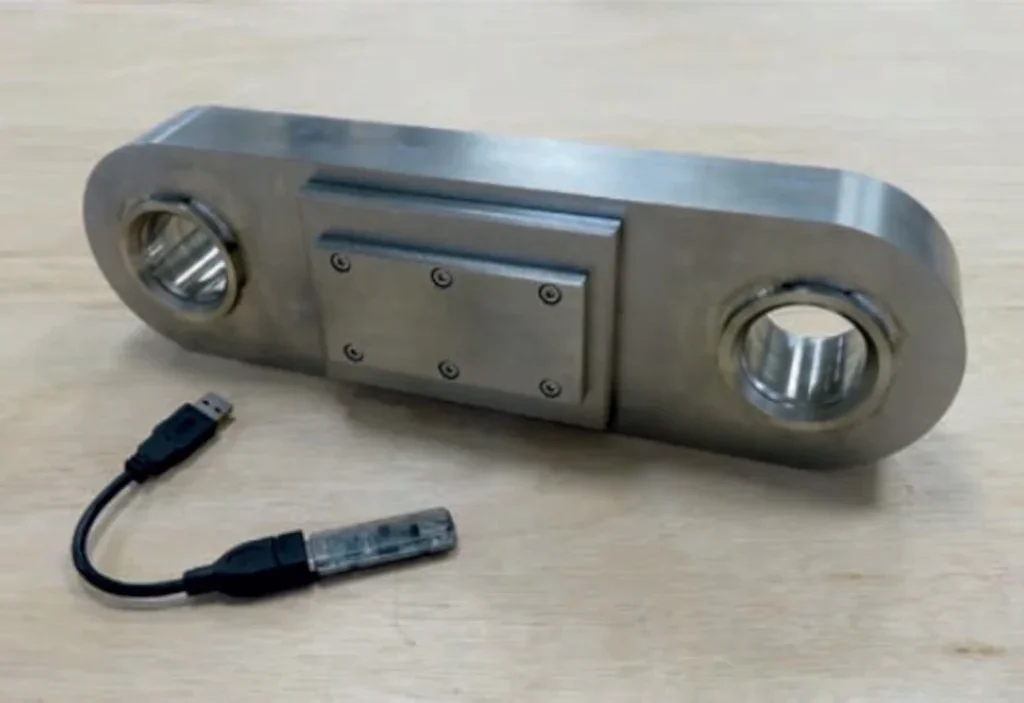
There are also shear forces, at each end of the pin where it is supported by the shackle. All of this has consequences for the output of any strain gauges attached. It will be complex and probably not very linear, and probably not very repeatable.
Load sensing shackles therefore come with bobbins, which partially resolve the issue. The bobbin is essentially a metal collar that tapers in the middle to give a shallow V-shape in which the load-bearing rope sits. The bobbin fits over the loadsensing shackle pin and can rotate freely upon it. Its inside dimensions align with shear grooves engraved on the load pin. It serves three functions.
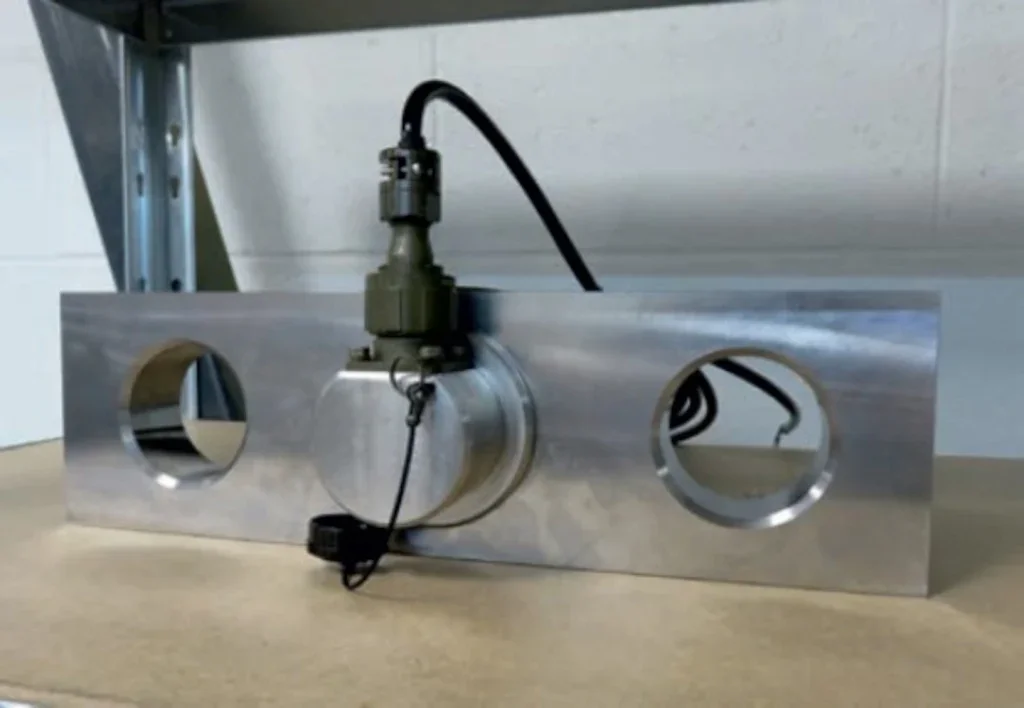
Here is how manufacturers Crosby Straightpoint explain them:
Firstly, the bobbin spreads the load across the whole of the pin, to the shear grooves at either side of the load pin, rather than concentrating it in the middle. In doing so the bobbin absorbs the bending moment and ensures that the pin is under simple shear. Secondly, V-shape of the bobbin centres the rope and ensures that the load is always applied to the same point, which ensures repeatability. Any lifting accessories and attachments – slings, chains, hooks, wire rope will naturally position themselves at the centre of the bobbin, consistently applying the load in one place.
Thirdly, the bobbin supplies strength, so increasing the WLL and the safety factor. For these reasons and others, therefore, it is unwise to operate the load shackle without its bobbin. Even with the bobbin though, load pins and load shackles are generally less accurate than load links.
Crosby Straightpoint manufactures load links, load pins and load shackles. Capacities range from 1t to 2,000t. Smart cell device apps, for Android or IOS, can wirelessly monitor loads via a Bluetooth connection from up to 50m away, though wired versions are also available. The company says it is the first load cell manufacturer to incorporate RFID tags in all its link load cells as standard and is the only manufacturer in the world with load monitoring and measuring products that are certificated to be used within hazardous gas environments.
Despite their lesser accuracy, load shackles do have advantages in some applications. They are more suitable for heavy loads, of the order of many tons. For lighter loads they can be useful also. A load link needs a shackle at its top, to attach it to the hook, and a shackle at the bottom, to attach it to the load. It has a length of its own in any case. These extra lengths can add significantly to the distance between the hook and the load. For low headroom applications this may be an important consideration. For an example of a manufacturer responding the low-headroom needs, see the box. But in general, using a load shackle replaces three components with just one, so does not affect the below-the-hook distance.
There is however more to load monitoring than just weighing the load. Wear and tear is cumulative. Many lifts can have the same effect as a few heavy ones; so data on how many lesser weights your hoist has lifted, and how many times, and over what period of time, is also useful. In an ideal world you want a full record of each and every load cycle, and their cumulative total.
Digital data logging can give you exactly that. Adding data logging and telemetry to your load measuring devices gives far more than simple overload checks. “Collection and analysis of load data can give performance monitoring and operational optimisation. Load cells installed in crane and winch systems can record load weights, lifting cycles and operating conditions, providing valuable insights into equipment utilisation, efficiency and maintenance requirements. By analysing load data over time, operators and maintenance teams can identify trends, detect anomalies and implement proactive maintenance strategies to prolong equipment lifespan, minimise downtime and improve overall operational efficiency.”
That is how monitoring equipment manufacturers LCM put it. The phrase ‘Proactive maintenance strategies’ is in there, and in slightly plainer English means preventative maintenance. You no longer have to replace possibly-wornout parts to a strict timetable, but on a software-calculated schedule that takes into account all the usage parameters of the hoist – cycles, heavy lifts, lighter lifts, unloaded runs of the trolley, accelerations, decelerations, braking effort, temperatures of the motor and brakes and how long they remained at those temperatures….So as well as monitoring just the weight you want a device to log all these inputs, that you can then pass to your predictive maintenance software which will tell you when is the safest and most economical time to replace this part or that part, thus avoiding breakdowns (so saving downtime) without having to replace parts that do not yet need replacing (so saving money.) The readout displays, and their ability to transmit their collected data to software, is a part of load monitoring, and is offered by most manufacturers as part of their package.
LMS (Load Monitoring Systems) for example specialise in the design, manufacturing, sales, rental, and calibration of intelligent lifting equipment and load monitoring products and services. Last year it was awarded the prestigious Kings Award for Enterprise, which, since the company is less than seven years old, is no small achievement. The award is recognition of its success in exporting: LMS has gained an average of 9-10 new customers each month, of which 20% are international. It is now active in more than 45 countries. Load pin shackles, load pins, load links, load cells and load cell data logging, of up to 100 devices simultaneously, are among its lineup.
Its ‘Combo kit’ is designed to make load monitoring simple. It is a rugged case, easily transportable, with foam compartments that hold a aluminium load link, a shackle load pin, two safety box shackles, a T24 HA Handset which can operate with both the load link and the pin, a centralising bobbin and a spare battery set. It can be easily customised for low head height situations.
At the same time as it was earning its Kings Award the Aberdeen-based company was forming a strategic partnership with leading Austrian chain manufacturer Pewag, and had been diversifying the applications that it serves. “Our global vision has been augmented by looking across sectors and diversifying into other industries which include entertainment, aquaculture, construction and renewables as well as traditional spheres such as oil and gas and subsea” said managing director Kirk Anderson.
Monitor Systems Engineering is also based in Aberdeen. It was established rather earlier, in 1997, but happily has also won the King’s Award for Enterprise, which it gained last year.
Its Engineering and Measurement Technology division specialises in the design and build of electrical and electronic control and monitoring instrumentation systems for energy industry vessels such as jack-ups, semisubmersibles, platforms, drill ships, support vessels and FPSOs to industry compliant standards. But it too is diversifying: it now has contracts in onshore and offshore renewables, tank farms, food and drink, and factory automation.
The division designs and manufactures rugged, multi-channel winch line control, wireline monitoring and tensiometer instrumentation. Products are used to control and monitor speed, payout, and tension – both cable and chain – in singleand multi-winch systems. Running Line Tensiometers come with sealed double roller bearings in standard sizes rated from 20 KIPS to over 800 KIPS – smaller capacity units also available – with 17-4 hardened stainless steel sheaves. Tension and payout sensors can be located for easy access. Software is windows-based, with data files easily exported into Excel for post-analysis and display units give clear real-time data, full programmability, and six alarms which are independently linked to any high or low set-point parameters determined by the operator.
Most strain gauges, as we have seen, work on the principle of a strip of metal changing its electrical resistance when it is deformed. Aanderaa Data Systems AS, (part of Xylem Analytics), has a unique strain sensor called the Mipeg S-sensor that works on a different principle. The variable in this case is not electrical resistance but resonance: the natural resonant frequency of a piece of metal varies according to the tension in it. Pluck a guitar- or violin-string and it produces a higher note when it is strung more tightly. The S-sensor uses the same phenomenon.
The heart of the sensor is an S-shaped metal strip fixed at both ends to the inside of a metal ring. When the ring is deformed, the tension of the strip changes; so therefore, does the frequency with which it naturally vibrates.
The frequency is detected as an AC voltage in a coil positioned close to the strip. The vibration is started (‘excited’) by a short pulse of electricity in that same coil; and the frequency of the AC voltage indicates the amount of deformation of the ring – and hence the strain and hence the load. Strip, ring and coil are hermetically sealed inside a stainless-steel housing.
An advantage is that the signal generated is substantial, and therefore needs no amplification. (As we have seen, standard strain gauges produce only very small changes in resistance, which needs careful measurement; this is generally done by means of a Wheatstone Bridge circuit.
Other benefits are that the frequency output is of low impedance, which gives a high immunity to electromagnetic noise. It can be used to measure tensile or compressing forces; it can withstand a ten-times overload without failure; and it is certified for use in ATEX hazardous zones.
The company specialises in digital-based solutions to water-related applications, both maritime and for onshore utilities – for example drinking- or waste-water systems. With their sensor goes their Mipeg X Compact safe load indicator system, which monitors the crane operation and displays it on a 7” colour touch screen.
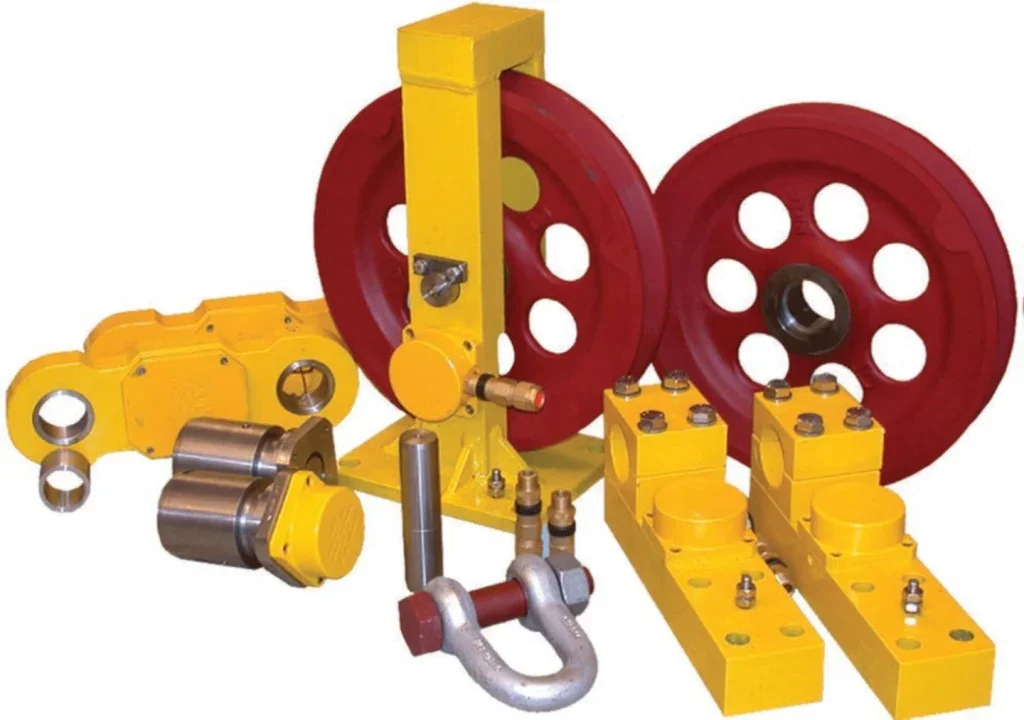
A large, clear analogue pointer shows the percentage of safe working load on top of a “traffic light” Green, yellow and red colour band. Other data can also be displayed.
The lesson from all this is that data from load monitoring systems can be sent to, and considered part of, the overall Internet of Things (IoT); and, if you look at last month’s article on Artificial Intelligence, it can feed into that as well. Which means in turn that it could become, at some future date, part of the operating system of the whole plant.
It is rather more than just measuring the weight of the load.
LARGE AND SMALL LOAD MONITORS FROM LCM
A tiny load link was recently despatched by LCM Systems to a customer in the Netherlands. Due to space restrictions the load link needed to be as small as possible while still achieving a load rating of 5 tons; at just 130mm long by 69mm wide, LCM managed to design a load link that exactly met the customers specification.
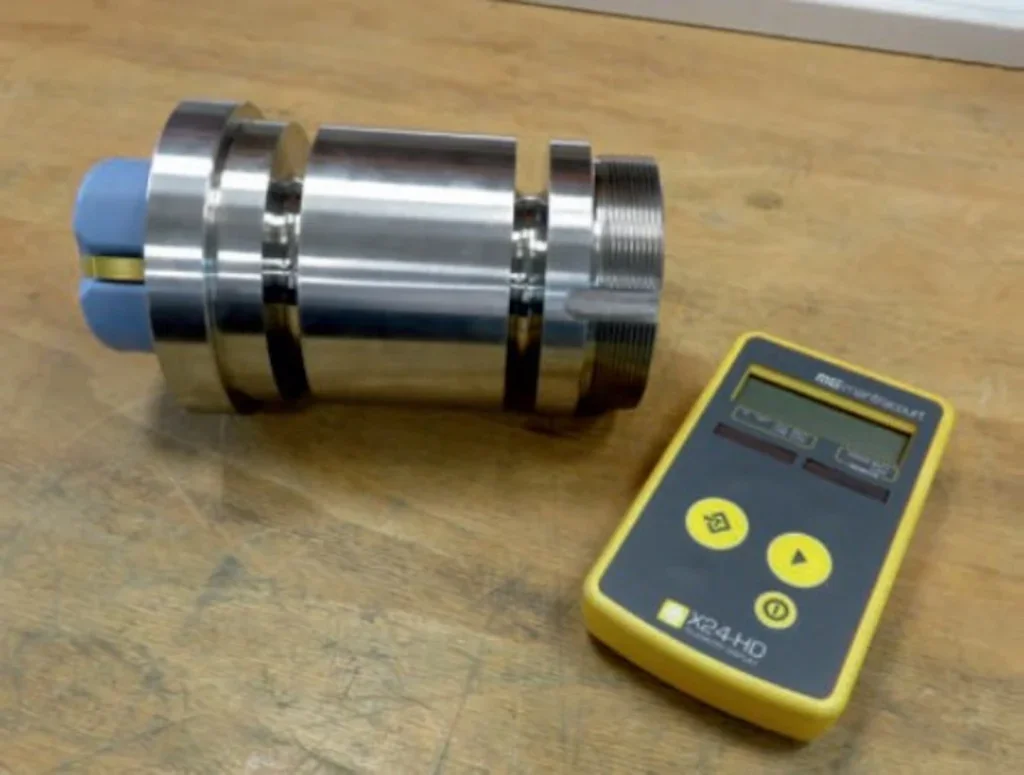
Another example from the same company is smaller still, at less than half that size. At just 75mm by 18mm it is one of the smallest load cells they manufacture.
The stainless-steel dual cantilever beam load cell has a load rating of 50kgs, but is also available in load ratings as low as 2kgs. Widely used in tensile test machines and hopper/vessel weighing systems, this load cell will be going to a UK research facility that supports industries that handle powder or granular materials as part of their processes. The dual cantilever design of the BF2 enables the rejection of off-centre forces, which is helpful for ensuring maximum accuracy for applications where the weight is unevenly distributed. As with most LCM standard product ranges, it can be adapted to suit specific requirements, including load ratings, electrical connectors and dimensions.
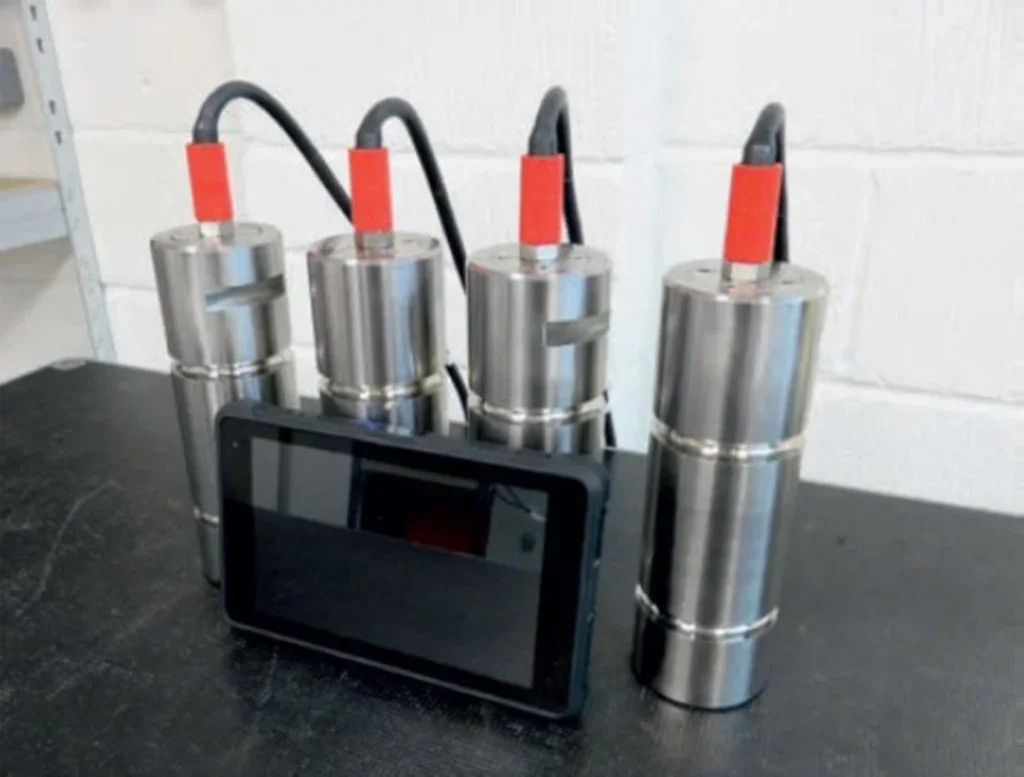
At the other end of the size and capacity scale, LCM have supplied a 9000kN (900 ton) rated load pin, which was shipped in September to an engineering company in Spain, where it will be used for fatigue testing. Weighing in at 230kgs, this 250mm diameter by 600mm long load pin will be installed in an assembly to monitor the applied forces/stresses it is subjected to during operation, allowing engineers to assess how it responds to repeated loading. By analysing the data the structures endurance limit, fatigue life and stress behaviour can be determined.
CM HOIST HAS BUILT-IN MONITORS
Not all monitoring devices are belowthe- hook add-ons. Columbus McKinnon’s Lodestar VS Electric Chain Hoist is available with the company’s Intelli-Connect Diagnostics and Analytics technology built in. This makes it, says the company, the only chain hoist that allows operators to wirelessly program the hoist. But it does not only allow control; it also makes it the only chain hoist able to send detailed diagnostic and analytic information, of the type we have been talking about, from the hoist itself to a smartphone or tablet. Intelli-Connect is available as an option on all new Lodestar VS units or in retrofit kits for units already in the field.
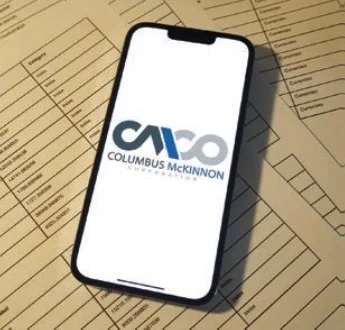
“By combining the capabilities of Intelli- Connect with the Lodestar VS, we’ve made it easier than ever to program, maintain, monitor and troubleshoot your hoist,” said Bryan Holby, senior global product manager, powered chain hoists. “Customers can get insight into how their hoist is operating to easily and proactively monitor performance and schedule maintenance, helping them address issues more quickly, keep operators safer and ultimately reduce downtime.”
Intelli-Connect eliminates the need to connect a tablet or PC to the hoist with a cord. Users can access information wirelessly through the Intelli-Connect Mobile or Mobile+ apps from their mobile device. Intelli-Connect Mobile+ includes continuous equipment monitoring complete with longterm performance information, such as runs, faults, alarms and VFD status variables like fault codes, motor voltage, current, available hoist operating life, and more.
The Intelli-Connect Mobile app is available as a free download on Google Play or the Apple App Store. Users can upgrade to Intelli-Connect Mobile+ functionality for a one-time fee through the app.