UK overhead crane builder Lloyds Konecranes claims to be the only crane service company to use the method for testing crane rope. The system, which scans rope that is reeved, is commonly used in Germany for tram cables. Such cables are required to be tested by NDT, according to Dirk Moll, an engineer at the Institute of Materials Handling at the University of Stuttgart, which sells the system along with wire rope manufacturer Casar.
Although there are no such requirements for crane ropes in the UK, the company is planning to offer the service not just for overhead cranes but also for mobile and tower cranes. Derek Reece, KCI Konecranes Benelux general manager, said he sees most applications in process cranes.
“I think there’s an opportunity for it in places like paper mills and press shops where they change their ropes as a matter of course on a regular basis to offset the danger of failure through internal wear,” Reece said.
He added that as of mid-July he had two orders, from a factory with a machine press and a paper mill, both of which rely on their cranes for production, he said.
With the machine, Lloyds Konecranes can scan ropes from 16mm to 40mm diameter. It paid £40,000 (E60,000) to purchase the reader, several sizes of dies, and training from wire rope manufacturer Casar, Reece said. Pricing had not been set.
The University of Stuttgart charges E300 (plus travel costs) for testing a rope, which takes two hours, and writing a report, which takes another two hours, according to Moll. Other testing agencies using this equipment include German certification bodies Tuev Nord in Hannover, Tuev Sud in Munich, DMT (Deutsche Montan Technologie) in Bochum and the certification body Det Norske Veritas (DNV)’s offices in Norway and Sweden.
The machine consists of an electromagnet that, when charged, generates an eddy current around each wire strand that passes through the sensor. Wire rope breaks show up as spikes in a plot of the signal over the length of rope. This method of magnetic testing dates back the early years of the 20th century, and has often been used for cablecar wire ropes.
The technical breakthrough over the last few years has been an improved sensitivity of the machine to enable it to be used with wire rope, according to Roland Verreet, an engineer with German vendor Wire Rope Technology. The signal strength of a break is related to the size of the wire. Cablecar wire ropes often consist of a few big strands, so it is easy to detect cable breaks. Wire ropes for lifting, on the other hand, are often made of many very small wires.
It takes a skilled engineer to be able to read a plot for breaks in a lifting rope, argues rope manufacturer Pfeifer Seil-und Hebetechnik export manager Roger Burgstall. “You have a printout, but it doesn’t mention the number of breaks. You have to be able to recognise whether a peak is a break.” Burgstall says he still favours visual inspection of ropes. “If the calculation of the crane design and running scheme and sheaves and drum and diameter ratios are okay according to the standards, then the indication of broken wires on the outside of the rope will be sufficient to know whether the rope is in good working condition or not.”
“You need a guy with a lot of experience to say what the signal is,” said Moll at the Institute. “We are doing a lot automatically, but we can’t do everything. Signals differ from wire break to wire break, and with corrosion and wear, there is no normal signal.”
To get around the problem, Ulrich Breim, research and development manager for Casar, advises customers to take early scans of the rope for comparison with measurements when the rope is operating. In fact, he advises that customers have a scan of the rope done in the workshop, even before it is reeved on the crane.
In an association going back about 10 years, Casar and the Institute of Materials Handling have collaborated on the system. Casar develops the hardware, the University the software. Both market and sell the system. During this time, they have sold about a dozen machines.
Computer software now sold with the machine checks the trace and automatically counts only the most obvious signals – the others it leaves for the operator to check. Those that the machine does check, however, it tallies up automatically, comparing this data to major standards’ wire rope discard criteria, and then pronounces a verdict on whether or not the rope needs to be changed.
He said that the system is not sensitive enough to distinguish more than one wire break if they are close together. “Therefore it is very important to see the history of the rope. If within one rope life you have had quite a few measurements, five for example, then you can see the development of degradation or the increase in the number of broken wires.” He added that the system cannot tell where in the rope a detected break is, although a prototype in testing has 64 sensors that can determine where in the rope the break is. H
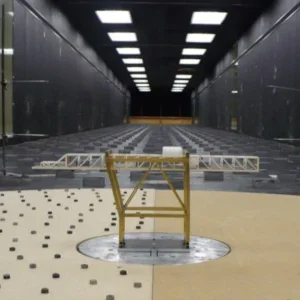