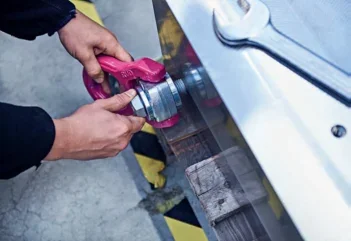
Below the hook there has to be the load. Something has to join the two of them together. If you are lucky there will be a suitable hole at a suitable point on the load in which to inset the hook. Generally, however, you are not lucky. One option is to add your own hole. In other words, you screw in some kind of lifting point.
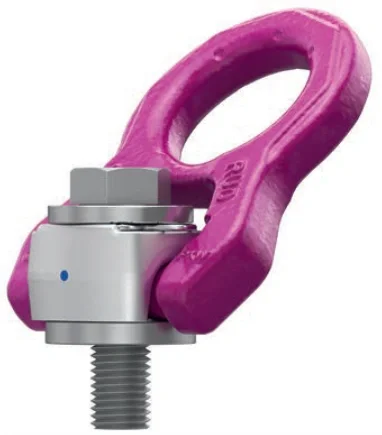
Lifting points are where load and lifting device interact. Lifting points include ring lifting lugs, eyebolts, flanges, and many others; one key to the design is that they should reduce or eliminate transverse stresses on the load. If the lift is being done from several lifting points all attached to a single main hook, then lugs attached rigidly to the load will experience a sideways pull from the shackle as well as a vertical one; and that sideways pull can stress or distort the load. A sudden drop in load is also possible, if the lifting stress makes the shackle rearrange itself on the lug.
Caldwell is reporting strong interest in its RUD ACP-Turnado lifting points which seem to be in demand. Caldwell expanded the series last year, by introducing the Max and Supermax ACP-Turnado models, designed to lift bigger loads with weight load limits up to 30% greater.
‘ACP’ stands for Automatic Center Point, which means the ACP’s lift shackle turns in the load direction automatically as soon as it is lifted, so it cannot remain in an incorrect position. Transverse stresses are reduced, and sudden drop of the load is excluded.
Robert Allen, Caldwell’s outside sales manager for the RUD product line in the U.S. and Canada, explained: “Since the ‘smart’ centric lifting point automatically turns into the correct load direction when the load is lifted, the lift bail cannot remain stationary, and a sudden drop of the load is not possible.” An innovative spring mechanism inside is what makes it happen: “The spring is the actual heart of the ACPTurnado. It provides its unique ‘intelligence’ and makes it a ‘smart’ lifting point.”
“In addition, all ACP-Turnado lifting points have a universal bolt head with internal and external hexagon, which enables optimum handling. The bolt is captive, but still replaceable, which is useful in many applications.
There is also an adapted thread length for each dimension instead of a standard thread length across several sizes. Jürgen Grubmüller, marketing director, RUD, said: “This concept allows us to offer fully customized thread types and thread sizes as well as thread lengths even in smallest batch sizes. Even customized special threads or special lengths up to 300mm are possible; this means that each of the three designs – original, Max and Supermax – is optimally matched to a defined WWL [weight load limit] range and individual requirements.”
With the line expansion, RUD now has ACP-Turnado lifting points available from M8 to M100 as well as ½ inch to 4 inch, each with the advantages of the concept.
“By offering these expanded sizes, RUD has a solution to fit a much broader range and greater variety of applications, including extreme heavy-duty use. The series can now serve an ever bigger range of projects,” said Allen.
A practical feature of the Max and Supermax versions is the deflector disc, which makes the user’s work easier. It has an angle marking, which allows a quick and simple assessment of the current stop angle. The disc also displays important information for the user such as the WLL specification in tonnes and pounds, the design factors (4:1 and 5:1), as well as the torque moment. The ACP-Turnado therefore fulfils the requirements of the American standard ASME B30.26. Another plus is that wear lenses are installed at the critical points of the power transmission, making it easy to assess whether the lifting point has reached discard maturity.
Screw-in lugs are not the only option. Clamps are another, less invasive, way of joining hook to load; they are widely used to lift metal sheets. Caldwell own the ‘Renfroe’ brand of lifting clamps. The brand has an interesting history. The Renfroe company originated in 1940 in Jacksonville, Florida, with Joseph Renfroe and his four sons. Local lore has it that Mr Renfroe Senior was a frequent riverboat gambler, and while waiting at dockyards for boats to sail started to notice the way they were being built and loaded. He thought there must be an easier way to lift sheets of steel, and so devised the plate clamp. The company has been making them ever since, and such clamps became known as ‘Renfroes’. Caldwell acquired the company in 2014 and moved all its production to its Rockford, Illinois facility.
These clamps were, and are, built to last. The company recently received a call from a user who was officially “retiring” a Renfroe Model S 12-ton clamp that has been in use since 1976, which makes a rather impressive 48 years of service. Renfroe offer a replacement parts service to extend the life of current clamps online, though whether their stock includes parts for 48-year-old models I do not know.
But Renfroe maintains another tradition, that of the printed paper Buyers Guide.
“Customers always ask for catalogues, because while some might consider it ‘old school’, they are easy to transport in their vehicles and take to jobsites,” says Doug Stitt, president, Caldwell. “Users never need a cell signal to access the Buyer’s Guide and it’s easier to compare a couple of different models just by turning the pages. It’s also easier to get a feel for the range of sizes available for each clamp.” It is reassuring to know that books written on paper are not quite dead.
Featured in the Buyer’s Guide are almost 70 of the most popular sizes and styles of Renfroe clamps, in stock every day, as well as a full list of rebuild kits. In-stock models are easily identified with a clearly marked orange label. The Renfroe 2024 Buyer’s Guide book, can be ordered from their website, it is also available as a PDF download from the same site.
Suction pads and vacuum lifters do not even need a hole, bump, flange or irregularity to lift their load. They work in fact much better on smooth surfaces that would seem to offer no purchase at all. Nevertheless, they are one of the most flexible of lifting attachments. They can lift massive concrete slabs; they can lift floppy sacks of grain or powder; sheets of glass of course are the classic application. There are even mini versions operated by AA batteries that watchmakers and modelmakers use to pick up tiny components and dropped screws. For applications where many hands would normally be required, in the form of the vacuum lifter they can allow workpieces, even heavy or awkward ones, to be handled, raised, moved and manipulated by just one person.
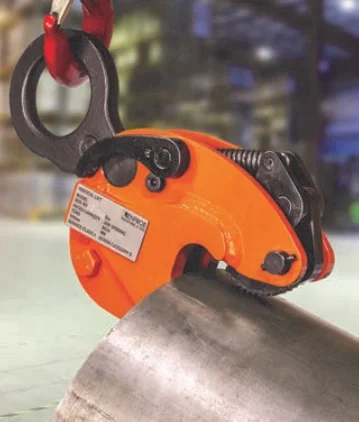
Yaplex are specialists. As they point out, vacuum devices can lift heavy loads of up to 10,000 kilograms, can be supplied to lift flat or curved products, and can be designed to handle products in both vertical and horizontal orientations. You can tilt or rotate your hanging product – tilting and rotation can be manual or powered. Energy sources are surprisingly unproblematic. Options include mains current, on-board batteries and chargers, and somewhat counter-intuitively, compressed air.
For compressed air to create a vacuum it is fed through a narrow venturi nozzle, which compresses and accelerates it; then it enters a wider space where it expands, sucking in air from a tube which is connected to the suction cap so creating a partial vacuum there. Afterwards, the compressed air and the aspirated air escape through the silencer of the venturi pump.
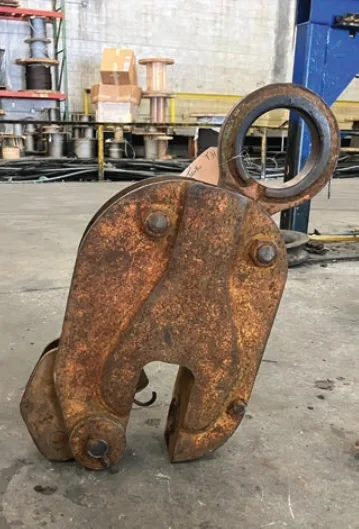
Schmalz, family-owned vacuum system specialists based in Glatten, Germany, have also what they call an eco-nozzle system, which is essentially several venturi nozzles arranged in series: the compressed air passes through several nozzles on after the other. A higher total suction rate can be achieved this way as the volumes of the individual nozzles is added up.
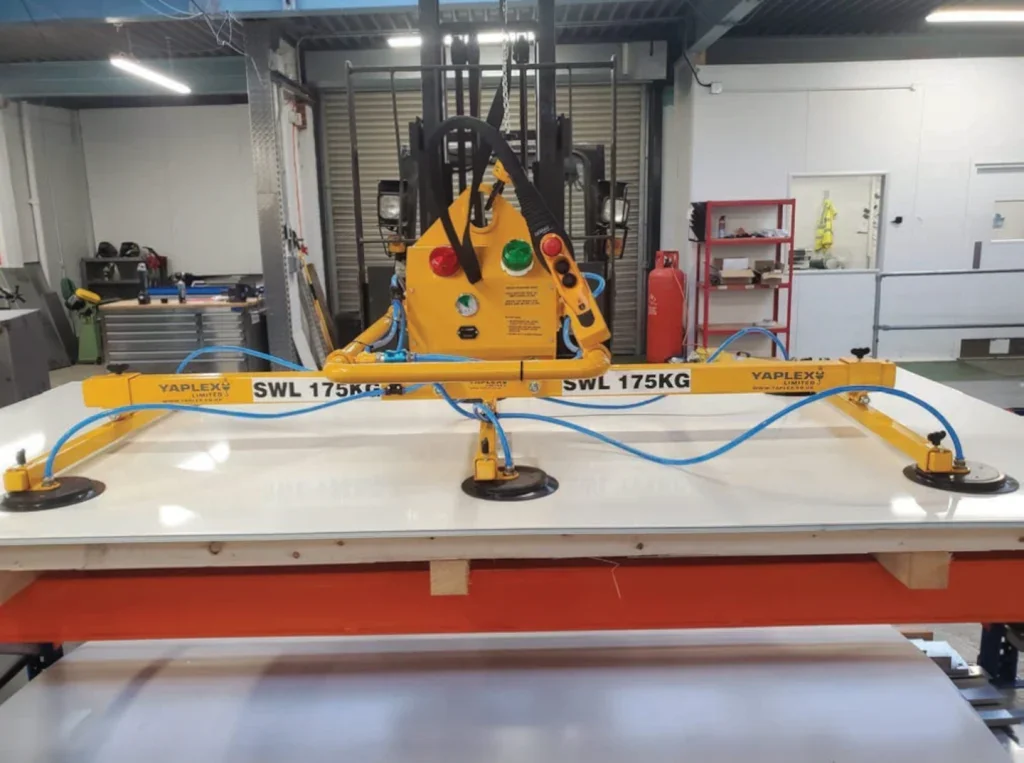
To save air and energy, the vacuum generation can be automatically halted as soon as the required degree of vacuum has been reached. The vacuum generation stays interrupted until the vacuum falls below a preset minimum value, at which point it automatically switches on again.
Its Schmalz Vacumaster is designed to be hung from overhead hoists and monorails. It’s described as the ultimate workhorse, as it can handle metal plates, wooden boards, plastic sheets, barrels, windows or glass sheets, with weights up to several tons.
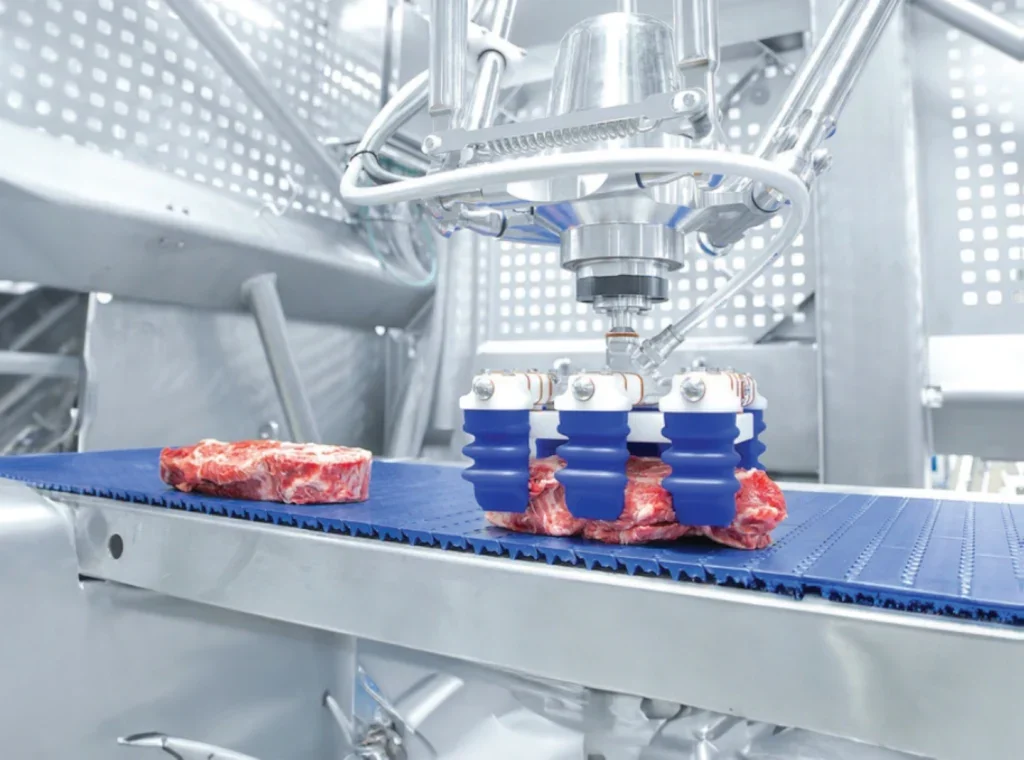
It is a modular design. Various basic units, operator handles, load beams and suction plates allow you to customize the configuration. The necessary suction force is generated by the on-board vacuum generator; suction plates – as few or as many as are required – are mounted on an aluminium load beam which, for safety purposes, is hollow and also acts as a vacuum reservoir. A chain hoist is required for lifting or lowering motion; Schmalz offers these along with a compatible crane system.
The VacuMaster Basic and VacuMaster Comfort models cover standard applications weighing up to 750 kg; the main difference is that the Comfort has the controls integrated into the handle. The Vario goes up to 2,000kg; metal plates and rotor blades are some suggested applications. There is also the Eco, an ingenious design which requires no power source at all. The vacuum is generated by the hoist’s lifting chain, which is attached to the top of a piston running vertically in a cylinder. When the hoist lifts the chain the chain lifts the piston, which moves up the cylinder generating a vacuum below it. When that vacuum is great enough to overcome the weight of the rest of the apparatus and load beneath it, the whole lot, load and all, rises into the air. Capacities range from 75 kg for the Eco75, which has just a single suction plate, right up to the one-ton eight-plate Eco 1000. Schmalz recommend a minimum workpiece weight of 10% of the lift capacity to generate the proper vacuum. Loads for the Eco should be smooth and airtight. Rough and porous loads, as we have seen, can be handled by powered vacuum lift devices.
Schmalz also offers additional lifting devices which are specially designed for the specific requirements of certain industries. It recently expanded its gripper portfolio: in August this year the familyowned company from Glatten in Germany acquired the mGrip product family from the US company Soft Robotics (SRI); the acquisition brought with it all the mGrip finger gripper configurations, patents and the associated know-how. These below-the-hook devices are especially applicable to the food industry: they are a solid and versatile option for handling delicate objects that are difficult to grip due to their changing shape. They also have high hygienic suitability, which of course is crucial for handling food products. Typical applications are the direct handling of baked good, fruit and vegetable as well as meat and fish. The mGrip products will continue to be manufactured in the existing location in Boston Massachusetts.
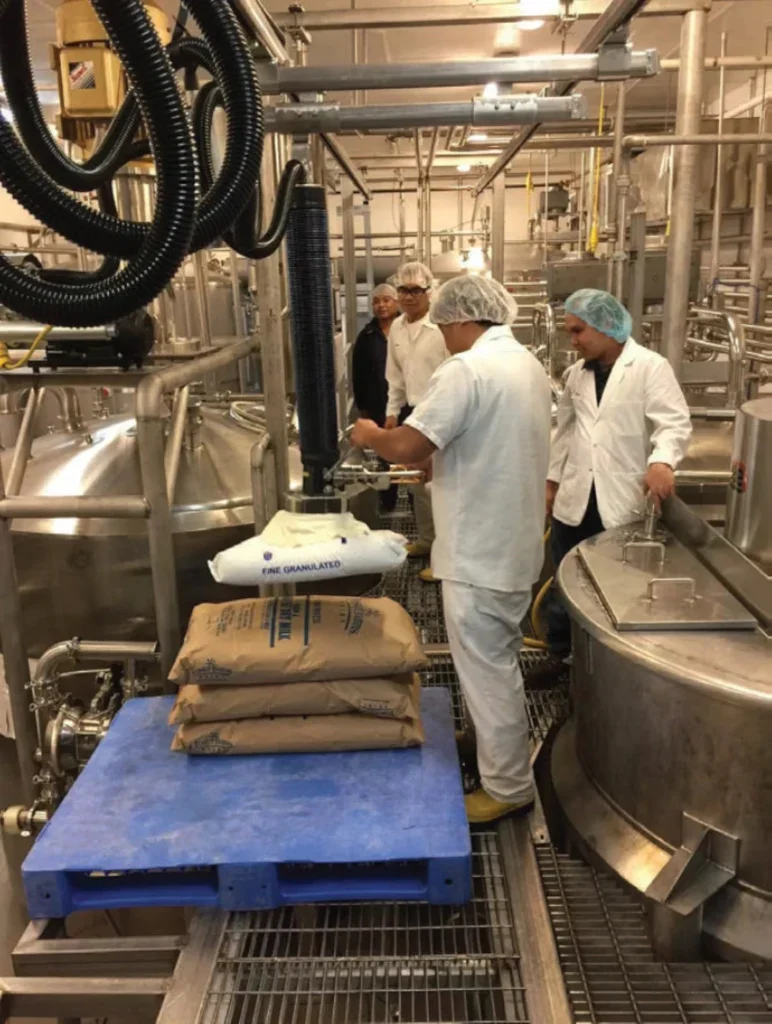
Heavy yet fragile porcelain products, like basins, toilets and bathtubs, need to be handled with care. They have no obvious lifting points, but their surfaces are usually very smooth, and of course impermeable. The application would seem tailor made for vacuum lifting: it offers the gripping ability, power to lift these objects, and the precision to handle them with care. Tawi suggests its most flexible model, the Tawi Multifunctional Lifter, for the task. It is available in several models, handling up to 270 kg. There is a wide selection of standard suction feet, and the ability to modify suction feet for individual requests, which means, say Tawi, that their lifters can grip anything you need to lift. If white goods, washing machines and the like, need to be lifted – say for packing onto pallets – the vacuum lifter can easily grip them from the top, or from the side, making lifting and loading faster and easier.
An obvious benefit is a much less physical stress on workers – health and safety, as well as common sense and common decency, require that unnecessary strain on backs, shoulders and knees should not happen. Related to that is a much more flexible labour force. Every employee, even the most frail, becomes able to handle a heavy washing machine or a bath tub; there is no more downtime waiting for someone strong enough to lift it. Work becomes much more efficient.
For high speed handling of smaller objects, Tawi’s high frequency lifter can handle loads up to 65kg. The load is lifted with just one hand on the control handle, giving the operator optimal freedom to move.
There are of course hundreds, indeed thousands, of other devices and ways to attach load to hook. The hook is sometimes all that is needed; but it is by no means the end of the story.
BRITLIFT BOLTS BEAMS
Britlift has designed a new type of lifting beam that users say represents a significant step-change for the industry. Many engineers spent their childhood immersed in Meccano (Erector sets in the US.) Pre-drilled metal components could be bolted together in uncountable different ways to make cranes, vehicles, bridges, indeed almost anything mechanical that the imagination could devise. Britlift’s new product is the Meccano of lifting beams.
As with Meccano, it consists of standardised sections and adaptors that can be bolted together as desired. They can form lifting beams (of whatever length is needed – just bolt more sections end-toend), under beams, spreader beams, H-frames, rectangular lifting frames, counterweight lifting beams, fork pocket lifting beams… need I go on? Components can be put together in whatever lengths or configurations the project needs. Assembly can be performed onsite, making it ideal for quick adjustments and last-minute changes.
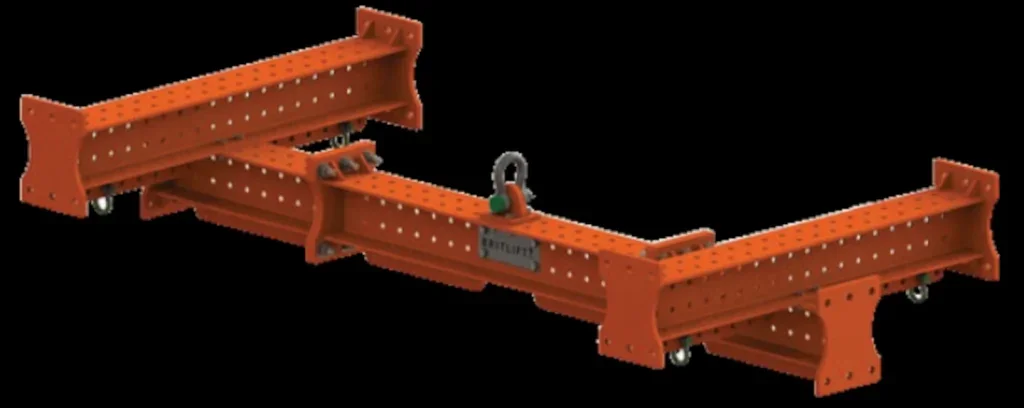
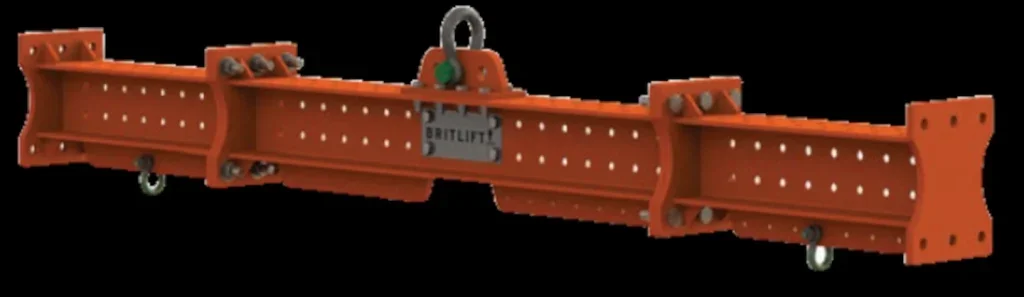
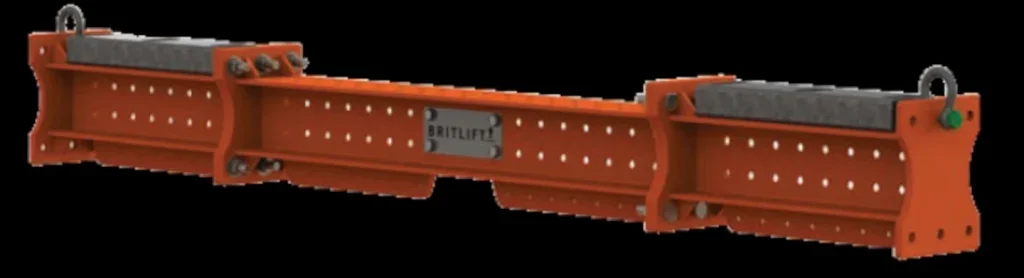
As a lifting beam or an H-frame it has a safe working load of up to 16t; as a semi-spreader, up to 23t, in which form it has a maximum span of 10 metres. SWLs vary with assembled lengths and configurations.
Warrington-based Sunbelt Rentals worked with Britlift on developing the ML180 and was so confident in the product that it placed the first order for it based only on the preliminary designs.
It has taken delivery of the first consignment and has already supplied them to some of its biggest customers. Britlift has a patent pending on the design. “The feedback we have received from our clients is impressive,” said Gary Joyice, director, Lifting, Sunbelt Rentals UK & Ireland. “One of the common challenges occurring on site is when they realise that they don’t have the right beam for a specific lift, which leads to delays while one is sourced. The Multilifter minimises this downtime because it can be quickly reconfigured.”
It has also been called the Swiss Army Knife of the lifting industry. Andy Davidson, National business development manager for Lifting at Sunbelt Rentals added: “We have already started to see enquiries coming in daily for the ML180, so we are confident it will take off.”
MODULIFT OFFSHORE ENERGY PROJECT
Specialist spreader beam manufacturer Modulift is facilitating the construction of a complex offshore energy project in the North Sea. “Princess Elisabeth” is deemed to be the world’s first artificial energy island and marks a significant milestone in renewable energy infrastructure development.
Situated 30 miles off the coast of Belgium, in the 3.5-GW Princess Elisabeth offshore wind zone, the island will act as an international energy hub to centralise all electricity produced by wind farms in the zone and will contribute to the EU’s goal of 300GW offshore wind capacity by 2050.
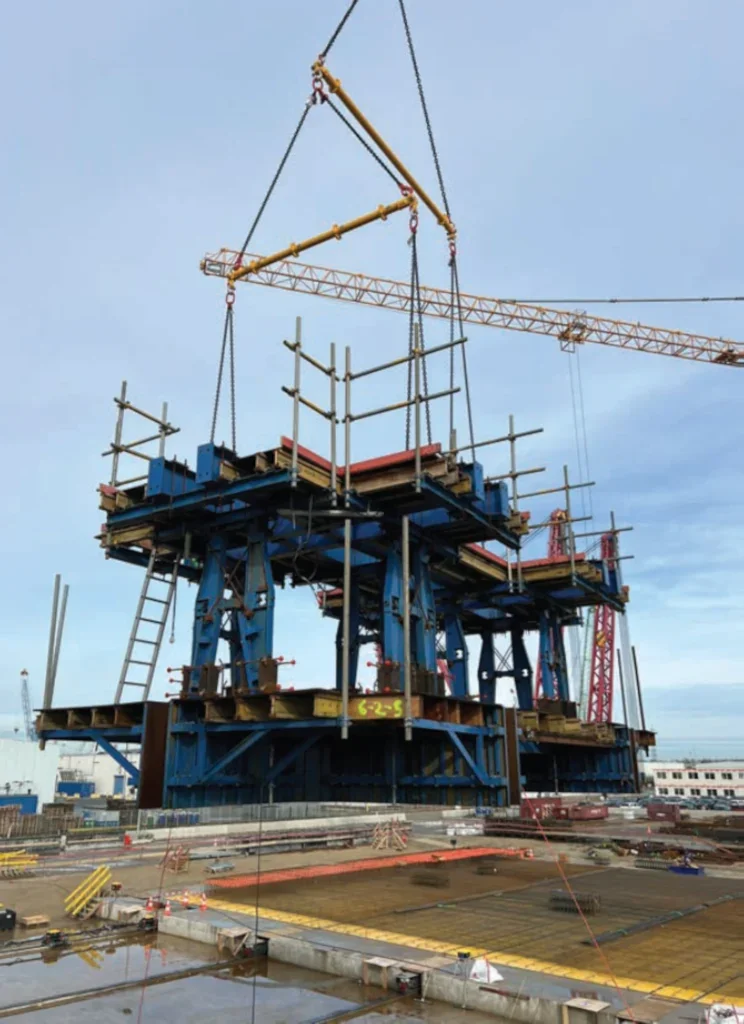
Assembling the infrastructure of the energy island requires lifting and manoeuvring large structural elements and equipment. The outer perimeter of the island will be made up of a series of concrete caissons. These are built onshore before being transported to their offshore location.
Joint venture TM Edison is responsible for construction of the island. Ruben Verschueren, their Site Superintendent of Civil Works, said “Modulift’s spreader beams have been integral to the construction of the concrete sections. Each formwork section is 10m long and weighs around 17 tons. We are using a 1-over-1 configuration, utilising an MOD 34 spreader beam at the top and an MOD 24 on the bottom. Modulift spreader beams have been instrumental in safely hoisting the formwork into position.”
The deployment shines a light on lifting equipment in such complex offshore projects, said Sarah Spivey, MD, Modulift. “Modulift is known for its iconic yellow spreader beams across the renewable and offshore energy sectors, and has set the precedent for safety, efficiency, and fast delivery in the global lifting industry. MOD spreader beams are DNV Type Approved up to 2000t and interchangeable by design, offering a reusable solution for lengthy projects. We are very proud to be part of this groundbreaking project.”
Construction of the Princess Elisabeth Island is expected to last until the end of 2026.