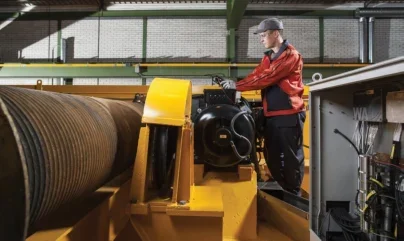
Konecranes and Demag South Africa was recently awarded a R20 million crane electrical modernisation contract for an industrial company based in southern Africa. Originally purchased from Konecranes and Demag South Africa, the crane had started to show signs of wear in mid-2024.
“At the onsite assessment, we conducted a full electrical and mechanical evaluation of the crane. This showed that the downtime and resulting breakdowns experienced by the client were a result of the age of the electrical system, which was no longer performing optimally.
We recommended that an electrical modernisation programme be undertaken,” said modernisation and sales support specialist, Alwyn Rautenbach.
The modernisation programme included the replacement of all key electrical components and reprogramming of the variable speed drives. “As we hold a large supply of mechanical and electrical components for our products at our premises, we were able to supply all of the parts required to complete the modernisation upgrade from our Johannesburg distribution centre,” said sales manager, Ian Grobler.
Components such as variable speed drives, encoders, auxiliary panels, brakes, and hoist resistors formed part of the consignment of components. Full functionality testing and a factory acceptance test were conducted before the complete electrical upgrade was delivered to site. The process took one month, with ongoing monitoring of the crane’s performance continuing for a further two months. “Despite the removal of the crane’s complete electrical system, the modernisation transition was smooth and efficiently conducted,” said Rautenbach. “We will continue to supply assistance on site and conduct unscheduled maintenance that limits downtime for the customer, while we ensure that everything in the new system is performing as it should.”
Grobler added, “The cost of maintaining crane electrical and control systems increases over time. An electrical system modernisation not only helps improve the performance of your existing equipment, it also extends the lifespan of your crane without the major capex expenditure of purchasing a new crane.” New safety features and positioning capabilities can simply replace high-maintenance, obsolete components with newer technology offering a newer, tailored and fully integrated system. We are proud to have been able to resolve the customer’s crane challenges as cost efficiently and as timeously as possible. The end result has delivered a modernised and fully operational ‘new crane’. We are also delighted to be the preferred supplier to the same customer for a further two to three electrical crane upgrades over the next two years.”
“Konecranes receives a substantial number of enquiries from clients based in southern Africa, no matter the make of the crane. Key factors in our successful resolution of any mechanical or electrical performance issue are our quick technician-to-site response time for assessment purposes, and our ability to supply spare parts and components from our distribution centre easily to site. This ensures that the refurbished crane equipment is fully operational quickly, without cutting any safety requirements,” concluded Rautenbach.
Wire ropes are part of many critical applications in mining, at ports, for crane operations, and in dredging, among other sectors. This means that the correct maintenance of wire ropes is a key component of plant operations. However, Colin Ford, MD of Lubrication Engineers (LE) South Africa says that using traditional methods can take maintenance teams hours to clean one wire rope, and even more time to apply new lubrication to that rope.
Modern lubrication equipment does a much faster and more effective job than these traditional manual methods. LE is a distributor of wire rope lubrication products from Viper, an Australian company, that significantly reduce the time required to lubricate wire ropes.
“Whenever machines using wire ropes come to a standstill, a plant loses valuable time. The Viper system helps because where it would take several people maybe two hours or three hours of scrubbing a rope to clean it – which sometimes leaves a machine like a winder rim or a shaft closed for more than a day – with Viper products, we’re able to clean and lubricate in a single pass within an hour,” said Gary Wentzel, senior technical sales representative, LE.
A Viper lubricator is a collar with seals that is strapped down and held in place so that a rope can move through it.
A wire rope cleaner can be attached to the front of the system, and this spins against the rope as it moves through it, removing old product and cleaning it. Then fresh product is applied as it moves through the rope lubricator.
The Viper lubricator comes in three different sizes to accommodate ropes from 6mm to 165mm: the mini kit ranges from 6mm to 44mm; the mid kit is from 6mm up to 67mm; and the maxi kit can handle ropes from 50mm to 165mm in diameter.
“Other products only coat the outside of a rope and seal the moisture inside the rope, which can cause corrosion. However, the Viper does more than just coat the wire rope; it lubricates it right through to the core of the rope,” says Wentzel.
Often, corrosion occurs on the inside of the rope, which is difficult to see without special equipment. An advantage with the Viper lubrication system is that as the lubricant penetrates to the core of the rope, it expels any water that could cause corrosion from the rope. Different types of greases and lubricants can be used with the Viper system, depending on the requirements for the particular application and rope being used.
Another factor is the reduced risks of this system compared to manual greasing, is It is safer for staff to use, requires smaller volumes of lubricant, and results in less leakage and mess.
Viper is becoming increasingly popular in the South African market, as operations managers see its effectiveness and the benefits of the time it saves their teams. “The interest in the market has been amazing and there has been a wide variety of people that have had interest in the Viper system,” added David Beukman, global business development manager, Viper.
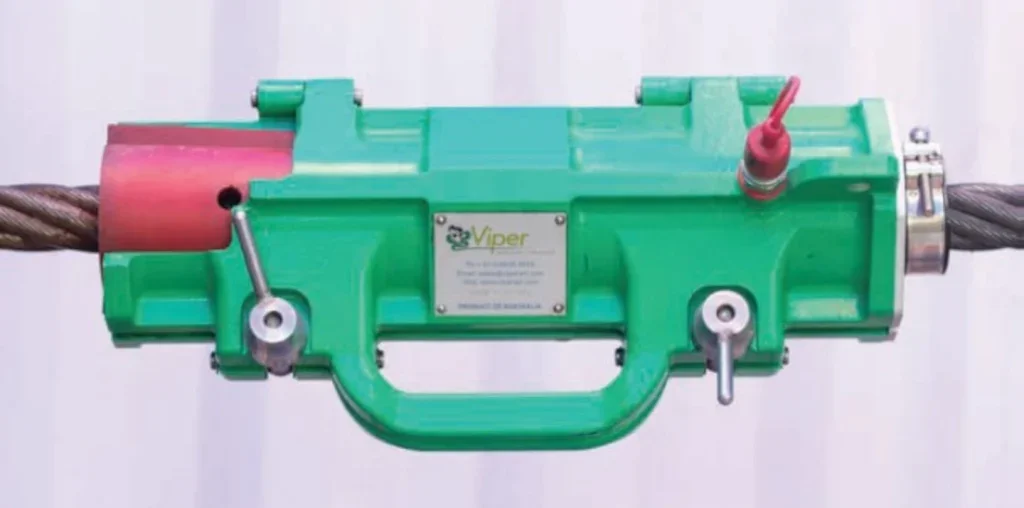
Beukman says the interest from so many different industries is also a positive indication of the potential growth in these sectors. After a difficult few years for industries like mining, sentiments are positive and the willingness to invest in products like the Viper that prolong equipment component lifespans indicate that these businesses have adapted to their current economic environment and are still looking to contribute positively to the South African economic landscape.
Lubrication Engineers (LE) South Africa represents the LE brand in South Africa, Botswana, Namibia, Mozambique, Zimbabwe and Zambia. LE hold the rights to Southern Africa on the LE brand, recognised internationally as a specialist in lubrication.
Through LE Incorporated, they are a member of a worldwide network of companies spanning Europe, South America, Asia and Africa, while LE Incorporated operates in the USA and covers North America including Canada, Mexico and the USA.
LE provides high performance, heavyduty, quality lubricants for virtually every industry and application, as well as expert technical back-up and support.
RGM CRANES: LIFTING ACROSS
BORDERS Hoist Magazine recently sat down with Alex Dowling, Group CEO and Chairman of RGM Cranes, to discuss the company’s continued growth, its technological innovations, and its role in shaping the heavy lifting industry across South Africa, Africa and the United Kingdom.
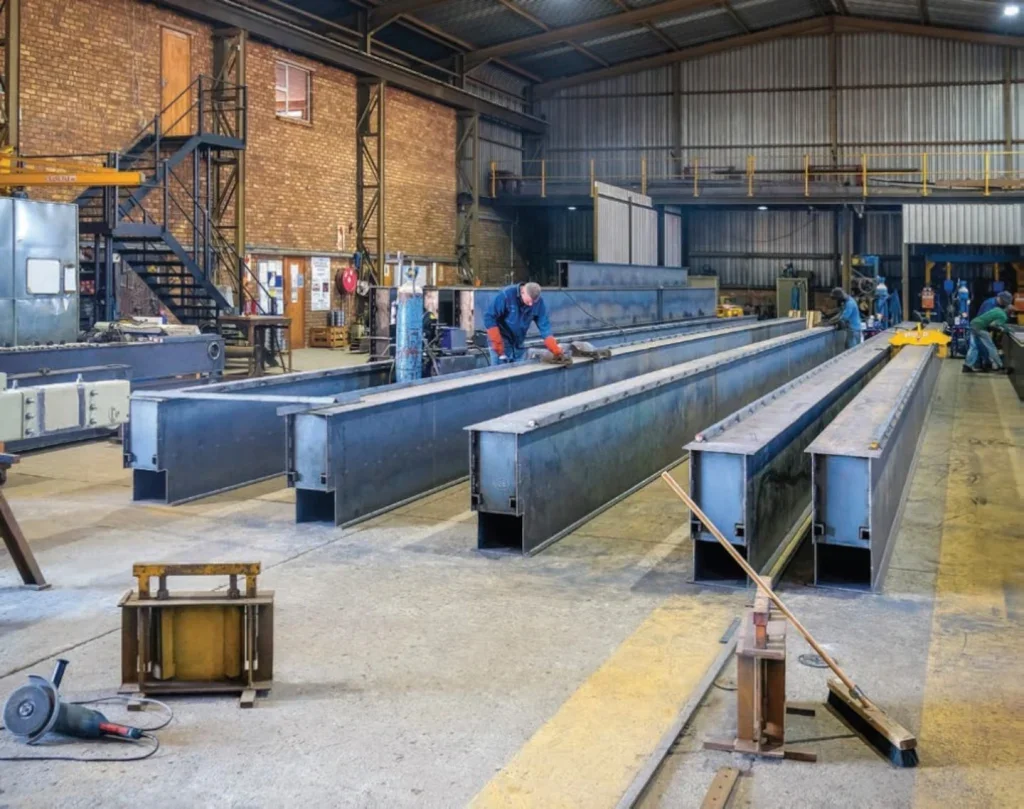
“We’ve built this company on a foundation of trust, expertise, and an unwavering commitment to our clients,” says Dowling. “Our success is driven by the dedication and skill of our team, whose expertise and passion ensure we consistently deliver exceptional results. Our mission is to not only meet industry standards but exceed them, ensuring every crane we deliver supports the critical work our clients are doing.”
Over the years, RGM Cranes has steadily expanded its presence beyond South Africa, taking on projects across the African continent and into the United Kingdom. From Namibia to Zambia, Tanzania to Botswana, Mauritius to Swaziland, and the UK, RGM Cranes has become a key player in supporting industrial growth across diverse regions.
“We don’t just deliver cranes,” Dowling explains. “We deliver solutions that empower businesses, enabling them to operate safely and efficiently in some of the most demanding environments.”
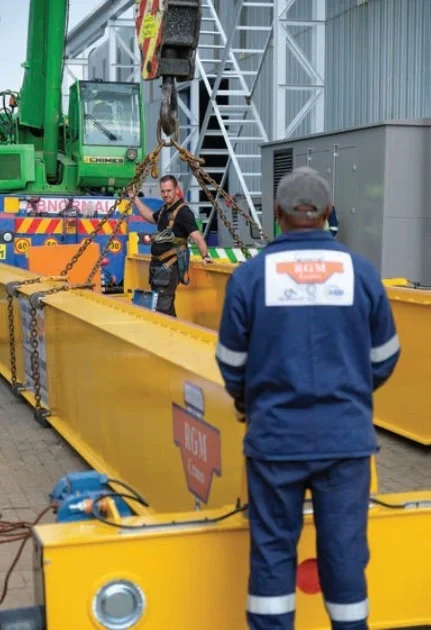
In an industry where safety, efficiency, and precision are paramount, technological innovation is not just an advantage—it’s a necessity. RGM Cranes’ development of the Nexxus platform highlights its forwardthinking approach. This cloud-based asset management system was developed to modernise crane management, operations and maintenance, replacing outdated paper-based processes with real-time digital solutions.
“We designed Nexxus to simplify crane management for our clients,” Dowling shares. “It’s not about selling a flashy product—it’s about solving real problems and making operations safer, more efficient, and easier to manage.”
Nexxus gives clients real-time access to essential information like crane expenditure, number of breakdowns, cost per breakdown, crane safety records, service certifications, and load test certifications. Its features ensure that crane management is not only efficient but also proactive, helping clients identify and address potential issues before they escalate.
Additional features include our inhouse designed crane monitoring system, which provides time- and date-stamped recordings of all crane motions, along with overload monitoring, side pull detection, and predictive maintenance alerts.
“This system eliminates the guesswork involved in calculating the life span and duty cycle of each crane currently in operation,” says Dowling. With live data and proactive notifications, Nexxus ensures that equipment remains compliant, operational, and safe.
One of the platform’s most significant advantages is its compatibility with any crane or hoist makes, making it accessible to a wide range of industries. “We wanted a solution that wasn’t limited to just RGM equipment,” says Dowling. “Nexxus is designed to benefit the industry as a whole, ensuring businesses can achieve operational excellence no matter what equipment they’re using.”
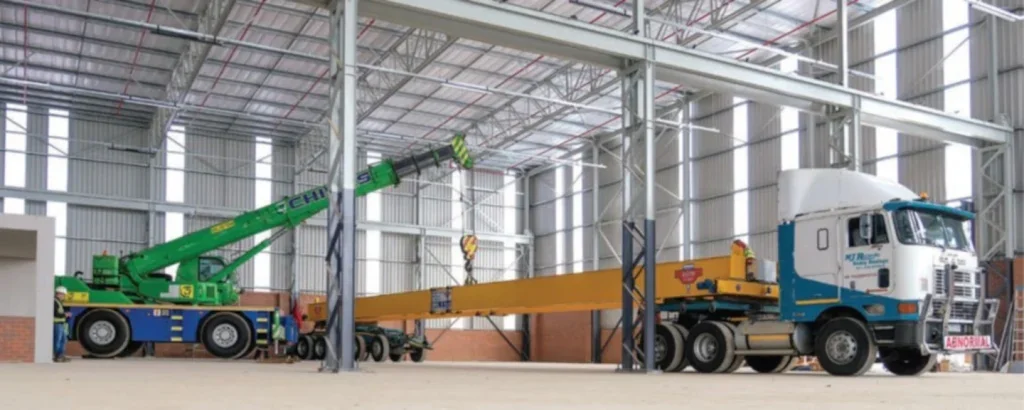
RGM Cranes’ work extends beyond delivering equipment. By providing ongoing support, including inspections and maintenance, the company helps clients maximise the lifespan and performance of their cranes.
“Safety is the cornerstone of our industry,” Dowling emphasises. “A crane is a critical asset, and its reliability can’t be left to chance. Regular maintenance, proper inspections, and proactive care are essential—not optional.”
Projects like a 25-ton double girder crane in Walvis Bay, and several cranes for Richards Bay clients reflect RGM Cranes’ ability to adapt to varied industries and operational needs. Beyond Africa, RGM Cranes has made significant inroads into the UK market, having sold 22 cranes and with several additional projects currently underway. From mining and manufacturing to logistics, the company remains a trusted partner in lifting solutions across regions.
At the core of RGM Cranes’ success is its commitment to quality. The company’s expert team works closely with clients from the initial concept stage through to design, manufacturing, and installation, ensuring that every lifting solution is tailored to meet specific needs.
“Our clients trust us because we prioritise reliability,” Dowling notes. “It’s not just about selling a product—it’s about delivering a solution that works every time.”
This dedication doesn’t end with the installation of a crane. RGM Cranes’ comprehensive after-sales support ensures that clients receive the ongoing assistance they need to maintain peak performance and compliance with safety regulations.
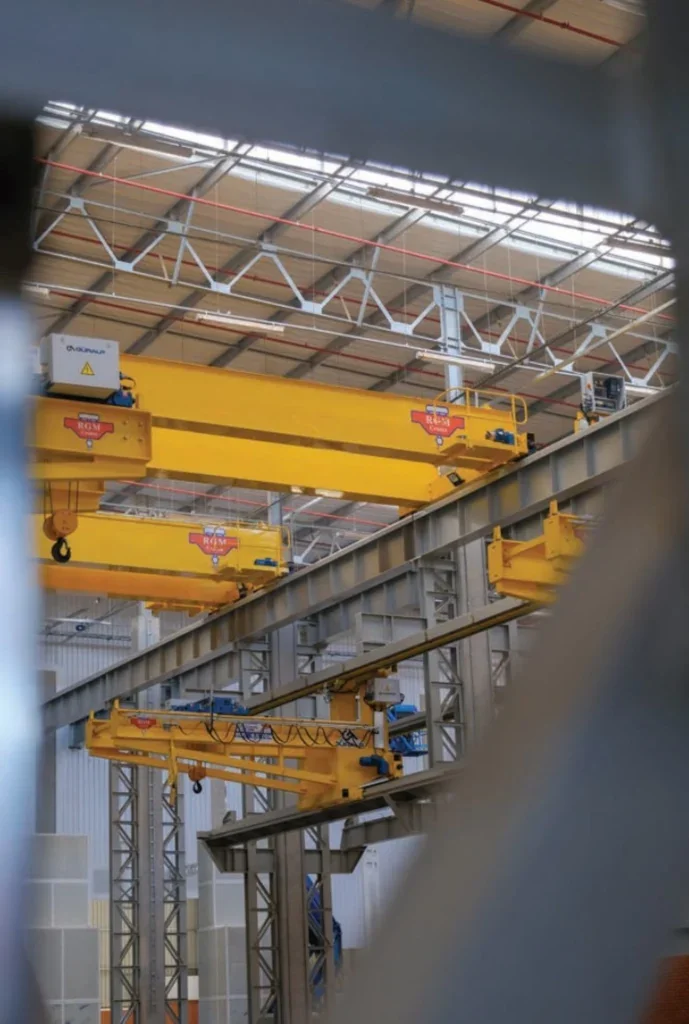
As RGM Cranes continues to expand its footprint across Africa and the United Kingdom, its mission remains clear: to deliver industry-leading lifting solutions and empower businesses with reliable, innovative technology.
Reflecting on the company’s journey, Dowling concludes, “The work we do is about more than lifting loads. It’s about lifting industries, supporting growth, and providing our clients with the tools they need to succeed. We’re proud of how far we’ve come and excited for the future we’re building—both for our company and the industries we serve.”
By focusing on quality, innovation, and customer support, RGM Cranes is not just meeting the demands of today’s industrial landscape—it’s shaping the future of heavy lifting in Africa.
In other news, BB Cranes is to manufacture its first 30-metre-span overhead crane, a record for this Cape Town-based company and the direct result of improved manufacturing capabilities and a recently expanded factory floor.
The wide-span double-girder electric overhead travelling crane is one of six ordered by boatbuilders Robertson and Caine, the largest manufacturer of catamarans in the Southern Hemisphere and the third largest globally. BB’s 30 metre span, 5-ton capacity crane is for the factory in Montague Gardens, Cape Town.
Robertson and Caine has also ordered two single-girder and two double-girder BB machines, all with 5-ton capacity.
They will span 20 metres (two cranes), 19 metres and 18 metres. The sixth crane on order is a 10-ton double-girder machine with a span of 20 metres.
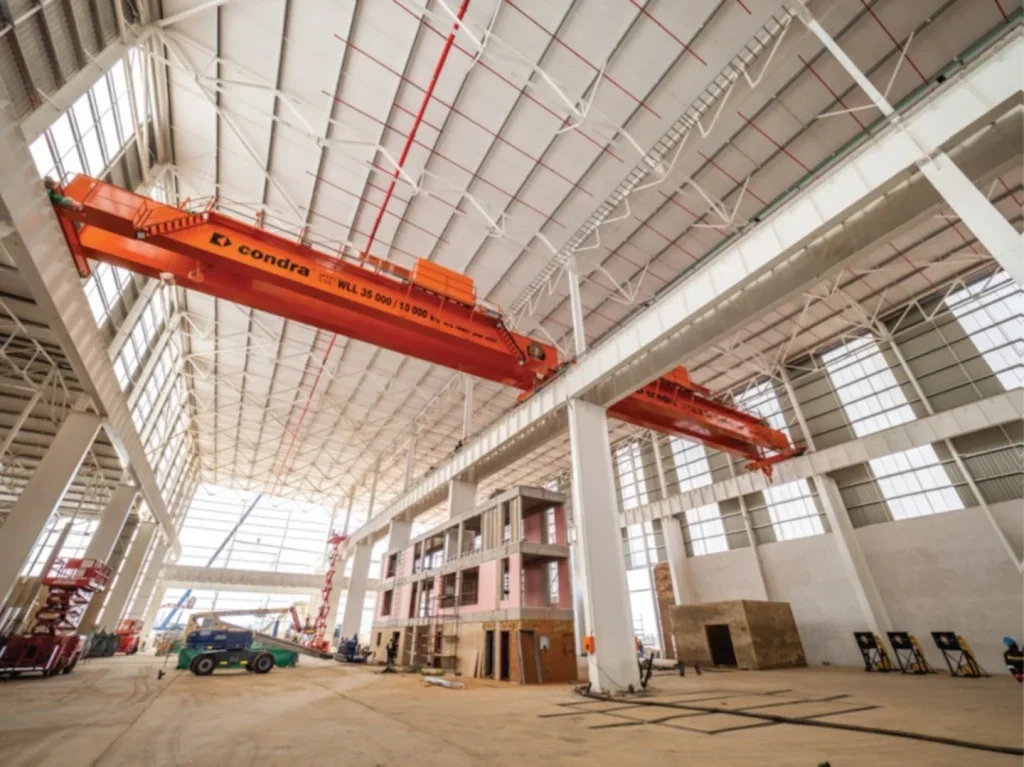
BB will assemble all six from standard components and fit them with twinned short-headroom Condra hoists – two per crane. There will be variable-speed drives on the long- and cross-travels for precise boat positioning.
A spokesman for BB Cranes said three of the six cranes would be manufactured simultaneously with two other widespan machines ordered by Rovic, an independent agricultural machinery manufacturer that commissioned three double-girder overhead cranes in the first half of 2024, two of them designed with 28-metre spans just two metres shy of BB’s new 30-metre record.
“Our crane spans are usually anything between 18 and 25 metres, so we see the 28-metre-span machines for Rovic – and especially the 30-metre span crane for Robertson and Caine – as justifying our decision to expand BB’s capabilities and increase our factory floor space,” the spokesman said.
BB has steadily upgraded its capabilities and procedures at Rivergate Industrial Park since 2022, when BB Cranes became a member of the Condra group.
In June 2024, the company increased its factory floor area by 400 square metres.
“All of these cranes represent turnkey deliveries from design through to installation. For us, they are affirmation of BB’s decision to grow,” said the spokesman.
Robertson and Caine has been BB Cranes’ customer for 20 years. Current work for the boatbuilders includes partial on-site automation of a 16-ton crane used in repetitive applications, control of which will be reduced to the single push of one button to accelerate production and improve productivity.
The BB Cranes spokesman explained that the number of enquiries for automated cranes was increasing.
“We offer automation across our product range, working in collaboration with Condra’s design office,” he said.
“Condra is accumulating automation experience and is currently automating a crane for use in wrap-and-protect operations in Gauteng. We hope to see more automated cranes among our customers here in Cape Town,” said the spokesman.
Currently equipped with eight BB cranes, Robertson and Caine’s new order will bring its total of BB machines to 14.
All six of the new cranes were delivered in November and December 2024.