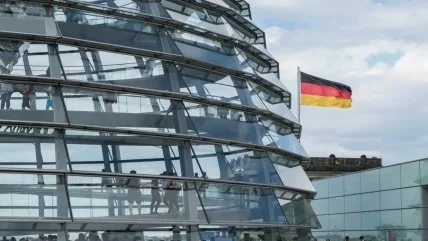
The German Government consisting of the SPD ‘Sozialdemokratische Partei Deutschlands’ (Social Democrats), Greens and FDP ‘Freie Demokratische Partei’ (Free Democratic Party) are looking to approve an EU free trade agreement with a ratification law (whereby a state indicates its consent) for CETA (Canada Comprehensive Economic and Trade Agreement).
“At last, the German government has decided to tackle the ratification process for the EU free trade agreement with Canada (CETA). Back in the spring, the Federal Constitutional Court had ruled that Germany could continue to participate in the trade agreement between the EU and Canada. The fact that the German government has nevertheless hesitated so long with ratification is all the more incomprehensible given that it sees itself in the role of European champion against the growing global protectionism from which the German export industry is increasingly suffering,” explains Ulrich Ackermann, head of the foreign trade department at VDMA (the German Mechanical Engineering Industry Association).
“The extent to which international trade is now being obstructed is emphatically demonstrated by a VDMA study on global trade barriers published recently.
“The other EU member states that have not yet ratified CETA should now also quickly make up for lost ground – not least for reasons of credibility. Because no one will still negotiate a free trade agreement with the EU in the future if its implementation is not ensured.”
Commenting on the parliamentary deliberations on the Report on Vocational Training 2022, the VDMA claims Germany’s prosperity is based above all on its strong industries such as mechanical and plant engineering but without a sufficient number of young technical specialists, Germany has no future as a location that wants to attract industry.
“Vocational guidance and technical education at schools remain weak points in the education system. It is not acceptable, as a comparison of the German federal states by the VDMA shows, that technical education continues to lead a shadowy existence in most schools. Technology must be established as a subject in all types of schools,” says Dr. Jörg Friedrich, head of the VDMA’s education department,.
“In the announced reform of the Skilled Workers Immigration Act, access to vocational training in Germany should also be made easier for young people from countries outside the EU who are capable of receiving training.
“Following the significant drop in the number of applicants for apprenticeships during the Corona pandemic, the situation on the training market for our companies is becoming even more acute. Politicians should therefore take the Report on Vocational Training 2022 as a warning signal,” he adds.
Despite skilled shortage challenges business is booming in the country, as witnessed by Demag Cranes & Components for example, which recently partnered with Wilhelm Layher & Co. to provide automation of an incoming goods and production area to process raw materials at its new plant.
The scaffolding systems manufacturer is building a production line in Güglingen- Cleebronn, Germany and awarded a contract to Demag to design and implement the corresponding automated crane, materials handling system and safety equipment.
It will install five automated process cranes to ensure tubes will be effectively stored, picked, and supplied on time with a material flow to manufacture components for scaffolding. The planned throughput for the plant is 120,000 tons per year and 25 tons per hour.
Demag is implementing a complete system solution for the ground-level and overhead material flows, including the corresponding long material store.
“We’re glad that we were able to win this very challenging contract. The complexity is the result not just of the turnkey delivery and planning scope, but also of the fact that a lot of unique requirements had to be considered during planning together with our customer Layher,” said Thomas Bönker, senior VP, process cranes, Demag.
“Thanks to this partnership, which was already initiated at an earlier stage, we were able to identify and exploit significant potential for improvements in advance.”
Layher is planning to build an independent plant in Güglingen- Cleebronn for the production and hot-dip galvanizing of parts for its all-round scaffolding system. Plant 3 will cover an area of approximately 11 hectares, of which around five will consist of roofed production and storage areas.
The production process for the entire location is scheduled to start in 2023: This means galvanizing the scaffolding elements and, depending on the specific component, the corresponding hot working, ledger welding, standard element welding, and assembly as well.
Bundles of tubes will be delivered from various production plants and then placed in Demag stacking racks at transfer stations to the inbound goods storage area.After the material data is captured by the Demag Warehouse Management System (WMS) and registered with the customer’s SAP Hana system, two Demag crane systems take care of the automated material transport operation.
To do this, the cranes, which have an 8 ton load capacity and 25 metre span, store the stacking racks until they are called up for production.
The WMS will use various parameters to determine the storage locations for the bundles of tubes, which will vary in terms of length and wall thickness. The crane systems will also take care of automated stock retrieval. To this end, the bundles of tubes will be placed on one of three conveyor lines that will then transfer the bundles to the intended production area.
In future, three additional automatic cranes with span dimensions of 11 metres and a load capacity of 8 tons will operate in the ledger-welding/cutting areas and in the hot working area. These process cranes will transport the individual bundles to the intermediate storage areas upstream of production – alternatively, they will also take care of serving individual machines with stock directly.
In addition, the Demag WMS system will incorporate and process production plans and data from the Layher quality assurance system.
In the production area, bundles of tubes will be temporarily stored on a platform above the processing machines with a planned buffer of one production day to ensure that material is supplied quickly.
The Demag WMS system will organize retrieval operations on the FIFO principle and will be able to re-organise stock to create stacks of bundles of the same type when workloads are low, for example. It will also be able to transfer material between the two bays.
In other news, Kalmar, part of Cargotec, has signed an agreement with NTB North Sea Terminal Bremerhaven & Co. to supply a further 12 hybrid Kalmar Straddle Carriers for its container terminal in Germany. Additionally, NTB has complemented its order with a batch of 15 hybrid Kalmar Straddle Carriers, booked in 2022 Q1 order intake, bringing the order to a total of 27 straddle carriers.
The delivery of both orders is scheduled to take place during 2023.
“This investment in hybrid technology will help us pave the way for a more eco-efficient future at our terminal. We are confident that the high performance of the new Kalmar Straddle Carriers will ensure our ability to continue providing excellent customer service also in the future,” said Sören Krüger, general manager, finance and administration, NTB.
NTB North Sea Terminal Bremerhaven & Co. (NTB) is one of the largest European container terminals.
It handles over 3 million TEU annually with links to 130 ports around the world. NTB serves about 45 ships per week in Bremerhaven, using six berths for large ships and a container yard of more than 1 million m2. NTB currently has nine Kalmar straddle carriers in operation.
“We are pleased to help NTB with their sustainability targets and proud to be supplying the next follow-up hybrid straddle carriers to the Port of Bremerhaven. Today, our eco-efficient straddle carriers are the choice of more and more terminals. To date, more than 400 hybrid versions have already been ordered and shipped around the world,” added Mikko Mononen, VP, sales & marketing, Kalmar.
Another milestone in the ports sector saw Liebherr present its new mobile harbour crane series LHM at TOC Europe in Rotterdam two months ago, which is more digital, more automated and has a new look.
Philipp Helberg, senior marketing manager, Liebherr Maritime Cranes, said the new features include; the crane control system, sensor technology and digital information transmission. In addition, the Liebherr hybrid system Pactronic and the driver’s cab have been improved in line with customer needs.
The Liebherr Pactronic 2.0 hybrid system represents the second generation of a hydraulic drive system using hybrid technology. An accumulator serves as an energy store and provides support when needed by supplying additional, temporarily stored power. The second generation of the Pactronic offers the operator a choice of two operating modes, depending on the current work situation.
The redesign of the LHM operator’s cab focuses on the crane operator. Thanks to the coupling of joystick and armrest, it increases driver comfort and the control of the crane becomes even more precise and safe. With the integrated touch panel, all crane functions can be selected clearly and intuitively, which simplifies the operation of the crane. A revised air-conditioning concept also increases the well-being of the operator, ensuring fogged windows are quickly dehumidified, for a clear view and more safety.
Also, at TOC Europe, Jan-Willem Schoneveld, MD, Dellner Bubenzer, Germany, showcased its ‘One Brake, One Buel’ Buel H brand series designed for wheel brakes on rail mounted cranes, where high pulling forces for mechanical wheel brakes are required.
Buel H simplifies and streamlines Dellner Bubenzer’s family of SB Brakes with a single Buel specifically engineered to suit a customer’s braking system. It includes the SB16+ Buel H1; SB23.3+ Buel H3 and SB28.5+ Buel H5 braking systems for the safest crane operations worldwide.
“We are excited about the new brakes, and the Buel design we’re showcasing here. We are promoting the fact that we have narrowed the sizes of the Buels’ down, to three sizes, from the three frame sizes, which is going to be a gamechanger in the industry, allowing customers to consolidate their sizes down, to one per unit. This is going to be something that is really instrumental in our growth, and helping our customers have commonality in the industry,” said Joel Cox, global sales director (Americas) Dellner Bubenzer, USA.
Schoneveld added: “We are doing a few new things that are exciting for this market; one brake, one Buel, means we have a standardization within the company and we are available to answer customer’s requests more rapidly.”
The company also promoted its KFB motor mounted brakes at the show, which is a spring applied safety brake, mainly used in gantry, trolley and hoisting application on harbour crane systems, in dynamic and static use at general industrial applications, in mechanical engineering, steel mills, coal mining or wind energy systems.
Finally, Columbus McKinnon Engineered Products has supplied Pfaff-silberblau BETA-EL4 series wire rope winches and associated wire rope pulley blocks to BF Engineering to enable flexible solar simulation using height-adjustable irradiation of hydrogen-powered car or truck prototypes in a climate chamber.
Specially approved, high-quality components are necessary for this application, as the technical lighting systems of the facility require special safety measures due to their high irradiance of up to 1200 W/m², their large irradiation surface and the number of water-cooled lamps.
BETA wire rope winches in accordance with DGUV V 17/18 are also suitable for applications in such test beds.
Hydrogen-powered systems are considered a clean alternative to combustion engines.
In the fuel cell, electric current is generated from hydrogen by reversing electrolysis. Hydrogen reacts with oxygen to form water, thereby generating energy.
A battery serves as a buffer or temporary storage and covers peak loads, e.g. when accelerating the vehicle. Since hydrogen is a reactive and highly volatile gas, special precautions must be taken in the test beds.
BF Engineering develops, produces and installs corresponding solar simulation systems worldwide. The objective is to expose the test specimens from the automotive sector in the prototype stage not only to climatic tests but also to the effects of global radiation with and without UV exposure. When it comes to solar simulation systems with UV or infrared light or lighting for high-speed filming, BF Engineering is at the forefront.
The solar simulation system, which can be adjusted in height via the wire rope winches, is a so-called global radiation system according to CIE 85, with spectral components according to DIN 75220 (filtered UV-B wavelengths from 280 nm to 320 nm). The entire system comprises 42 liquid-cooled metal vapour lamps with 4000 W each. The lamps are positioned in three racks, each unit being independently height-adjustable.
In addition to taking DGUV V 17/18 into account, such applications require a high product quality for the components used. That is why BF Engineering chose the Pfaff-silberblau brand BETA winches from Columbus McKinnon Engineered Products. These specially adapted winches are suitable for use in a climatic chamber with temperatures between -30 °C to +60 °C. The height adjustment movement of about 1500 mm is implemented between a working height of 4000 mm and the parking position at 5500 mm. The adjustment is used to adapt the required lighting intensity to different vehicle heights.
The BETA EL4 electric wire rope winch with a load capacity of up to 1600 kg is used in this solar simulation system to raise and lower the racks together with the large and heavy water-cooled lights.
The high quality standard of Pfaff-silberblau and the proven technology, such as the 4-wire grooved drum, enable trouble-free, safe and long-term test bed operation. Wire rope pulley blocks have been installed for redirecting the ropes.
The surface of the wire rope winch is sealed with a 2-component paint system with a thickness of at least 240 mm.
The drive and the electrical components are protected with a sealed brake according to protection class IP65. The winch has been equipped with anti-condensation heaters to effectively prevent unwanted moisture in the housing after switching off and cooling down, which could lead to leakage currents, spark-overs or short circuits.
In addition to the lighting system, the entire package of services provided by BF Engineering also includes the electronic components for power distribution mounted outside the climate cell, the control system including the software, as well as the entire cabling, commissioning and training during handover to the test bed operator. BF Engineering has placed its trust in the quality of Pfaff-silberblau products for many years.