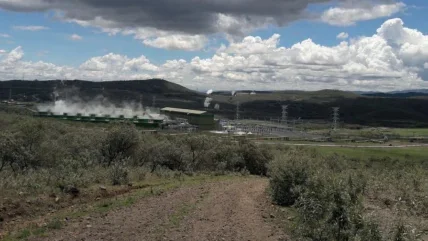
Wind used to be considered the most promising of renewables. That is perhaps outmoded now: the promise has been delivered upon. Around 7.8% of the world’s electricity became wind in 2023 and capacity is growing and expected to continue to grow: that percentage is expected to quadruple by mid-century. Of all the renewables it is one of the fastest-growing.
Wind turbines have some obvious and special characteristics. One of them is height. The hub height of towers of onshore wind turbines stood at around 80m a decade ago but the latest installations are 103m high, and designs for 150m hub heights are on the drawing board for nearfuture construction. Offshore towers are higher still, by a factor of 1.5 or more.
Reaching the turbines at the top of those towers therefore presents a problem. They need maintenance and occasional repair; service personnel need to be lifted up to the nacelles; so too do replacement parts, throughout the lifetime of the turbine. The solution is to have winches permanently housed in the nacelles; and those winches need special characteristics.
Prime among these, of course, is very high lift heights – so large drums, or capacious chain containers, to accommodate long lengths of rope or chain are incorporated.
Lifting to such heights takes time: so, the ability to run for considerable periods without interruption is also a requirement. Many manufacturers have produced or adapted their models for exactly that purpose.
Columbus McKinnon, for example, has its CM Lodestar and Shopstar hoists for standard applications. It also has ‘Wind Editions’ of both of these which have been remodelled specifically for use as service and maintenance hoists for wind turbines. Lift heights exceed 300 feet (91 metres). Both are designed to withstand the application and environment, and both can lift parts and equipment from the ground to the nacelle with no interruption and minimal chain vibration, says CMCO.
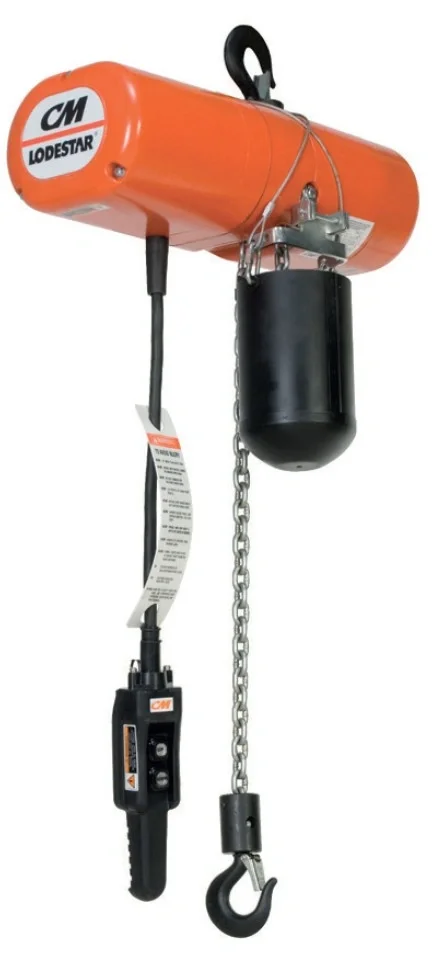
Coffing is one of the Columbus McKinnon brands, and Coffing EC-HL Models are designed to exceed the requirements needed for the exceptional lifting ranges for wind turbine maintenance. They have a specially designed motor configuration that allows the unit to lift 100% of capacity at the extended run times needed to cover the height of the tower.
GIS has its GPW electric chain hoists for wind power plants. Lifting speeds are up to 16m/min and lifting heights up to 200m.
There is temperature monitoring with shutdown function of the motor in case of overheating. A geared limit switch automatically switches to low lifting speed as the load reaches the gondola.
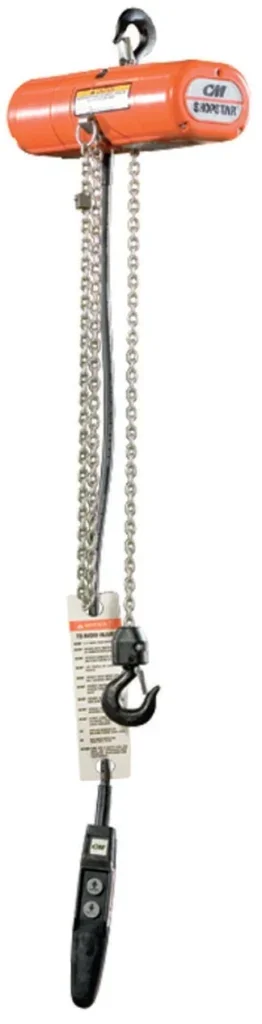
Demag’s DC-Wind chain hoists are used for the maintenance and service of wind turbines all over the world in both onshore and offshore applications Offshore installations face much harsher environments – corrosion in particular, but stormforce winds, isolation and inaccessibility are other factors; reaching even the base of the monopile can be expensive and problematic in good weather, and next to impossible in some seasons of the year.
Operators will want to keep routine maintenance of ancillary equipment to a minimum, and yet offshore cranes are worked very seldom. They must start and perform at top efficiency even after months or years of standing idle.
Demag’s DC-Wind units are intended for such adverse conditions. The gearbox and the slipping clutch of Demag’s machines are designed to be maintenance-free for up to 10 years; and components are selected to meet the needs of different climate zones. They can transport loads and tools weighing up to 1,500 kg to heights of up to 180 metres.
Demag also has the DS10-Wind rope winch. This is a multilayer drum machine with high lifting speeds of up to 48m/min capable of raising loads up to 1,000kg.
Space within a nacelle is extremely limited, so this is a low-headroom design. It can be mounted on an overhead monorail for transporting components around the interior of the nacelle.
Liftket supplies wind turbine winches for different load capacities and lifting heights. It has, for example, a winch designed for a lifting height of 200 m with load capacity of 800 kg and lifting speed of 20 m/min.
But these are far from the limits. Depending on the requirements, lifting heights of up to 250 m can be served and lifting capacities of several tons can be realised with products from Liftket while still remaining within the compact dimensions needed for the confined spaces of nacelles.
Liftket provides a ‘plug and play’ solution for simplified installation. The prefabricated installation solution can be used worldwide as it is designed for voltage levels from 110 to 690 V and for 50 or 60 Hz.
Since enormous heights sometimes have to be overcome Liftket also supplies solutions with radio remote control with several transmitters to reduce waiting times and thus also costs. Lifts can be performed within the hollow monopile tower.
In order not to damage the inside of the tower during the lift by the load hook, an electric chain hoist for wind power applications is equipped with a rubber sleeve.
As well as serving the onshore sector Liftket offers solutions for offshore plants. The main difference is that product requirements offshore are much higher. Conditions, as we have said, are rough, and strains are heavy. Alternative paints and materials may have to be used. For such applications Liftket products can be equipped with stainless steel chain and hooks, for example, so that no corrosion can occur.
Wind of course is not the only source of renewable energy. Hydro power (usually, but not always) requires large dams in environmentally sensitive areas.
Solar currently supplies some 4.5% of the world’s energy and remains the third largest renewable electricity technology behind hydropower and wind.
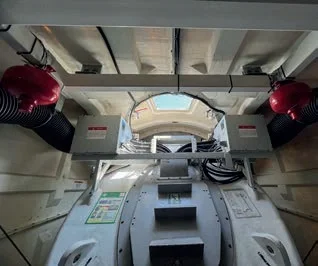
In the US, the updated Western Solar Plan targets 31 million acres (12.5 million Ha) for solar development; 428 gigawatts of solar capacity was installed last year.
Solar presents no particular lifting challenges, which may be an advantage to those developing it but limits the space we need devote to it in these pages.
Geothermal power does require more heavy lifting machinery. It has a surprisingly long history. The Romans used it – not just to supply hot water for their baths, (as for example at Bath in Somerset) but also for space heating.
A geothermal electricity generating station was built in Italy in 1911. Unlike wind and solar energy, geothermal plants produce power at a constant rate regardless of weather or season. Capital construction costs are considerable, but running costs of an established plant are minimal: the US Department of Energy estimates that electricity from modern geothermal plants would cost around 5 cents per kilowatt hour.
Thermal plants depend on the working fluid – steam or hot water – having a high temperature. This has restricted geothermal power to areas of high geological activity such as Iceland, parts of the US west coast, and the East African Rift Valley (see box); but deep drilling to reach hotter rocks, around 3km down, – depths that the oil industry is well used to exploiting – help circumvent this problem.
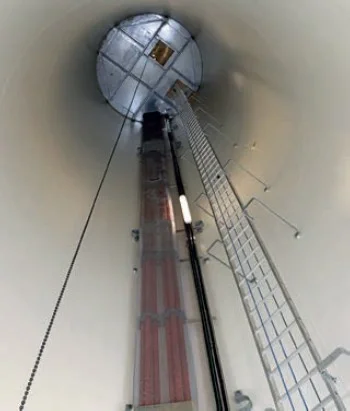
So too does the so called ‘binary cycle’, a plant design that usefully exploits water at temperatures as low as 57°C and may make it economic for many more locations. Geothermal power may well have an increasing future.
However, the sustainable energy sources of the future may divide themselves out, hoists and lifting gear will be needed for them.
DEMAG HOISTS OPERATE HYDRO BEAMS
The Albbruck-Dogern run-of-river power plant on the High Rhine is a hydroelectric power plant, located right on the German-Swiss border. Rather than a high retaining dam to accumulate potential energy in the water retained behind it, it uses the slope and the kinetic energy of the river to generate environmentally friendly renewable energy. Along with a weir power plant built later, the operator Schluchseewerk generates an annual average of 650 million kilowatt hours of CO2-free electricity at this site to supply 180,000 households.
The water volumes required for the power plant are supplied through a weir channel. Three machine sets, each of a generator and turbine, are installed in the power plant channel. To allow regular inspection work on the turbines they can be sealed off from the water with the help of the dam beams and emptied. For this purpose, the 11-metre-long dam beams are lowered into niches provided for them.
Previously, these beams had been lowered and raised by a doublegirder overhead travelling crane; after several decades this was long overdue an extensive renovation. In the upgrade, Demag DH hoist units play a central role.
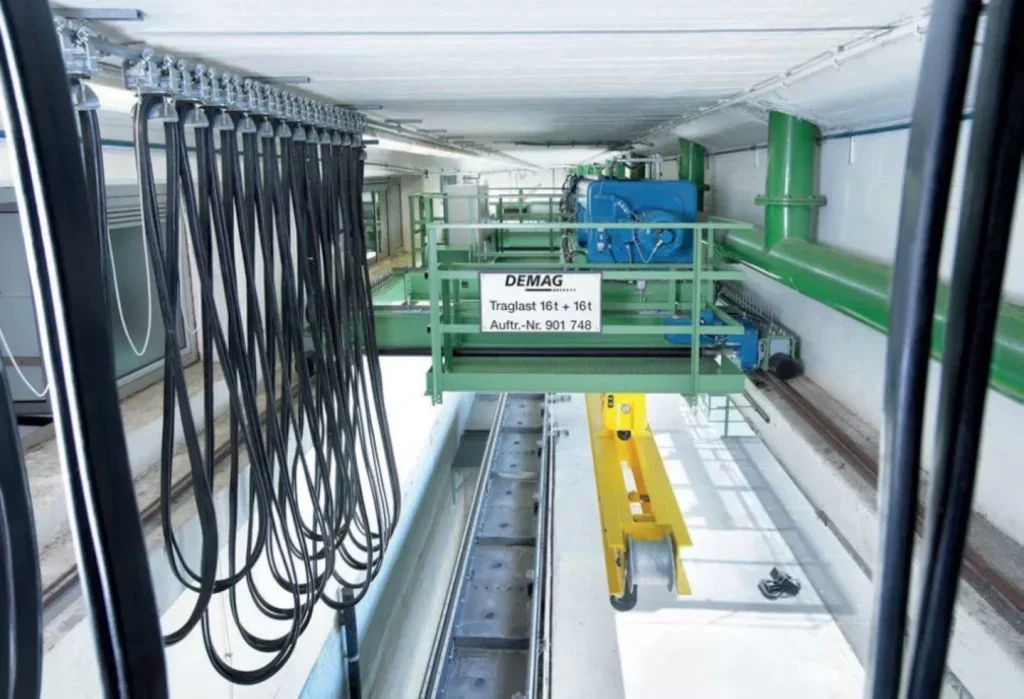
The requirements for the lifting concept were clearly defined.
They were the complete replacement of the moving steel structural elements and the load bar; installation of two 16-ton hoist trolleys, which can also operate in tandem; and safety control. Precise positioning was needed, given by frequency-controlled drives in three axes. The drive concept was eight driven crane wheels and four trolley drives. Secure year-round operation was a necessity; so heated electric switchgear cabinets were installed.
Positioning and removing the dam beams at depths of up to 22 metres requires high positioning accuracy. Two 20-ton DH 2100 hoist units with a 4/2 reeving system prevent any hook travel. They are installed on two mechanically coupled trolleys that travel with a span of 3.54 metres on an 80-metre-long crane runway. By means of a selector switch on the pendant controller the hoist units can be used individually or in tandem for loads weighing up to 32 tons. Both trolleys have a hook lead-off of 7 metres to secure the load bar for mounting the dam beams.
Further safety functions such as overload protection with summated load cut-off and a load spectrum recorder are integrated into the hoist units. An additional technical feature makes it easier for the crane operator to position a dam beam precisely: the length of the hook path is measured via rotary encoders on the hoist units and shown on large pivoting displays on the crane bridge. Personnel are thus shown the deposit position of a dam beam with centimetre precision, which can be documented and precisely controlled for subsequent removal. Two additional large displays show the current weight held by the hoist units.
The operator Schluchseewerk also uses the hoist units to transport people to carry out inspection and maintenance. The two DH hoist units were therefore equipped with a second brake as a holding brake for this purpose. Their functioning can be checked via an additional button integrated into the ground control panel. A test function for the emergency limit switch and a tare button have also been integrated into the control unit.
A total of eight travel unit combinations from the Demag modular drive system are used for the drives used for long-travel motions. Wheel blocks with 160 mm travel wheel diameters supply cross travel and are driven in pairs. Control for variable-speed travel and hoist operation is provided by Demag Dedrive Compact frequency inverters.
Year-round operation must be ensured. Although the crane installation runs under a concrete roof protected against precipitation, the equipment is exposed to outdoor temperatures through the side opening along the length of the crane runway. The trolleys are therefore equipped with additional heaters for the switchgear cabinets. The region experiences cold winters, so the electronics are optimally protected against these weather conditions.
The power supply system also took account of the effects of the weather and the confined space conditions: the track profile for guiding the trailing cable runs along the 80-metre-long crane runway and then at a right angle at the end of the runway. With this spacesaving solution, the cable accumulating section is located at the end position of the crane and the crane maintains the best possible approach dimensions. The solution is an ingenious lifting concept for generating natural electricity in southern Germany.
ELECTROMECH AT GEOTHERMAL POWER PLANT
The Olkaria Geothermal Station in Hell’s Gate National Park in Kenya’s Rift Valley is the first of its kind in Africa. It was established in 1981 and generates geothermal power from underneath Hell’s Gate from the area’s hot springs and geysers. It is one of the seven sectors of the Greater Olkaria geothermal area in the central part of the Rift Valley in Kenya.
To tap these huge energy resources, three more geothermal stations were added over the years. Subsequently, a fifth geothermal station in was planned and execution began soon after. The Olkaria V project was for a 2 x 70MW geothermal power plant.
To produce power from geothermal energy, wells are dug a mile deep into underground reservoirs to access the steam and hot water there, which is used to drive turbines for generating electricity.
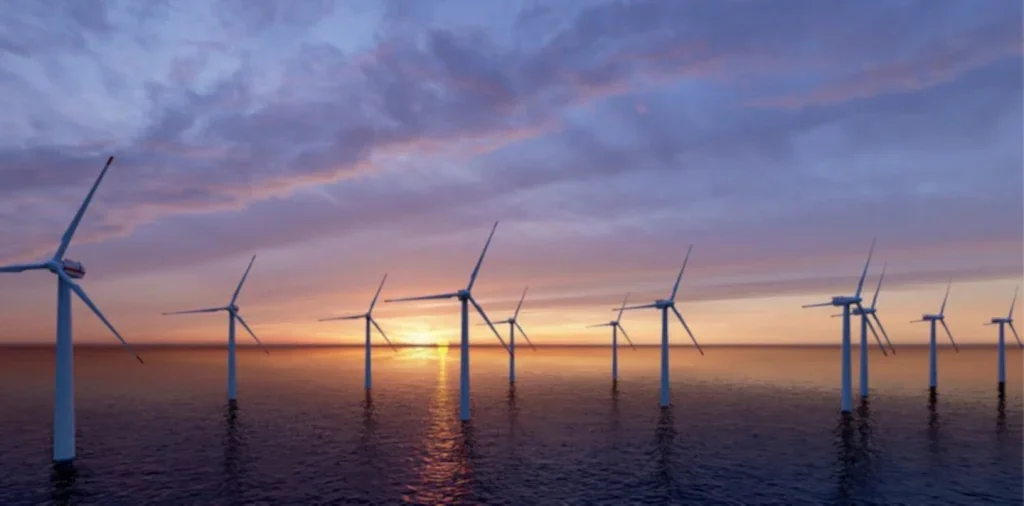
The ready availability of steam makes geothermal power plants less complex to construct than standard thermal power plants, and they require less equipment. The Turbine Generator (TG) is the most critical and important component in such plants and its perfect alignment is extremely important for the desired performance. In handling such a heavy and precision-manufactured turbine during its installation, special care is needed. This calls for a specially developed handling system which can offer excellent manoeuvrability and ensure high level of safety.
At Olkaria-V the turbine along with other auxiliary components weighed approximately 55t. The customer was looking for a suitably designed crane for the TG Hall which would offer the needed manoeuvrability and safety. The crane was required mainly to handle the turbine and other components during installation. After the commissioning of the plant, during routine maintenance operations, the turbine casing and rotor are required to be lifted, removed and refitted, for which the same cranes would be used.
Another challenge in this case was the presence of hydrogen sulphide gas in the atmosphere, which is a peculiar feature almost every geothermal plant. All the electricals require special insulation and other equipment require special care for corrosion resistance in such plants. The Olkaria-V geothermal plant is situated at an altitude of nearly 2000m, which meant that the selection of appropriate motors while designing the lifting equipment was important.
There was also a requirement for a smaller capacity crane in an adjacent bay for handling other aggregates such as absorber pumps, compressors, etc.
The material handling solution for the requirements at came in the form of a double girder crane with several specialised features.
The 65/20t capacity double girder crane has a main hoist of 65t and an auxiliary hoist of 20t fitted with encoders on the motor shafts for continuous feedback. The crane has an anti-fall feature which is automatically activated in case of a brake failure and avoids sudden freefall of the load. The crane is also provided with a load limiter and a load summation device.
In the adjacent bay another single girder crane of 10 tons has been provided for handling smaller components. Both cranes are provided with features to cater for the atmospheric conditions. Instead of the standard PVC cables, PE (Polyethylene) cables are used. PE cables demonstrate excellent resistance to corrosion and to abrasion; they have good quality insulation and can withstand temperatures from minus 55°C to 600°C. Special cable plans made of brass are used instead of rubber glands.
The stainless steel electrical panel is designed as per IP 65 and the motor covers are also of stainless steel to avoid external damage. The bus bars of both cranes are copper conductors with stainless steel strips. Powder coated accessories are used for higher corrosion resistance.
LIFT WEIGHT, SAVE ENERGY
Gravity batteries are a technology that may ride to the rescue of intermittent renewable sources. Hoists are central to the system.
One of the major bottlenecks in the transition to sustainable energy is storage. Solar and wind supply electricity intermittently. The first of course produces only during the daytime; the second is strongly dependent on the weather.
Storing energy in conventional chemical batteries is problematic. Lithium-ion technology is at present the most widely used for large-scale storage (as well as for cell-phones and the like); but it is expensive, and mining lithium and rare earths used in other types of battery can be environmentally destructive. Stored hydrogen is an alternative that is being considered: peak-generated electricity is passed through water to split it into hydrogen and oxygen; the hydrogen is compressed and stored under 200 atmospheres pressure, in lined underground rock shafts, to be used as emissionsfree fuel when needed. Several companies are working on the technology.
Gravity storage is another developing technology. It is in principle very simple: electricity at a time of surplus is used to lift a heavy weight; at time of peak demand the weight is allowed to fall slowly, generating electricity as it does so. Such systems using pumped water as the weight are well-established.
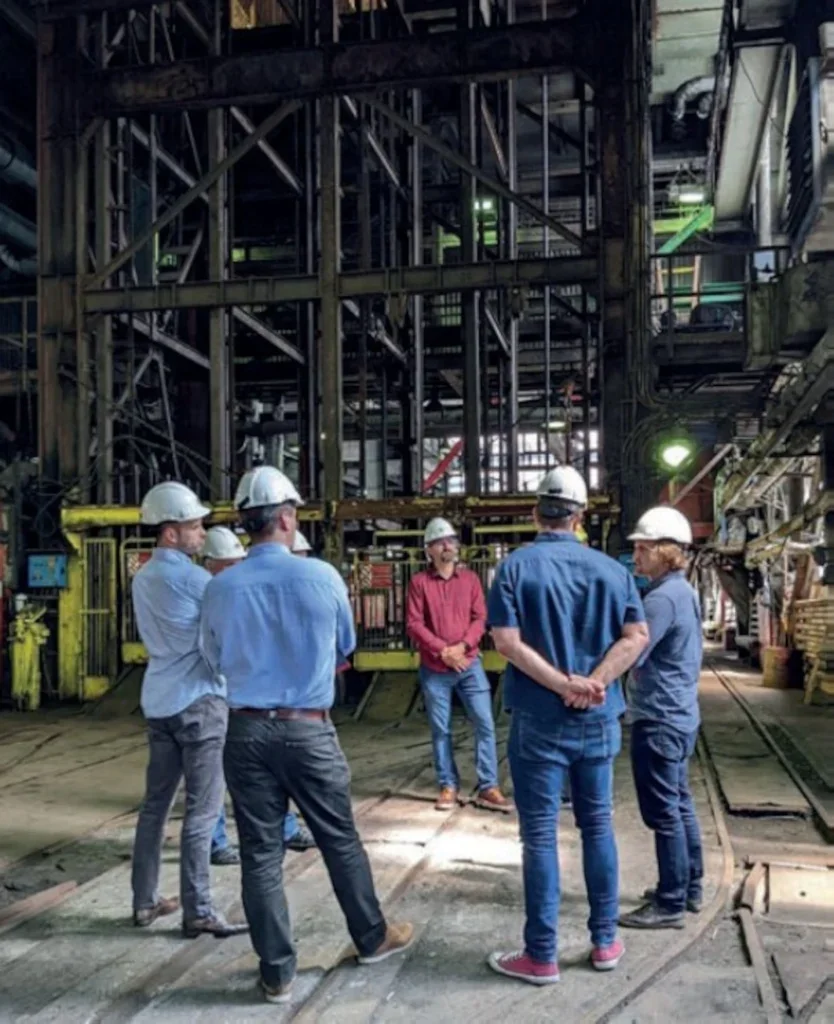
Dinorwig, in North Wales, began operating in 1984. Its six turbines give an installed capacity of 1800 MW, capable of very rapid response and drawn on at times of peak demand. Pumped hydro currently makes up more than 94% of world power storage. It is generally limited to areas that have high mountains and plentiful water. Recent interest has focused on using not water but solid weights as the storage element; they are raised and lowered either inside speciallyconstructed buildings, or up and down repurposed mineshafts.
The latter method offers greater available heights of rise and fall, and hence greater energy storage. Exhausted deep mineshafts are present in many locations, often close to large centres of population. The technology obviously depends on the hoists that are used to raise and lower the weights. Here hoist technology can prove itself central to the transition to sustainable energy. The same hoist that uses electricity to raise the weight simply operates in reverse to generate electricity when turned by the weight of the load, and that electricity is fed back into the grid. Efficiencies of 75-80% can be achieved, which is greater even than pumped hydro’s 70-75%; and, unlike with conventional chemical batteries, there is no gradual leakage of stored energy over time, and gravity batteries can operate for decades without any loss of performance.
A leading company in developing gravity storage is UKbased Gravitricity. During 2021 they successfully constructed, commissioned, and operated a 250kW, grid-connected gravity energy storage demonstration project using a 15-metre-high rig at the Port of Leith, Edinburgh. The demonstrator used two 25-ton weights suspended by steel cables from a standard hoist by Huisman.
Since then they have progressed further. In December 2023, Gravitricity signed an agreement with Swiss mining technology company ABB to accelerate the development of the system towards commercial adoption in former mines. Called GraviStore, the aim is to store more than 20MWh, in systems that offer some of the best characteristics of lithium-ion batteries and pumped hydro storage.
ABB is a market leader for mine hoists, with an installed base of more than 1,000 hoist solutions worldwide. ABB will collaborate by providing research and development, product development and engineering teams specializing in the design, engineering and operations of mine hoists for gravity batteries and mechanical, electrical and control technologies for hoisting.
The aim of commercialising the technology is bearing fruit. In February this year Gravitricity inked a deal to install its gravity energy storage system in a 1,444-metre deep mine near the Finnish community of Pyhäjärvi, 450 kilometres north of Helsinki. A 530-metre deep auxiliary shaft is to be transformed into a 2MW capacity prototype of Gravitricity’s technology. It will be the first commercial use of the system in Europe.
“As the world generates more electricity from intermittent renewable energy sources, there is a growing need for technologies which can capture and store energy during periods of low demand and release it rapidly when required,” said Martin Wright, Gravitricity’s co-founder and executive chairman. “Our GraviStore underground gravity energy storage uses the force of gravity to offer some of the best characteristics of lithium-ion batteries and pumped hydro storage – at low cost, and without the need for any rare earth metals.”
By repurposing disused mine shafts for energy storage, mine shafts can fill a productive function for up to 50 years beyond their original lifetime, and can mitigate decommissioning costs, while simultaneously creating new job opportunities and contributing to the green energy transition.
“We are already seeing significant interest from mine operators in Europe, India and Australia and this partnership with ABB – with decades of electrification and mine hoist system expertise – will help us accelerate our ambitious commercialization plans. I am delighted we are working in tandem.”
The teams will work together on feasibility studies to understand the application of existing hoisting technology in gravity energy stores. ABB will also offer mining industry consultation and work to identify suitable sites and shafts for the deployment of GraviStore.