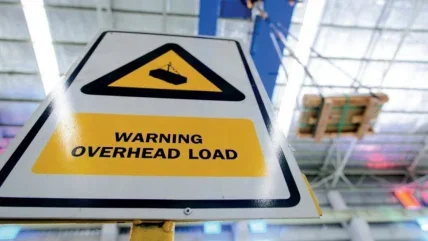
Highlighted are four deaths that occurred in the United States in 2023 that were reported and investigated by OSHA, the Occupational Safety and Health Administration. There are others to chose from; I have not included all from that period. Similar accidents occur in the UK.
Readers, with the benefits of hindsight, will have no difficulty in identifying the causes of those accidents, and in working out what should have been done to prevent them. Inadequately secured loads featured in two of the cases. (Note that in the first case lifting points were not secured to the major part of the load). Bad operator practice would seem to be present in most or all of the cases: whether training was at fault, or simply lack of attention to best practice, we cannot say. Every one of these deaths seems, again with hindsight, to have been avoidable.
Lifting heavy objects is inherently dangerous. Sound technology, used with best practice and with proper training, can reduce those dangers. Regulations and regulatory bodies, such as ASME and OSHA in the United States provide guidance.
The definitive source documents for hoist safety in the US are ANSI/ ASME standards B30.16 and B30.21, and publications available from the Hoist Manufacturers Institute (HMI). [To obtain copies contact ASME at 800-843-2763 or visit . HMI is at 704-676- 1190 or at ]
In the UK, the equivalent body is the Health and Safety Executive [HSE] and PUWER [Provision and Use of Work Equipment Regulations 1998,] and LOLER [Lifting Operations and Lifting Equipment Regulations 1998.
Industry bodies such as the HMI (Hoist Manufacturers Institute) also offer guidance in the form of publications, webinars, pre-inspection checklists, and online resources – see for example MHI’S ‘Hoist Safety Guidelines to protect your Operation’.
Manufacturers also offer guidance. The instruction manuals that accompany new equipment are of course essential reading for any user; but as Harrington Hoists so accurately point out, the operation of a hoist involves more than activating its controls. ‘As stated in the ANSI/ASME B30 standards, the use of a hoist is subject to certain hazards that cannot be mitigated by engineered features, but only by the exercise of: intelligence, care, common sense and experience in anticipating the effects and results of activating the hoist’s controls’ they say. Notably, that warning accompanies the Harrington’s web page that deals with manual lever-operated ratchet hoists – small and relatively simple pieces of kit when compared to overhead gantry cranes of hundred-tonne capacity or more; but even small lifts can be dangerous if mishandled. All of these bodies emphasise one factor: training.
Bob Burkey is a senior engineering advisor at Columbus McKinnon and a participant in a recent HMI webinar exploring safety best practice.
‘Not only does HMI strongly recommend comprehensive operator training in the safe use of a hoist, but the Occupational Safety and Health Administration (OSHA) and American Society of Mechanical Engineers (ASME) do too’, he said.
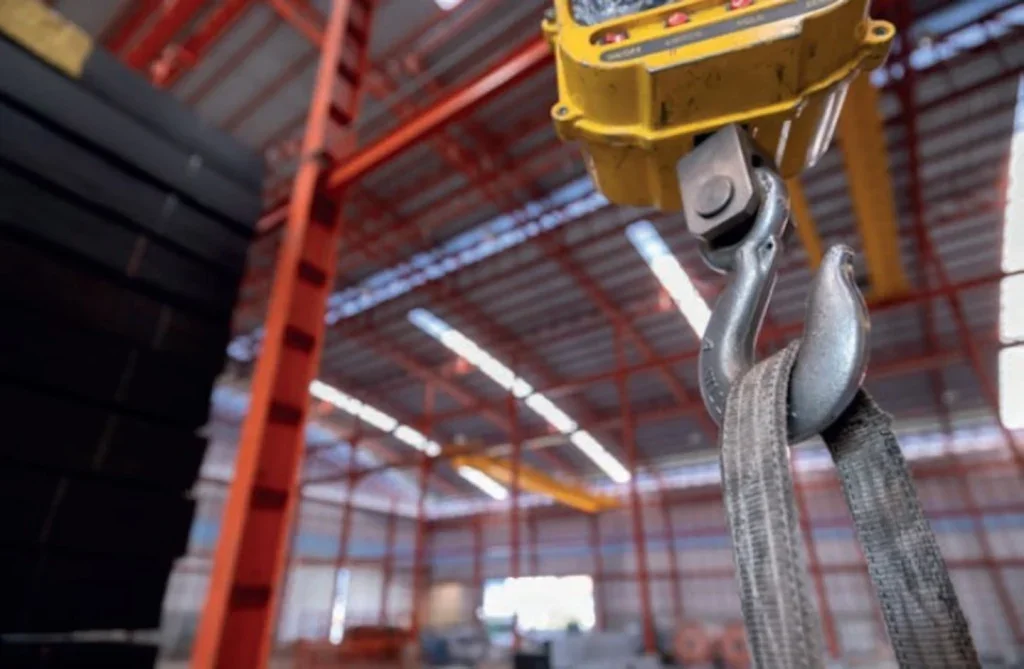
“Proper training includes a review of the hoist’s manual, HMI’s recommended operating practices, and hands-on use of the hoist. No training is complete until the operator has demonstrated the ability to operate the hoist in the actual application.”
Technology has transformed the risks involved in lifting – and by ‘transformed the risks’ we mean ‘reduced them greatly.’ This is especially true of digital technology, and it has done so in a remarkably short space of time, in the space of barely a decade. Lifts by overhead crane, as we all know, should be performed vertically, to avoid the load initially dragging on the floor and subsequently swaying. (Note that non-vertical positioning was a factor in the third of the fatalities cited above.) It used to be that operators needed their hardearned skills and judgement to position the trolley and hook directly over the load. Hook position sensors now do this automatically – and can set the load down in exactly the required position as well.
Once lifted, a swaying load is dangerous; moving the load without it swaying was again a considerable accomplishment of the skilled and experienced operator. Anti-sway technology is now bog-standard.
When it is installed, the newest recruit can achieve a non-swaying rope and load movement without effort; the technology has taken over the job.
Anti-collision technology is also standard. No manufacturing plant is entirely free of obstructions for its overhead travelling cranes; walls, pillars, fixed machinery have to be manoeuvred around. One hopes that the routes of travel are free of people also: one of the most elementary rules of safe lifting is ‘Do not have anybody standing or walking underneath the load.’
Restricted travel areas, also known as ‘no-fly zones’ can be set digitally, so that the crane will not move its load close to obstructions and walking routes. Simple limit switches will restrict trolley movements to rectangular zones; digital laser and encoder devices can accommodate more complex boundaries.
Related to no-fly zones is anti-collision technology, for situations where, for example, two or more cranes operate in the same area; sensors ‘tell’ each crane where the other is, and prevent them from trying to occupy the same space.
Had these technologies been installed in the fourth of our opening examples, where a C-hook struck a piece of machinery making its coil fall off the hook, would the fatality still have occurred?
In the absence of further information, one would be very strongly tempted to answer ‘No, it would not have. The employee would still be alive.’
Nor should expense be a consideration in installing such technology. There is no need to replace existing, pre-digital, overhead cranes if they are still in good condition; retrofitting of digital sensors and controls is almost always an option.
In the UK, the Lifting Operations and Lifting Equipment Regulations (LOLER) 1998 require that all lifting equipment used at work is inspected by a competent person at least every 12 months (six months if it is used to carry people. Accessories also must be inspected every six months.) The inspection must be done by a ‘competent person’. The term ‘competent person’ is not defined in law but the LOLER Approved Code of Practice and guidance (Paragraph 296 on ‘competent persons’) states that:
‘You should ensure that the person carrying out a thorough examination has such appropriate practical and theoretical knowledge and experience of the lifting equipment to be thoroughly examined as will enable them to detect defects or weaknesses and to assess their importance in relation to the safety and continued use of the lifting equipment.’
The competent person is often employed by an outside organisation. This is not essential as long as they are ‘sufficiently independent and impartial to ensure that in-house examinations are made without fear or favour.’ However, this should not be the same person who undertakes routine maintenance of the equipment – as they would then be responsible for assessing their own maintenance work. Records must be kept of all inspections.
HSE point out that this ‘thorough inspection’ is NOT the same as ‘routine maintenance.’ ‘Maintenance’ is a requirement under PUWER and involves such things as lubrication, checking and replacing worn or damaged parts and time-expired components, topping up fluid levels, and making routine adjustments. It avoids risks associated with wear or deterioration.
‘Thorough examination’ may indicate areas of poor maintenance but is not intended to replace it. You should not wait for the results of a thorough examination before carrying out maintenance on your lifting equipment.
In the US, OSHA has established comprehensive inspection requirements to ensure that cranes operate safely and efficiently. 29 CFR 1910.179 is the standard that pertains to overhead and gantry cranes used in general industry settings. It includes requirements for crane design, inspection, testing, maintenance, and operation. The standard outlines inspection frequencies and procedures to ensure that cranes are safe for operation. 29 CFR 1910.184 is the standard for slings, which may also be relevant if they are used with your overhead cranes, and 29 CFR 1926.251 applies also to shackles.
Training, as we have seen, is paramount to safety. Communication is also vital, as the case in the box so sadly shows. One more factor needs to be mentioned. It is common sense.
Most safety precautions are fairly obvious. Do not stand underneath a hanging load. Make sure that your crane is in good condition. Do not use a frayed rope or slings. Do not lift a load that exceeds the capacity of your hoist. Make sure your load is securely attached. Make sure that you can see where the load is at all times and that the load path is clear. All of these are common sense. These are all covered in the regulations.
The regulations, though, are an addition to common sense. They are not a substitute for it. Every lift is unique, and regulations cannot cover every eventuality. The best way to avoid accidents is to follow the regulations – and to use common sense.
Training is essential to safety. This is as true for small, manually-operated rachet lever hoists as for the largest of equipment. Employers have a legal requirement to ensure that their employees are suitably trained for any equipment they may be required to use. In the UK, the Health and Safety at Work Act 1974 requires all employers to provide suitable and relevant training to ensure that employees are able to work safely at all times. Many specialist training organisations exist to provide such training and the certification that different jurisdictions and industry bodies may require.
As an example, Plant and Safety, headquartered in Staffordshire with a base also in Dumbarton in Scotland, are industry experts in inspection, testing, certification and training. They have over 50 training courses available including, among others, Health and Safety, Working at Height, Lifting Equipment and Lifting Operations. The courses can be provided at the client’s premises if required.
Their ‘LOLER Inspection and Thorough Examination Training Course: Portable Lifting Equipment and Accessories’ has as its objective ‘to teach delegates how to carry out a LOLER Thorough Examination and LOLER Inspection on a range of the most common portable lifting equipment and accessories in accordance with LOLER 1998 and PUWER 1998. The lifting equipment and accessories covered within the LOLER Inspection training course includes, but is not limited to; Wire Ropes, Chain Slings, Webbing Slings, Eyebolts, Shackles, Hooks, Chain Blocks, and Lever Hoists etc.
This LOLER inspection training course is designed for both new/novice and experienced personnel.’
SpeedyHire is a Merseyside equipment hire and sales company that also offers training courses. Their ‘Safe Use of Hoist’ course is designed for anyone who will be lifting loads using a hoist, with the aim of teaching operators to safely sling loads and to use chain hoists. The course lasts one day, with a maximum of six students, with certified accreditation. It is classroom based, with practical exercises and group participation; on completion participants will know their statutory duties under the Health & Safety at Work Act 1974; the correct procedure for using hand and electrically operated hoists; safe methods of slinging; the importance of weight and centre of gravity in relation to the safe working load of the lift tackle.
Some hoist manufacturers also offer training courses on their equipment, intended for users or for inspectors or for technicians required to maintain the equipment, or for inspectors. As an example, Columbus McKinnon offer courses, at three locations in the US, one in Germany and one in the UK; they also offer on-line certification training.
Courses cover overhead cranes, hoists and rigging products and include ‘Qualified Rigger’ ( a 2-day workshop), ‘Overhead Crane and Hoist Inspection certification’ (a 2-day course); and ‘Rigging and Crane Operator Safety Train the Trainer’, a four-day workshop. A specialised course is for riggers and hoist maintenance professionals in the entertainment industry.
Their UK training centre is at a purposebuilt facility in Cheshire. Courses there include the ‘Camlok Lifting Clamps’ course, a sales-driven classroom course aimed to improve confidence when selecting and specifying the right clamp for the job. The ‘CM Lodestar electric chain hoist’ course is aimed at service engineers. A basic level of understanding and familiarisation with electric chain hoists would be expected prior to attending.
Lifting 365, based in London, are lifting gear suppliers who also offer an online course on manual chain hoists. Participants, they say, will acquire a fundamental understanding of the health and safety considerations relevant to the Health and Safety Act including practical knowledge of different types of hoists, their purposes, operation and legal requirements. The course also has a focus on inspection, usage considerations, maintenance, and storage which ensures participants are well-versed in safe and effective hoist handling. Upon completion there is a downloadable certificate.
They also offer courses in electrical hoist safety awareness; pneumatic chain hoist safety awareness; and lever hoist safety awareness.
Some applications are by their nature more hazardous than others, and therefore require additional skill sets. Wind farms are one. Nacelle hoists are at great heights above the ground, and accessing them and operating them is far from simple.
Two incidents involving hoist safety on wind farms are detailed in the case studies. One was at an offshore site one onshore. Fortunately no injuries resulted, but both had the potential to cause fatalities.
The Global Wind Organisation in July 2023 published its tenth training standard, which adds Crane and Hoist operations to the portfolio. The standard ensures a basic level of safety awareness in lifting operations where no formal training or certification is required owing to the limited size of the lifting equipment in wind turbine environments.
The training enables wind industry employees to safely operate, inspect and maintain common types of fixed cranes and hoists in the wind industry.
The Crane and Hoist training Standard is divided into two modules. The Basic User Module ensures safety awareness when using cranes and hoists in service operations. It also provides participants with an introduction to safely operating common types of fixed cranes and hoists.
The Inspection and Maintenance Module enables the technician to inspect, maintain and test cranes and hoists complying with relevant legislation and according to the relevant manufacturers` inspection and maintenance manuals and documents. The Crane and Hoist Basic User Module is a prerequisite for participating in this module.
Thomas Grønlund, senior training project manager at GWO, explained the importance of the Crane and Hoist Training Standard. “The goal of this training is to contribute to a safe work environment for daily lifting operations in the wind industry” he said. “The training focuses on the ability to take responsibility for doing the right thing when operating cranes and hoists.”
CRANE STRIKES SCISSOR LIFT, FRACTURES SKULL
In April this year two UK companies were sentenced and fined after a worker fell from a scissor lift that was struck by an overhead crane. The worker, an electrician, landed on the factory floor. He fractured his skull, leaving him in an induced coma.
The electrician, employed by Optilight Electrical Services, had been repairing light fittings at Expert Tooling and Automation’s site on Sayer Drive, Coventry. He was in the cage of a raised scissor lift approximately 10 metres high when a worker at Expert Tooling began to operate a nearby overhead crane. The crane operator did not notice the electrician in the scissor lift. The crane collided with the scissor lift, causing it to twist and hit nearby racking before landing on the factory floor.
The electrician came out of the cage while it was falling, hitting his head on the floor and sustaining serious injuries.
A second worker at Optilight Electrical narrowly avoided being crushed by the scissor lift, jumping out of the way before it landed on the floor.
The injured worker sustained a fractured skull, two brain bleeds, a broken collarbone, eight broken ribs, a broken elbow and wrist as well as a punctured lung. He was later placed in an induced coma and underwent several operations.
A HSE [Health & Safety Executive] investigation found that Optilight Electrical had not identified the operation of overhead cranes as a risk to its employees that were working at height at Expert Tooling’s site. Expert Tooling did not put procedures in place to prevent the use of overhead cranes while the work at height was taking place. Expert Tooling instead relied on contractors identifying risks and implementing control measures, rather than ensuring procedures were already in place. Both companies did not communicate to each other how the work they were undertaking could impact their staff’s safety at the site.
HSE guidance recommends implementing “permit to work” systems for work activities that require extra care. They are a more formal system stating exactly what work is to be done and when, and which parts are safe. Permit to work systems also provide a means of communication between site management, supervisors, operators and those who carry out the work.
Expert Tooling & Automation, of Sayer Drive, Coventry, West Midlands, pleaded guilty to breaching Section 3(1) of the Health and Safety at Work etc. Act 1974. The company was fined £50,000 and ordered to pay £1,985.97 in costs at Birmingham Magistrates’ Court on April 29, 2024.
Optilight Electrical Services, of Oakwood Road, Mansfield, Nottinghamshire, pleaded guilty to breaching Section 2(1) of the Health and Safety at Work etc. Act 1974. The company was fined £7,000 and ordered to pay £1,985.97 in costs at Birmingham Magistrates’ Court on April 29, 2024.
HSE inspector Charlotte Cunniffe said: “This case clearly illustrates the disastrous consequences that can occur when two companies each assume the other has taken responsibility for safe working practices. Risk often arises through a failure to communicate effectively.”
CHAIN DROP AT ONSHORE FARM
A team were on site carrying out a service on an on-shore wind turbine. Prior to commencing work at height, a Demarcated Area was established at the base.
Technician 1 climbed to the nacelle and lowered the chain hoist to lift the tool bag up.
Technician 2, at the base of the tower, hooked on the bag and started climbing. Technician 1 began hoisting up the tool bag. At about 20m up, the chain hoist stopped.
In the nacelle, both technicians inspected the chain hoist and could see nothing wrong. They tried to select ‘up’ om the hoist but nothing happened. They selected ‘down’. The chain broke in the chain hoist and the tool bag and approximately 30 meters of chain fell to the ground from a height of 20 meters. Nobody was hurt because nobody was in the area: the exclusion zone had done its job.
As immediate steps, the chain hoists were straight away taken out of service via the issue of an Operational Restriction. A review was carried out across the fleet for chain hoists of similar type and /or configuration. An investigation was carried out.
The findings were that the hoist in question is unusual in the chain bag or bucket is offset from the chain hoist – the chain is fed from the chain hoist to the bucket (and vice-versa) via an angled tube. The lubrication on the chain had over the years accumulated and become slightly sticky: the turbines were approximately 14 years old.
During the event, the chain had stopped flowing through the tube and started backing up.
The chain eventually backed up all the way into the chain hoist and jammed it. When the technician selected “down” the chain was therefore bunched up inside the chain hoist and was not being fed correctly onto the chain hoist mechanism. The chain came sideways onto the pully wheel and a link was cut between the pully wheel and the link guide. The cut chain, and the load, dropped to the ground.
Recommended actions were that all chains and tubes were cleaned, inspected and a functional check completed by a competent person before returning the chain hoists to service. Inspection and cleaning of residual grease has been added to the annual service. Demarcated Areas are established PRIOR to any work at height that could give rise to a falling or dropped object.
CHAIN DROP AT OFFSHORE PLATFORM
Two technicians were operating the davit crane hoist on the external working platform of an offshore wind turbine. Having lowered all their bags to the crew transfer vessel below, they reeled in the chain hoist without any load when the stored chain unexpectedly fell from the chain bag, dropping towards the vessel.
One of the technicians tried to grab the chain, which was too greasy to hold, while the other rotated the davit crane towards the platform and so away from the vessel. Consequently, the chain, weighing around 3.85 kg, dropped and landed close to the vessel.
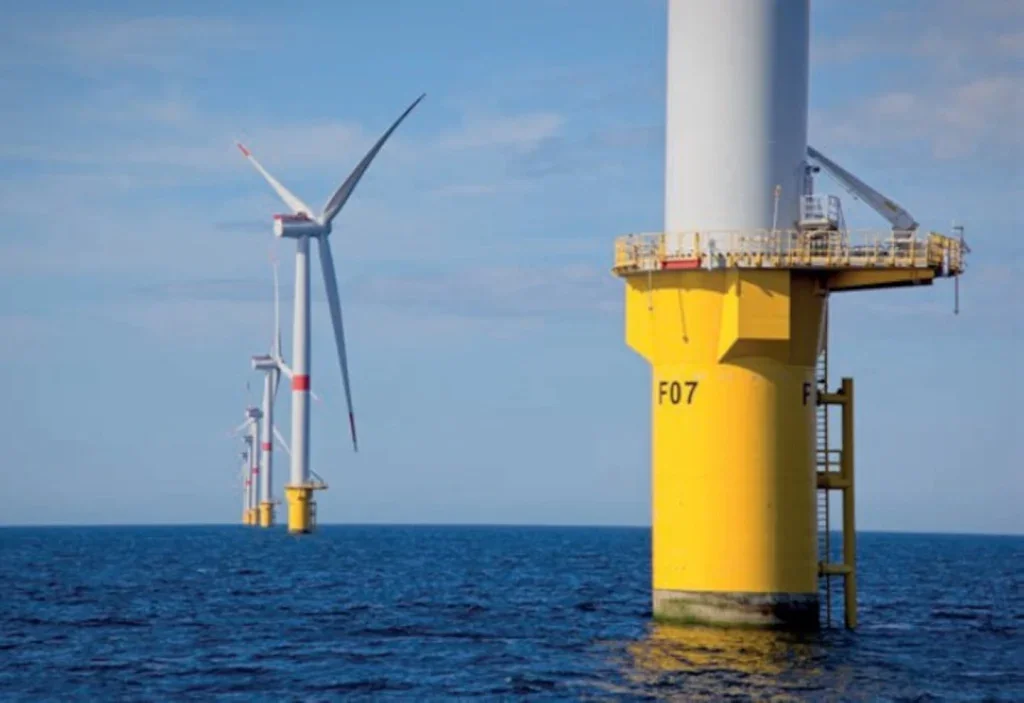
The deck crew had followed procedures and were standing at least 8 metres away from where the chain landed. According to the drops calculator, the chain’s estimated fall from 10-15 metres could potentially lead to a fatality.
A similar event occurred three months later, coinciding with the implementation of investigation actions from the initial occurrence. However, on this occasion, the chain fell further away from the vessel and into the sea. This incident too could potentially have resulted in a fatality.
The investigation concluded that the chain hoist design was not inherently safe as it allowed the chain to fall out of the chain bag under specific conditions. With no load on the chain hoist, technicians were unaware of the potential risks associated with proximity to the drop zone. Additionally, technicians lacked awareness of the hazards associated with attempting to grab the falling chain.
At 9:00 in the morning on October 18, 2023, an employee working as a tool and die maker for a plastics manufacturer was using an overhead crane to move a large metallic die. The die broke away from the components that were secured to the lifting eyes causing the die to drop several feet. The die struck the employee as it fell, puncturing and fracturing his skull and killing him.
At 2:30 in the afternoon of June 29, 2023, an employee, a grinder and plasma cutter, was operating a 10-ton overhead gantry crane to hoist a large rectangular piece of sheet metal, measuring 101-inch by 1/4-inch by 73-inch and weighing 614 lbs (280 kg) to nearby metal sawhorses. Once the employee positioned the vertically suspended sheet metal above the stationary sawhorses, the sheet metal unexpectedly fell from the vertical clamp. The sheet metal momentarily landed vertically on the sawhorses before falling flat in the direction of the employee who was standing on the ground between the two sawhorses. As the sheet metal fell, it struck the employee and slammed him onto the concrete floor with enough force to fracture his upper right femur. The employee died four days later due to peritonitis brought on by a perforated duodenal ulcer due to the fracture.
At 3:00 p.m. on May 2, 2023, an employee was moving a steel coil using an overhead crane and a C-hook when the coil struck a large piece of machinery and fell off the hook. The coil struck the employee, killing him.
At 5:38 p.m. on November 9, 2023, an employee was pre-staging a panel die that weighed 88.8 tons for a press machine. He moved the die while standing between two dies with an overhead crane. The die tilted because the crane was not centred over the die. The die moved towards him and pinned him between it and another die in storage. He died from his injuries of traumatic asphyxia at the scene.