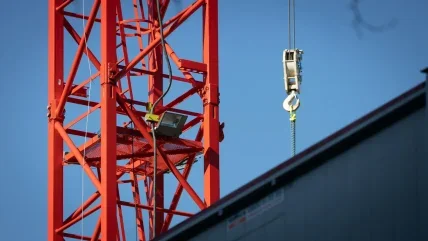
Of the myriad problems presented by securing loads to a lifting machine, let us start with perhaps the simplest: weight. A heavy load requires a hole, shackle, lug or some other projection or cavity on which to attach a hook. LiftEurop designs and manufactures standard and customised lifting equipment and accessories, such as lifting slings, lifting beams and lifting clamps for such purposes and distributes them in over 40 countries worldwide.
The newest addition to its product range is the MLA swivel lifting shackle, designed to lift loads up to 250t, and available in five different working load limits, starting at 85t. Resistant, since it is made of hardened steel, it is designed for lifting in all directions with optimal load distribution. It comes with threaded bolts in place, which avoids the need to drill an oversized hole in the load, and has adaptable centre distances to suit the customer’s needs.
Shackles alone, however, are not sufficient for all lifts. Modular building units – cabins, wall panels, entire preassembled rooms indeed – are prime examples, and modular building, for residential and other uses, is a growing sector, being cheaper, quicker and more efficient to construct than conventional bricks and mortar. It presents its own problems in load security, both in the factory where the units are prefabricated and, especially, on site. Modules are large, fragile, and with few obvious attachment points. Increasingly, they are being used as part of high-rise developments, which only increases the challenge. A new system from Britlift is helping improve productivity for such lifts.
Rainbird Crane Services works predominantly in central London, specialising in lifts onto high-rise buildings of prefab and modular units. It needed a modular system that could help it safely and quickly lift a variety of different bathroom pods and turned to Britlift for a solution.
“The pod manufacturer provided a frame, but it relies on a slotted system where you have to move the brackets and rigging on top of the framing each time,” says Jonathan Rainbird, director of Rainbird Crane Services. “We wanted a modular product that could speed up the entire process for us and make it less onerous.”
Britlift designed and supplied a bespoke modular system specifically for lifting the pods. It has removable corner pieces with fixed length struts, meaning that Rainbird can lift different pods without having to make any adjustments such as bolting or unbolting sections.
Britlift’s system incorporates lugs along the strut length, plus multiple lifting lugs on each corner piece. The lugs are colourcoded to correspond to a specific make and model of bathroom pod, making it quick and easy for Rainbird’s crews to use.
“We needed the system to cover eight different types of pods and Britlift were able to do that for us,” says Rainbird. “For example, for pod A we might use the bluecoloured lugs and for pod B we would use the red points. It has sped up the whole process massively for us.”
Rainbird uses cranes to lift the pods onto cantilevered loading decks and scaffold landing platforms. The pods are then tracked across the floor plates using movement equipment before being positioned, aligned and levelled.
“I have used Britlift before for modular beams and frames,” says Rainbird. They have provided us with the perfect piece of kit for lifting these pods and it is saving us a huge amount of time”.
KITO CROSBY
Britlift is based in Dorset, UK. A little further east along the coast, in Waterlooville, Hampshire, is a new, larger production facility of Kito Crosby. A new product from the site was launched in June last year. Kito Crosby brand Crosby Straightpoint’s LoadConnect product is a cloud-based software solution that monitors loads and enables users to remotely observe load cell data via an online dashboard.
It allows users to remotely monitor loads from anywhere in the world. Each base station can connect to up to 16 load cells simultaneously and wirelessly transmit data to cloud-based software, LoadConnect, or via SMS to a mobile phone. It will read data from most Crosby Straightpoint cabled or wireless load cells and display live load data, load alerts, and productivity and utilisation reports.
The new production facility, for load monitoring equipment and crane camera systems, made a short trip inland to Waterlooville from its previous location in Havant. With the new facility, the company doubles its floor space, which will facilitate improved workflow; the site suits current production requirements but can be extended in line with future demand.
Thomas Dietvorst, senior global product director, wire rope hardware and tech solutions at Kito Crosby, says: “We knew upon acquisition of Crosby Straightpoint and Crosby BlokCam [brands] that we would need to eventually invest in a larger facility to facilitate growth plans. The new site meets our requirements and immediately gives us a larger factory, improved capacity, and enhanced stock levels. Staffing levels have doubled over the past four years, and this move also reflects that.”
VACUUM LIFTER
Wind power is, of course, a huge growth sector, and one that comes with its own, considerable lifting problems. Consequently, ingenious solutions have been and are being developed.
One ingenious solution for lifting a complete wind farm tower during transport to the site involved a Modulift spreader beam (see ‘Modulift moves monopile’). But even lifting such towers in sectional form is not easy.
The monopiles that support the turbines are heavy, tall and generally not cylindrical: they taper towards the top. It follows that when they are fabricated in sections, either of steel or of concrete, each section will be a slightly different shape from the one above it and the one below it. Designing a lifting device that will securely fit all of them is therefore a challenge.
However, Dutch vacuum-lifting company Aerolift has done it.
“The tower of a wind turbine is a great example of a conical-shaped object,” says the company’s Zoya Boonstra. “On the ground, the diameter of the tower is much larger than at the top. Every element of the tower deviates a little more and more. The precast element on top has completely other dimensions than an element on the ground.
“It was a puzzle to solve – a search for the perfect combination of the number of suction pads, shape, distance and adjustability. We designed a vacuum lifter whose pads are adjustable to meet all shapes of the precast elements to be lifted.”
Before that comes into play for assembling the units, though, the units themselves have to be made – and for that Aerolift designed and built the world’s largest vacuum lifter. It is used to lift the heavy steel plates – which weigh up to 85 tons – that are used to construct the wind turbine tower.
Originally, the vacuum lifter was designed, and was built, to lift steel plates up to 24m and 70 tons. The design consisted of a base frame that could be made longer with extensions on both outer ends.
“Five years later, the customer requested an upgrade, to also be able to lift the heaviest steel plates in the factory – up to 85 tons,” says Boonstra. “For the upgrade, we engineered two extra extensions, which can be placed between the base frame and the first extensions. Without any extensions, the vacuum lifter can lift steel plates up to 16.4m."
If 85 tons seems a lot to lift by vacuum power – it is.
“Due to the extreme heavy load, we decided in consultation with the customer to engineer each suction pad as a separate vacuum device with its own vacuum tank,” says Boonstra. “If one suction pad should fail, this will have no effect on the other suction pads. The operator will receive a warning of the malfunction, but the heavy load of 85 tons will stay safely attached. This is one of our additional safety features for extreme loads or circumstances.”
The vacuum frame itself weighs 32t, and has, by coincidence, 32 suction pads, which are electrically powered. It is in five sections of a base frame plus the two sets of extensions and, with the extensions in place it is 31m long.
Challenges in load security will continue to present themselves. And the odds are that, with ingenuity and imagination, aided by hard work, solutions will continue to be found.
Modulift moves monopile
The rise in renewable energy sources has accelerated demand for Modulift spreader beams to lift turbines, towers and monopiles at onshore and offshore wind farms worldwide. As part of this expansion, global ship operator G2 Ocean deployed a Modulift spreader beam to Colombia for the lift of a 63t Nordex Wind Tower.
Colombia provides good conditions for wind power generation, with wind forces of around 9m/s. G2 Ocean assembled a MOD 250 Spreader Beam on-site in the north of Colombia, the location of most wind farms in the country due to the position off the Caribbean coast. The Nordex TS105 wind tower sections – these ones were cylindrical – were successfully lifted from the Star Lysefjord vessel to Puerto Brisa, a small cargo terminal in the north.
“Conditions at the port were challenging,” says Richard Stannard, senior equipment manager at G2 Ocean “The remote location and lack of infrastructure at the port raised concerns about how we could safely lift and unload the tower sections. We were also working to a tight deadline, so time was of the essence.
“The nearest port was Santa Marta, but due to issues with road transport from the port to the project site – largely clearance issues under bridges – we had to rethink how to get the tower sections to the site. Puerto Brisa was the next option but as it is a coal loading facility there were no cranes available at the terminal.”
To overcome this, the cranes on-board the ship were used to carry out the lift. The Nordex TS105 tower sections measured 36m in length, with a 4.3m diameter.
Stannard says: “The heavier sections were loaded further forward on the deck and unloaded using the ship’s cranes in tandem. However, the upper sections could only be reached with one crane, which was achieved using the single 75t crane.”
An additional challenge was low headroom, so the rigging had to be as short as possible. Stannard continues: “There were limitations on the allowable sling angle at the load. We needed a 45° angle on the slings above the spreader beam.”
Taking this into account, the MOD250 was rigged at 18m, with a safe working load of 91t and 45° sling angle. Using a modular spreader beam also sped up the turnaround time – with the longest strut at only 6m and total component weight of 4t, G2 Ocean was able to airfreight the beam to Colombia, transport it by road and easily assemble it on-site.
Sarah Spivey, managing director of Modulift, says: “G2 Ocean’s project presented several challenges which Modulift was able to help overcome. The modular design allowed for easy transportation, and the lack of headroom was not an issue as the rigging was able to be short. We were pleased G2 Ocean could deliver on this project safely and efficiently with the help of our products.”