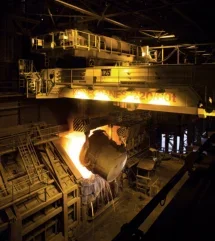
Things are changing in steel production. Green steel is becoming a reality. Electric furnaces are becoming more precise, more efficient, through digitallyimproved control systems. The whole process is complex, from inputs of scrap metal in varying compositions to exacting furnace temperatures and timings, admixtures of ores, scrap and additives in varying ratios, cooling rates, rolling speeds… And all of that takes place after the mining and refining of the ores. Steel production needs reams of data, interacting in hugely complex ways, to produce end products of various different properties of hardness, ductility, corrosionresistance and the rest. Consequently, it is ripe for Artificial Intelligence – which is indeed entering the process. New mills and furnaces are embracing A.I., with good reason.
Italian company Danieli, perhaps the worlds manufacturer of equipment for steel making, is involved in dozens of new projects worldwide; it supplies furnaces, shredders (for scrap metal), tundishes (the bucket-shaped containers full of molten metal that get carried around by overhead cranes) as well as feed cranes. It has a concept for steel production, which it calls ZHA, ‘Zero Humans Around’.
Given the heat and dust of foundries, and the continuous presence overhead of huge buckets of red-hot molten metal, having no people in the vicinity is clearly desirable. But there is more to it than that.
“The use of AI technologies brings us to the development of a new level of automation for both production and business processes,” says Danieli. “It steers us towards what was recently described as ‘hyperautomation’. Hyperautomation (or Intelligent Automation) means automating all the processes that can be automated within an organization applying the right priority and the integrated tools capable of covering the need for digitization in its entirety.
“This is already a technological reality in many steelmaking plants,” it says, “even if only as pilot projects and experiments.” Advancing AI from experimentation to generating practical sustainable results is, it says, the next challenge. “AI’s growing capabilities – connected with advanced automation and applied to production process and flexible and efficient machines – gives us the opportunity to push the limits of the concepts of autonomous plants and zero-humans-around.”
The goal is to have plants that satisfy quality requirements with lower operating costs in raw materials, consumables or energy. Another target is to extend the capability of a specific production process beyond its original limit, in terms of quality of product, with the prospect of serving markets not originally envisaged.
All of this changes the role of the overhead crane. It no longer makes sense – if it ever did – to treat it in isolation. It is no longer an entity in itself, with its own control system – either human or automated. Its control is part of the AI system organising the whole process, from ordering of material to delivery of finished product – and perhaps to the production of new products by varying the parameters of heat, timings, and raw materials while still using the same equipment in the plant.
So humans need not be anywhere near all of this. Scared yet? Wait a bit and you might be. For Danieli also speaks of the interaction between artificial ‘intelligence’ and biological ‘intelligence’: “In this sense, the human-machine interaction must be conceived and implemented as an integration between machines and people. The human operator must be able to understand the behaviour of the machine in order to trust it, use it, and bring about its evolution, building a relationship much like those existing between colleagues, with mutual exchange of knowledge and skills.” The distinction between machine and human begins to break down. We must hope that AI turns out to be a skilled, helpful and co-operative colleague, like most (but sometimes not quite all) of our human ones.
That said, the essentials of making steel – and the physical types of lifting that are needed at the various stages – have not changed. Iron ore and coke still need to be moved; scrap metal remains an ingredient, and has to be delivered to the scrapyard, from where a process crane must transfer it to the foundry. There, the hazards and challenges increase: open flame and molten metals abound.
The scrap is loaded in the furnace by an overhead charging crane. An auxiliary hoist on the crane opens and closes the bucket during loading. Depending on the facilities, a basic oxygen furnace or an electric arc furnace could be used. Iron ore and coking coal are combined in a direct reduction process to produce metallic iron. A ladle crane lifts the melted iron. The molten scrap is added to it; a teeming crane helps to mix the red-hot liquids in the right proportions.
Once the mix is right, liquid steel is then cast into shape. The molten steel is moved to the moulds overhead in huge open vessels – they are called tundishes, and the overhead cranes that move them are called tundish cranes.
So severe heat, dangerous loads and continuous production demands typify the process.
The charging crane, ladle crane, teeming crane, and tundish crane are all similar in construction and can be defined by their location and function in the plant.
They are usually overhead traveling cranes that are fitted with special attachments to lift the giant ladles that contain liquid metal. They often perform more than one function and are used as backup for each other. Auxiliary hoists can be attached for scrap charging and maintenance functions, such as cleaning the empty ladles or lifting the furnace shell.
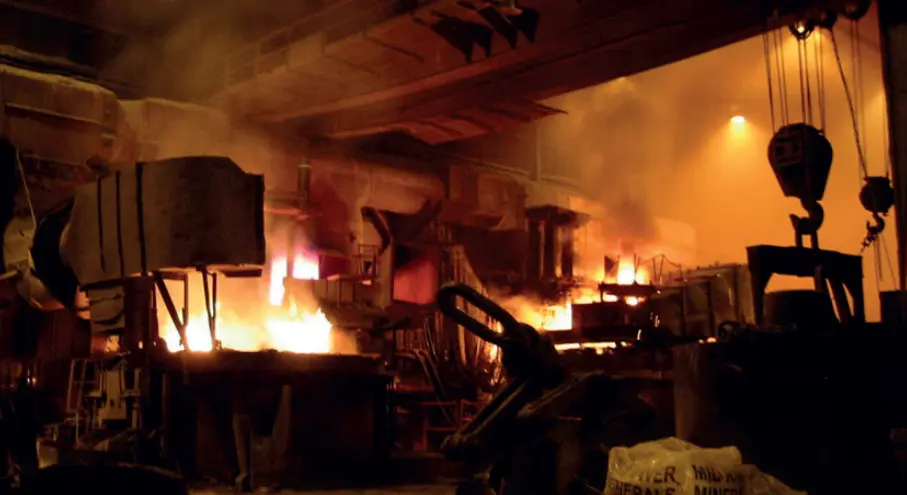
And it goes without saying that all of these must be reliable. Steel production by its very nature has to be continuous; you cannot shut down a furnace for an hour or two just to repair a crane. Despite operating 24 hours at a stetch, seven days a week, in the harshest of environments these cranes simply must not be allowed to fail. Redundancies, fail-safes and back-ups must be the order of the day.
Even when the metal has been cast and cooled, the need for lifting and handling is far from over. The metal must be rolled, stored, cut to size, delivered. The hoists, cranes and lifting gear in the steel industry is perhaps as varied, and as rugged, as you could find.