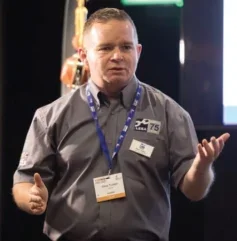
Manual chain hoist inspection should be performed systematically and critically to the statutory regional global requirements, typically this is 12 monthly for goods lifting and six monthly is used in the lifting of persons. The frequency of inspection maybe adjusted to take into account duty cycles (frequency of use) and also to increase workplace health and safety.
As with all inspection of lifting equipment, the examiner should reference the manufacturer’s specific data for discard allowances, which should always be treated as the maximums. In the absence of this, standards maybe used provided the hoist was built to them, otherwise recommendations as provided by LEEA may be used.
In an ideal world the examiner should have access to all documentation (Declaration of Conformity, where necessary and depending on location of use, and manufacturers certification) which can be cross referenced to the equipment to ensure it is still as intended from the manufacturer, with no unauthorised or illegal modifications.
In addition to this, other documentation may be required such as previous inspection reports, which may detail previous findings including minor defects and previous wear in the hoist assembly or repairs, which the examiner can then verify have been carried out correctly using authorised replacement parts.
The documentation can also be used to verify the markings on the hoist assembly, which must be clear and legible for the lifetime it is in service. This must include not only the markings on the data tag but also the load chain (of the correct grade) and load / suspension hooks (of compatible capacities).
Once the examiner is happy the hoist is as intended then, ideally, the hoist should be suspended from a suitable suspension point, freeing the examiner’s hands whilst also allowing testing to be performed at the discretion of the competent person.
The complete hoist assembly will generally be made from steel, so generic metallic defects the examiner would be looking for throughout all components (both chains, hooks, anchorage, covers, guide rollers, etc) would be excessive nicks, cuts and gouges as these can lead to stress raisers causing unexpected premature failure.
Minor defects may be dressed and removed carefully using a file, however deeper defects, especially in high stress areas, would be classed as discard criteria. Excessive corrosion (pitting) would also lead to discard however light surface corrosion may be removed by suitable cleaning methods. Any form of heat or chemical attack is immediate discard as this is likely to effect the internal steel grain structure or alter the manufacturers heat treatment, potentially making any component brittle. No mechanical deformation is acceptable which can be classed as permanent set, ie, change of original shape (bending, twisting deformation and distortion. And under no circumstances should the examiner try to straighten a component through cold working or the application of heat.
When in use, lifting equipment will start to wear over a period of time. In the absence of manufacturers’ or standard discard criteria LEEA allows for the following maximums: suspension and load hooks 8%, load chain loss of diameter 8%, elongation due to interlink wear 3% and no elongation due to stretch (overload). By having sight of previous inspection reports the examiner can also verify whether the wear is gradual over a period of time, or accelerated due to a change of duty cycle, or indeed potential misuse, and recommend more frequent inspections if required.
Security of all components should be taken into consideration, ensuring that only the manufacturer’s components are used (load pins) and that they are captive and secure, whilst also confirming that any component (typically load and suspension hooks) that are designed to articulate and rotate do so freely with a smooth operation and that they are not stiff or seized or are slack / loose due to internally worn components.
Testing is always at the discretion of the competent person. A functional test with no load through the full height of lift confirms the hoist is operating correctly through all configurations, whilst ensuring the chain links of both the hand and load chain engage and freely leave the respective pocket wheels, and that the chain stripper is functioning correctly.
A light load test typically between 2% to 10% of the rated capacity should be performed to verify the screw brake is functioning correctly, however if deemed necessary then it should be stripped by a competent person in a clean environment to verify the cleanliness of the brake assembly, condition of the brake discs and other critical components (toothed ratchet wheel and spring tension in the ratchet pawls).
Following any thorough examination the competent person must create a formal report, detailing all their findings, repairs and defects noted whilst accurately recording any tests that may have been carried out.