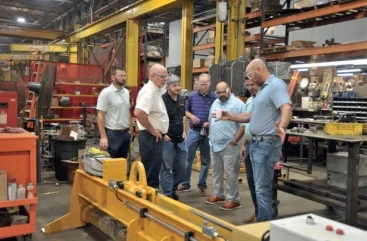
We face a battle to attract the next generation of skilled craftspeople into our industry and we’ve got to entice them in, to fight with, and for us. That’s how I see the task set before #GLAD2024, and the barometer to use, by which to measure its success is welcoming an influx of workers.
The good news is, we’ve made progress since the inaugural awareness day in 2020, launched in the depths of a global pandemic, perhaps when minds were more in tune with logistics than ever before.
But progress is not the prize here; only a monumental shift will see us win. The challenge is in the name itself. Global. Lifting. Awareness. Day. We’re looking to address the entire planet. Tell them what lifting is and why it matters. Raise awareness in a largely invisible sector. And get them to participate in a single 24-hour period to change their attitudes forever. Luckily, we work in one of the most dynamic sectors in the world; we defy gravity every minute of every day.
Five years in, we are starting to get some critical mass. Truth is, it’s no longer just a ‘day’ — this year it’s on July 18 — but there’s a growing level of understanding of what it is and how we can all support it beyond just that Thursday.
We have a steady hand at the wheel. The Lifting Equipment Engineers Association (LEEA), known to many in the US, especially members of the Associated Wire Rope Fabricators (AWRF). Ross Moloney, CEO at LEEA, even delivered a well-received presentation to a delegation at the recent AWRF Spring General Meeting in Nashville, Tennessee.
Like #GLAD2024 itself, we have to acknowledge a process is in play regarding the traction LEEA is getting in North America. It will certainly be fast-tracked by AWRF’s Accreditation Program because it is powered by LEEA’s third-party audits. What nobody disputes is LEEA’s level of expertise, particularly working with companies around the world, so engaging with our community on accreditations can only help. My company has been a member of LEEA for a number of years, so we’re doing our bit to share the benefit of first-hand experience.
I remember a few years ago, when I just joined the AWRF board, and Jeff Bishop, of Bishop Lifting, discussed the idea of creating a quality certification for members. It’s probably taken another decade, 15 years, even, to get to this point.
At AWRF, an officer of the board serves a one-year term, but the vision Jeff created has endured and now we have a great certification process between AWRF and LEEA. That’s credit to the continued support from the AWRF board as well as individual board members like Jeff, Knut Buschmann, Bill Franz, and Brett Woodland, to name just a few.
It’s also testament to the value of patience and determination — and #GLAD2024 campaigners will certainly need plenty of each of them.
LEEA has done a great job of laying the foundations. Trade media is engaged across vertical markets; magazines that cover everything from agriculture to zoology have promoted the concept to their readers, recognising the role lifting plays in their marketplaces. A recent round of messaging addressed the importance of ‘high quality’ in terms of products, inspection, and training. It’s worth looking at each of them in more detail.
High quality products lead to safety and productivity. Further, we live in a constantly developing world where quality products and information about their safe use, have never been more accessible.
As LEEA and AWRF members prove, our industry is constantly enhancing and innovating. This, in turn, creates more opportunities for users to choose not just high-quality products, but equipment that is specifically designed for their application.
With reference to high quality inspection, I don’t have a statistic to hand, but I am going to assume that many more issues happen in the field months or years after a lifting product or application is installed versus when they are first commissioned. It stresses the critical need to maintain high quality inspection standards to work to minimise incidents. Of course, this requires more than just diligence, but quality, well trained people who understand the industry and its requirements.
Finally, to maintain desired standards in an environment where many long-time workers with tremendous amounts of experience are aging out, a focus has to be on training. This is a two-sided coin; we need quality people to train, and we need quality, knowledgeable people to do the training.
AN AGING WORKFORCE
Earlier in this year’s campaign, LEEA had championed skills and employment as good pillars for 2024 engagement activities.
These themes are timeless but, as the industry looks to grow, we are looking to replace retiring workers with new entrants now more than ever. Finding good people and helping them develop the right skills is extremely important — and it will be next year, in 2026, and so on. Our businesses run better with good, well trained people and folks in our industry are more likely to operate in a safe manner if they are skilled and well trained.
All these roads lead to the same place in that our need for skilled craftspeople — welders, fabricators, riggers, operators, technicians, etc. — is critical and unrelenting. Largely, these employees in our industry are not working on a simple, repetitive assembly line (not that there’s anything wrong with that), but rather they have to work on a variety of tasks and products that require experience, skills, and the ability to think.
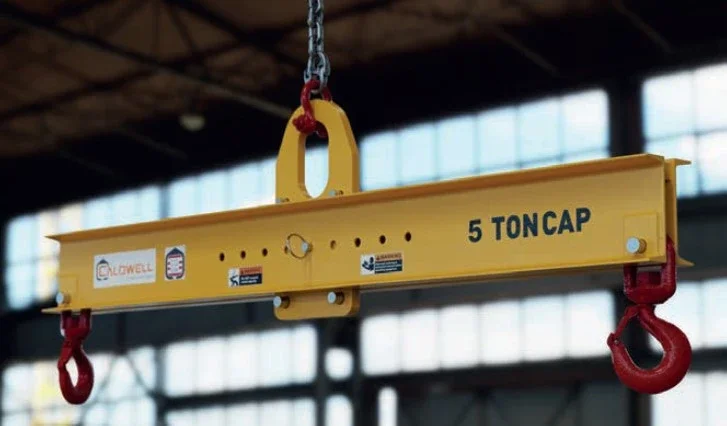
A fabricator in Caldwell’s world is someone who often gets a number of pallets of parts and a set of prints. Their job is to put those pieces together as per the prints and specifications. We need more of those kinds of people across the industry and the U.S. has not done a good job of continuing to develop and support those types of skills development.
However, if I had to put my futurist hat on, I wonder if that cycle has already started to turn, as I hear more and more about people that are entering or considering trade programmes.
In the 1980s, many people felt there were two paths — college or everything else. Today, people are starting to question that a simple college education is the answer.
Additionally, trades are now offering an alternative for many who may have previously considered a college track as a path to certain levels of compensation. I suspect that many today are thinking, ‘I can do a skilled trade programme for 12 or 24 months, versus four years in college’. They are also aware that they have a higher assurance in some cases of getting a job when finished at a decent wage. That path is becoming attractive again for many.
THINK LIFTING
In conclusion, #GLAD2024 is relevant to anyone who is lifting or moving something. And that’s pretty much everyone. That’s how we need to explain to people outside of our industry what we do. From Caldwell’s perspective, if you are lifting a concrete sewer pipe, a new coil of steel, or a prototype military drone, you are a target for the message. While the complexities in those applications vary, my mind goes back to the Think Lifting campaign that LEEA launched earlier in the GLAD journey. It was extremely beneficial in highlighting this thing called ‘lifting’ that many people don’t pay attention to.
Think Lifting on July 18 — and every other day besides.