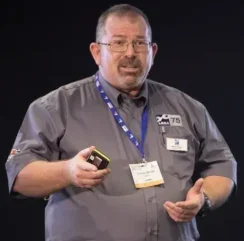
I recently wrote about whether Safe Working Load, Working Load Limit or Rated Capacity was the correct terminology to describe the lifting capacity of lifting equipment. As we all know, the industry has a bigger lexicon than those three terms, much of which is used throughout the LEEA COPSULE (Code of Practice for Safe Use of Lifting Equipment) that is the source of lifting best practice and can be downloaded for free at leeaint.com/copsule.
Being clear on what these terms actually mean is important in an industry where risk of accidents is prevalent and the need for compliance with regulations is widespread. So let’s run through the key terms in the lifting lexicon.
Current legislation uses the term competent person for a variety of duties to describe a person with the necessary practical and theoretical knowledge, experience, training, skill and ability to perform the specific duty to which the requirement refers. So, there can be several competent persons, each with their own duties and responsibilities. A trained person actually using the equipment is usually referred to as an operative.
When we talk about inspection to ensure the safety of equipment, there are three levels: Pre-use inspection is normally completed by the operator of the equipment before each use and in accordance with the manufacturer’s instructions. Interim Inspection, also referred to as frequent inspection, focuses on critical components identified in the risk assessment (from which the nature and extent of the inspections is derived) that may become a danger before the next periodic thorough inspection (examination). The third level is a thorough examination, also known as periodic inspection or thorough inspection. This is a visual examination of the lifting equipment, carried out by a competent person carefully and critically and, where appropriate, supplemented by other means such as measurement and testing in order to check whether the equipment is safe to use. It is also used as a check of the suitability of the equipment and the inspection / maintenance regime.
Lifting equipment, also commonly referred to as lifting devices, is a generic term to indicate loosely all lifting accessories and appliances. A lifting appliance is any machine that can raise, lower or suspend a load such as cranes, hoists, jacks, etc. However, the term excludes machines incorporating a guided load (such as lifts) and continuous mechanical handling devices (such as conveyors).
Multipurpose equipment, usually referred to as general purpose equipment in standards, is any equipment designed to a standard specification to lift a variety of loads up to the marked SWL. Used for multiple general purposes, it is not designed for one specific lifting application. Single purpose equipment or engineered lifting, is any equipment designed for and dedicated to lifting a specific load in a specified manner or working in a particular environment.
Lifting accessory, or accessory for lifting, is used in current legislation to mean an item of equipment used to attach a load to a lifting appliance. Such equipment is also known as ‘rigging equipment’, ‘lifting gear’ or ‘lifting tackle’. In terms of supply legislation, the term can include equipment that is intended to constitute an integral part of the load, and which is independently placed on the market.
The minimum breaking or failure load is the specified load (mass or force) below which the item of equipment does not fail, either by fracture or distorting to such an extent that the load is released.
The factor of safety is the ratio between minimum breaking load and SWL, sometimes referred to in standards and legislation as the working coefficient, coefficient of utilisation or design factor.
A proof or test load is a load (mass or force) applied by the competent person for the purpose of a test. This load appears on reports of thorough examination, if a proof test has been made by the competent person in support of their examination, and on test certificates.
Report of test, previously known as ‘test certificate’, is a report issued by the competent person who did the test and details the specifics of the test. Test reports are not legal documents allowing the equipment to be used, except when used in support of legal documents such as the Manufacturers Certificate or Report of Thorough Inspection/Examination.
Verification is the generic term used to describe the procedures adopted by the manufacturer or Competent Person to ensure that lifting equipment is to the required standard or specification, meets legal requirements and is safe to operate. This includes proof load tests, sample break tests, non-destructive tests, calculation, measurement and thorough examination.
There is more on these terms and how they are used in best practice in the free to download LEEA COPSULE. Being aware, and having an understanding, of this essential terminology will help you become fluent in the language of lifting and, critically, better able to carry out safer operations.