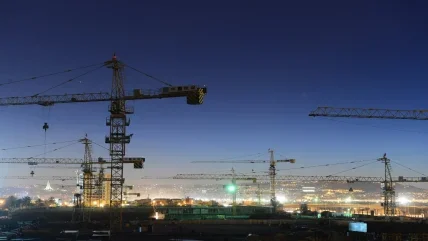
Your crane supplier should specialise in supplying bridge cranes, with a primary focus on safety and proven applications, within the automotive industry. There are three primary types of cranes essential for vehicle manufacturing: the coil crane (when applicable), which facilities the initial stages of steel processing that feed steel or aluminum blanks to the presses, the die handling crane that is responsible for supplying dies to and from the presses for the formation of car body components, and the die maintenance crane needed for the repairs needed to the dies as they wear. While manual die handling cranes are still prevalent, a growing trend towards fully automated die gripper cranes is emerging. This discussion will focus on the automated die gripper cranes.
GAINING TRACTION
The allure of automation is spreading rapidly across manufacturers with a notable recent increase in interest. As automotive and tier one suppliers witness successful implementations of fully automated die gripper cranes in press shops around the world from one manufacturer to the next, other manufacturers are sharing that desire to maximise the safety and higher productivity an autonomous crane brings. The focus for this automation is to remove as much of the manual, laborious and personnel risk activities associated with the changing of the body panel dies in a three to five bolster press as possible. These presses are a critical element in vehicle manufacturing process – they produce the body and shape of the cars and trucks we see driving down the roads every day. A press shop operates 24/7 so the amount of manual interface to a press is extensive and worth reducing as much as possible.
SAFETY
Removing the human element from die handling is paramount for safety reasons. Emphasis on automating this process minimises the risk associated with manually lifting massive dies. In addition to improved safety, automation accelerates production by expediting die change-outs, contributing to inventory efficiency, accuracy and reducing the required real estate needed in the die storage warehouses.
The unique safety culture within the automotive industry, driven by its stringent mandates and requirements, plays a pivotal role in the adoption of advanced crane technologies. The industry’s focus on safety as a top priority is influenced by multinational companies seeking consistent and everincreasing safety standards across their facilities worldwide.
GLOBAL LANDSCAPE
While Asia and Europe have embraced fully automated die handling crane systems, North America is rapidly embracing and considering implementing such technology. The solution is ready, but the transition requires time, especially due to safety considerations. The hesitancy to switch to full automation reflects a cautious approach as it involves all aspects of the operation teams to make such a system work. Automating a die storage warehouse does not come without challenges. There is a great deal of coordination and collaboration needed to make an automated crane system work including close communication between the crane manufacturer’s positioning software and automation engineers and the automotive company’s IT department, enterprise resource planning administrators that need to communicate with the crane warehouse management system (WMS) that controls where each and every die resides in the die storage warehouse, the car company’s safety department, and of, course, the production team, which is the daily beneficiary of the automated die gripper system. Konecranes, for example has a team of automation/WMS engineers to make this integration as smooth and productive as possible.
Its automated cranes are the result of cutting-edge safety technologies, including hook centring, target positioning, and protected areas. Furthermore, the company’s support and service, along with the TruConnect system – a real-time data analytics platform that allows for predictive maintenance, ensuring optimal crane performance and safety – contribute to a proactive approach to crane management.