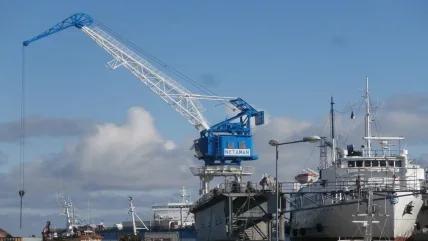
The increasing number of collisions due to an imbalance of weight, during material handling is a key driver for technology in the anti-sway market. There is also a rising demand for more supervised systems to reduce the burden of crane operators, which has influenced the adoption of integrated controls. These automated controlling systems can balance weight shift, allow for a better visual to properly transport the material from one place to another and owing to Government regulations regarding health and safety at work, all these factors have positively influenced market growth.
The findings come from a report by Global Market Estimates (GME), (‘Global Anti-Sway Crane Controller Market’, published February 25, 2021), which predicts the sector will grow with a high CAGR value between 2021 to 2026. In terms of region, it claims Asia Pacific is projected to hold the largest market share by 2026 due to expansion in the construction and transportation industry, as well as increasing investment in technologically advanced products. North America will also see significant growth in the coming years. Increasing automotive production along with rising demand for more safe operations to avoid heavy fines in lawsuits will influence demand. The region has also witnessed a high collision rate due to weight fall and unstable load swing. The Middle East and Africa is projected to see the highest gains due to demand from the oil and gas industry. The regional growth is also influenced by stringent labour laws and labour safety programs.
Accidents can be very expensive in terms of equipment damage, property destruction, worker injury, and lawsuits from victims and property owners. According to Konecranes Training Institute, more than 37% of accidents happen due to load disbalancing while swaying the load. It says its updated anti-sway crane controller can be installed in existing as well as new cranes. However, the cost of installation depends on the hoist model and compatibility.
GME claims nearly all industries depend on Electric Overhead Travelling cranes (EOTs) for their heavyweight maintenance, manufacturing and process needs. The fleets of these essential workhorses of industry have experienced exponential growth over the last 20 years, with rapid economic growth until the Covid pandemic mothballed some sectors of industry and cut production in others.
Now this growth is poised to resume, as Asia-Pacific nations focus on renewed export drives and extensive infrastructure and industry projects to stimulate growth domestically.
Sectors such as construction, public and private infrastructure, logistics, manufacturing, metals, automotive, steel, mining and energy, waste-to-energy and utilities projects are among major sectors earmarked for expansion — in areas extending from China and India, down through SE Asia-Pacific to Australasia, according to Konecranes.
With this resurgence in demand for EOT cranes, will come a renewed focus on achieving the highest standards of reliability, cost-efficiency and safety — a process driven by not only technology innovations in new cranes, but modernization among existing fleets of EOT cranes as the region has experienced the largest and longest economic expansion in its collective history.
“As thousands of new cranes have entered service over the past 20 years, the countries of the region have built up a massive and maturing pool of existing cranes. Many of these have been under-utilized in recent times, but are substantially sound and can achieve strong cost-efficiency, lifespan and safety gains by being modernized rather than replaced,” says Mark Beckwith, operations manager, Konecranes and Demag (part of Konecranes Group). Some older cranes won’t be able to compete with the efficiency of new crane technologies, but, for others, overhead crane modernization can present a cost-saving alternative to buying new equipment. This will assist a wider range of businesses to benefit from the more efficient, updated technology that is available in brand-new cranes tailored to particular industries.”
Crane modernization raises operational productivity and profitability, as operators of upgraded equipment see a decrease in maintenance costs and control capital expenditures in highly competitive industries. “If you haven’t looked into crane modernization, you’ll likely be surprised by the range of safety and productivity enhancements possible through updating older cranes,” adds Beckwith.
He believes modernization reduces the weight of older cranes, as new motors, trolleys, hoists and other components are significantly lighter than original equipment. Reduction of dead weight can often increase the capacity of an overhead crane as the load demands on equipment have likely increased over the years. The objectives of any crane modernization should be more efficient operation and improved productivity, both of which lead to increased profitability.
Enhanced safety is also key. Sway control technology, one of the more popular safety upgrades in crane modernization projects, limits load swing by controlling the bridge and trolley acceleration and deceleration. Active sway control is designed to dampen also the existing load sway. It is based on continual measurement of the rope angle. Waiting for load sway to stop or attempting to prevent or reduce it can considerably lengthen the duty cycle.
A variety of automated features can be added in crane modernization projects. For example, cranes in busy, congested facilities can be automated to run on selected safe travel paths. And automated zone control allows a crane to be programmed to operate only in certain areas, to protect personnel and property.
Another high-tech upgrade is distance-detection control, which senses proximity of other cranes on a runway to prevent collisions. One of Konecranes crane modernization services includes TRUCONNECT digital technologies responding to Industry 4.0, which can be retrofitted to EOT cranes, such as those employing CXT wire rope hoists.
TRUCONNECT Remote Monitoring collects condition, usage and operating data from control systems and sensors on an asset and provides alerts of certain anomalies. Remote Monitoring data is used in maintenance planning and in predicting possible component or equipment failure.
“Crane modernization offers more possibilities than you might imagine for updating old equipment to new standards of productivity and safety,” says Beckwith.
Companies considering whether a modernization is a valid option can use Konecranes Crane Reliability Study (CRS) and Steel Structure Analysis for a deeper insight into the condition, safety and efficiency of lifting equipment.
“Sometimes the best option may be a new crane. But the number of existing cranes out there is huge, and many properly maintained cranes can be cost efficiently modernized,” adds Beckwith.
“Modernizing a good existing crane to the best global standards can be a very attractive option where the machinery is assessed as fundamentally sound after thorough compliance, condition and safety audits to help to establish which is the best choice for each operation and industry.” Precise loading and unloading of material is of utmost importance in the industrial sector. Numerous parameters are involved to achieve these daily operations including but not limited to wind flow, speed direction, inclination, and container positioning.
Remote supervision
ABB goes one step further to suggest there are more advanced features manufacturers should be aware of when choosing a drive for crane applications. These include: inbuilt sensorless anti-sway; brake match (catching the load on the fly, if there is a problem with a mechanical brake); HSO – Hoist Speed Optimization (running with or without a load and optimising the speed); smooth lifting (when starting with loose ropes, to avoid shock load when the rope tightens up); master/follower (a motor working together in the same gearbox) and synchro control (electrical shaft, to synchronise multiple hooks).
It claims safe crane operation and control can now be simplified by using flexible IEC 61131-3 programming and certified safety functions placed inside the drives.
“We always try to offer our customers a variety of choices, without locking them into one singular solution. For example, they can choose a drive-based control with our software, or they can use their own programming software, or they can use an external PLC. ABB offers a wide selection of flexibility, but it is all built on standardized ABB configurations and IEC 61131-3 based application programming software for easy compatibility,” says Mikael Holmberg, segment sales manager, Cranes and Marine Winches, ABB Drives.
Remote supervision is a growing trend in the industry, according to ABB and allows the crane drives and PLC to be connected for possible remote support and diagnostics. Ethernet-based modules are available for this purpose. In addition, its ACS880 drives include a memory unit for quick replacement or updating without the need of a PC.
Holmberg adds, overhead cranes need to be carefully designed to operate efficiently and safely, whether they are moving containers, buckets of liquid metal, rolls of paper or waste. Every detail matters when selecting crane control for hoist, trolley and long travel movements. ABB’s ACS880 industrial drives with built in crane control software have a range of safety functions to achieve excellent crane performance.
For example, load sway can occur in trolley and long travel movements. The ACS880 drive’s anti-sway control program automatically compensates for it when it happens. The control program creates a mathematical model of the crane’s pendulum. It estimates the pendulum’s time constant by continually measuring the hoist position and load properties, and then factors in the swing velocity and angle.
When the operator changes the speed of the crane’s travel, the drive instantly recalculates the required speed reference to compensate for the crane’s speed change, preventing the load from swaying.
OEMs have historically achieved crane control by custom-made programming via a PLC. However, this approach means that the OEM must essentially do everything by themselves which requires high manpower, dedicated in-house skills and continuity over a long time span, often making it very costly.
A modern alternative to this approach is to use ready-made crane applications that provide the necessary crane control via variable speed drives. ABB has recently developed a platform that allows crane control to be done via a variety of routes, all of which utilize the power of the drives.
These alternatives include: drive-based crane applications done either by readymade ABB crane software inside the drives or; do-it-yourself solutions with IEC61131-3 programming inside the drives or; PLCbased control, where the crane application is running in the PLC controller which communicates via gateways with the drive.
Here too the programming language is the same IEC61131-3 as in the ACS880 industrial drives.
“Our crane solutions offer a combination of safety, flexibility and standardization for the crane control market. Certified safety functionality which is delivered via the drives is a big advantage. In addition, ability to use the same IEC programming language, whether the control is going through the drives or a PLC, is an important benefit giving standardization between the drives and PLC,” says Holmberg.
Under all circumstances, the equipment must perform safely and precisely, without any risk of a load drop or swaying.
Additional value for indoor crane control is delivered with a dedicated link between drives D2D (drive to drive) for master/ follower configuration, where two or more motors are driving the same gearbox. Sensorless anti-sway control is also now standard on ACS880 crane drives, meaning hook swinging is reduced for greater effective indoor crane use. Both trolley and long travel drives can be used with antisway in the x-y directions and load swing compensations can be made at same time for both directions.
Software benefits are also realized on outdoor tower cranes where a new slew control algorithm ensures that the jib is turning around the boom without oscillation.
This feature generates both better safety and productivity on construction work sites.
Precise manipulation of loads
According to PaR Systems there is an increasing awareness, among those who use heavy duty cranes in industries such as aerospace, automotive, and metal processing, that improving crane safety and productivity is of paramount importance and the degree of crane safety and productivity at a given facility can largely be attributed to the crane operators. The skill with which operators are able to drive a crane directly affects load swing, collisions, efficiency, crane maintenance, and the general safety of plant personnel.
Its ExpertOperator (EO) implemented within the Siemens platform, is a hardware module that helps operators of all skill levels drive a crane like an expert, which means even novice crane operators can reduce load swing, position loads more efficiently, avoid collisions, and reduce operator-error induced maintenance requirements. It uses equipment such as Simatic S7 PLCs, Simatic HMI Panels, and Scalance W Industrial Wireless Modules. Unique algorithms within PaR’s software enables crane operators to more easily, quickly, and safely control the movements of payloads, such as dies and coils in automotive stamping plants, it is most effective for applications that require high throughput, and precise manipulation of loads to meet production demands and prevent collisions with sensitive equipment and personnel.
EO anti-sway technology has been in use since 2011 in hundreds of applications worldwide. Users claim it can control crane loads with 95% less sway and 90% fewer “close calls” or collisions by intercepting pendent or radio-pendent commands.
“The primary advantage of using ExpertOperator anti-sway technology is that it allows novice and expert crane operators to reduce payload swing by 85-95% while positioning efficiency is increased and collisions and near misses are significantly reduced,” says Miles Close, director, Product Management, PaR Systems.
“It is a sensorless technology that does not require the use of any sensors (hoist encoder, load sensor) or operator inputs to implement. The technology automatically compensates for sway at any hook height, payload, rigging configuration and auxiliary hook applications. It has proven to be reliable technology especially for demanding 24/7 production environments in primary metal and automotive die stamping applications.”
During trials six different load movement scenarios were captured on video and analysed to quantify the effectiveness of EO at suppressing load swing, with results determining it is capable of reducing load swing by approximately 90%. When EO was disabled, the average load swing exhibited by all the cranes was approximately 3.5 feet. Whereas, when EO was enabled, the average load swing was 3.3 inches.
Many of PaR’s customers run 24×7 operations and have reported significant improvements in productivity. For example, one customer in a high-throughput locomotive manufacturing process reported that the critical path load positioning time was reduced from approximately four minutes to less than two minutes. This result is not atypical. End users who implement EO generally report between 10% and 50% reduction in load positioning time.
Each time a crane operator pushes a button, electric current rushes through the power section of the drives. The current also flows into the motors, and this causes torque to be propagated in the mechanical drive train through to the gears, wheels, and finally the rails of the crane’s infrastructure. When the number of starts, stops and surges in current are reduced by 60%-80% with ExpertOperator, then the life of that critical equipment is prolonged.
As a result, the mean time between failure (MTBF) statistics is improved by a factor of 2-3 times and maintenance costs are reduced