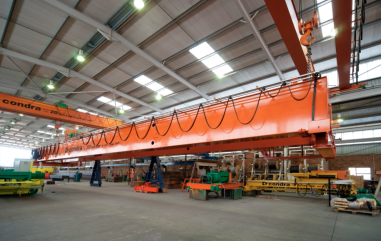
Rovic, a South African manufacturer of agricultural machinery, has decided to modify its shopfloor workflow to cut component assembly times, improve staff safety and increase the rate of production.
In order to do this, a new production sequencing will be applied to the company’s large and small grain planter range, which led to a lifting equipment tender submitted as a joint project by three South African companies working in close cooperation: BB Cranes (which took the order), iTek Drives and Condra.
BB Cranes’ contract comprises three double-girder electric overhead travelling cranes to be installed in the Rovic’s factory under construction in Blackheath, Cape Town.
Key to the improved workflow will be a simplified and precise positioning of grain-planter components. The fixed gantries used for this procedure in the existing factory will not be replicated in the new one. Instead, twin overhead BB cranes fitted with multiple hoists will service the production line to allow simultaneous assembly of various planters without having to move the cranes.
Precise hoist load positioning will be achieved by Invertek Optidrive variable-speed drives supplied by iTek Drives.
The old assembly sequence made use of forklifts to move planter components to a number of fixed gantries on an as-and-when-required basis. There, gantry staff positioned and fastened them in a time-consuming process that included fitting up to 53 identical planting units one by one to each machine.
In the new assembly sequence, two identical double-girder overhead cranes spanning the entire 28-metre width of the factory floor will service multiple planters arranged in a row, allowing simultaneous assembly of an increased number of machines, and removing from the shop floor the obstruction to movement represented by the fixed gantries.
Multiple hoists fitted to the cranes will work independently to lift and position chassis components and planting units to the various machines.
Each of the twin overhead cranes will feature six hoists: two 3,2-ton crab-mounted units for the chassis components, and four underslung 1-ton hoists fitted two to each girder for the planting units. All six hoists on each crane will work simultaneously across the row being serviced.
The space between the overhead crane girders will be a wider-than-normal 2,5 metres, allowing the crab-mounted hoists to adjust chassis component position without having to move the crane.
The third overhead crane, the 20-tonner, will be used to move completed planters out of the factory for shipping.
Rovic manufactures agricultural machinery sold to customers worldwide under the Syncro brand. Products include large and small grain planters, mist blowers, spreaders and tillage equipment.
When the company commissioned construction of a second, larger factory to meet demand, the approach was unusual: instead of specifying lifting equipment capabilities and then inviting tenders, management instead communicated a willingness to reconsider and radically modify current workflow and assembly sequences, leaving it up to the companies submitting tenders to optimise their proposed solutions.
BB Cranes of Cape Town worked closely with two Johannesburg companies –iTek Drives and Condra – to develop and fine-tune the handling protocol for the winning component-positioning and assembly proposal.
BB Cranes steered the compilation of the proposal and secured the order, with Condra supplying design office support and cooperating closely with iTek Drives and BB Cranes throughout the design phase.
Manufacture of the three cranes has begun. Delivery is scheduled for July 2024.