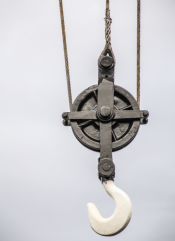
Wire ropes, essential components in industries such as mining, construction, and transportation, require careful attention to lubrication to ensure their longevity and safe operation. Ron Byrnes, a senior technical sales representative and Wire Rope specialist at Lubrication Engineers (LE) South Africa, emphasizes that proper lubrication is critical, highlighting that wire ropes are intricate machines rather than just cables. With over 30 years of experience in the field, including work with major Southern African mines and wire rope manufacturers, Byrnes explains that wear in wire ropes occurs not only between individual wires but also between the strands as they move against each other.
Byrnes stresses that without lubrication, wire ropes are prone to corrosion, which can lead to the gradual loss of steel within the rope components. This internal wear is often difficult to contain and can be impossible to manage without adequate lubrication. While rust corrosion is an issue, internal friction and wear are the primary causes of rope failure. Correct lubrication helps mitigate these effects, extending the useful service life of wire ropes and improving operational safety.
Despite the importance of lubrication, Byrnes notes that many industries take an inconsistent approach to rope maintenance. Often, operational teams rely on visual inspections and intermittent lubrication, with a more thorough assessment only occurring during non-destructive electromechanical tests. To improve these practices, Byrnes advocates for an “application theory approach,” which focuses on understanding both the function of the wire rope in its specific application and the behavior of the lubricant in reducing wear and corrosion.
In South Africa, where both locally manufactured and imported wire ropes are in use, lubrication practices vary based on the type of lubricant applied during manufacturing. Locally, a bitumen-based lubricant is commonly used, but Byrnes emphasizes that this doesn’t necessarily dictate the best approach for maintenance. He recommends LE’s Wirelife Monolec Penetrating Lubricant 2001 for imported high-performance wire ropes and LE’s Wirelife Almasol Coating Grease 452 for round, non-spin, and 6-stranded triangular ropes. These lubricants are designed to penetrate the rope’s interstices and remain effective, even when applied to ropes with pre-existing bitumen-based coatings.
Byrnes also highlights the advantages of using a Viper Rope Lubricator, a device that ensures consistent application of lubricant while cleaning the rope of old lubricants. The system helps to massage fresh lubricant into the core of the rope, ensuring optimal lubrication for enhanced performance.
The benefits of these modern lubricants extend beyond performance. Bitumen-based lubricants can become brittle in cold temperatures, flinging off the rope and causing damage. In contrast, Wirelife Almasol Coating Grease 452 remains effective in a wide range of temperatures, from -20°C to over 120°C. Additionally, LE’s products meet stringent environmental standards, producing fewer harmful emissions and reducing safety risks compared to bitumen-based lubricants.
Byrnes also emphasizes the importance of aligning lubrication practices with health and safety regulations, such as the Mine Health and Safety Act and OSHA standards, to protect workers and the environment. Adopting a more systematic and scientifically informed approach to wire rope lubrication can significantly enhance the safety, performance, and sustainability of these vital components in various industries.