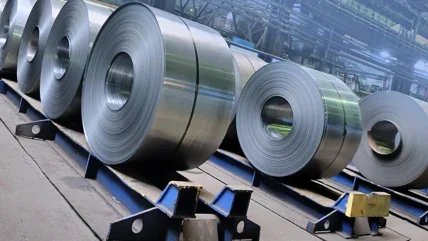
Just in the first half of this year, according to The Wall Street Journal, a total of 15 US workers died in steel mill accidents. Not all of these involved cranes, but some did. This seems to be quite high given that in all of 2006 (the last year for which US government statistics are available), 14 workers were killed in iron and steel mills, up from eight in 2005, nine in 2004 and eight in 2003.

While this seems to be a large number of incidents involving overhead cranes at steel mills, Earl W Hicks, a spokesperson for the US Occupational Safety & Health Administration (OSHA) says it does not appear that there has been a major spike in the frequency of these accidents.
“It is impossible to say if the amount of crane related steel accidents has increased or decreased,” says Michael Wright, head of health, safety and environment for the United Steelworkers of America (USW) labour union. “There aren’t good enough statistics other than for fatalities. Also the numbers are too small to draw a statistical conclusion. But any accident and especially every fatality is a tragedy. We don’t care if they increased or decreased. It doesn’t matter to family members who lost a loved one if there are others as well. We aren’t satisfied until no one has died or was seriously injured on the job,” Wright adds.
That is also what steelmakers are trying to achieve, says Katie Patterson, a spokesperson for Chicago-based ArcelorMittal USA. She says “ArcelorMittal’s greatest responsibility and priority is ensuring the health and safety of our employees on a daily basis. While we are the largest and fastest growing steel company in the world, if we are to realise our true potential we must also be recognised as one of the safest steel companies in the world.”

She says the company’s commitment to health and safety was recently strengthened through its agreements with the USW, the International Metal Workers Federation and the European Metalworkers Federation to establish joint health and safety committees in all of its facilities worldwide.
ArcelorMittal USA, Patterson continues, “are undertaking new initiatives to provide our employees with the necessary tools and training to improve work planning and on-the-job hazard assessment and control of hazards to provide every employee with a full understanding of how to best prevent serious injury and accidents while on the job,” she says.
Wright says “Steel mill workers do get very extensive training on operating, rigging and preparing cranes. The USW and the steel mills try to make sure they are as comprehensive as possible.”

“There are certainly optional training programs available to the end-user community from us, other crane manufacturers and elsewhere,” says Gene Buer, executive director of hoist products for Columbus McKinnon Corp., Amherst, New York. “We are seeing substantial demand for training programs for crane and hoist safety and operating procedures. It is available and more and more end users are taking advantage of the training being offered,” he adds.
“OSHA is always seeking to engage employers and employees in cooperative efforts, such as partnerships and alliances to promote their special safety needs and to provide training,” says Hicks.

Meanwhile, the USW has been pushing for mills to be audited periodically for all of the factors involved with crane operation, says Wright. “They need to be periodically monitored to see what can go wrong. There are a number of potential problems that could be identified in advance. A lot of things that could be hazardous conditions can be identified in a periodic audit,” he maintains.
Wright says: “Primarily it would help to alleviate certain unsafe conditions as well as certain unsafe acts of operators. Sometimes something is wrong with the crane or people work too close to the cranes. These are sometimes things that a comprehensive safety audit would have identified.”
He is a big supporter of crane training, including training “that does not just tell workers what the rules are, but why those rules are in place. Workers need to have a deep understanding of the rules and procedures in place, as well as the fact that they have the right to remove themselves from a dangerous situation,” even when being pushed by management to be in that situation.
Looking into the future, the overhead crane industry should follow in the footsteps of the tower and mobile crane industry and push for certification of crane operators, riggers and signal persons, says Graham Brent, executive director of the Fairfax, Virginia-based National Commission for the Certification of Crane Operators (NCCCO). Already, Brent says there are certain states that require that construction crane operators be certified.
“While certification of crane operators is not a cure all, it could go a long way in mitigating risk,” he says, adding: “There has been evidence in the mobile crane industry that there has been a dramatic decrease in accidents and near misses over a sustained period of time largely due to crane operator training and certification.” One example, he says, is California where there has been an 80% drop in crane fatalities and a 50% drop in injuries due to a mandatory program for certification of mobile crane operators there.
There are voluntary certification programs for overhead crane operators, Brent says, but there has been a slow acceptance curve. He says his group does not yet offer certification programme?s for overhead crane riggers and signal persons, although it does for those involved with tower and mobile cranes. “It depends on the response of that industry whether we expand it to overhead cranes.”
Hicks says the OSHA could make no predictions about the number of accidents related to overhead cranes in the future, but “the agency remains hopeful that, with increased attention paid to these hazards and the sources of help available, including training, outreach and cooperative efforts, fewer accidents will occur.”
Steel mill accidents involving overhead cranes
– July 2007: a worker at Nucor Steel Corp.’s Marion, Ohio, facility was killed after being yanked into a crane. He had been suspended in a harness 30-40ft above the ground while working on the mill’s air conditioning system. The harness reportedly became tangled in the crane’s shaft causing the man to be pulled into the crane.
– February 2008: an AK Steel Corp. Coshocton, Ohio, worker, David Wemtz, was killed while performing maintenance work. He was crushed by a steel coil that was being lowered by an overhead crane.
– March 2008: a worker at the Montpelier, Iowa, plate mill of Ipsco Inc. (now known as SSAB North American Division) was killed when he fell approximately 100ft from a crane.
– March 2008: a Keystone Steel & Wire Co. worker, Edward Schimmelpfennig, died when the crane he was operating tipped over. He had been either loading or unloading steel from a flat bed truck crane flipped.
– March 2008: a crane operator, Jason Lee Blackmon, fell 40ft to his death at Gerdau Ameristeel Corp.’s Jackson, Tennessee, facility. Reportedly he had been on a platform about to board the crane during a shift change when the the crane failed to come to a complete stop, as it is required to do when a worker boards the crane.
– May 2008: Russell Payne, a millwright at ArcelorMittal USA’s Burns Harbor, Indiana, facility died when he was caught between two steel beams and crushed. The crane caught one beam and dragged it to another. Reportedly the crane operator had thought that Payne had moved out of the area, and attempted to put the crane back in place via remote control.
– June 2008: a crane collapsed during a storm at OAO Severstal’s Sparrows Point, Maryland, steel mill. Two men working on the crane were stuck 50-70ft above the ground when it collapsed, but they escaped uninjured.
A viewpoint from Europe

“In Europe the crane design standards have recently become far more prescriptive with regard to ensuring the safety of personnel in certain steel mill crane applications. For example, cranes for ‘lifting and transporting hot molten masses’ must now be designed in such a way that in the event of a structural component failing in the kinetic chain the load is prevented from falling. This makes it mandatory to fit emergency brakes which act on the hoist drum in the event of a failure in the hoist transmission. Mandatory ‘safety categories’ have also been introduced for crane control systems involving electronics.”
Andrew Pimblett, managing director, Street Crane
EN 14492-2 is the relevant European standard.
These pictures represent typical lifting scenarios in steel facilities and are in no way connected with any of the accidents referred to in this article