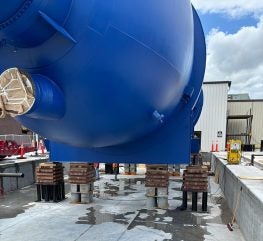
Engineered Rigging (ER) has partnered with Belger Cartage Service to design lift plans, provide equipment rental and deliver onsite technical support for an epic autoclave machine.
An autoclave is a machine used to carry out industrial and scientific processes requiring elevated temperature and pressure. This particular autoclave was needed to cure composites for airplane parts, weighing a million pounds, at 55 feet long and 25 feet wide.
Before construction could begin on a new manufacturing facility in Tulsa, Okla, the autoclave had to be moved into position so Belger approached Engineered Rigging to help them.
“Having multifaceted capabilities under one roof, Engineered Rigging was able to fulfil Belger’s needs within the required six-week deadline,” said John Kuka, director, Business Development, Engineered Rigging.
Upon delivery to the construction site, the autoclave was placed in an out of the way location that would require two separate lateral moves to align the machine to the eight pylons which were the machine’s foundation.
A total of more than 50 feet of lateral movement was needed, including a portion at elevation over the approximately 5.5 feet deep pit where the pylons were located. Once positioned, the building would be constructed around the massive autoclave.
When developing the plan, several factors were considered by ER’s engineering team including the load weight, dimensions, lifting points, depth of the pit, center of gravity and site conditions.
Engineered Rigging determined that two Enerpac LH400 low-height Skidding Systems were the ideal solution for the lateral moves. By doubling the track on each skidding system, the load capacity was doubled to safely skid the million pound weight of the autoclave.
The skidding systems were powered by two Enerpac SFP421SJ Split Flow Pumps while Enerpac HCR20010 double-acting hydraulic cyclinders were used to lift and lower the autoclave onto the foundation
The first lateral move was 21 feet from west to east. After it was completed, Engineered Rigging’s technicians lifted the autoclave to reset the skidding systems and track to traverse north to south. The autoclave was then slid another 32 feet.Once in position above the support foundation, a precise sequence of stage lowering was followed using a combination of the Enerpac 200-ton cylinders with a 10 inch stroke, load stools and cribbing to jack and crib the autoclave down into its final elevation.