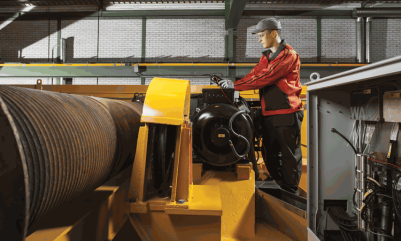
Konecranes and Demag South Africa has been awarded a R20 million crane electrical modernisation contract for an industrial company based in southern Africa. Originally purchased from Konecranes and Demag South Africa, the crane had started to show signs of wear in mid-2024.
“At the onsite assessment, we conducted a full electrical and mechanical evaluation of the crane. This showed that the downtime and resulting breakdowns experienced by the client were a result of the age of the electrical system, which was no longer performing optimally. We recommended that an electrical modernisation programme be undertaken,” said Alwyn Rautenbach, modernisation and sales support specialist, Demag Cranes & Components.
The modernisation programme included the replacement of all key electrical components and also the reprogramming of the variable speed drives. “As we hold a large supply of mechanical and electrical components for our products at our premises, we were able to supply all of the parts required to complete the modernisation upgrade from our Johannesburg distribution centre,” said Ian Grobler, sales manager, EMEA South Africa, Konecranes and Demag.
Components such as variable speed drives, encoders, auxiliary panels, brakes, and hoist resistors formed part of the consignment of components. Full functionality testing and a factory acceptance test were conducted before the complete electrical upgrade was delivered to site.
The process took one month, with ongoing monitoring of the crane’s performance continuing for a further two months. “Despite the removal of the crane’s complete electrical system, the modernisation transition was smooth and efficiently conducted,” said Rautenbach. “We will continue to supply assistance on site and conduct unscheduled maintenance that limits downtime for the customer, while we ensure that everything in the new system is performing as it should.”
Grobler added, “The cost of maintaining crane electrical and control systems increases over time. An electrical system modernisation not only helps improve the performance of your existing equipment, it also extends the lifespan of your crane without the major capex expenditure of purchasing a new crane.”
New safety features and positioning capabilities can simply replace high-maintenance, obsolete components with newer technology offering a newer, tailored and fully integrated system. We are proud to have been able to resolve the customer’s crane challenges as cost efficiently and as timeously as possible.
The end result has delivered a modernised and fully operational ‘new crane’. We are also delighted to be the preferred supplier to the same customer for a further two to three electrical crane upgrades over the next two years.”
“Konecranes receives a substantial number of enquiries from clients based in southern Africa, no matter the make of the crane. Key factors in our successful resolution of any mechanical or electrical performance issue are our quick technician-to-site response time for assessment purposes, and our ability to supply spare parts and components from our distribution centre easily to site. This ensures that the refurbished crane equipment is fully operational quickly, without cutting any safety requirements,” added Rautenbach.