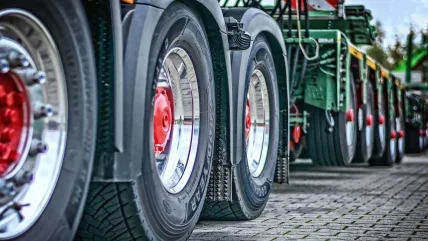
Mitsubishi Logisnext Americas says that with Lift Link, businesses receive access to accurate and actionable data delivered in real-time, enabling them to more effectively operate their fleet, while maximising uptime and usage.
The solution offers fleet-wide insights and is compatible with various types of material handling equipment, from warehouse products to electric and internal combustion forklifts. This solution equips customers with the ability to, for example, manage/limit forklift usage to only authorised operators; use existing employee badges (proximity cards) or PIN codes; enforce the completion of pre-operation forklift inspections; improve driver behaviours utilising impact detection and management; track planned maintenance milestones to aid on-time planned maintenance service; communicate with operators with twoway communication.
“We are excited to introduce the Lift Link telematics solution, which represents Mitsubishi Logisnext Americas significant advancement in connectivity and fleet management,” said Jerry Sytsma, executive vice president of sales and aftermarket services at Mitsubishi Logisnext Americas. “With Lift Link, our customers can harness the power of realtime data to make informed decisions, improve operational efficiency and ensure a safer work environment.”
During the summer, Mitsubishi Logisnext Americas celebrated the groundbreaking for its new production facility in Houston, Texas. Located on the Houston headquarters campus, the new facility will support the manufacturing of electric warehouse products across the Jungheinrich, Cat lift trucks, Mitsubishi forklift trucks and UniCarriers Forklift product lines. It represents a key investment in the company’s long-term electric growth strategy to support its customers throughout North America.
The state-of-the-art facility will provide increased production capabilities to further support the growing demand for electric lift trucks and warehouse products.
With a total floor area of 73,000ft2, the new facility will expand Logisnext’s current electric manufacturing capabilities by serving as a dedicated fabrication space for in-house welding and painting of masts and frames. The facility will also integrate cutting-edge technologies such as Mixed Model Line Design, Industry 4.0 process monitoring and one-piece flow. The expansion of robotic welding, along with the optimisation of paint capacity and weld fixtures, will contribute to Logisnext’s ongoing focus for improved efficiency.
Jay Gusler, executive vice president of operations at Mitsubishi Logisnext Americas, said: “The material handling industry is rapidly changing, and we are proud to be on the forefront of this change. We’re committed to investing in our manufacturing capabilities and new product development to ensure we continue providing our customers with the most advanced, yet sustainable, electric products and solutions in the future.”
Leading the groundbreaking was Ken Barina, president, Mitsubishi Logisnext Americas, as well as Gusler.
Construction of the new facility is expected to be completed in the first quarter of 2024.