Operators were using an air balancer to load 35-70lb motor adaptor castings into a twin spindle machine.
The adaptors were lifted to the milling machine, lined up and placed on a soft-jaw chuck before being moved to a table and deburred.
The pump manufacturer wanted to decrease the slamming of adaptors onto the chuck, and therefore the potential for operator injury and product damage.
Gorbel advised replacing the air balancer with a G-Force lifting device.
To prevent slamming of adaptors, the G-Force was programmed with virtual limits and was equipped with a sensor to divide the work cell into pick and drop zones. In the pick zone the G-Force operated at normal speed, and in the other zone it operated more slowly.
Gorbel said that the manufacturer has increased its productivity, decreased floor inventory, and no longer had to wait for the air balancer to bleed pressure.
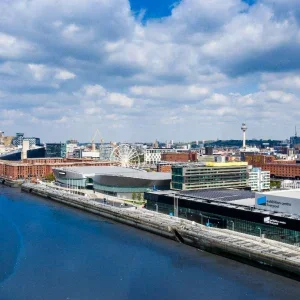