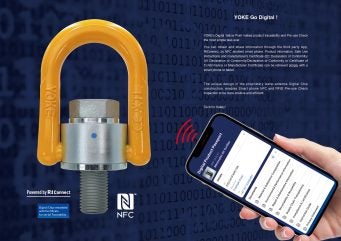
YOKE Industrial Corp. has equipped its full range of lifting and rigging products with Digital Product Passports (DPP), supporting the European Union’s Ecodesign for Sustainable Products Regulation (ESPR).
The company’s diverse product catalogue, which includes Grade 80 and Grade 100 lifting chain fittings, swivel hoist hooks, shackles, wire rope clips, and lifting points, now incorporates radio frequency identification (RFID) chips in each item. This integration allows users to track and manage products throughout their lifecycle using DPPs, a tool that records key data such as material composition, energy performance, maintenance guidelines, and recycling methods.
The introduction of these DPPs aims to promote transparency, resource efficiency, and compliance with environmental regulations.
The move comes as the EU gears up to fully enforce the Machinery Regulation in less than two years, marking the repeal of the Machinery Directive 2006/42/EC. Among the most significant changes will be the requirement for original certifications and manuals to be provided digitally with products. Meanwhile, the ESPR, which replaced the Ecodesign Directive 2009/125/EC last year, focuses on improving sustainability through enhanced circularity, energy performance, recyclability, and durability of products sold in the EU market.
Steven Hong, president of YOKE, expressed strong support for the ESPR, noting that the regulation aligns with the company’s core principles of compliance, traceability, status, and net zero, as encapsulated in its RiConnect Compliance Management System. YOKE has long advocated for the use of RFID and Software as a Service (SaaS) in the lifting industry, and the growing acceptance of these technologies is seen as a positive shift toward digitalisation and streamlined compliance management.
YOKE’s use of Near Field Communication (NFC) RFID technology has made it possible for users to verify product identity and safety using only their mobile phones—no app required. The system allows for seamless integration with smart devices, ensuring that product information is accessible without the need for physical labels. The app’s functionality extends beyond DPPs, offering paperless asset management, compliance documentation, and pre-use checks.
Hong highlighted that while the lifting industry is traditionally conservative and slow to embrace new technology, NFC RFID chips are changing this mindset. He noted that such digital solutions open the door to greater adoption of innovative technology by manufacturers and partners worldwide.
Each YOKE product receives a unique DPP upon manufacture, giving users continuous access to complete product details. The accompanying app features modules for asset compliance management, offering enhanced tracking, monitoring, and overall asset management capabilities. The company’s NFC RFID chips, which are pressure-fitted into steel or retrofitted onto other products, undergo rigorous testing for durability, temperature resistance, waterproofing, and corrosion resistance, ensuring reliability in extreme environments.
As the industry shifts toward digital solutions, YOKE aims to phase out traditional hard labels, which are prone to wear and fading, replacing them with more accurate, easily updatable digital systems. Hong explained that this transition not only improves data management efficiency but also reduces resource waste, aligning with the principles of a circular economy and sustainable development.